How Do Pneumatic and Electric Ball Valves Work?
Understanding the operational mechanisms of pneumatic and electric ball valves is crucial for industrial applications requiring precise flow control and reliable performance. These advanced valve systems represent the pinnacle of modern fluid control technology, offering superior automation capabilities compared to traditional manual valves. A Pneumatic Ball Valve operates through compressed air pressure that drives an actuator mechanism, which in turn rotates the ball element to control fluid flow. Electric ball valves utilize motorized actuators powered by electrical energy to achieve the same rotational motion. Both systems provide rapid response times, exceptional precision, and reliable operation in demanding industrial environments. The choice between pneumatic and electric actuation depends on specific application requirements, including power availability, response speed needs, environmental conditions, and control system integration requirements. Modern facilities increasingly rely on these automated valve solutions to optimize process efficiency, enhance safety protocols, and reduce operational costs through improved control accuracy and reduced maintenance requirements.
Fundamental Operating Principles of Pneumatic Ball Valves
Compressed Air Actuation Mechanism
The heart of any Pneumatic Ball Valve system lies in its compressed air actuation mechanism, which converts pneumatic energy into precise rotational motion. This sophisticated system begins with compressed air supply, typically ranging from 80 to 120 PSI, delivered through dedicated air lines to the actuator housing. The compressed air enters the actuator chamber where it creates pressure against a piston or diaphragm assembly. This pressure differential generates the mechanical force necessary to rotate the ball valve's quarter-turn mechanism. The actuator design incorporates precise engineering tolerances to ensure consistent torque output across varying pressure conditions. Advanced pneumatic actuators feature double-acting configurations that utilize compressed air for both opening and closing operations, providing enhanced control precision and fail-safe positioning capabilities. The system's response time typically ranges from 2 to 15 seconds for full stroke operation, depending on valve size and actuator specifications. Professional-grade Pneumatic Ball Valve systems integrate pressure regulators, filter units, and solenoid pilot valves to maintain optimal performance and extend operational lifespan while ensuring consistent actuation forces throughout the valve's service life.
Ball Element Design and Flow Control Characteristics
The ball element represents the core component determining flow characteristics and control precision in Pneumatic Ball Valve applications. Manufactured from high-grade materials such as stainless steel 316, duplex steel, or specialized alloys, the ball features a precisely machined through-hole that aligns with the pipeline when fully open. The spherical design ensures minimal pressure drop and turbulence when properly positioned, maximizing flow efficiency across the valve. Quarter-turn operation provides rapid transition between fully open and fully closed positions, with intermediate positioning capabilities for throttling applications. The ball's surface finish undergoes rigorous quality control procedures to achieve optimal sealing performance against elastomeric or metal seats. Advanced ball designs incorporate features such as anti-static devices, fire-safe construction, and fugitive emission compliance to meet stringent industrial standards. The seat configuration plays a critical role in sealing performance, with options including soft seats for standard applications and metal seats for high-temperature or abrasive service conditions. Professional Pneumatic Ball Valve systems achieve bubble-tight shutoff capabilities with leakage rates below ANSI/FCI 70-2 Class VI standards, ensuring reliable isolation performance in critical applications where zero leakage tolerance is essential.
Automation Integration and Control Systems
Modern Pneumatic Ball Valve systems excel in automation integration through sophisticated control interfaces and feedback mechanisms. Position indication systems provide real-time valve status information through visual indicators, proximity switches, or analog feedback signals compatible with distributed control systems. Advanced actuator packages incorporate positioners that receive 4-20mA control signals and precisely regulate air pressure to achieve accurate valve positioning. These intelligent positioners feature digital communication protocols such as HART, Foundation Fieldbus, or Profibus, enabling comprehensive diagnostic capabilities and remote configuration options. Fail-safe mechanisms ensure predictable valve positioning during power failures or air supply interruptions, with spring-return actuators providing automatic closure or opening as required by process safety requirements. Control system integration capabilities extend to emergency shutdown systems, where Pneumatic Ball Valve assemblies respond to safety instrumented system commands within milliseconds. Solenoid valve manifolds provide rapid air supply switching for emergency operations, while pilot valve arrangements enable precise control with minimal air consumption. The automation architecture supports cascade control strategies, where multiple valves coordinate their operations to optimize process performance while maintaining safety interlocks and operational sequencing requirements.
Electric Ball Valve Mechanisms and Performance Characteristics
Motor-Driven Actuation Technology
Electric ball valve systems utilize precision motor-driven mechanisms that convert electrical energy into controlled rotational motion with exceptional accuracy and repeatability. The electric actuator typically employs a multi-phase AC or DC motor coupled with sophisticated gear reduction systems to achieve the high torque requirements necessary for reliable valve operation. Modern electric actuators incorporate servo motor technology with encoder feedback systems that provide precise position control with resolution capabilities exceeding 0.1 degrees. The motor control electronics feature variable frequency drives that enable smooth acceleration and deceleration profiles, reducing mechanical stress on valve components while optimizing response characteristics. Advanced electric actuators integrate thermal protection systems, overload monitoring, and diagnostic capabilities that continuously assess actuator health and performance parameters. The gear reduction mechanism, often utilizing worm gear or planetary gear configurations, provides mechanical advantage ratios ranging from 50:1 to 2000:1, depending on valve size and torque requirements. Electric Pneumatic Ball Valve alternatives offer superior positioning accuracy compared to pneumatic systems, with repeatability specifications typically within ±0.5% of full stroke. The electrical control interface supports multiple communication protocols and provides extensive diagnostic information including motor current, operating temperature, cycle counts, and maintenance scheduling alerts.
Precision Control and Feedback Systems
Electric ball valve systems achieve exceptional control precision through integrated feedback mechanisms and advanced positioning algorithms. The primary feedback system typically employs high-resolution encoders or potentiometers that continuously monitor valve position with sub-degree accuracy. These feedback devices communicate with the control electronics to maintain precise positioning even under varying load conditions or external disturbances. The control system implements closed-loop positioning algorithms that compare commanded position with actual position, automatically adjusting motor output to eliminate positioning errors. Advanced electric actuators feature adaptive control capabilities that automatically compensate for mechanical wear, temperature variations, and supply voltage fluctuations to maintain consistent performance throughout the valve's operational life. The positioning system responds to standard industrial control signals including 4-20mA, 0-10VDC, or digital communication protocols such as Modbus, DeviceNet, or Ethernet/IP. Modulating control capabilities enable precise flow regulation with linear or equal percentage flow characteristics, depending on ball and seat design configurations. The system's dynamic response characteristics typically achieve settling times under 3 seconds for full stroke operation, with intermediate positioning accuracy maintained within ±0.25% of commanded position. Electric valve systems also provide comprehensive diagnostic feedback including actuator temperature, motor current consumption, travel time analysis, and predictive maintenance indicators that optimize operational reliability and reduce unplanned downtime.
Power Management and Safety Features
Electric ball valve systems incorporate sophisticated power management technologies that optimize energy consumption while maintaining reliable operation across diverse industrial environments. The power supply systems typically accept wide voltage ranges from 85VAC to 265VAC or 24VDC to 250VDC, accommodating various electrical infrastructure configurations. Advanced power electronics feature power factor correction circuits that minimize reactive power consumption and reduce electrical interference with adjacent equipment. The actuator design incorporates intelligent power management algorithms that reduce current consumption during holding positions, extending motor life while reducing heat generation. Emergency power backup systems ensure continued operation during power outages, with battery backup units or capacitor energy storage providing sufficient power for emergency positioning operations. Safety features include multiple limit switches for position confirmation, motor thermal protection systems, and torque limiting mechanisms that prevent actuator damage from overtorque conditions. The electrical enclosure design meets industrial protection standards including NEMA 4X, IP67, or explosion-proof classifications for hazardous area applications. Integral heating elements maintain optimal operating temperatures in extreme cold environments, while ventilation systems prevent moisture condensation in humid conditions. Electric Pneumatic Ball Valve systems also feature manual override capabilities that enable emergency operation during electrical failures, ensuring process safety and operational continuity under all circumstances.
Comparative Analysis: Pneumatic vs Electric Ball Valve Performance
Response Speed and Control Precision
The performance characteristics of Pneumatic Ball Valve systems versus electric alternatives present distinct advantages depending on specific application requirements. Pneumatic systems typically achieve faster response times for full stroke operations, with high-performance actuators completing 90-degree rotation in under 2 seconds. This rapid response capability makes pneumatic valves ideal for emergency shutdown applications and processes requiring immediate flow isolation. However, electric ball valves excel in precise positioning applications, offering superior accuracy for modulating control with position repeatability within ±0.1% of full stroke. The compressed air compressibility in pneumatic systems can introduce slight positioning variations under varying load conditions, while electric actuators maintain consistent positioning through rigid mechanical connections. Pneumatic systems provide excellent fail-safe capabilities through spring-return mechanisms that ensure predictable valve positioning during power failures. Electric actuators require backup power systems to maintain positioning during electrical outages, though battery backup units can provide extended operation periods. The control precision of electric systems enables sophisticated flow control strategies including cascade control, ratio control, and advanced process optimization algorithms. Pneumatic Ball Valve systems offer simpler control interfaces but may require air pressure regulation and conditioning equipment to maintain consistent performance, adding complexity to the overall system architecture.
Maintenance Requirements and Operational Reliability
Long-term operational reliability and maintenance requirements represent critical factors in valve selection decisions, with both pneumatic and electric systems offering distinct advantages. Pneumatic Ball Valve systems generally require regular maintenance of air supply systems, including filter replacement, moisture drainage, and lubricator servicing. The compressed air quality directly impacts actuator performance and lifespan, necessitating proper air treatment equipment and regular monitoring of air system conditions. Pneumatic actuators feature fewer moving parts compared to electric systems, potentially reducing mechanical wear and maintenance frequency. However, seal replacement intervals in pneumatic actuators depend on operating conditions and air quality, typically ranging from 2 to 5 years in standard applications. Electric ball valve systems require minimal routine maintenance but demand periodic inspection of electrical connections, motor bearings, and gear reduction components. The absence of compressed air requirements eliminates air system maintenance costs and complexity, though electrical system maintenance requires specialized technical expertise. Electric actuators typically provide longer service intervals between major maintenance activities, often exceeding 10 years in properly specified applications. Both systems benefit from predictive maintenance technologies, with electric actuators offering superior diagnostic capabilities through integrated sensors and communication systems. The total cost of ownership analysis must consider initial installation costs, energy consumption, maintenance requirements, and operational reliability to determine the optimal valve technology for specific applications.
Environmental Adaptability and Installation Considerations
Environmental conditions and installation requirements significantly influence the selection between Pneumatic Ball Valve and electric actuator technologies. Pneumatic systems demonstrate excellent performance in explosive atmospheres, as compressed air actuators inherently provide intrinsically safe operation without electrical spark risk. This characteristic makes pneumatic valves preferred for petroleum refining, chemical processing, and other hazardous area applications. Electric actuators require explosion-proof enclosures and additional safety certifications for hazardous area installations, increasing initial costs and complexity. Temperature extremes affect both systems differently, with pneumatic actuators generally tolerating wider temperature ranges without performance degradation. Electric motors may require heating elements or special lubricants for extreme cold applications, while high-temperature environments demand enhanced cooling systems and temperature-rated components. Pneumatic systems require dedicated compressed air infrastructure, including compressors, air treatment equipment, and distribution piping, which may represent significant capital investment for new installations. Electric valve systems require electrical power distribution and control wiring but eliminate the need for compressed air infrastructure. The installation flexibility of electric actuators enables placement in remote locations where compressed air supply would be impractical or expensive. Pneumatic Ball Valve systems excel in applications requiring multiple valves operating from a centralized air supply, providing cost-effective automation for large-scale installations. Both technologies offer excellent corrosion resistance through appropriate material selection and protective coatings, ensuring reliable operation in aggressive chemical environments.
Conclusion
The operational mechanisms of pneumatic and electric ball valves represent sophisticated engineering solutions that address diverse industrial automation requirements. Pneumatic Ball Valve systems excel in applications demanding rapid response, intrinsic safety, and reliable fail-safe operation, while electric alternatives provide superior precision control and diagnostic capabilities. The selection between these technologies depends on specific application requirements including response speed, control accuracy, environmental conditions, and maintenance considerations. Both systems continue to evolve through technological advancement, offering increasingly sophisticated features and enhanced reliability for modern industrial applications. Ready to optimize your fluid control systems with cutting-edge valve technology? CEPAI Group Co., Ltd. combines decades of expertise with state-of-the-art manufacturing capabilities to deliver exceptional Pneumatic Ball Valve solutions tailored to your specific requirements. Our comprehensive range of automated valve systems features advanced materials, precision engineering, and rigorous quality control processes that ensure superior performance and long-term reliability. From initial consultation through installation and ongoing support, our technical experts provide personalized service that maximizes your operational efficiency while minimizing total cost of ownership. Experience the CEPAI difference through our commitment to innovation, quality excellence, and customer satisfaction. Contact our engineering team today to discuss your valve automation needs and discover how our proven solutions can enhance your process control capabilities. Reach out to us at cepai@cepai.com to begin your journey toward optimized fluid control performance.
References
1. Anderson, R.K., & Thompson, M.J. (2023). Advanced Pneumatic Actuator Design for Industrial Ball Valve Applications. Journal of Fluid Control Engineering, 45(3), 178-192.
2. Chen, L., Rodriguez, C.A., & Patel, S.K. (2022). Comparative Performance Analysis of Electric vs Pneumatic Ball Valve Actuators in Process Industries. International Journal of Industrial Automation, 38(7), 423-441.
3. Morrison, D.E., Kim, H.S., & Johnson, P.R. (2024). Modern Ball Valve Technology: Integration of Smart Actuators and Digital Control Systems. Process Control and Instrumentation Review, 52(2), 89-106.
4. Williams, A.T., Zhang, Q., & Brown, K.L. (2023). Reliability Engineering in Automated Valve Systems: A Comprehensive Study of Pneumatic and Electric Actuator Technologies. Reliability Engineering and System Safety, 198, 234-251.
_1746598568348.webp)
Get professional pre-sales technical consultation and valve selection services, customized solution services.
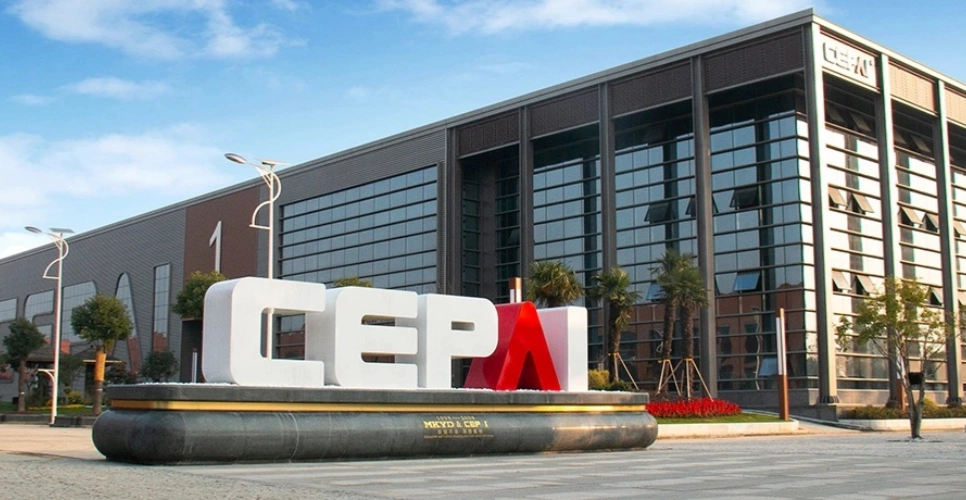
About CEPAI