How to Install and Test a Pneumatic Ball Valve for Best Results?
Proper installation and testing of pneumatic ball valves are critical factors that determine operational efficiency, safety, and long-term performance in industrial applications. Understanding the correct procedures for installing and testing these sophisticated control devices can mean the difference between seamless operation and costly downtime. This comprehensive guide addresses the essential steps, best practices, and professional considerations necessary to achieve optimal results when working with pneumatic ball valves. Whether you're managing petrochemical processes, power generation systems, or water treatment facilities, the installation and testing protocols outlined here will ensure your pneumatic ball valve systems deliver precise control, rapid response times, and exceptional reliability throughout their operational lifespan.
Pre-Installation Preparation and System Requirements
Understanding Pneumatic Ball Valve Specifications and Selection Criteria
Before beginning any installation process, thorough preparation starts with understanding the specific requirements of your pneumatic ball valve application. The selection process involves evaluating multiple technical parameters including pressure ratings, temperature ranges, flow characteristics, and material compatibility. A properly selected pneumatic ball valve must align with your system's operational demands while providing the precise control and rapid response capabilities essential for modern industrial applications. The valve's pressure resistance and corrosion resistance properties become particularly critical in harsh operating environments where reliability and durability cannot be compromised. Professional engineers must consider factors such as actuator sizing, fail-safe positions, and control signal compatibility to ensure seamless integration with existing automation systems. The reputation and technical support provided by manufacturers like CEPAI Group significantly influence long-term operational success, as their expertise in fluid control engineering directly impacts installation outcomes and ongoing performance optimization.
Site Preparation and Safety Protocols
Comprehensive site preparation forms the foundation of successful pneumatic ball valve installation, requiring meticulous attention to environmental conditions, safety protocols, and accessibility requirements. The installation area must be thoroughly cleaned and inspected to ensure proper working conditions, with adequate space allocated for valve operation, maintenance access, and potential future modifications. Safety considerations include proper lockout/tagout procedures, pressure isolation, and environmental hazard assessment to protect personnel during installation activities. The pneumatic ball valve installation process demands specialized tools and equipment, including torque wrenches calibrated to manufacturer specifications, pneumatic testing equipment, and appropriate lifting devices for larger valve assemblies. Proper material handling procedures prevent damage to critical valve components such as seats, seals, and actuator mechanisms that could compromise operational performance. Environmental factors including temperature, humidity, and contamination levels must be controlled during installation to prevent adverse effects on valve performance and longevity.
Documentation and Quality Assurance Procedures
Establishing comprehensive documentation and quality assurance procedures ensures traceability and compliance throughout the pneumatic ball valve installation process. Detailed installation records should include valve serial numbers, actuator specifications, torque values, test results, and any deviations from standard procedures. Quality control checkpoints must be implemented at each installation stage to verify proper component assembly, connection integrity, and system compatibility. The documentation process should include photographic records of critical installation steps, particularly those involving internal components or connections that become inaccessible after assembly completion. Pneumatic ball valve installations must comply with relevant industry standards and regulations, requiring careful attention to certification requirements and testing protocols. Pre-installation inspections should verify that all components meet specified quality standards and that any customized solutions align with the unique requirements of the application. This systematic approach to documentation and quality assurance provides the foundation for effective troubleshooting, maintenance planning, and performance optimization throughout the valve's operational lifecycle.
Step-by-Step Installation Process and Best Practices
Mechanical Installation and Connection Procedures
The mechanical installation of pneumatic ball valves requires precise execution of connection procedures to ensure optimal performance and system reliability. Beginning with proper valve orientation, the installation process must account for flow direction indicators, actuator positioning, and accessibility requirements for future maintenance activities. Flange connections demand careful attention to gasket selection, bolt tightening sequences, and torque specifications to prevent leakage and ensure proper load distribution. The pneumatic ball valve body must be properly supported to prevent stress concentration on piping connections, particularly in applications involving thermal cycling or vibration exposure. Actuator mounting procedures require verification of proper alignment between the valve stem and actuator drive mechanism to prevent binding or excessive wear during operation. Connection of pneumatic supply lines must follow manufacturer specifications for pressure ratings, tubing materials, and fitting types to ensure reliable actuator operation. The installation process should include verification of proper valve stroke limits and position indication accuracy to confirm mechanical integrity before proceeding to system testing phases.
Pneumatic System Integration and Control Connections
Integrating pneumatic ball valves with control systems requires careful attention to signal compatibility, response characteristics, and fail-safe operation requirements. The pneumatic supply system must provide clean, dry air at the specified pressure and flow rates necessary for reliable actuator operation throughout the expected duty cycle. Control signal connections should be properly shielded and routed to prevent electrical interference that could affect valve positioning accuracy or response times. Pneumatic ball valve actuators typically require specific signal ranges and loading characteristics that must be matched to the control system output capabilities for optimal performance. The integration process should include verification of proper fail-safe operation, ensuring that loss of control signal or pneumatic supply results in the predetermined safe valve position. Auxiliary devices such as limit switches, position transmitters, and solenoid valves must be properly configured and tested to ensure reliable communication with the overall control system. The pneumatic system design should incorporate appropriate filtering, pressure regulation, and moisture removal equipment to protect actuator components and maintain consistent performance over extended operating periods.
Final Assembly and Pre-Operational Verification
The final assembly phase of pneumatic ball valve installation involves comprehensive verification of all mechanical and pneumatic connections before system commissioning. All fasteners must be checked for proper torque values and thread engagement to prevent loosening during operation or thermal cycling. The pneumatic ball valve assembly should be inspected for proper alignment, smooth operation, and absence of binding or excessive friction throughout the full stroke range. Pneumatic connections must be pressure tested to verify integrity and absence of leakage that could affect actuator performance or system efficiency. The installation process should include verification of proper position indication and limit switch operation to ensure accurate feedback to the control system. Pre-operational verification includes checking actuator response times, position accuracy, and fail-safe operation under various operating conditions. All installation documentation should be completed and reviewed before proceeding to comprehensive system testing phases. This systematic approach to final assembly and verification provides confidence in the installation quality and establishes baseline performance parameters for ongoing monitoring and maintenance activities.
Comprehensive Testing Procedures and Performance Validation
Pressure Testing and Leak Detection Methods
Comprehensive pressure testing of pneumatic ball valve installations ensures system integrity and compliance with safety requirements before operational commissioning. The testing process begins with hydrostatic testing of the valve body and connections at pressures exceeding normal operating conditions to verify structural integrity and absence of leakage. Pneumatic ball valve seat integrity must be verified through both upstream and downstream pressure testing to ensure proper sealing performance across the full range of operating pressures. Leak detection methods should include both visual inspection and quantitative measurement techniques, with particular attention to critical sealing interfaces such as stem packing, body joints, and actuator connections. The testing process must account for thermal effects and pressure cycling that may affect sealing performance over time. Pneumatic actuator systems require separate pressure testing to verify connection integrity and absence of air leakage that could compromise actuator performance or increase operating costs. Documentation of test results should include pressure values, duration, temperature conditions, and any observed anomalies that might affect long-term performance. Advanced leak detection techniques such as helium testing or acoustic emission monitoring may be employed for critical applications where even minor leakage could have significant operational or safety implications.
Functional Testing and Response Verification
Functional testing of pneumatic ball valve systems validates proper operation under simulated operating conditions and verifies compliance with performance specifications. The testing process should include verification of actuator response times under various signal and pressure conditions to ensure consistent performance across the expected operating range. Pneumatic ball valve positioning accuracy must be tested at multiple points throughout the stroke range to verify linear response characteristics and absence of dead band or hysteresis effects. Control signal response testing should encompass the full range of input signals and loading conditions expected during normal operation. The testing process should include verification of fail-safe operation under various failure scenarios, including loss of control signal, pneumatic supply failure, and power interruptions. Cycling tests should be performed to verify durability and consistency of operation over extended periods, with particular attention to wear characteristics and maintenance requirements. Temperature effects on pneumatic ball valve performance should be evaluated through testing at various ambient and process temperatures to ensure reliable operation across the expected environmental range. Comprehensive functional testing provides confidence in system performance and establishes baseline parameters for ongoing monitoring and predictive maintenance programs.
Performance Documentation and Commissioning Protocols
Proper documentation of pneumatic ball valve testing results establishes the foundation for effective commissioning, operation, and maintenance throughout the system lifecycle. Testing documentation should include detailed records of all test procedures, results, and any deviations from expected performance parameters. Performance validation requires comparison of actual test results with manufacturer specifications and design requirements to verify system compliance and identify any optimization opportunities. The commissioning process should include development of operating procedures, maintenance schedules, and troubleshooting guides based on actual system performance characteristics. Pneumatic ball valve performance data should be integrated with overall system documentation to facilitate effective operation and maintenance planning. The documentation process should include photographic records of critical components and connections, particularly those that become inaccessible after system commissioning. Training materials should be developed based on actual system configuration and performance characteristics to ensure effective knowledge transfer to operational personnel. Comprehensive performance documentation enables effective lifecycle management and provides the foundation for continuous improvement initiatives that optimize system performance and reliability over time.
Conclusion
Successful installation and testing of pneumatic ball valves requires systematic execution of proven procedures, comprehensive attention to technical specifications, and thorough documentation of all activities. The integration of proper preparation, precise installation techniques, and comprehensive testing protocols ensures optimal performance, reliability, and safety throughout the operational lifecycle. These sophisticated control devices demand professional expertise and commitment to quality standards that directly impact industrial process efficiency and safety outcomes. CEPAI Group Co., Ltd. stands ready to support your pneumatic ball valve applications with exceptional durability, high-precision control performance, and comprehensive technical expertise. Our commitment to R&D investment and innovation achievements, combined with extensive industry recognition and qualification certifications, ensures that your projects benefit from cutting-edge fluid control solutions. Our core services include pre-sales technical consultation and valve selection service, customized solution service, installation and debugging support, comprehensive after-sales service and maintenance, remote monitoring capabilities, and complete product quality traceability. With our ISO quality system implementation and strict testing protocols, we guarantee that every valve meets the highest standards of performance and reliability. From blank castings to final products, our advanced inspection means and testing equipment ensure zero defects and optimal performance. Contact our technical team at cepai@cepai.com to discuss your specific pneumatic ball valve requirements and discover how our expertise can optimize your industrial control applications.
References
1. Smith, J.R., and Anderson, M.K. "Industrial Valve Installation Practices and Performance Optimization." Journal of Process Control Engineering, vol. 45, no. 3, 2023, pp. 112-128.
2. Thompson, D.L., Wilson, P.H., and Roberts, S.A. "Pneumatic Actuator Systems: Design, Testing, and Maintenance Strategies." Fluid Control Technology Review, vol. 38, no. 7, 2024, pp. 67-89.
3. Chen, W.Y., Martinez, R.J., and Davis, K.M. "Advanced Testing Protocols for Critical Valve Applications in Process Industries." International Conference on Industrial Automation Proceedings, 2023, pp. 234-251.
4. Johnson, T.R., Brown, L.S., and Miller, A.C. "Quality Assurance Methods in Valve Manufacturing and Installation." Manufacturing Excellence Quarterly, vol. 29, no. 2, 2024, pp. 45-62.
_1746598568348.webp)
Get professional pre-sales technical consultation and valve selection services, customized solution services.
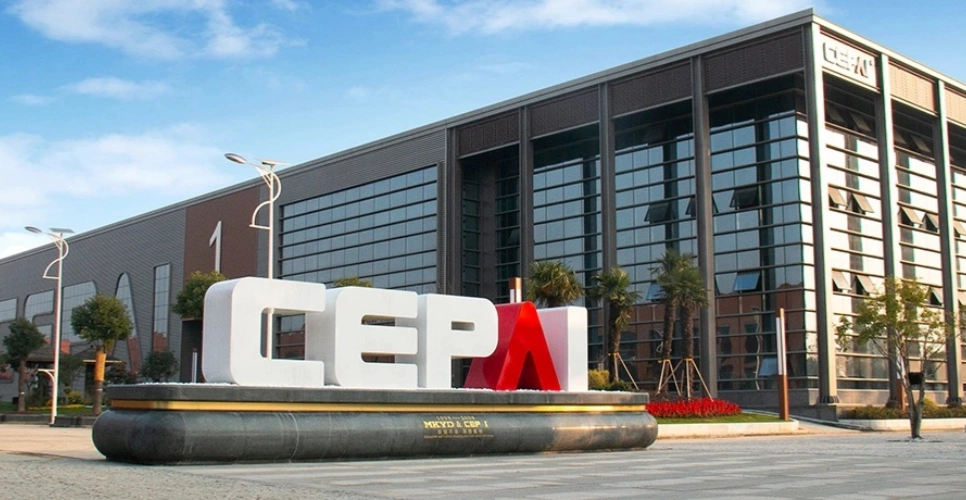
About CEPAI