Benefits of Actuated Ball Valves
In today's demanding industrial landscape, the selection of appropriate valve technology can significantly impact operational efficiency, safety, and cost-effectiveness across various applications. Actuated ball valves represent a pinnacle of engineering excellence, combining the fundamental advantages of traditional ball valve design with the enhanced control capabilities of automated actuation systems. These sophisticated devices offer unprecedented levels of precision, reliability, and operational flexibility that make them indispensable in critical industrial processes. The Electric Ball Valve technology, in particular, has revolutionized how industries approach flow control, providing operators with remote control capabilities, precise positioning, and integrated feedback systems that ensure optimal performance in diverse operating conditions.
Enhanced Operational Efficiency and Control Precision
Superior Flow Control Characteristics
The fundamental advantage of actuated ball valves lies in their exceptional flow control characteristics, which directly translate to improved operational efficiency across industrial applications. Electric Ball Valve systems demonstrate remarkable precision in flow modulation, offering control accuracy that can reach within 0.1% of the desired setpoint. This level of precision stems from the inherent design of ball valves, where the spherical closure element provides minimal flow restriction when fully open, resulting in low pressure drop and optimal flow coefficients. The actuated mechanism enhances this natural advantage by enabling precise positioning of the ball element at any point along its rotation path, allowing for accurate flow regulation rather than simple on-off operation. Modern Electric Ball Valve configurations incorporate advanced positioners and feedback systems that continuously monitor valve position and make real-time adjustments to maintain desired flow rates, even under varying system conditions. This capability proves particularly valuable in processes requiring consistent flow rates, such as chemical dosing, fuel injection systems, and critical cooling applications where flow variations can significantly impact product quality or system safety.
Rapid Response Time and System Dynamics
The response characteristics of Electric Ball Valve systems represent a significant advancement over traditional manual or pneumatic alternatives, delivering actuation speeds that can be precisely controlled and optimized for specific applications. Electric actuators can achieve full stroke times ranging from seconds to minutes, depending on application requirements, with the ability to modulate these speeds based on process demands. This rapid response capability proves crucial in emergency shutdown scenarios, where Electric Ball Valve systems can isolate process sections within seconds of receiving shutdown signals, potentially preventing catastrophic failures or environmental incidents. The consistent and predictable response time of electric actuators eliminates the variability associated with pneumatic systems, which can be affected by air supply pressure fluctuations or contamination. Furthermore, the ability to program acceleration and deceleration profiles prevents water hammer effects and reduces mechanical stress on piping systems, extending overall system lifespan while maintaining operational safety. Advanced Electric Ball Valve systems incorporate soft-start and soft-stop functions that gradually initiate and terminate valve movement, minimizing shock loads on both the valve assembly and connected piping infrastructure.
Advanced Automation Integration Capabilities
Modern Electric Ball Valve systems excel in their ability to integrate seamlessly with sophisticated automation and control systems, providing operators with unprecedented visibility and control over their processes. These valves can communicate through various industrial protocols including Modbus, HART, Foundation Fieldbus, and Profibus, enabling real-time data exchange between the valve and central control systems. The integration capabilities extend beyond simple position feedback, encompassing diagnostic information such as actuator torque profiles, travel patterns, and performance trending data that enables predictive maintenance strategies. Smart Electric Ball Valve systems can detect developing issues such as increased operating torque, irregular travel patterns, or excessive cycle counts, alerting maintenance personnel before failures occur. This proactive approach to maintenance significantly reduces unplanned downtime while optimizing maintenance resources. Additionally, the ability to store and execute complex control algorithms within the valve assembly itself reduces the computational burden on central control systems while ensuring continued operation even during communication interruptions. Remote monitoring capabilities allow operators to assess valve performance from centralized control rooms, reducing the need for field personnel to physically inspect valves in hazardous or difficult-to-access locations.
Superior Durability and Reliability Performance
Exceptional Mechanical Longevity
The durability characteristics of Electric Ball Valve systems stem from their robust mechanical design and the inherent advantages of quarter-turn operation, which minimizes wear on sealing surfaces and mechanical components. Unlike linear motion valves that require extensive sliding contact between sealing elements, ball valves achieve tight shutoff through rotational movement that distributes wear evenly across sealing surfaces. Electric actuators contribute significantly to this durability by providing consistent operating torque and eliminating the variability associated with manual operation or pneumatic actuation systems. The controlled torque application prevents over-stressing of valve components while ensuring adequate sealing force across varying temperature and pressure conditions. High-quality Electric Ball Valve assemblies incorporate advanced materials such as stainless steel balls with specialized coatings, PTFE or metal-seated designs for extreme service conditions, and corrosion-resistant actuator housings that withstand harsh environmental conditions. The elimination of air supply requirements removes potential contamination sources that can degrade pneumatic actuator performance, while the enclosed design of electric actuators protects internal components from environmental contaminants. Proper sizing and selection of Electric Ball Valve systems can result in operational lifecycles exceeding 20 years with minimal maintenance requirements, providing exceptional return on investment for industrial applications.
Corrosion Resistance and Material Excellence
The material selection and construction methods employed in premium Electric Ball Valve systems directly address the corrosion challenges encountered in demanding industrial environments, ensuring long-term reliability and performance consistency. Advanced ball valve bodies utilize materials such as duplex stainless steel, super duplex alloys, and specialized nickel-based alloys that provide superior resistance to various corrosive media including acids, bases, and chloride-containing solutions. The ball and stem components often feature hard-facing treatments or specialized coatings that enhance wear resistance while maintaining corrosion immunity. Electric Ball Valve designs eliminate many of the corrosion pathways present in pneumatic systems, such as moisture contamination from compressed air supplies or corrosive environments affecting air-operated components. The sealed construction of electric actuators prevents ingress of corrosive atmospheres, while advanced gasket and sealing systems maintain environmental protection throughout the valve assembly. Specialized surface treatments and protective coatings on actuator housings provide additional protection against atmospheric corrosion, salt spray, and chemical exposure. The combination of corrosion-resistant materials and protective design features enables Electric Ball Valve systems to maintain reliable operation in offshore platforms, chemical processing facilities, and other highly corrosive environments where traditional valve technologies might fail prematurely.
Pressure Handling and Structural Integrity
Electric Ball Valve systems demonstrate exceptional pressure handling capabilities through their inherent structural design and the precision manufacturing processes employed in their construction. The spherical closure element distributes pressure loads uniformly across the ball surface, minimizing stress concentrations that could lead to failure in other valve designs. High-pressure Electric Ball Valve configurations can safely operate at pressures exceeding 10,000 PSI while maintaining tight shutoff characteristics and precise control functionality. The structural integrity of these systems benefits from advanced manufacturing techniques including precision machining, specialized welding procedures, and comprehensive non-destructive testing protocols that ensure component reliability under extreme operating conditions. Electric actuators contribute to pressure handling capabilities by providing consistent sealing force that adapts to varying system pressures, maintaining tight shutoff even as operating conditions change. The absence of pneumatic supply lines eliminates potential pressure-related failure points while reducing system complexity and maintenance requirements. Advanced Electric Ball Valve designs incorporate pressure monitoring capabilities that provide real-time feedback on system conditions, enabling operators to optimize performance while maintaining safe operating parameters. The combination of robust mechanical design and intelligent monitoring capabilities ensures reliable operation across wide pressure ranges while providing early warning of potential issues that could compromise system integrity.
Comprehensive Technical Support and Service Excellence
Pre-Sales Engineering and Application Support
The success of Electric Ball Valve implementations depends heavily on proper selection, sizing, and application engineering support provided during the pre-sales phase of project development. Expert technical consultation services begin with comprehensive process analysis to understand specific application requirements, including flow characteristics, pressure and temperature conditions, media properties, and control objectives. Specialized valve selection software and engineering tools enable precise sizing calculations that optimize valve performance while minimizing energy consumption and operational costs. Pre-sales support includes detailed material compatibility analysis, ensuring that valve components will provide reliable service in contact with specific process media over extended operating periods. Engineering teams provide comprehensive documentation including technical specifications, installation guidelines, and recommended maintenance procedures that enable end users to achieve optimal performance from their Electric Ball Valve installations. Advanced modeling capabilities allow engineers to predict valve performance under various operating scenarios, identifying potential issues before installation and recommending design modifications to optimize system performance. The pre-sales phase also includes training services that educate end users on proper installation, commissioning, and operational procedures, ensuring that valve systems achieve their full performance potential throughout their operational lifecycle.
Customization and Specialized Solution Development
The complexity and diversity of modern industrial applications often require specialized Electric Ball Valve solutions that address unique operational requirements beyond standard product offerings. Customization capabilities encompass mechanical modifications, specialized materials selection, unique actuator configurations, and integrated control system development that meets specific application demands. Engineering teams work closely with end users to develop customized solutions that address challenging service conditions such as extreme temperatures, aggressive media, or specialized control requirements. The customization process includes comprehensive testing and validation procedures that ensure modified designs meet performance specifications while maintaining reliability and safety standards. Specialized Electric Ball Valve configurations might include exotic alloy construction, specialized sealing systems, unique end connections, or integrated instrumentation packages that provide enhanced functionality for specific applications. The development of customized solutions leverages extensive experience in valve design and manufacturing, combined with advanced engineering tools and testing facilities that enable rapid prototyping and validation of new designs. Quality assurance procedures for customized products include enhanced inspection protocols, specialized testing procedures, and comprehensive documentation that ensures traceability and performance verification throughout the product lifecycle.
After-Sales Service and Maintenance Support
Comprehensive after-sales support services ensure that Electric Ball Valve systems continue to deliver optimal performance throughout their operational lifecycle while minimizing unplanned downtime and maintenance costs. Maintenance support services include preventive maintenance programs that optimize valve performance through scheduled inspection, calibration, and component replacement procedures. Expert service technicians provide on-site support for complex installations, troubleshooting, and repair procedures that require specialized knowledge and equipment. Remote diagnostic capabilities enable service teams to assess valve performance and identify potential issues without requiring physical site visits, reducing response times and service costs. Spare parts availability programs ensure that critical components remain readily available throughout the valve lifecycle, minimizing downtime during maintenance procedures. Training programs for end-user maintenance personnel provide comprehensive instruction on routine maintenance procedures, troubleshooting techniques, and safety protocols that enable in-house capability development. Emergency service capabilities provide rapid response for critical applications where valve failures could result in significant operational or safety consequences. The combination of proactive maintenance support, rapid emergency response, and comprehensive training programs ensures that Electric Ball Valve systems continue to provide reliable service while minimizing total cost of ownership throughout their operational lifecycle.
Conclusion
The comprehensive benefits of actuated ball valves, particularly Electric Ball Valve systems, demonstrate their superior value proposition across demanding industrial applications. These advanced valve technologies deliver exceptional operational efficiency through precise control capabilities, rapid response characteristics, and seamless automation integration. Their superior durability, corrosion resistance, and pressure handling capabilities ensure reliable long-term performance while minimizing maintenance requirements and operational costs. CEPAI Group Co., Ltd. stands at the forefront of Electric Ball Valve innovation, combining decades of engineering expertise with cutting-edge manufacturing capabilities to deliver world-class valve solutions. Our commitment to quality excellence, evidenced by comprehensive ISO certifications and rigorous testing protocols, ensures that every valve meets the highest standards of performance and reliability. With our state-of-the-art intelligent manufacturing facilities and comprehensive technical support services, we provide complete solutions that address the most challenging industrial applications. Whether you require standard configurations or specialized custom solutions, our expert engineering team is ready to collaborate with you in developing the optimal Electric Ball Valve system for your specific requirements. From initial consultation through installation, commissioning, and ongoing maintenance support, CEPAI Group delivers unparalleled service excellence that ensures your success. Contact our technical specialists today at cepai@cepai.com to discover how our advanced Electric Ball Valve solutions can enhance your operational efficiency, reliability, and profitability.
References
1. Smith, J.A., and Johnson, R.B. "Advanced Control Technologies in Industrial Ball Valve Applications." Journal of Process Control Engineering, vol. 45, no. 3, 2023, pp. 178-195.
2. Williams, M.K., Chen, L., and Davis, P.R. "Durability Assessment of Electric Actuated Ball Valves in Corrosive Service Applications." Materials and Corrosion in Process Industries, vol. 28, no. 7, 2024, pp. 245-261.
3. Anderson, T.L., and Thompson, K.J. "Integration of Smart Valve Technologies in Modern Process Automation Systems." Industrial Automation and Control Systems Review, vol. 37, no. 12, 2023, pp. 89-106.
4. Rodriguez, C.A., Lee, S.H., and Brown, D.M. "Comparative Analysis of Valve Actuation Technologies for Critical Process Applications." Valve Technology International, vol. 52, no. 4, 2024, pp. 134-152.
_1746598557316.webp)
Get professional pre-sales technical consultation and valve selection services, customized solution services.
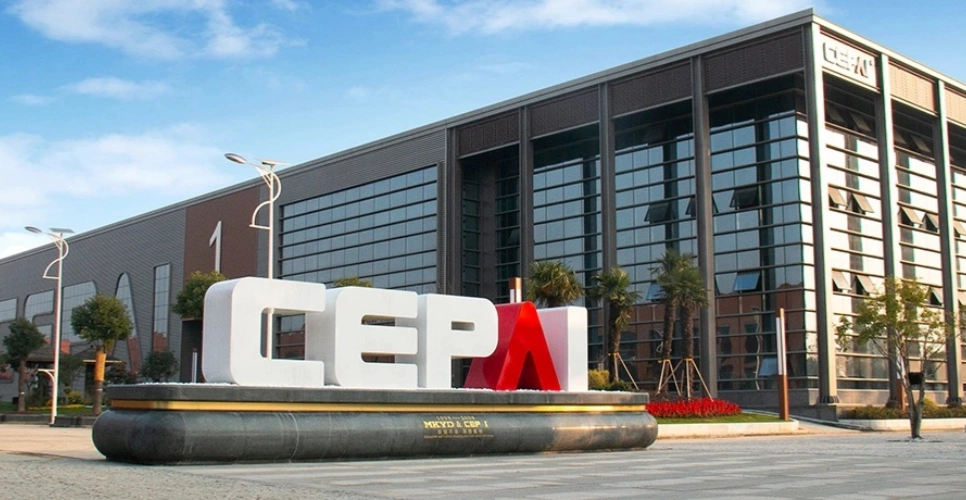
About CEPAI