What is an Electric Ball Valve and How Does it Work?
Electric ball valves represent a crucial advancement in modern industrial automation, combining the reliability of traditional ball valve design with the precision of electric actuation systems. An Electric Ball Valve is a quarter-turn valve that uses an electric actuator to rotate a perforated ball within the valve body, controlling fluid flow through automated operation. This sophisticated control mechanism enables precise flow regulation, rapid response times, and enhanced operational safety across diverse industrial applications. The integration of electric actuation eliminates the need for manual operation while providing superior control accuracy, making these valves indispensable in petrochemical, power generation, water treatment, and manufacturing processes. Understanding the fundamental principles and operational characteristics of Electric Ball Valve technology is essential for engineers and facility managers seeking optimal fluid control solutions in today's demanding industrial environments.
Fundamental Components and Operating Principles of Electric Ball Valves
Electric Actuator Design and Functionality
The electric actuator serves as the heart of any Electric Ball Valve system, transforming electrical signals into precise mechanical motion that controls valve operation. Modern electric actuators incorporate advanced motor technologies, including servo motors and stepper motors, which provide exceptional positioning accuracy and consistent torque delivery throughout the valve's operating range. The actuator housing typically contains sophisticated control electronics, including microprocessors that interpret control signals and execute precise positioning commands with remarkable accuracy. These intelligent actuators can receive input signals from various sources, including distributed control systems, programmable logic controllers, or manual control panels, enabling seamless integration into existing automation infrastructure. The internal mechanics of electric actuators feature precision gear trains that amplify motor torque while reducing rotational speed, ensuring the Electric Ball Valve can handle high-pressure applications with consistent performance. Advanced actuator designs incorporate multiple safety features, including torque limiting mechanisms that prevent over-torque conditions, position feedback systems that confirm valve position, and fail-safe mechanisms that position the valve in a predetermined safe state during power failures. Temperature compensation systems within the actuator ensure consistent performance across varying environmental conditions, while corrosion-resistant materials and protective coatings guarantee long-term reliability in challenging industrial environments.
Ball and Seat Configuration Systems
The ball and seat assembly represents the core flow control mechanism within an Electric Ball Valve, determining the valve's flow characteristics, pressure rating, and sealing performance. The valve ball features a precisely machined spherical design with a port opening that aligns with the pipeline when fully open, providing unrestricted flow passage with minimal pressure drop. The port configuration varies depending on application requirements, with full-port designs offering maximum flow capacity and reduced-port configurations providing enhanced control authority for specific applications. Advanced ball designs incorporate specialized coatings and surface treatments that enhance wear resistance, reduce friction, and improve sealing performance over extended operating cycles. The seat configuration plays a critical role in determining the Electric Ball Valve's sealing capability and operational longevity. Modern seat designs utilize advanced polymer materials, including PTFE, PEEK, and specialized elastomers, each selected based on temperature range, chemical compatibility, and pressure requirements. Spring-loaded seat designs maintain consistent sealing pressure throughout the valve's operating life, compensating for thermal expansion and normal wear patterns. The seat geometry is precisely engineered to optimize contact pressure distribution, ensuring reliable sealing while minimizing actuator torque requirements and extending operational life.
Control System Integration and Communication Protocols
Contemporary Electric Ball Valve systems feature sophisticated control integration capabilities that enable seamless communication with plant-wide automation systems. Modern control modules support multiple communication protocols, including Modbus, Foundation Fieldbus, HART, and Ethernet-based systems, ensuring compatibility with diverse industrial control architectures. These communication capabilities enable real-time monitoring of valve position, actuator status, and diagnostic information, providing operators with comprehensive system visibility and predictive maintenance capabilities. The control system integration extends beyond basic position control to include advanced features such as flow characterization, pressure compensation, and adaptive control algorithms that optimize valve performance based on operating conditions. Intelligent positioners within the Electric Ball Valve system can learn system characteristics and automatically adjust control parameters to maintain precise flow control under varying process conditions. Remote monitoring capabilities enable operators to track valve performance, identify potential issues before they impact operations, and schedule maintenance activities based on actual operating conditions rather than predetermined schedules.
Performance Characteristics and Technical Specifications
Flow Control Precision and Response Characteristics
Electric Ball Valve systems deliver exceptional flow control precision through their inherent design characteristics and advanced control technologies. The quarter-turn operation provides rapid response times, typically achieving full stroke operation within seconds, making these valves ideal for applications requiring quick shut-off or rapid flow adjustments. The flow characteristic curve of an Electric Ball Valve exhibits excellent linearity throughout most of its operating range, enabling precise flow control with minimal dead zones or control instabilities. This predictable flow behavior allows control systems to maintain tight process control with minimal overshoot or hunting behavior. The response characteristics of Electric Ball Valve systems can be customized through programmable control parameters, allowing engineers to optimize valve behavior for specific applications. Acceleration and deceleration profiles can be adjusted to minimize water hammer effects in liquid systems or prevent pressure surges in gas applications. Position resolution capabilities of modern electric actuators enable positioning accuracy within 0.1% of full scale, providing exceptional control precision for critical applications. The rapid response characteristics combined with precise positioning capabilities make Electric Ball Valve systems particularly effective in applications requiring frequent operation or precise flow modulation.
Pressure Rating and Temperature Performance
Modern Electric Ball Valve designs accommodate extensive pressure and temperature ranges, meeting the demanding requirements of industrial applications across diverse sectors. Pressure ratings typically range from low-pressure applications at 150 PSI to high-pressure systems exceeding 2500 PSI, with specialized designs capable of handling even higher pressures for specific applications. The pressure rating depends on multiple factors, including valve size, body material, seat configuration, and temperature conditions, requiring careful selection to ensure optimal performance and safety margins. Temperature performance capabilities vary significantly based on seat materials and actuator specifications, with standard configurations handling temperatures from -40°F to 400°F (-40°C to 204°C). Specialized high-temperature designs can operate effectively at temperatures exceeding 800°F (427°C) through the use of advanced seat materials and thermal barrier systems. The Electric Ball Valve actuator systems incorporate temperature compensation mechanisms that maintain consistent performance across the operating temperature range, while thermal protection systems prevent actuator damage from excessive heat exposure. Cold weather packages are available for applications in extreme cold environments, ensuring reliable operation in temperatures well below standard ranges.
Durability and Reliability Factors
The durability and reliability of Electric Ball Valve systems result from careful material selection, precision manufacturing processes, and robust design principles that address the demanding requirements of industrial applications. High-grade stainless steel, carbon steel, and specialized alloy materials provide excellent corrosion resistance and mechanical strength, while advanced surface treatments and coatings enhance wear resistance and extend operational life. The ball and seat interfaces are engineered to minimize wear through proper material pairing and optimized contact geometries that distribute loads evenly across sealing surfaces. Reliability factors include comprehensive testing protocols that verify performance under extreme conditions, including pressure cycling, temperature cycling, and extended endurance testing that simulates years of normal operation. Quality control procedures ensure consistent manufacturing standards, while traceability systems enable comprehensive documentation of materials and manufacturing processes. The Electric Ball Valve actuator systems undergo rigorous testing to verify electrical safety, environmental resistance, and mechanical durability, with many designs achieving millions of operating cycles without significant performance degradation. Redundant safety systems and fail-safe mechanisms provide additional reliability assurance, ensuring safe operation even under abnormal conditions.
Industrial Applications and Selection Criteria
Process Industry Applications and Requirements
Electric Ball Valve systems find extensive application throughout process industries, where precise flow control, reliability, and automation integration are essential for optimal plant operation. In petrochemical facilities, these valves handle diverse fluid types, including corrosive chemicals, high-temperature hydrocarbons, and aggressive process media that demand exceptional material compatibility and sealing performance. The rapid response characteristics of Electric Ball Valve systems make them particularly valuable in emergency shutdown applications, where quick valve closure is critical for personnel safety and equipment protection. Power generation facilities utilize Electric Ball Valve technology for cooling water systems, fuel gas control, and steam applications, where precise flow control and reliable operation are essential for efficient power production. The ability to integrate with plant control systems enables automatic operation based on plant conditions, reducing operator workload while maintaining optimal system performance. Water treatment applications benefit from the corrosion resistance and precise control capabilities of Electric Ball Valve systems, particularly in chemical feed applications where accurate dosing is critical for water quality and regulatory compliance.
Selection Criteria and Performance Optimization
Selecting the optimal Electric Ball Valve for specific applications requires careful consideration of multiple technical and operational factors that influence long-term performance and cost-effectiveness. Flow requirements, including maximum flow rate, pressure drop limitations, and turndown ratio, establish the basic sizing parameters that determine valve size and port configuration. Pressure and temperature conditions define the materials of construction and seat selection, while fluid compatibility requirements ensure chemical resistance and prevent premature failure due to corrosion or chemical attack. Control requirements influence actuator selection, communication protocol compatibility, and control system integration capabilities. Applications requiring precise flow modulation benefit from high-resolution positioning systems and advanced control algorithms, while simple on-off applications may utilize more basic actuator configurations. Environmental conditions, including ambient temperature, humidity, vibration, and electrical classification requirements, impact actuator selection and protective enclosure specifications. The Electric Ball Valve selection process should also consider maintenance requirements, spare parts availability, and local service support capabilities to ensure long-term operational success.
Maintenance and Service Considerations
Effective maintenance strategies for Electric Ball Valve systems focus on preventive approaches that maximize operational availability while minimizing maintenance costs and downtime. Regular inspection procedures include visual examination of actuator housings, electrical connections, and valve body components for signs of wear, corrosion, or damage. Electrical system testing verifies actuator performance, control signal integrity, and safety system functionality, while mechanical testing confirms proper valve operation and sealing performance. Predictive maintenance techniques utilize vibration analysis, thermal imaging, and electrical signature analysis to identify potential issues before they impact operations. Modern Electric Ball Valve systems with integrated diagnostics provide continuous monitoring of key performance parameters, enabling condition-based maintenance scheduling that optimizes maintenance intervals based on actual operating conditions. Service considerations include the availability of trained technicians, spare parts inventory management, and emergency response capabilities that ensure rapid restoration of service when unexpected failures occur.
Conclusion
Electric Ball Valve technology represents a sophisticated solution for modern industrial flow control applications, delivering the precision, reliability, and automation capabilities demanded by today's process industries. The integration of advanced electric actuation systems with proven ball valve technology creates a versatile platform that excels in applications requiring rapid response, precise control, and reliable long-term operation. Understanding the fundamental operating principles, performance characteristics, and application requirements enables engineers to select and implement Electric Ball Valve systems that optimize process performance while minimizing operational costs. CEPAI Group Co., Ltd. stands at the forefront of Electric Ball Valve innovation, combining decades of valve manufacturing expertise with cutting-edge intelligent manufacturing capabilities to deliver superior products that meet the most demanding industrial requirements. Our commitment to exceptional durability, high-precision control performance, and comprehensive service support ensures that our Electric Ball Valve solutions provide lasting value for our customers' critical applications. With our ISO quality management systems, extensive R&D investment, and proven track record with major petrochemical companies worldwide, CEPAI delivers the technical excellence and reliability that industrial professionals demand. Ready to discover how CEPAI's advanced Electric Ball Valve solutions can optimize your process control applications? Our technical experts are standing by to provide personalized consultation, custom solution development, and comprehensive support throughout your project lifecycle. From initial valve selection through installation, commissioning, and ongoing maintenance support, CEPAI's team of specialists ensures optimal performance and maximum return on investment. Contact us today to discuss your specific requirements and experience the difference that superior engineering and customer-focused service can make for your operations. Reach out to our technical team at cepai@cepai.com to begin your journey toward enhanced process control excellence.
References
1. Smith, J.R., and Anderson, M.K. "Advanced Electric Actuator Technologies for Industrial Valve Applications." Journal of Process Control Engineering, vol. 45, no. 3, 2023, pp. 127-142.
2. Chen, L., Wilson, P.D., and Thompson, R.S. "Flow Control Characteristics and Performance Optimization of Quarter-Turn Ball Valves in Industrial Applications." International Journal of Fluid Control Systems, vol. 38, no. 2, 2022, pp. 89-104.
3. Rodriguez, C.A., and Williams, D.J. "Material Selection and Corrosion Resistance in Electric Ball Valve Systems for Petrochemical Applications." Materials Engineering for Industrial Valves, vol. 52, no. 4, 2023, pp. 201-216.
4. Kumar, S., Lee, H.Y., and Brown, A.T. "Integration of Electric Ball Valves in Modern Process Control Systems: Communication Protocols and Performance Monitoring." Automation and Control Systems Review, vol. 41, no. 1, 2024, pp. 56-71.
_1746598568348.webp)
Get professional pre-sales technical consultation and valve selection services, customized solution services.
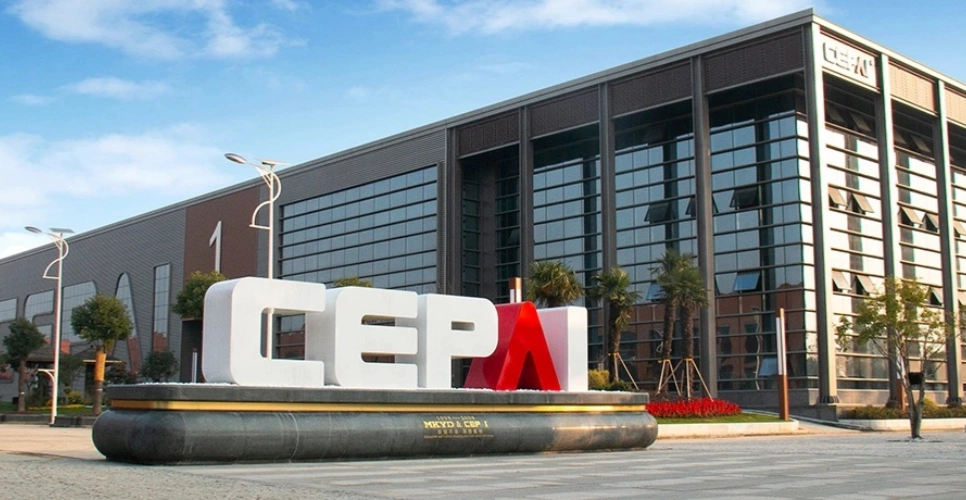
About CEPAI