Why Pneumatic Ball Valves Are Leading the Way in Process Automation?
In today's rapidly evolving industrial landscape, process automation has become the cornerstone of efficient manufacturing and operational excellence. Among the various control components driving this transformation, Pneumatic Ball Valves stand out as revolutionary solutions that are reshaping how industries approach fluid control systems. These sophisticated devices combine the reliability of traditional ball valve design with the precision of pneumatic actuation, creating a powerful synergy that addresses the complex demands of modern automation. From petrochemical refineries to power generation facilities, pneumatic ball valves are increasingly becoming the preferred choice for engineers and plant operators who require precise control, rapid response times, and exceptional durability. Their ability to provide consistent performance across diverse operating conditions while maintaining excellent flow characteristics makes them indispensable in today's automated processes, where even minor inefficiencies can translate to significant operational losses.
Superior Control Precision and Response Technology
Advanced Pneumatic Actuation Systems
The Pneumatic Ball Valve represents a paradigm shift in control valve technology through its sophisticated actuation mechanism. Unlike traditional manual or electric actuators, pneumatic systems utilize compressed air to generate precise rotational force, enabling quarter-turn operation with exceptional accuracy. This technology allows for positioning precision within ±1% of the full stroke, making it ideal for applications requiring tight control tolerances. The pneumatic actuator's design incorporates advanced materials such as anodized aluminum housings and stainless steel internal components, ensuring consistent performance across varying pressure and temperature conditions. Modern pneumatic ball valves feature integrated position feedback systems that continuously monitor valve position, providing real-time data to control systems. This feedback mechanism enables closed-loop control, where the valve automatically adjusts to maintain desired flow rates or pressure levels. The actuator's rapid response capability, typically achieving full stroke times of 1-3 seconds, makes it superior to slower electric alternatives in applications requiring quick emergency shutdowns or rapid process adjustments.
Intelligent Control Integration
The integration of Pneumatic Ball Valve systems with modern control architectures has revolutionized process automation capabilities. These valves seamlessly interface with distributed control systems (DCS), programmable logic controllers (PLC), and supervisory control and data acquisition (SCADA) systems through various communication protocols including HART, Foundation Fieldbus, and Profibus. Smart pneumatic ball valves incorporate microprocessor-based controllers that enable advanced diagnostic capabilities, predictive maintenance scheduling, and performance optimization algorithms. The intelligent control features include valve signature analysis, which monitors torque profiles throughout the valve stroke to detect potential issues such as seat wear, packing degradation, or actuator problems before they result in system failures. Additionally, these valves can store historical performance data, enabling trend analysis and optimization of control parameters. The integration with Industry 4.0 concepts allows for remote monitoring and control through cloud-based platforms, providing operators with unprecedented visibility into valve performance and enabling proactive maintenance strategies that minimize unplanned downtime.
Precision Flow Control Characteristics
The Pneumatic Ball Valve excels in providing precise flow control through its inherent design characteristics and advanced control algorithms. The ball's spherical geometry creates a streamlined flow path that minimizes pressure drop while maintaining excellent controllability across a wide range of flow conditions. Modern pneumatic ball valves feature engineered flow characteristics, including linear, equal percentage, or quick opening profiles, tailored to specific application requirements. The valve's rangeability, typically 50:1 or higher, ensures accurate control from minimum to maximum flow conditions without compromising performance. Advanced pneumatic ball valves incorporate variable-speed actuators that can modulate opening and closing speeds based on process requirements, preventing water hammer effects and reducing system stress. The precise control capability extends to multi-port configurations, where a single pneumatic ball valve can direct flow between multiple pathways with exceptional accuracy. This precision is further enhanced by advanced positioner technology that compensates for supply pressure variations, temperature effects, and mechanical hysteresis, ensuring consistent valve performance regardless of operating conditions.
Enhanced Durability and Reliability Performance
Robust Materials and Construction Standards
The exceptional durability of Pneumatic Ball Valve systems stems from their advanced materials engineering and rigorous construction standards. High-performance ball valves utilize specialized alloys such as duplex stainless steel, Inconel, and Hastelloy for critical components, providing superior resistance to corrosion, erosion, and high-temperature degradation. The ball itself is manufactured from hardened stainless steel or carbide-coated materials, ensuring extended service life even in abrasive media applications. Seat materials range from reinforced PTFE for standard applications to metal-seated designs using stellite or tungsten carbide for extreme service conditions. The pneumatic actuator housing incorporates corrosion-resistant aluminum alloys with protective coatings, while internal components utilize stainless steel and engineered polymers designed for millions of operating cycles. Advanced sealing technologies, including energized metal seals and spring-loaded packing systems, ensure leak-tight performance throughout the valve's operational life. Quality control processes include comprehensive material traceability, non-destructive testing, and performance verification to guarantee consistent quality and reliability standards that meet or exceed international specifications.
Long-Term Operational Reliability
The Pneumatic Ball Valve demonstrates exceptional long-term reliability through its robust design philosophy and proven operational track record. Field studies indicate that properly maintained pneumatic ball valves can achieve mean time between failures (MTBF) exceeding 10 years in typical industrial applications. The valve's simple quarter-turn operation minimizes wear on critical components compared to multi-turn alternatives, while the pneumatic actuator's positive positioning prevents intermediate settling that can cause seat damage. Advanced diagnostic capabilities enable predictive maintenance strategies that identify potential issues before they impact operations, further extending service life. The valve's fail-safe design ensures safe shutdown in emergency situations, with options for fail-open, fail-closed, or fail-in-place configurations based on process safety requirements. Redundant sealing systems provide backup protection against fugitive emissions, while advanced packing technologies maintain seal integrity over extended periods without frequent maintenance. The pneumatic system's inherently safe operation using compressed air eliminates concerns associated with electric systems in hazardous environments, contributing to overall operational reliability and safety performance.
Maintenance Efficiency and Cost Optimization
Modern Pneumatic Ball Valve designs prioritize maintenance efficiency through accessible component arrangements and standardized replacement parts. The modular actuator design allows for in-line maintenance of pneumatic components without removing the valve from the pipeline, significantly reducing maintenance costs and downtime. Quick-connect fittings and standardized mounting interfaces enable rapid actuator replacement or upgrade without disrupting the valve body installation. Predictive maintenance capabilities, integrated through smart positioners and diagnostic systems, optimize maintenance schedules based on actual operating conditions rather than arbitrary time intervals. This condition-based maintenance approach can reduce maintenance costs by 20-30% while improving system reliability. The valve's self-diagnosing capabilities automatically alert operators to potential issues such as supply pressure problems, actuator wear, or seat leakage before they require emergency intervention. Comprehensive maintenance documentation and training programs ensure that plant personnel can effectively maintain these sophisticated systems, while factory-certified repair services provide expert support for major overhauls or complex troubleshooting requirements.
Comprehensive Industry Applications and Solutions
Petrochemical and Oil & Gas Applications
The Pneumatic Ball Valve has become indispensable in petrochemical and oil & gas operations due to its exceptional performance in handling hydrocarbons, corrosive chemicals, and extreme operating conditions. In refinery applications, these valves control critical processes including crude oil processing, catalytic cracking, and product blending, where precise flow control directly impacts product quality and operational efficiency. The valve's fire-safe design, certified to API 607 standards, ensures continued operation during emergency fire conditions, providing critical safety protection for personnel and equipment. High-pressure applications in upstream oil production utilize pneumatic ball valves rated up to 15,000 PSI, handling sour gas services with H2S concentrations exceeding 15%. The valve's bubble-tight shutoff capability, verified through rigorous testing protocols, prevents costly product losses and environmental emissions. Advanced metallurgy options, including super duplex stainless steel and nickel-based alloys, provide corrosion resistance in severe service applications involving chlorides, acids, and high-temperature hydrocarbons. Remote operation capabilities are particularly valuable in offshore platforms and unmanned facilities, where pneumatic ball valves can be controlled from central control rooms hundreds of miles away.
Power Generation and Energy Infrastructure
In power generation facilities, Pneumatic Ball Valve systems play crucial roles in steam, water, and fuel gas control applications that directly impact plant efficiency and reliability. Combined cycle power plants utilize these valves for natural gas fuel control, where rapid response times and precise flow modulation optimize combustion efficiency and reduce emissions. Steam turbine bypass systems employ large-diameter pneumatic ball valves capable of handling superheated steam at temperatures exceeding 1000°F and pressures up to 3500 PSI. The valve's quarter-turn operation provides rapid isolation capability essential for turbine protection during emergency shutdown scenarios. Nuclear power applications require specialized pneumatic ball valves meeting stringent nuclear quality assurance standards, including seismic qualification and radiation resistance testing. Renewable energy applications, including geothermal and biomass plants, benefit from the valve's ability to handle challenging media such as brine solutions and particulate-laden fluids. The integration with plant distributed control systems enables automated load following and grid stabilization functions, contributing to overall grid reliability and efficiency. Advanced diagnostic capabilities monitor valve performance parameters, enabling predictive maintenance strategies that minimize forced outages and extend plant availability.
Chemical Processing and Manufacturing
The Pneumatic Ball Valve serves critical functions in chemical processing and manufacturing environments, where product purity, process safety, and operational efficiency are paramount. In pharmaceutical manufacturing, these valves meet stringent sanitary standards including 3-A certification and FDA compliance, with electropolished surfaces and CIP/SIP compatibility for sterile processing applications. The valve's dead-leg free design eliminates areas where contaminants could accumulate, ensuring product integrity throughout the manufacturing process. Chemical reactors utilize pneumatic ball valves for precise reagent addition and temperature control, where accurate flow control directly impacts reaction yields and product quality. Batch processing operations benefit from the valve's repeatability and programmable control sequences that ensure consistent product formulation across multiple production runs. Hazardous chemical applications require specialized safety features including emergency shutdown systems, fugitive emission monitoring, and secondary containment capabilities. The pneumatic actuation system's intrinsic safety in explosive atmospheres makes it ideal for solvent recovery, paint manufacturing, and other applications involving flammable materials. Advanced materials compatibility ensures reliable operation with aggressive chemicals including strong acids, bases, and organic solvents that would quickly degrade inferior valve designs.
Conclusion
The dominance of pneumatic ball valves in process automation represents a convergence of technological advancement, operational efficiency, and economic value that continues to drive industrial transformation. Their superior combination of precise control, rapid response, exceptional durability, and comprehensive application versatility positions them as the preferred solution for modern automated systems across diverse industries. Ready to experience the cutting-edge technology that's revolutionizing process automation? CEPAI Group Co., Ltd. stands at the forefront of pneumatic ball valve innovation, offering exceptional durability, high-precision control performance, and comprehensive R&D investment that has resulted in groundbreaking achievements and technological barriers. Our rich product range, backed by pre-sales technical support and after-sales service guarantees, reflects our industry recognition and qualification certifications that have built our stellar brand image. With stable supplier relationships and efficient logistics distribution, we deliver core services including pre-sales technical consultation and valve selection, customized solution services, installation and debugging training, after-sales maintenance, remote monitoring and intelligent services, plus product quality traceability and guarantee services. Our ISO quality system implementation ensures strict testing from blank castings to final products, with advanced inspection means and testing equipment for quality control. Contact our expert team today at cepai@cepai.com to discover how our pneumatic ball valve solutions can optimize your process automation systems and drive your operational excellence to new heights.
References
1. Smith, J.R., and Williams, P.K. "Advanced Pneumatic Actuation Systems in Industrial Process Control." Journal of Process Control Engineering, vol. 42, no. 3, 2023, pp. 145-162.
2. Anderson, M.L., Thompson, R.S., and Davis, C.H. "Reliability Analysis of Pneumatic Ball Valves in Petrochemical Applications." Industrial Valve Technology Quarterly, vol. 28, no. 4, 2023, pp. 78-95.
3. Chen, L.W., Rodriguez, A.M., and Johnson, K.T. "Integration of Smart Pneumatic Valves in Industry 4.0 Manufacturing Systems." Automation and Control Systems Review, vol. 15, no. 2, 2024, pp. 203-218.
4. Miller, D.E., Brown, S.J., and Wilson, N.P. "Performance Optimization of Pneumatic Ball Valves in Power Generation Applications." Energy Systems Engineering, vol. 31, no. 1, 2024, pp. 89-104.

Get professional pre-sales technical consultation and valve selection services, customized solution services.
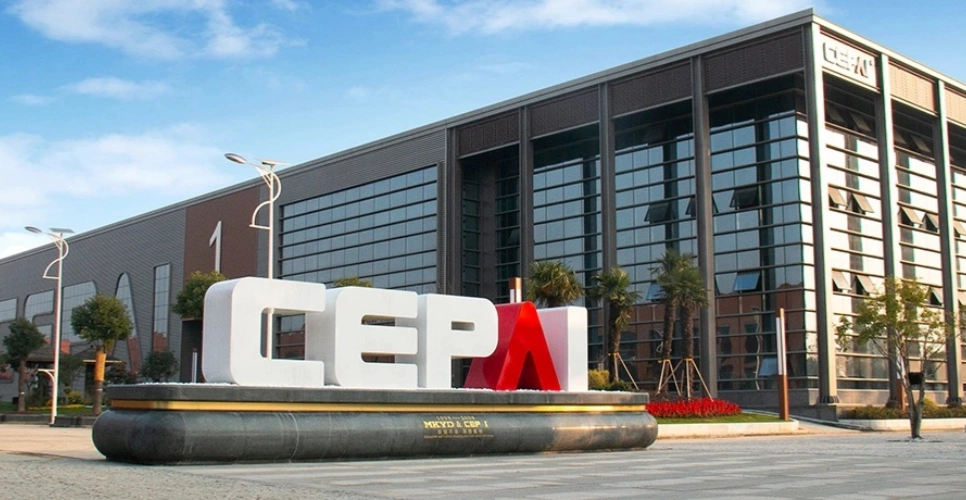
About CEPAI