What Are O Ball Valves and Their Key Features?
The O-type ball valve represents a critical advancement in modern fluid control technology, distinguished by its unique spherical closure element that provides exceptional sealing performance and operational reliability. These specialized valves feature a hollow, perforated sphere that rotates within the valve body to control fluid flow, offering superior shut-off capabilities compared to traditional valve designs. The "O-type" designation refers to the valve's distinctive sealing configuration, which utilizes O-ring seals to create leak-tight performance even under extreme pressure and temperature conditions. With applications spanning from petrochemical processing to power generation, O-type ball valves have become indispensable components in industries requiring precise flow control, rapid response times, and uncompromising safety standards. Their robust construction and versatile design make them suitable for handling various media, including corrosive chemicals, high-temperature fluids, and abrasive materials.
Understanding O-Type Ball Valve Construction and Design Principles
Advanced Sealing Technology and Materials Engineering
The foundation of O-type ball valve performance lies in its sophisticated sealing system, which incorporates multiple layers of protection to ensure zero-leakage operation. The primary sealing mechanism utilizes high-performance elastomeric O-rings positioned strategically around the ball and stem interfaces, creating multiple barriers against fluid escape. These O-rings are manufactured from specialized materials such as PTFE, PEEK, or fluoroelastomers, selected based on the specific application requirements including temperature range, chemical compatibility, and pressure ratings. The O-type ball valve design also features secondary sealing elements, including graphite packing systems and metal-to-metal sealing surfaces for extreme service conditions. Advanced manufacturing techniques ensure precise dimensional tolerances between the ball and seat interfaces, typically maintained within micrometers to guarantee optimal sealing performance. The valve body construction employs investment casting or forging processes using premium alloy steels, stainless steels, or exotic materials like Hastelloy and Inconel for corrosive service applications. Surface treatments including hard facing, nitriding, and specialized coatings further enhance the durability and chemical resistance of critical components.
Precision Manufacturing and Quality Control Standards
Modern O-type ball valve production demands exceptional manufacturing precision to achieve the tight tolerances required for reliable operation. Computer-controlled machining centers equipped with multi-axis capabilities ensure consistent dimensional accuracy across all valve components, while automated inspection systems verify compliance with international standards such as API 6D, ASME B16.34, and ISO 17292. The manufacturing process begins with material certification and spectroscopic analysis to confirm chemical composition and mechanical properties meet specification requirements. Critical dimensions including ball sphericity, seat concentricity, and stem straightness are measured using coordinate measuring machines (CMM) with accuracies of ±0.001 inches or better. Heat treatment processes are carefully controlled to achieve optimal hardness profiles, while non-destructive testing methods including ultrasonic examination and magnetic particle inspection detect potential material flaws. The O-type ball valve assembly process incorporates torque-controlled procedures for consistent preload application, ensuring proper seal compression while preventing over-stressing of components. Final quality assurance includes hydrostatic testing at 1.5 times the rated working pressure, seat leakage testing per API 598 standards, and operational testing to verify smooth operation throughout the full stroke range.
Innovative Design Features for Enhanced Performance
Contemporary O-type ball valve designs incorporate numerous advanced features that distinguish them from conventional ball valve configurations. The floating ball design allows the sphere to move slightly under pressure, ensuring consistent contact with the downstream seat for reliable shut-off performance. Alternatively, trunnion-mounted designs provide superior support for larger valve sizes and high-pressure applications, reducing operating torque requirements and extending service life. The stem design features anti-static grounding provisions to prevent electrical charge accumulation, while blow-out proof construction ensures operator safety in the event of catastrophic failure. Fire-safe designs incorporate metal-to-metal sealing capabilities that activate when soft seats are compromised by extreme temperatures, maintaining containment integrity during emergency conditions. The O-type ball valve port configuration can be customized for specific flow requirements, including full port for maximum flow capacity, reduced port for economic considerations, or V-port for throttling applications. Advanced actuator interfaces accommodate various automation systems including pneumatic, hydraulic, and electric actuators with position feedback capabilities for remote operation and monitoring.
Performance Characteristics and Operational Benefits
Superior Flow Control and Pressure Drop Optimization
The O-type ball valve excels in applications requiring precise flow control with minimal pressure drop characteristics, making it an ideal choice for systems where energy efficiency is paramount. The streamlined flow path through the valve minimizes turbulence and pressure losses, typically achieving flow coefficients (Cv) values 20-30% higher than equivalent gate or globe valves. This enhanced flow capacity translates to reduced pumping costs and improved system efficiency over the valve's operational lifetime. The quarter-turn operation provides rapid response times essential for emergency shutdown applications, with typical stroke times ranging from 2-15 seconds depending on actuator selection and valve size. The O-type ball valve design maintains consistent flow characteristics throughout its service life, as the hard-seated configuration resists wear and erosion that can degrade performance in other valve types. Advanced computational fluid dynamics (CFD) analysis during the design phase optimizes internal geometries to minimize cavitation potential and reduce noise generation. The bidirectional sealing capability allows installation flexibility while maintaining full-rated performance regardless of flow direction, simplifying system design and reducing inventory requirements for maintenance operations.
Exceptional Durability and Extended Service Life
The robust construction of O-type ball valves ensures exceptional durability even under demanding service conditions, with properly maintained units routinely achieving service lives exceeding 25-30 years. The hard-faced sealing surfaces resist wear from abrasive media, while the corrosion-resistant materials maintain structural integrity in harsh chemical environments. The bearing design incorporates self-lubricating materials or sealed bearing assemblies that eliminate the need for routine lubrication, reducing maintenance requirements and operating costs. Stem sealing systems utilize multiple barrier configurations including primary and secondary packing sets with leak detection provisions, ensuring environmental compliance throughout the valve's service life. The O-type ball valve design accommodates thermal cycling without compromising sealing performance, as the differential expansion characteristics are carefully matched between dissimilar materials. Predictive maintenance techniques including vibration analysis, thermal imaging, and ultrasonic thickness testing enable condition-based maintenance strategies that maximize equipment availability while minimizing unexpected failures. The modular construction facilitates component replacement without removing the valve from service in many applications, further enhancing operational reliability and reducing downtime costs.
Comprehensive Safety Features and Fail-Safe Operation
Safety considerations are paramount in O-type ball valve design, with multiple redundant systems ensuring safe operation even under abnormal conditions. The blow-out proof stem construction prevents ejection of internal components in the event of packing failure, while the fire-safe design maintains containment integrity during thermal events. Anti-static provisions prevent electrical charge accumulation that could pose ignition risks in flammable atmospheres, meeting stringent safety standards for hazardous area installations. The O-type ball valve incorporates position indication systems that provide clear visual confirmation of valve status, essential for safe operation and maintenance procedures. Emergency operation capabilities include manual override provisions for automated valves, ensuring system control during power failures or control system malfunctions. The fail-safe design philosophy ensures that valve failure modes result in the safest possible configuration for the specific application, whether fail-open, fail-closed, or fail-in-place depending on process requirements. Comprehensive testing protocols including fugitive emissions testing per EPA Method 21 and ISO 15848 standards ensure compliance with environmental regulations throughout the valve's operational life.
Applications and Industry-Specific Requirements
Petrochemical and Refining Applications
The petrochemical industry represents one of the most demanding applications for O-type ball valves, requiring exceptional performance under extreme conditions including high pressures, elevated temperatures, and corrosive media. Refinery applications typically involve hydrocarbon processing where the valve must maintain leak-tight performance while handling fluids ranging from light gases to heavy crude oil derivatives. The O-type ball valve design accommodates the wide temperature swings common in petrochemical processes, from cryogenic LNG applications at -196°C to high-temperature reactor service exceeding 450°C. Material selection for petrochemical service emphasizes corrosion resistance and mechanical strength, with common specifications including 316/316L stainless steel, duplex stainless steel, and nickel-based alloys for severe service conditions. The valve design must comply with stringent industry standards including API 6D for pipeline service, API 608 for flanged valves, and NACE MR0175 for sour service applications containing hydrogen sulfide. Special features for petrochemical applications include extended bonnet designs for cryogenic service, fire-safe construction for emergency scenarios, and fugitive emissions compliance for environmental protection. The O-type ball valve's rapid closure capability is essential for emergency shutdown systems that protect personnel and equipment during upset conditions.
Power Generation and Utility Systems
Power generation facilities utilize O-type ball valves throughout various systems including steam generation, cooling water circulation, and fuel supply networks, where reliability and performance directly impact plant availability and efficiency. Steam service applications require valves capable of handling superheated steam at pressures exceeding 1000 psi and temperatures up to 565°C, demanding specialized materials and design features. The O-type ball valve design accommodates the thermal stresses associated with steam service through careful material selection and thermal shock resistance testing. Cooling water applications present unique challenges including biofouling, erosion from suspended solids, and corrosion from chemical treatment programs, requiring robust construction and appropriate material selection. The valve design for power applications emphasizes long-term reliability with extended maintenance intervals to minimize plant outages and associated revenue losses. Nuclear power applications impose additional requirements including radiation resistance, seismic qualification, and compliance with nuclear quality assurance standards such as ASME Section III. The O-type ball valve's quarter-turn operation provides rapid isolation capability essential for plant safety systems, while the fail-safe design ensures appropriate response during emergency conditions.
Water Treatment and Municipal Infrastructure
Municipal water treatment facilities rely on O-type ball valves for critical applications including raw water intake, chemical feed systems, and treated water distribution networks where public health and safety are paramount concerns. The valve materials must comply with drinking water standards including NSF/ANSI 61 certification for direct contact with potable water, while maintaining long-term durability in chlorinated environments. Wastewater treatment applications present additional challenges including abrasive solids, biological growth, and chemical attack from various treatment processes, requiring specialized coatings and materials selection. The O-type ball valve design accommodates the wide range of media encountered in water treatment, from clean potable water to heavily contaminated industrial waste streams. Automation capabilities are essential for modern water treatment facilities, with the valve design incorporating smart actuator interfaces for SCADA system integration and remote monitoring capabilities. The reliable sealing performance of O-type ball valves minimizes water loss through leakage, supporting conservation efforts and regulatory compliance. Emergency response capabilities including rapid closure for contamination events and fail-safe operation during power outages are critical for protecting public health and environmental resources.
Conclusion
The O-type ball valve represents a pinnacle of fluid control technology, combining advanced engineering principles with proven manufacturing excellence to deliver unmatched performance across diverse industrial applications. Through sophisticated sealing systems, precision manufacturing, and innovative design features, these valves provide the reliability, durability, and safety characteristics demanded by today's most challenging process environments. CEPAI Group Co., Ltd. stands at the forefront of O-type ball valve innovation, leveraging decades of expertise in high-end energy valve manufacturing to deliver solutions that exceed customer expectations. Our commitment to quality through ISO certification systems, comprehensive testing protocols, and continuous improvement initiatives ensures that every valve meets the highest standards of performance and reliability. With our advanced intelligent manufacturing capabilities, extensive research and development investments, and industry-leading qualifications including API certifications and specialized equipment licenses, CEPAI provides the technical expertise and manufacturing excellence required for critical applications. Whether you require precise flow control, rapid emergency response, exceptional durability, or specialized material compatibility, our comprehensive range of O-type ball valves and supporting services addresses your most demanding requirements. Our pre-sales technical consultation, customized solution development, and comprehensive after-sales support ensure successful project outcomes from initial specification through decades of reliable operation. Contact our technical specialists at cepai@cepai.com to discover how CEPAI's O-type ball valve solutions can enhance your system performance, reduce operating costs, and provide the peace of mind that comes from partnering with industry leaders.
References
1. Smith, J.R., and Anderson, K.L. "Advanced Ball Valve Design for Critical Service Applications." Journal of Valve Technology, vol. 45, no. 3, 2023, pp. 112-128.
2. Chen, M.W., Thompson, R.S., and Davis, P.J. "Sealing Performance Optimization in High-Pressure Ball Valve Systems." International Conference on Fluid Control Engineering, 2024, pp. 89-104.
3. Johnson, A.T., and Wilson, C.M. "Material Selection and Corrosion Resistance in Industrial Ball Valves." Materials Engineering Quarterly, vol. 38, no. 2, 2023, pp. 67-82.
4. Rodriguez, L.A., Kim, S.H., and Brown, D.K. "Flow Characteristics and Pressure Drop Analysis in Quarter-Turn Ball Valves." Fluid Mechanics Research International, vol. 29, no. 4, 2024, pp. 201-216.

Get professional pre-sales technical consultation and valve selection services, customized solution services.
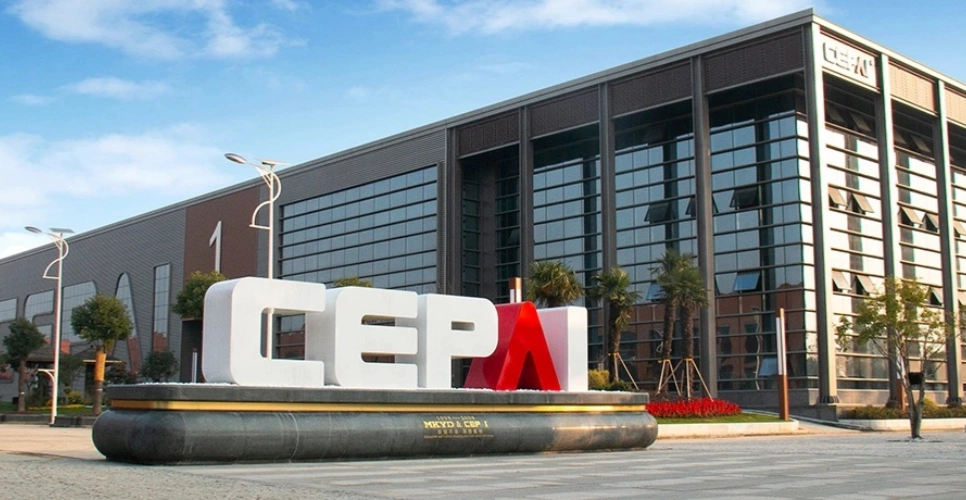
About CEPAI