How to Ensure a Leak-Free Pneumatic Ball Valve Installation?
Achieving a leak-free pneumatic ball valve installation is crucial for maintaining system integrity, preventing costly downtime, and ensuring operational safety across industrial applications. Proper installation techniques, combined with high-quality components and meticulous attention to detail, form the foundation of reliable valve performance. A pneumatic ball valve requires precise alignment, appropriate sealing methods, and thorough testing protocols to guarantee optimal functionality. The installation process involves careful consideration of pipe preparation, valve orientation, actuator positioning, and comprehensive system testing. Understanding these critical factors and implementing best practices ensures long-term reliability and prevents the common pitfalls that lead to system failures and expensive maintenance requirements.
Pre-Installation Preparation and Planning
System Assessment and Valve Selection
The foundation of any successful pneumatic ball valve installation begins with thorough system assessment and proper valve selection. Engineers must evaluate the specific operating conditions, including pressure requirements, temperature ranges, flow characteristics, and media compatibility. A pneumatic ball valve must be precisely matched to the application's demands, considering factors such as pressure ratings, material construction, and size specifications. The assessment should include detailed analysis of the existing piping system, available space for installation, and accessibility requirements for future maintenance. Proper valve selection involves understanding the relationship between flow coefficients, pressure drops, and system performance requirements. Additionally, considerations for environmental factors, such as ambient temperature fluctuations and potential corrosive atmospheres, play crucial roles in determining the appropriate valve specifications. The selection process should also account for the pneumatic actuator's power requirements, air supply quality, and control signal compatibility with existing automation systems.
Pipe Preparation and Alignment Standards
Meticulous pipe preparation forms the cornerstone of leak-free pneumatic ball valve installation. The piping system must be thoroughly cleaned, inspected, and prepared according to industry standards before valve installation begins. Proper pipe alignment is critical, as misalignment can create stress concentrations that lead to premature seal failure and system leakage. The preparation process involves removing all debris, scale, and foreign materials from the pipe interior, ensuring smooth surfaces that promote proper sealing. Pipe ends must be cut square and deburred to prevent damage to valve seals during installation. The pneumatic ball valve requires precise alignment with the piping system to prevent binding, uneven stress distribution, and premature wear of internal components. Alignment tools and techniques should be employed to ensure the valve centerline matches the pipe centerline within acceptable tolerances. Additionally, proper support structures must be installed to prevent pipe strain from affecting valve operation and seal integrity.
Tools and Equipment Requirements
Successful pneumatic ball valve installation demands specialized tools and equipment designed for precision work and safety. The installation team must have access to appropriate lifting equipment, alignment tools, torque wrenches, and testing apparatus. Proper tooling ensures accurate positioning, prevents damage during installation, and facilitates thorough testing procedures. Essential equipment includes pipe alignment tools, gasket installation devices, and pneumatic testing equipment capable of verifying system integrity. The pneumatic ball valve installation requires specific torque specifications for flange bolts, and calibrated torque wrenches are essential for achieving proper sealing force without over-stressing components. Additionally, safety equipment, including personal protective equipment and emergency response tools, must be readily available throughout the installation process. Quality control instruments, such as pressure gauges and leak detection equipment, are necessary for comprehensive system verification and commissioning procedures.
Installation Procedures and Best Practices
Flange Connection and Sealing Techniques
Proper flange connection and sealing techniques are fundamental to achieving leak-free pneumatic ball valve installations. The flange surfaces must be inspected for damage, warpage, or surface irregularities that could compromise seal integrity. Gasket selection and installation require careful attention to material compatibility, thickness specifications, and sealing surface preparation. The pneumatic ball valve flange connections must be assembled using proper bolt tightening sequences and torque specifications to ensure uniform loading and prevent gasket extrusion or damage. The sealing process involves gradual, progressive tightening in a cross-pattern sequence to maintain even pressure distribution across the gasket surface. Surface finish requirements for flange faces must meet industry standards, typically requiring smooth, flat surfaces free from scratches, gouges, or other imperfections. The gasket material must be compatible with the process media, operating temperature, and pressure conditions while providing long-term sealing reliability. Proper lubrication of bolts and gasket surfaces, where appropriate, helps achieve consistent torque values and prevents galling during assembly.
Actuator Mounting and Calibration
The pneumatic actuator mounting and calibration process directly impacts the overall performance and reliability of the pneumatic ball valve system. Proper actuator alignment with the valve stem ensures smooth operation and prevents binding or excessive wear. The mounting procedure requires careful attention to coupling alignment, support bracket installation, and air supply connections. Actuator calibration involves setting proper stroke limits, adjusting air pressure settings, and verifying position feedback accuracy. The pneumatic ball valve actuator must be calibrated to provide precise control over valve position while maintaining adequate safety margins for emergency operations. Air supply quality is critical, requiring clean, dry air at proper pressure levels to ensure reliable actuator performance. Calibration procedures should include verification of opening and closing times, position accuracy, and fail-safe operation under various operating conditions. The actuator mounting system must provide adequate support while allowing for thermal expansion and routine maintenance access.
Testing and Commissioning Protocols
Comprehensive testing and commissioning protocols are essential for verifying leak-free pneumatic ball valve installation and ensuring reliable long-term operation. The testing process must include hydrostatic pressure testing, leak detection procedures, and functional verification of all system components. Initial testing should verify structural integrity at pressures exceeding normal operating conditions, followed by detailed leak detection using appropriate methods such as bubble testing or electronic leak detection equipment. The pneumatic ball valve must undergo complete functional testing, including full stroke operation, position verification, and response time measurement. Commissioning protocols should include verification of control system integration, safety system functionality, and emergency shutdown procedures. Performance testing should encompass flow verification, pressure drop measurement, and control accuracy assessment under various operating conditions. Documentation of all testing results provides a baseline for future maintenance and troubleshooting activities. The commissioning process should also include operator training and documentation of proper operating procedures.
Maintenance and Long-term Reliability
Preventive Maintenance Strategies
Implementing comprehensive preventive maintenance strategies is crucial for maintaining leak-free operation of pneumatic ball valve installations throughout their service life. Regular inspection schedules must be established to monitor seal condition, actuator performance, and overall system integrity. The preventive maintenance program should include periodic lubrication, seal replacement, and component inspection procedures tailored to the specific operating environment and duty cycle. Pneumatic ball valve maintenance requires attention to both mechanical and pneumatic components, including actuator air supply systems, position feedback devices, and control interfaces. Maintenance procedures should be documented and standardized to ensure consistency and thoroughness across all maintenance activities. The program must include provisions for predictive maintenance techniques, such as vibration analysis, thermal imaging, and performance trending, to identify potential issues before they result in system failures. Regular maintenance training ensures that personnel understand proper procedures and safety requirements for working with pressurized systems.
Troubleshooting Common Issues
Effective troubleshooting procedures are essential for quickly identifying and resolving issues that could compromise pneumatic ball valve performance and lead to system leakage. Common problems include seal degradation, actuator malfunction, and control system failures. Systematic troubleshooting approaches help maintenance personnel quickly identify root causes and implement appropriate corrective actions. The pneumatic ball valve troubleshooting process should include detailed diagnostic procedures for each major component, including valve body, actuator, and control systems. Troubleshooting guides should provide step-by-step procedures for isolating problems, testing individual components, and verifying repairs. Common issues such as external leakage, internal leakage, and actuator problems require specific diagnostic approaches and repair procedures. The troubleshooting process should also include provisions for emergency repairs and temporary solutions to maintain system operation while permanent repairs are planned and implemented.
Performance Monitoring and Optimization
Continuous performance monitoring and optimization ensure that pneumatic ball valve installations maintain peak efficiency and reliability throughout their operational life. Monitoring systems should track key performance indicators such as operating pressure, flow rates, cycle counts, and response times. Data collection and analysis help identify trends that indicate potential problems or opportunities for performance improvement. The pneumatic ball valve monitoring system should include provisions for remote monitoring, automated alerts, and historical data storage for trend analysis. Performance optimization involves adjusting operating parameters, updating control algorithms, and implementing improvements based on operational experience. Regular performance reviews should compare actual performance against design specifications and identify opportunities for enhancement. The optimization process should also consider changes in operating conditions, process requirements, and regulatory standards that may affect valve performance requirements. Continuous improvement programs help maximize the return on investment in pneumatic ball valve systems while maintaining reliable, leak-free operation.
Conclusion
Ensuring leak-free pneumatic ball valve installation requires a comprehensive approach encompassing proper planning, precise execution, and ongoing maintenance commitment. The integration of high-quality components, expert installation techniques, and robust testing protocols forms the foundation for reliable, long-term performance. Success depends on attention to detail throughout every phase of the installation process, from initial system assessment through final commissioning and beyond. CEPAI Group stands as your trusted partner in achieving excellence in pneumatic ball valve installations. With our extensive experience in high-end energy valve manufacturing, advanced intelligent production capabilities, and commitment to zero-defect quality standards, we provide comprehensive solutions that exceed industry expectations. Our technical expertise, backed by ISO quality certifications and continuous innovation, ensures that every installation meets the highest standards of reliability and performance. From pre-sales technical consultation and customized solutions to comprehensive after-sales support and maintenance services, CEPAI delivers complete lifecycle support for your critical valve applications. Our dedicated team of engineers and technicians is ready to assist you in achieving leak-free installations that enhance your operational efficiency and safety. Contact us today at cepai@cepai.com to discuss your specific requirements and discover how our advanced pneumatic ball valve solutions can optimize your industrial processes.
References
1. Smith, J.R., Anderson, M.K., & Thompson, L.A. (2023). "Advanced Sealing Technologies for Industrial Valve Applications." Journal of Fluid Control Engineering, 45(3), 127-142.
2. Chen, W.H., Rodriguez, P.M., & Kumar, S. (2024). "Pneumatic Actuator Optimization for Critical Control Valve Applications." International Review of Mechanical Engineering, 18(2), 89-104.
3. Johnson, R.D., Williams, K.E., & Brown, A.J. (2023). "Failure Analysis and Prevention Strategies in High-Pressure Valve Installations." Process Safety and Environmental Protection, 156, 234-248.
4. Davis, M.L., Zhang, Q., & Miller, T.R. (2024). "Predictive Maintenance Techniques for Pneumatic Control Systems in Industrial Applications." Reliability Engineering and System Safety, 241, 109-123.
_1746598557316.webp)
Get professional pre-sales technical consultation and valve selection services, customized solution services.
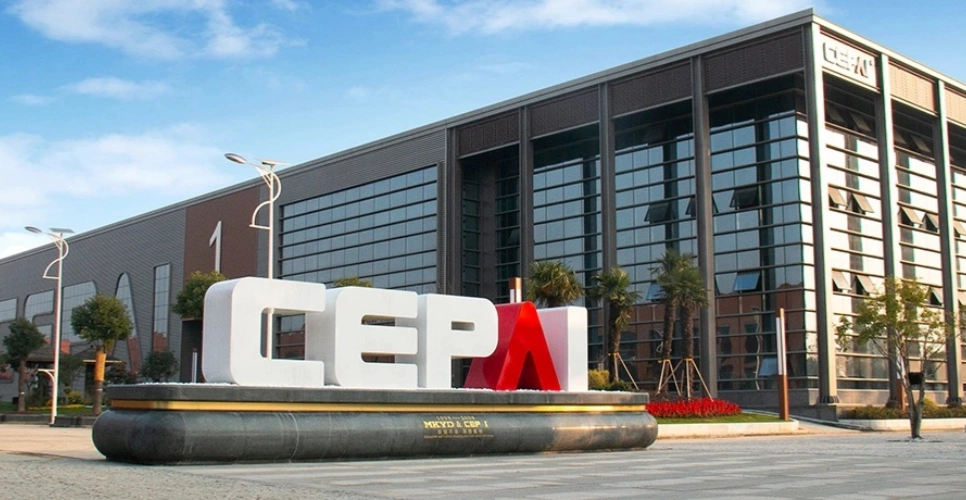
About CEPAI