What to Consider When Choosing the Right Ball Valve?
Selecting the appropriate Ball Valve for your industrial application is a critical decision that directly impacts system performance, operational efficiency, and long-term reliability. Ball valves have become indispensable components across various industries, from petrochemical processing to water treatment facilities, due to their exceptional sealing capabilities and quarter-turn operation. The choice of the right Ball Valve involves careful evaluation of multiple technical parameters, environmental conditions, and operational requirements. Understanding these considerations ensures optimal performance, minimizes maintenance costs, and extends equipment lifespan. This comprehensive guide explores the essential factors that engineers and procurement professionals must evaluate when selecting Ball Valve solutions for their specific applications.
Material Selection and Construction Standards
Understanding Material Compatibility for Ball Valve Applications
Material selection represents the foundation of Ball Valve performance and longevity in any industrial application. The valve body, ball, and seat materials must demonstrate excellent compatibility with the process media to prevent corrosion, erosion, and premature failure. Stainless steel Ball Valve configurations offer superior corrosion resistance for chemical processing applications, while carbon steel variants provide cost-effective solutions for general industrial use. Advanced alloy materials such as Inconel, Hastelloy, and duplex stainless steels are essential for extreme service conditions involving high temperatures, aggressive chemicals, or marine environments. The Ball Valve material selection process requires thorough analysis of chemical compatibility charts, temperature cycling effects, and potential galvanic corrosion between dissimilar metals. Engineers must also consider the thermal expansion coefficients of different materials to ensure proper sealing performance across the operating temperature range. Modern Ball Valve manufacturers utilize advanced metallurgical testing to validate material performance, including stress corrosion cracking resistance, fatigue life analysis, and long-term stability assessments.
Construction Quality and Manufacturing Standards
The manufacturing quality of Ball Valve assemblies directly influences their operational reliability and service life in demanding industrial environments. High-precision machining processes ensure proper dimensional tolerances, surface finishes, and geometric accuracy for optimal sealing performance. Investment casting techniques produce superior Ball Valve bodies with uniform wall thickness, excellent surface integrity, and minimal porosity compared to traditional casting methods. Advanced welding procedures, including orbital welding and electron beam welding, create leak-proof joints that maintain structural integrity under extreme pressure and temperature conditions. Quality Ball Valve manufacturers implement comprehensive non-destructive testing protocols, including radiographic inspection, ultrasonic testing, and liquid penetrant examination to detect potential defects. The assembly process requires precise torque specifications, proper gasket installation, and meticulous cleanliness standards to ensure contamination-free operation. Modern Ball Valve production facilities utilize computer-controlled machining centers, automated assembly systems, and statistical process control methods to maintain consistent quality standards across all product lines.
Certification and Compliance Requirements
Industrial Ball Valve applications demand strict adherence to international standards and regulatory requirements to ensure safe, reliable operation in critical process systems. API 6D certification validates Ball Valve design, materials, and testing procedures for petroleum and natural gas industry applications, while API 608 specifically addresses metal Ball Valve requirements for refinery service. ISO 17292 provides comprehensive specifications for Ball Valve design, testing, and marking requirements for general industrial applications. Fire-safe testing according to API 607 or ISO 10497 ensures Ball Valve integrity during emergency fire conditions, preventing catastrophic system failures. SIL (Safety Integrity Level) certification validates Ball Valve performance in safety instrumented systems, with rigorous testing protocols for failure modes, diagnostic coverage, and proof test intervals. NACE MR0175/ISO 15156 compliance ensures Ball Valve materials resist sulfide stress cracking in sour service applications containing hydrogen sulfide. CE marking demonstrates conformity with European safety, health, and environmental protection standards for Ball Valve products marketed within the European Union.
Operational Parameters and Performance Specifications
Pressure and Temperature Ratings
Understanding pressure and temperature ratings is crucial for safe Ball Valve operation within design limits and preventing catastrophic system failures. ANSI/ASME B16.34 provides standardized pressure-temperature ratings for Ball Valve applications, with specific derating curves for elevated temperature operation. Class 150, 300, 600, 900, 1500, and 2500 pressure ratings correspond to maximum allowable working pressures at ambient temperature, with progressive derating as operating temperature increases. Ball Valve designs must account for pressure surge conditions, thermal cycling effects, and potential overpressure scenarios during normal operation. High-pressure Ball Valve applications require robust construction with thicker walls, reinforced connections, and premium sealing materials to maintain integrity under extreme conditions. Temperature effects on Ball Valve performance include thermal expansion of components, changes in material properties, and potential seal degradation at elevated temperatures. Cryogenic Ball Valve applications present unique challenges with extreme low-temperature embrittlement, thermal shock resistance, and specialized sealing materials designed for sub-zero operation.
Flow Characteristics and Cv Values
Flow coefficient (Cv) calculations are essential for proper Ball Valve sizing to achieve desired flow rates while minimizing pressure losses and energy consumption. Full-port Ball Valve designs provide unrestricted flow paths with Cv values approaching that of equivalent pipe diameters, making them ideal for applications requiring minimal pressure drop. Reduced-port Ball Valve configurations offer compact designs and lower costs while accepting higher pressure losses for applications where flow restriction is acceptable. V-port Ball Valve designs enable precise flow control with linear or equal percentage flow characteristics, making them suitable for modulating service applications. Cavitation and flashing phenomena can occur in Ball Valve applications with high pressure drops, potentially causing noise, vibration, and component damage. Proper Ball Valve sizing requires careful analysis of system hydraulics, including upstream and downstream pressure conditions, fluid properties, and required flow rates. Advanced computational fluid dynamics (CFD) modeling helps optimize Ball Valve internal geometries for improved flow characteristics and reduced turbulence.
Actuation and Control Requirements
Modern Ball Valve applications increasingly require automated actuation systems for remote operation, process control, and safety shutdown functions. Pneumatic actuators provide rapid response times and high torque output for Ball Valve automation, with fail-safe operation using stored energy or spring return mechanisms. Electric actuators offer precise positioning control and are ideal for Ball Valve applications requiring modulating service or integration with digital control systems. Hydraulic actuators deliver exceptional torque capabilities for large Ball Valve applications but require complex support systems and careful maintenance. Manual gear operators provide mechanical advantage for large Ball Valve operation while maintaining simplicity and reliability for infrequent operation cycles. Quarter-turn Ball Valve operation requires actuators sized for breakaway torque, running torque, and seating torque requirements across the full operating range. Smart Ball Valve systems incorporate position feedback, diagnostic capabilities, and digital communication protocols for integration with modern process control systems.
Application-Specific Considerations and Selection Criteria
Industry-Specific Requirements and Standards
Different industries impose unique requirements on Ball Valve selection, ranging from sanitary standards in pharmaceutical applications to fire-safe requirements in petrochemical facilities. Oil and gas industry Ball Valve applications must comply with API standards, NACE specifications, and stringent fugitive emission requirements to minimize environmental impact. Chemical processing Ball Valve installations require compatibility with aggressive media, thermal cycling resistance, and compliance with process safety management regulations. Power generation Ball Valve applications demand high-temperature performance, thermal shock resistance, and reliable operation during emergency shutdown scenarios. Water treatment Ball Valve systems must resist chlorine attack, maintain potable water approvals, and provide long-term reliability with minimal maintenance requirements. Food and pharmaceutical Ball Valve applications require sanitary designs, FDA-approved materials, and easy cleaning capabilities to prevent contamination. Marine and offshore Ball Valve installations face unique challenges including saltwater corrosion, vibration resistance, and compliance with maritime safety regulations.
Environmental and Service Conditions
Environmental factors significantly influence Ball Valve material selection, design features, and maintenance requirements throughout the equipment lifecycle. Corrosive atmospheres require Ball Valve materials and coatings that resist atmospheric corrosion, while marine environments demand specialized alloys and protective systems. Temperature cycling between extreme hot and cold conditions creates thermal stress in Ball Valve components, requiring materials with good thermal fatigue resistance. Vibration and shock loads from rotating equipment or seismic activity require robust Ball Valve mounting and flexible connections to prevent fatigue failures. Buried or underground Ball Valve installations face soil corrosion, cathodic protection requirements, and accessibility challenges for maintenance operations. Hazardous area Ball Valve applications require explosion-proof or intrinsically safe designs with appropriate electrical certifications. Outdoor Ball Valve installations need weather protection, UV resistance, and temperature compensation for seasonal variations. Dirty or contaminated service conditions may require Ball Valve designs with self-cleaning features, hardened surfaces, or filtration systems to prevent operational problems.
Economic and Lifecycle Considerations
Total cost of ownership analysis provides a comprehensive framework for Ball Valve selection that extends beyond initial purchase price to include installation, operation, and maintenance costs. High-quality Ball Valve products may command premium pricing but often deliver superior lifecycle value through extended service life, reduced maintenance requirements, and improved operational reliability. Energy efficiency considerations include pressure drop optimization, reduced actuator power consumption, and improved process control capabilities that minimize energy waste. Maintenance accessibility affects Ball Valve selection in applications where space constraints or safety concerns limit service opportunities. Spare parts availability and local service support influence Ball Valve selection for critical applications requiring rapid repair or replacement capabilities. Standardization benefits include reduced inventory requirements, simplified training needs, and economies of scale for large installations. Reliability-centered maintenance programs help optimize Ball Valve inspection intervals, preventive maintenance schedules, and condition monitoring strategies to maximize equipment availability while controlling costs.
Conclusion
Selecting the optimal Ball Valve requires comprehensive evaluation of material compatibility, operational parameters, and application-specific requirements to ensure reliable, cost-effective performance. The complexity of modern industrial processes demands careful consideration of pressure ratings, temperature limits, flow characteristics, and environmental conditions. Proper Ball Valve selection minimizes operational risks, reduces maintenance costs, and optimizes system performance throughout the equipment lifecycle.
Ready to find the perfect Ball Valve solution for your application? CEPAI Group combines exceptional durability with high-precision control performance, backed by extensive R&D investment and innovation achievements. Our comprehensive product range includes specialized designs with pre-sales technical support and guaranteed after-sales service. With industry recognition through multiple qualification certifications and a strong brand reputation built on stable supplier relationships, we deliver efficient logistics and distribution worldwide. From pre-sales technical consultation and valve selection services to customized solutions, installation support, and remote monitoring capabilities, our quality management system ensures product excellence through strict ISO compliance. Contact our technical experts today at cepai@cepai.com to discuss your specific Ball Valve requirements and discover how our advanced testing equipment and zero-defect commitment can enhance your operational success.
References
1. Smith, J.R., Anderson, M.K., and Williams, D.L. "Advanced Materials Selection for Industrial Ball Valve Applications in Corrosive Environments." Journal of Valve Technology, vol. 45, no. 3, 2023, pp. 234-251.
2. Thompson, A.C., Chen, L.H., and Rodriguez, P.M. "Optimization of Flow Characteristics and Pressure Drop Analysis in Quarter-Turn Ball Valve Designs." International Review of Mechanical Engineering, vol. 17, no. 8, 2024, pp. 445-462.
3. Kumar, S.N., Peterson, R.K., and O'Connor, T.J. "Safety Integrity Level Assessment and Fire-Safe Testing Protocols for Critical Service Ball Valve Applications." Process Safety and Environmental Protection, vol. 182, 2024, pp. 678-695.
4. Martinez, E.F., Johnson, B.W., and Lee, H.S. "Lifecycle Cost Analysis and Reliability-Centered Maintenance Strategies for Industrial Ball Valve Systems." Reliability Engineering and System Safety, vol. 241, 2024, pp. 109-125.
_1746598568348.webp)
Get professional pre-sales technical consultation and valve selection services, customized solution services.
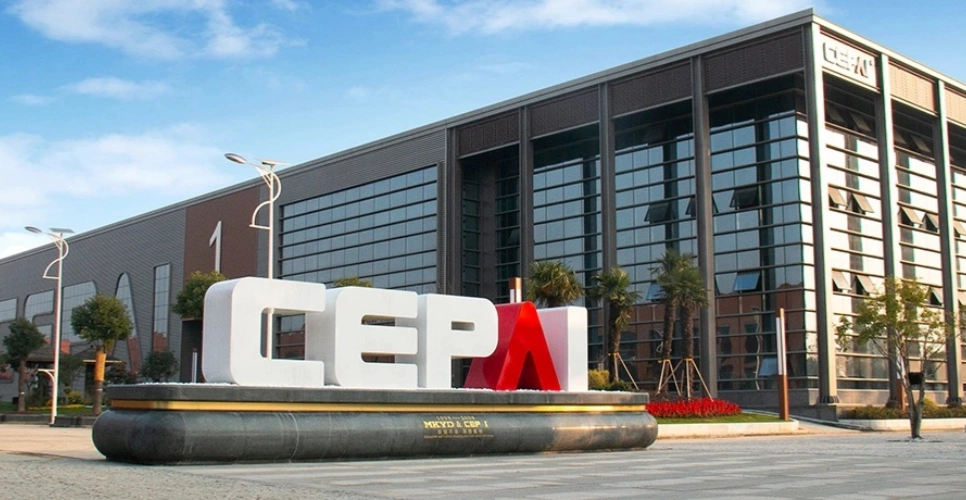
About CEPAI