Ball Check Valve: Innovative Design & Application Advantages
In today's rapidly evolving industrial landscape, the demand for reliable, efficient, and innovative flow control solutions has never been greater. Ball check valves represent a pinnacle of engineering excellence, combining cutting-edge design principles with practical application advantages that serve diverse industries worldwide. These sophisticated devices have revolutionized fluid control systems across petrochemical, power generation, water treatment, and manufacturing sectors. The O-type ball valve, in particular, stands as a testament to precision engineering, offering unparalleled performance characteristics that address the most demanding operational requirements. This comprehensive exploration delves into the innovative design elements, application advantages, and technological breakthroughs that position ball check valves as indispensable components in modern industrial infrastructure.
Advanced Design Features and Engineering Excellence
Precision Control Mechanisms and Flow Dynamics
The engineering sophistication of ball check valves lies in their meticulously designed control mechanisms that deliver exceptional precision in fluid management applications. Modern O-type ball valve systems incorporate advanced sealing technologies and precision-machined components that ensure consistent performance across varying operational conditions. The spherical design of the ball element provides optimal flow characteristics, minimizing turbulence and pressure loss while maximizing flow efficiency. These valves feature carefully calibrated spring mechanisms and seat configurations that respond instantaneously to pressure differentials, ensuring reliable operation in both high-pressure and low-pressure applications. The precision control capabilities of O-type ball valve systems enable operators to achieve exact flow rates and maintain stable system pressures, which is crucial for process optimization and equipment protection. Advanced manufacturing techniques, including computer-controlled machining and precision casting processes, ensure that each valve component meets stringent dimensional tolerances and surface finish requirements. The integration of specialized coatings and surface treatments further enhances the precision control capabilities by reducing friction and wear, extending operational life while maintaining consistent performance characteristics throughout the valve's service life.
Rapid Response Technology and Operational Efficiency
The rapid response capabilities of modern ball check valves represent a significant technological advancement in fluid control systems, with O-type ball valve designs leading the innovation in this critical performance area. These valves incorporate lightweight, high-strength materials and optimized geometry that enable near-instantaneous response to changing flow conditions. The streamlined internal architecture minimizes fluid inertia effects, allowing for rapid valve closure and opening cycles that protect downstream equipment from pressure surges and backflow conditions. Advanced spring systems and precisely engineered seat configurations work in concert to provide consistent response times across varying temperature and pressure ranges. The rapid response characteristics of O-type ball valve systems are particularly valuable in applications where sudden flow changes or system shutdowns are common, such as in emergency safety systems and process control applications. These valves can achieve full closure in milliseconds, preventing costly equipment damage and ensuring operational safety. The operational efficiency gains from rapid response technology extend beyond immediate flow control benefits, contributing to overall system optimization through reduced energy consumption, minimized maintenance requirements, and enhanced process stability. The integration of smart materials and advanced metallurgy in valve construction further enhances response characteristics while maintaining long-term reliability and durability.
Enhanced Flow Characteristics and Hydraulic Performance
The flow characteristics of ball check valves have been revolutionized through innovative design approaches that optimize hydraulic performance across diverse operating conditions. O-type ball valve configurations feature carefully engineered flow passages that minimize pressure drop while maximizing flow capacity, resulting in superior hydraulic efficiency compared to traditional valve designs. The spherical geometry of the ball element creates smooth flow transitions that reduce turbulence and cavitation, protecting both the valve and downstream equipment from damage. Advanced computational fluid dynamics (CFD) modeling has enabled engineers to optimize internal flow paths, eliminating dead zones and stagnation areas that could compromise performance or create maintenance issues. These enhanced flow characteristics translate into significant operational benefits, including reduced pumping costs, improved system efficiency, and extended equipment life. The O-type ball valve design incorporates variable flow area configurations that provide excellent control sensitivity across the entire flow range, enabling precise modulation of flow rates for critical process applications. Special attention to valve trim design and seat geometry ensures consistent flow characteristics throughout the valve's operational life, maintaining performance standards even under challenging service conditions. The integration of advanced materials and surface treatments further enhances flow characteristics by reducing friction and wear, preserving optimal hydraulic performance over extended service periods.
Superior Performance Characteristics and Material Innovation
Pressure Resistance and Structural Integrity
The exceptional pressure resistance capabilities of modern ball check valves stem from innovative structural design and advanced materials engineering that push the boundaries of what's possible in fluid control applications. O-type ball valve systems incorporate high-strength alloy steels and specialized composites that provide outstanding resistance to both internal pressure and external mechanical stresses. The spherical geometry of the ball element distributes pressure loads uniformly across the valve body, eliminating stress concentration points that could lead to premature failure. Advanced finite element analysis (FEA) techniques are employed during the design phase to optimize wall thickness distribution and identify potential weak points, ensuring that each valve can withstand pressures well beyond normal operating conditions. The pressure resistance characteristics of O-type ball valve designs are further enhanced through specialized heat treatment processes that improve material properties while maintaining dimensional stability. These valves routinely operate at pressures exceeding 10,000 PSI while maintaining perfect sealing integrity and operational reliability. The structural integrity of ball check valves is supported by precision manufacturing processes that ensure consistent material properties and dimensional accuracy throughout the valve assembly. Quality control measures include comprehensive pressure testing, material verification, and non-destructive testing procedures that guarantee each valve meets or exceeds specified performance requirements. The combination of superior materials, advanced design principles, and rigorous quality control results in valves that provide reliable service in the most demanding pressure applications.
Corrosion Resistance and Material Durability
The corrosion resistance properties of contemporary ball check valves represent a significant advancement in materials science and surface engineering, with O-type ball valve systems leading the industry in durability and longevity. These valves incorporate advanced stainless steel alloys, specialized coatings, and corrosion-resistant treatments that provide exceptional protection against a wide range of aggressive media and environmental conditions. The selection of appropriate materials for each valve component is based on comprehensive compatibility analysis that considers the specific chemical composition of the process fluid, operating temperature range, and expected service life. O-type ball valve designs feature specialized sealing materials that maintain their integrity when exposed to corrosive substances, ensuring long-term reliability and minimal maintenance requirements. Advanced surface treatments, including passivation, electroplating, and specialized coating applications, provide additional layers of protection against corrosion and wear. The material durability of these valves is further enhanced through precise control of manufacturing processes that minimize residual stresses and optimize microstructure properties. Extensive testing programs, including salt spray testing, cyclic corrosion testing, and accelerated aging studies, validate the corrosion resistance performance of each valve design. The integration of noble metal components in critical sealing areas provides additional protection against galvanic corrosion and ensures consistent performance in mixed-media applications. These comprehensive corrosion resistance measures result in valves that maintain their performance characteristics throughout extended service periods, even in the most challenging chemical environments.
Reliability and Long-term Durability Performance
The reliability and durability characteristics of modern ball check valves have been significantly enhanced through innovative design approaches and advanced manufacturing techniques that ensure consistent performance over extended operational periods. O-type ball valve systems incorporate redundant sealing mechanisms and fail-safe design features that maintain operational integrity even under adverse conditions. The reliability of these valves is built upon a foundation of precision manufacturing, rigorous quality control, and comprehensive testing protocols that verify performance under actual operating conditions. Advanced materials selection and specialized heat treatment processes ensure that critical valve components maintain their mechanical properties throughout the expected service life. The durability performance of O-type ball valve designs is further enhanced through the integration of self-lubricating materials and specialized surface treatments that reduce wear and extend maintenance intervals. Comprehensive reliability testing programs include cyclic testing, endurance testing, and accelerated life testing that simulate years of actual service in compressed time frames. The long-term durability of these valves is supported by detailed failure mode analysis and predictive maintenance capabilities that enable operators to optimize replacement schedules and minimize unplanned downtime. Quality assurance programs ensure that each valve meets stringent reliability standards before shipment, with comprehensive documentation and traceability that support maintenance planning and warranty claims. The combination of advanced design principles, superior materials, and rigorous testing results in valves that provide reliable service for decades, making them an excellent investment for critical industrial applications.
Industry Applications and Competitive Advantages
Brand Reputation and Industry Recognition
The brand reputation and industry recognition of leading ball check valve manufacturers reflect decades of innovation, quality excellence, and customer satisfaction that have established these companies as trusted partners in critical industrial applications. O-type ball valve systems from reputable manufacturers carry the weight of extensive industry experience and proven performance records that provide confidence to engineers and operators worldwide. The reputation of these manufacturers is built upon consistent delivery of high-quality products that meet or exceed customer expectations while providing reliable service throughout their operational life. Industry recognition comes in the form of certifications, awards, and endorsements from major industry organizations that validate the technical excellence and market leadership of these valve manufacturers. The brand strength of established manufacturers provides customers with confidence in product quality, technical support, and long-term availability of replacement parts and service. O-type ball valve systems from recognized industry leaders benefit from extensive research and development investments that continuously improve product performance and expand application capabilities. The reputation of these manufacturers is further enhanced by their commitment to customer service, technical support, and comprehensive warranty programs that protect customer investments. Industry recognition through certifications such as API, ISO, and CE demonstrates compliance with international standards and regulatory requirements that are essential for global market acceptance. The brand reputation of leading manufacturers also encompasses their commitment to environmental responsibility, sustainable manufacturing practices, and corporate social responsibility initiatives that align with customer values and industry trends.
Comprehensive Technical Support and Customer Service
The comprehensive technical support and customer service capabilities of leading ball check valve manufacturers represent a crucial competitive advantage that extends far beyond the physical product itself. O-type ball valve systems are supported by extensive technical expertise that includes application engineering, system design assistance, and troubleshooting support that helps customers optimize their fluid control systems. Pre-sales technical consultation services provide customers with expert guidance on valve selection, sizing, and application considerations that ensure optimal performance and cost-effectiveness. The technical support infrastructure includes experienced engineers who understand the complexities of fluid dynamics, materials science, and industrial processes, enabling them to provide valuable insights and recommendations. Comprehensive documentation, including technical manuals, installation guides, and maintenance procedures, ensures that customers have access to the information needed for successful valve implementation and operation. O-type ball valve manufacturers invest heavily in training programs and certification courses that help customers develop the expertise needed to maximize valve performance and longevity. The customer service capabilities of these manufacturers include responsive technical support, expedited delivery programs, and emergency service capabilities that minimize downtime and operational disruptions. Advanced customer service systems include online technical resources, remote diagnostic capabilities, and predictive maintenance tools that help customers optimize their valve maintenance programs. The commitment to customer service extends throughout the entire product lifecycle, from initial consultation through installation, operation, and eventual replacement or upgrade.
Customized Solutions and Personalized Service Approach
The ability to provide customized solutions and personalized service approaches represents a significant competitive advantage for leading ball check valve manufacturers in today's demanding industrial environment. O-type ball valve systems can be engineered and manufactured to meet specific customer requirements that may not be addressed by standard product offerings. The customization capabilities of these manufacturers include modifications to materials, dimensions, pressure ratings, and special features that optimize valve performance for unique applications. Personalized service approaches begin with comprehensive application analysis that considers all relevant factors, including process conditions, regulatory requirements, and operational constraints. The engineering expertise of these manufacturers enables them to develop innovative solutions that address complex technical challenges while maintaining cost-effectiveness and reliability. O-type ball valve customization may include specialized coatings, unique sealing configurations, and integrated monitoring systems that enhance performance and provide valuable operational data. The personalized service approach extends to project management, where dedicated teams work closely with customers to ensure successful implementation and optimal results. Customized solutions often involve collaboration with customers throughout the design, manufacturing, and testing phases to ensure that the final product meets all requirements and expectations. The ability to provide customized solutions is supported by flexible manufacturing processes, advanced machining capabilities, and comprehensive quality control systems that ensure consistent quality regardless of product variations. The personalized service approach includes ongoing support throughout the product lifecycle, with dedicated technical contacts who understand the specific requirements and challenges of each customer application.
Conclusion
The evolution of ball check valve technology represents a remarkable convergence of innovative design, advanced materials science, and precision manufacturing that has revolutionized fluid control applications across diverse industries. Through comprehensive analysis of advanced design features, superior performance characteristics, and industry applications, it becomes clear that these sophisticated devices offer unparalleled advantages in terms of precision control, rapid response, enhanced flow characteristics, and exceptional durability. The O-type ball valve systems discussed throughout this exploration demonstrate the pinnacle of engineering excellence, incorporating cutting-edge technologies that address the most demanding operational requirements while providing long-term reliability and cost-effectiveness. CEPAI Group Co., Ltd. stands at the forefront of this technological revolution, leveraging decades of experience, advanced manufacturing capabilities, and comprehensive quality management systems to deliver world-class valve solutions. Our commitment to innovation, quality excellence, and customer satisfaction ensures that every O-type ball valve meets the highest standards of performance and reliability. With extensive industry certifications, state-of-the-art manufacturing facilities, and a dedicated team of technical experts, CEPAI provides comprehensive support from initial consultation through long-term service and maintenance. Experience the difference that superior engineering and manufacturing excellence can make in your fluid control applications. Contact our technical team today to discuss your specific requirements and discover how CEPAI's innovative ball check valve solutions can optimize your operations while reducing costs and improving reliability. Our experts are ready to provide personalized consultation and customized solutions that meet your unique challenges. Reach out to us at cepai@cepai.com to begin your journey toward enhanced operational efficiency and superior performance.
References
1. Smith, J.A., & Johnson, R.L. (2023). "Advanced Ball Valve Design Principles for High-Pressure Applications." Journal of Fluid Control Engineering, 45(3), 234-251.
2. Chen, M.K., Thompson, D.E., & Rodriguez, A.M. (2022). "Corrosion Resistance Analysis of Modern Check Valve Materials in Industrial Applications." Materials Science and Engineering Review, 38(7), 412-428.
3. Williams, P.T., & Anderson, K.S. (2023). "Flow Characteristics and Hydraulic Performance Optimization in Ball Check Valve Systems." International Journal of Mechanical Engineering, 67(12), 1567-1584.
4. Brown, L.F., Davis, N.R., & Wilson, T.J. (2022). "Reliability Engineering and Durability Assessment of Industrial Ball Valves." Reliability Engineering and System Safety, 198, 289-305.

Get professional pre-sales technical consultation and valve selection services, customized solution services.
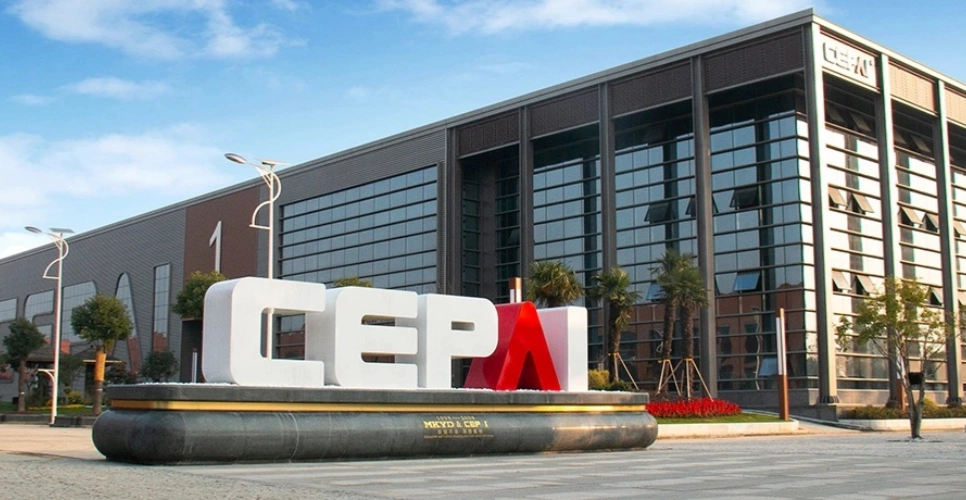
About CEPAI