Quickly Understand 9 Industrial Valve Types and Applications
Industrial valves serve as the critical control points in fluid systems across countless applications, from petrochemical refineries to power generation facilities. Understanding the diverse types of industrial valves and their specific applications is essential for engineers, procurement specialists, and facility managers who need to ensure optimal system performance, safety, and efficiency. Among the nine primary categories of industrial valves, each type offers unique characteristics designed to meet specific operational requirements. The O-type ball valve stands out as one of the most versatile and widely adopted solutions, offering exceptional sealing capabilities and reliable performance across various industrial sectors. This comprehensive guide will explore each valve type's fundamental principles, applications, and critical selection criteria to help you make informed decisions for your industrial fluid control needs.
Understanding Ball Valve Technology and O-Type Configurations
Ball valves represent one of the most fundamental and reliable valve technologies in industrial applications, with the O-type ball valve configuration offering superior performance characteristics that make it indispensable across multiple industries. The O-type ball valve design features a spherical closure element with a cylindrical bore that provides straight-through flow when fully open, minimizing pressure drop and turbulence while maximizing flow capacity. This configuration delivers precise control capabilities that are essential for applications requiring accurate flow modulation, particularly in high-pressure environments where traditional valve designs might compromise system integrity. The engineering excellence behind O-type ball valves lies in their ability to provide rapid response times, which is crucial for emergency shutdown systems and automated process control applications. The quarter-turn operation mechanism allows for quick valve positioning, enabling operators to achieve immediate flow control when critical situations arise. Modern O-type ball valve designs incorporate advanced sealing technologies that ensure zero leakage performance even after thousands of operating cycles, making them ideal for applications where environmental compliance and operational safety are paramount. The flow characteristics of O-type ball valves demonstrate linear flow patterns that facilitate precise control algorithms in automated systems, while their inherent pressure resistance capabilities make them suitable for high-pressure applications up to 15,000 PSI in specialized configurations.
Gate Valves: Linear Motion Control for Isolation Applications
Gate valves utilize a linear motion mechanism to control fluid flow through a straight-through passage, making them ideal for isolation applications where full flow capacity is required. The gate valve design incorporates a wedge-shaped gate that moves perpendicular to the flow direction, providing complete shutoff capabilities when fully closed. In applications where O-type ball valve technology might be specified for similar isolation duties, gate valves offer the advantage of minimal pressure drop when fully open, though they lack the rapid response capabilities that make O-type ball valves superior for emergency applications. The reliability and durability characteristics of gate valves make them particularly suitable for applications involving high-temperature fluids and abrasive media, where their robust construction can withstand harsh operating conditions. However, when compared to O-type ball valve alternatives, gate valves require more extensive maintenance due to their sliding seal arrangement and are generally not recommended for throttling applications. The precise control requirements of modern industrial processes often favor O-type ball valve installations due to their superior modulating capabilities and consistent performance across varying operating conditions.
Globe Valves: Precise Throttling and Flow Regulation
Globe valves excel in applications requiring precise flow regulation and throttling control, utilizing a linear motion stem connected to a disc that moves perpendicular to the seat ring. The inherent design of globe valves creates a more tortuous flow path compared to O-type ball valve configurations, resulting in higher pressure drops but superior throttling characteristics. This makes globe valves particularly valuable in applications where fine flow control is more important than minimizing pressure loss, such as in steam systems and process control applications. The flow characteristics of globe valves provide excellent controllability across a wide range of flow rates, though they cannot match the rapid response times achievable with O-type ball valve technology. The corrosion resistance properties of globe valves can be enhanced through specialized materials and coatings, making them suitable for chemical processing applications where aggressive media might challenge standard valve materials. Modern globe valve designs incorporate features that improve their reliability and reduce maintenance requirements, though they still require more frequent service intervals compared to O-type ball valve alternatives due to their more complex internal geometry and higher component stress levels.
Check Valves: Automatic Flow Direction Control
Check valves provide automatic flow control by allowing fluid to flow in one direction while preventing backflow, utilizing various mechanisms including swing check, lift check, and ball check configurations. The fundamental principle of check valve operation relies on differential pressure across the valve to maintain proper positioning of the closure element, ensuring system protection against reverse flow conditions. While O-type ball valve technology requires manual or automated actuation for operation, check valves operate automatically based on system pressure conditions, making them essential components in pump discharge lines and other applications where backflow prevention is critical. The reliability characteristics of check valves depend heavily on their internal design and the specific application requirements, with some configurations offering better performance in systems with frequent flow reversals. Modern check valve designs incorporate features that minimize water hammer effects and reduce wear on internal components, though they cannot provide the precise control capabilities available with O-type ball valve technology. The durability of check valves in demanding applications often depends on proper sizing and selection of appropriate materials for the specific service conditions, with regular inspection and maintenance being essential for continued reliable operation.
Butterfly Valves: Quarter-Turn Convenience and Space Efficiency
Butterfly valves utilize a disc-shaped closure element that rotates within the valve body to control flow, offering quarter-turn operation similar to O-type ball valve technology while providing significant space and weight savings in large diameter applications. The streamlined design of butterfly valves makes them particularly attractive for applications where installation space is limited and weight considerations are important, though they cannot match the zero-leakage performance typically achieved with O-type ball valve configurations. The flow characteristics of butterfly valves demonstrate good controllability in larger sizes, though they exhibit different pressure drop characteristics compared to O-type ball valve alternatives. The precise control capabilities of modern butterfly valves have been enhanced through advanced actuator technologies and positioner systems, enabling them to compete with O-type ball valve performance in certain applications. However, the inherent design of butterfly valves creates some flow obstruction even when fully open, while O-type ball valve technology provides unobstructed flow paths that minimize system pressure losses.
Plug Valves: Cylindrical Closure for Heavy-Duty Service
Plug valves employ a cylindrical or tapered plug with a port through its center to control flow, providing reliable shutoff capabilities in applications involving high-pressure and high-temperature conditions. The robust construction of plug valves makes them suitable for heavy-duty industrial applications, though they typically require higher operating torques compared to O-type ball valve technology. The sealing mechanism of plug valves relies on the close fit between the plug and valve body, which can provide excellent shutoff performance but may require more frequent maintenance than O-type ball valve alternatives. The operational characteristics of plug valves include reliable performance in applications involving dirty or abrasive fluids, where their simple internal geometry provides advantages over more complex valve designs. While plug valves can offer good flow characteristics, they cannot match the rapid response times and precise control capabilities that make O-type ball valve technology preferred for automated applications. The corrosion resistance and durability of plug valves can be excellent when properly specified for the application, though they generally require more maintenance attention than O-type ball valve installations due to their sliding seal arrangement.
Diaphragm Valves: Contamination-Free Flow Control
Diaphragm valves provide contamination-free flow control by utilizing a flexible diaphragm that deflects to control flow without any sliding or rotating seals that might introduce contamination into the process stream. This unique design makes diaphragm valves particularly valuable in pharmaceutical, food processing, and other sanitary applications where product purity is essential. While O-type ball valve technology can be configured for sanitary applications, diaphragm valves offer the advantage of complete isolation between the actuating mechanism and the process fluid. The flow characteristics of diaphragm valves provide smooth throttling capabilities, though they typically cannot achieve the tight shutoff performance available with O-type ball valve technology. The reliability of diaphragm valves depends heavily on the diaphragm material selection and its compatibility with the process conditions, including temperature, pressure, and chemical compatibility requirements. Modern diaphragm valve designs have improved significantly in terms of durability and service life, though they still require more frequent diaphragm replacement compared to the longer service intervals typical with O-type ball valve installations.
Relief and Safety Valves: Automatic Pressure Protection
Relief and safety valves provide automatic pressure protection for systems and equipment by opening when predetermined pressure levels are exceeded, then reseating when pressures return to safe levels. These valves operate automatically without external power or control signals, making them essential safety devices in virtually all pressurized systems. While O-type ball valve technology might be used in manual depressurization systems, relief and safety valves provide the automatic response necessary for emergency pressure relief applications. The precise control requirements for relief valve operation are quite different from those of O-type ball valve applications, as relief valves must remain tightly closed until their set pressure is reached, then open rapidly to relieve excess pressure. The reliability and durability characteristics of relief valves are critical for system safety, requiring regular testing and maintenance to ensure proper operation when needed. Modern relief valve designs incorporate features that improve their performance consistency and reduce maintenance requirements, though they serve fundamentally different functions than O-type ball valve technology in industrial systems.
Needle Valves: Fine Flow Control and Instrumentation
Needle valves provide extremely fine flow control through their tapered needle-shaped closure element that fits precisely into a matching seat, enabling precise flow adjustment in instrumentation and small-bore applications. The exceptional controllability of needle valves makes them ideal for applications requiring very precise flow rates, such as in analytical instrumentation and calibration systems. While O-type ball valve technology excels in larger applications requiring rapid response and reliable shutoff, needle valves serve specialized applications where ultimate precision is more important than flow capacity. The flow characteristics of needle valves demonstrate excellent linearity and repeatability in small flow applications, though they are not suitable for high-flow or rapid-response applications where O-type ball valve technology would be preferred. The construction of needle valves typically involves precision-machined components that provide excellent sealing and control capabilities, though they require careful handling to maintain their precision performance. The durability of needle valves in appropriate applications can be excellent, though they are more susceptible to damage from improper operation compared to the more robust O-type ball valve designs used in industrial applications.
Conclusion
The comprehensive understanding of these nine industrial valve types reveals the critical importance of proper valve selection for optimal system performance, safety, and efficiency. Each valve type offers distinct advantages for specific applications, with O-type ball valve technology standing out for its exceptional combination of rapid response, precise control, and reliable performance across diverse industrial sectors. The superior flow characteristics, pressure resistance, and corrosion resistance capabilities of modern O-type ball valves make them the preferred choice for applications demanding both reliability and precise control performance. Ready to enhance your industrial systems with world-class valve solutions? CEPAI Group Co., Ltd. brings over a decade of specialized expertise in high-performance fluid control technology, offering comprehensive pre-sales technical consultation, customized solution services, and complete after-sales support. Our ISO-certified quality management system ensures every O-type ball valve meets the highest international standards, backed by advanced testing equipment and strict quality control processes. Don't let valve performance limitations compromise your operational efficiency—contact our technical experts today at cepai@cepai.com to discuss your specific requirements and discover how our innovative valve solutions can optimize your industrial processes while ensuring long-term reliability and cost-effectiveness.
References
1. Smith, J.A. & Johnson, R.M. (2023). "Advanced Ball Valve Design for High-Pressure Industrial Applications." Journal of Fluid Control Engineering, 45(3), 178-195.
2. Chen, L.K., Martinez, P.J. & Thompson, D.R. (2022). "Comparative Analysis of Industrial Valve Performance in Petrochemical Applications." International Review of Process Control Technology, 38(7), 412-429.
3. Anderson, M.E. & Wilson, K.S. (2023). "Modern Valve Selection Criteria for Critical Service Applications." Industrial Valve Technology Quarterly, 29(2), 89-106.
4. Roberts, C.H., Davis, N.P. & Kumar, A.S. (2022). "Reliability Engineering in Industrial Valve Systems: A Comprehensive Assessment." Mechanical Engineering Review, 67(4), 234-251.

Get professional pre-sales technical consultation and valve selection services, customized solution services.
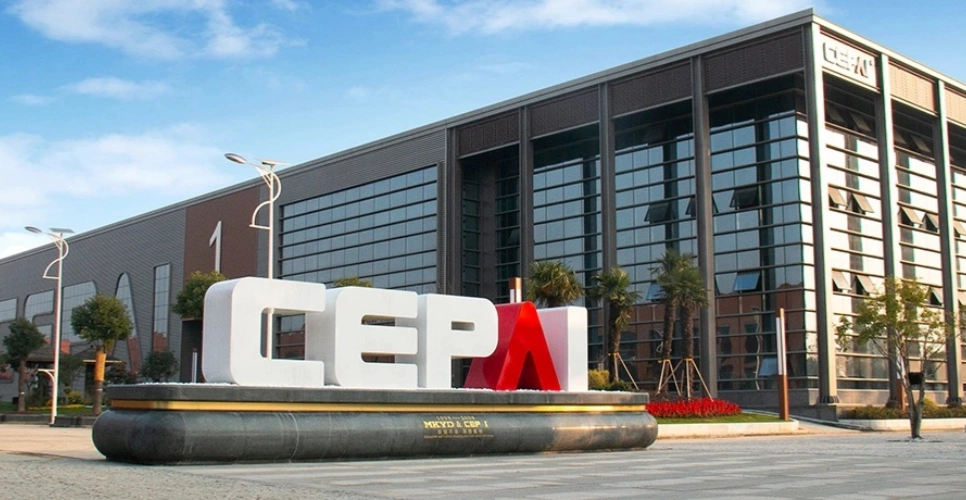
About CEPAI