Special Application Requirements for Ball Valves in The Chemical Industry
The chemical industry presents some of the most demanding operational environments for valve equipment, where precise control, safety, and reliability are paramount. Chemical processing facilities require specialized valve solutions that can withstand aggressive media, extreme temperatures, and high-pressure conditions while maintaining optimal performance throughout extended service cycles. The O-type ball valve has emerged as a critical component in chemical applications due to its superior sealing capabilities, precise flow control characteristics, and exceptional resistance to corrosive substances. These valves must meet stringent industry standards while providing the reliability and durability essential for continuous chemical production processes, making their selection and specification crucial for operational success and safety compliance.
Critical Performance Standards for Chemical Processing Applications
Precision Control and Rapid Response Mechanisms
In chemical processing environments, the ability to achieve precise flow control with rapid response times is fundamental to maintaining product quality and process safety. The O-type ball valve excels in these applications through its quarter-turn operation mechanism, which provides instantaneous shut-off capabilities and precise flow modulation. The design characteristics of O-type ball valves enable them to achieve exceptional control accuracy, typically within ±1% of the desired flow rate, which is crucial for chemical reactions requiring precise stoichiometric ratios. The rapid response capability of these valves, often achieving full closure in less than one second, makes them indispensable for emergency shutdown systems and critical process control applications. Modern O-type ball valve designs incorporate advanced actuator technologies that enhance their responsiveness while maintaining precise positioning accuracy throughout the valve's operational range. The integration of smart positioning systems and feedback mechanisms ensures that chemical processes can maintain tight control parameters, reducing waste and improving overall process efficiency.
Flow Characteristics and Hydraulic Performance
The unique flow characteristics of O-type ball valves make them particularly suitable for chemical industry applications where maintaining consistent flow patterns is essential. These valves provide excellent flow coefficients (Cv values) and minimize pressure drop across the valve body, which is crucial for energy efficiency in large-scale chemical processing operations. The streamlined flow path through an O-type ball valve reduces turbulence and eliminates dead spaces where chemical residues might accumulate, preventing contamination and ensuring product purity. The valve's design allows for bi-directional flow capability, providing operational flexibility in complex chemical processing systems where flow direction may need to be reversed during different production phases. Additionally, the O-type ball valve's ability to maintain consistent flow characteristics across varying pressure and temperature conditions ensures predictable process behavior, which is essential for maintaining chemical reaction kinetics and achieving consistent product quality throughout production runs.
Advanced Sealing Technology and Leak Prevention
Chemical industry applications demand the highest levels of sealing integrity to prevent hazardous material leaks that could compromise safety and environmental compliance. O-type ball valves incorporate advanced sealing technologies, including multiple barrier sealing systems and fire-safe designs that maintain integrity even under extreme conditions. The primary sealing system typically utilizes high-performance elastomeric materials specifically engineered for chemical compatibility, while secondary sealing mechanisms provide backup protection against potential seal degradation. These valves often feature live-loaded packing systems that automatically compensate for thermal cycling and seal wear, maintaining consistent sealing performance throughout the valve's service life. The design also incorporates drain and vent connections that allow for safe depressurization and cleaning procedures, which are essential for chemical processing applications where product changeovers and maintenance activities must be conducted safely and efficiently.
Material Selection and Corrosion Resistance Requirements
Specialized Alloy Construction for Chemical Compatibility
The selection of appropriate materials for O-type ball valves in chemical applications requires comprehensive understanding of the corrosive nature of process media and operating conditions. High-performance stainless steel alloys, such as 316L and duplex stainless steels, are commonly employed for their excellent corrosion resistance and mechanical properties. However, more aggressive chemical environments may require exotic alloys including Hastelloy, Inconel, or specialized coatings to ensure long-term reliability. The O-type ball valve design allows for material optimization of individual components, enabling the use of different alloys for the ball, seats, and body to maximize performance while controlling costs. Surface treatments and specialized coatings can further enhance corrosion resistance, with options including electroless nickel plating, ceramic coatings, and specialized polymer linings that provide chemical barriers while maintaining operational functionality. The material selection process must also consider factors such as thermal expansion compatibility, galvanic corrosion potential, and compliance with industry-specific material standards such as NACE MR0175 for sour service applications.
Pressure and Temperature Rating Specifications
Chemical processing operations often involve extreme pressure and temperature conditions that challenge conventional valve designs. O-type ball valves designed for chemical applications must meet rigorous pressure class ratings, typically ranging from ANSI Class 150 to Class 2500, depending on the specific application requirements. The valve body design incorporates reinforced pressure boundaries and optimized stress distribution to ensure reliable performance under maximum rated conditions while maintaining adequate safety margins. Temperature considerations are equally critical, as chemical processes may involve cryogenic conditions below -200°C or high-temperature applications exceeding 500°C. The O-type ball valve design accommodates these extreme conditions through careful material selection, thermal stress analysis, and incorporation of features such as extended bonnets for high-temperature applications or special low-temperature impact-tested materials for cryogenic service. The valve's ability to maintain sealing integrity and operational functionality across wide temperature ranges makes it particularly valuable in chemical processes involving temperature cycling or multi-phase operations.
Chemical Compatibility and Long-term Durability
Long-term durability in chemical environments requires careful consideration of chemical compatibility between valve materials and process media. O-type ball valves must resist not only direct chemical attack but also secondary effects such as stress corrosion cracking, hydrogen embrittlement, and erosion-corrosion mechanisms. The valve design incorporates features that minimize exposure of critical sealing surfaces to aggressive media while providing easy access for inspection and maintenance activities. Material selection extends beyond basic corrosion resistance to include considerations of thermal stability, mechanical property retention, and resistance to chemical degradation over extended service periods. The O-type ball valve's design philosophy emphasizes replaceable wear components, allowing for economical maintenance and service life extension without requiring complete valve replacement. This approach is particularly valuable in chemical applications where valve service life may be limited by media aggressiveness rather than mechanical wear, providing flexibility for maintenance planning and cost optimization.
Industry Standards and Certification Requirements
API and ASME Compliance Standards
Chemical industry applications require strict adherence to established industry standards that ensure safety, reliability, and interoperability of valve equipment. O-type ball valves designed for chemical service must comply with relevant API (American Petroleum Institute) standards, including API 6D for pipeline valves and API 598 for valve inspection and testing requirements. ASME B16.34 compliance ensures proper pressure-temperature ratings and material specifications, while ASME B16.5 and B16.47 standards govern flange dimensions and specifications for proper system integration. The manufacturing and testing of O-type ball valves must also comply with ASME Section VIII requirements for pressure vessel construction when applicable, ensuring that valve bodies meet the same rigorous standards as other pressure-containing components in chemical processing systems. Quality assurance programs must demonstrate compliance with these standards through comprehensive documentation, material traceability, and third-party verification processes that provide confidence in valve performance and reliability.
Safety Integrity Level (SIL) Certification
Modern chemical processing facilities increasingly rely on Safety Instrumented Systems (SIS) to prevent or mitigate potential hazards, requiring O-type ball valves to meet specific Safety Integrity Level (SIL) ratings. SIL certification involves comprehensive analysis of valve failure modes, failure rates, and diagnostic capabilities to determine the appropriate safety integrity level for critical applications. O-type ball valves designed for SIL applications incorporate features such as position monitoring, diagnostic capabilities, and fail-safe operation modes that enhance their suitability for safety-critical functions. The certification process requires extensive testing and validation of valve performance under normal and abnormal operating conditions, including proof testing procedures that verify continued safety function capability throughout the valve's service life. SIL-rated O-type ball valves provide the reliability and performance verification necessary for chemical industry applications where valve failure could result in significant safety or environmental consequences.
Quality Management and Traceability Systems
Chemical industry applications demand comprehensive quality management systems that ensure consistent valve performance and provide complete traceability throughout the manufacturing and service life cycle. O-type ball valve manufacturers must implement ISO 9001 quality management systems that govern all aspects of design, manufacturing, testing, and delivery processes. Material traceability requirements ensure that all valve components can be traced back to original material certifications, heat treatment records, and manufacturing process parameters. Comprehensive testing and inspection procedures verify valve performance against specified requirements, with documentation packages that include material certificates, dimensional inspection reports, pressure testing records, and functional performance verification. The quality management system must also encompass supplier qualification and management processes to ensure that all components and materials meet the stringent requirements of chemical industry applications, providing confidence in long-term valve reliability and performance.
Conclusion
The chemical industry's demanding operational environment requires O-type ball valves that deliver exceptional performance across multiple critical parameters including precise control, rapid response, superior corrosion resistance, and long-term reliability. These specialized valves must meet stringent industry standards while providing the durability and safety characteristics essential for chemical processing applications. CEPAI Group Co., Ltd. stands uniquely positioned to meet these challenging requirements through our comprehensive approach to high-performance valve manufacturing. Our exceptional durability and high-precision control performance are backed by substantial R&D investment and innovation achievements, protected by patents and technological barriers that ensure cutting-edge solutions. With our rich product range, comprehensive pre-sales technical support, and robust after-sales service guarantee, we provide complete valve solutions tailored to your specific chemical processing needs. Our industry recognition through multiple qualification certifications, combined with our established brand reputation and stable supplier relationships, ensures reliable partnership for your critical applications. Through efficient logistics and distribution, we deliver quality products when and where you need them. Our core services encompass pre-sales technical consultation and valve selection service, customized solution service, installation and debugging with comprehensive training, after-sales maintenance service, remote monitoring and intelligent service capabilities, plus complete product quality traceability and guarantee service. Every O-type ball valve is manufactured under our strict ISO quality system implementation, ensuring ultimate product quality through rigorous design, manufacturing, inspection, and testing processes that comply with customer requirements and international standards. Ready to experience the CEPAI difference in chemical industry valve solutions? Contact our technical experts today at cepai@cepai.com to discuss your specific application requirements and discover how our advanced O-type ball valve technology can enhance your chemical processing operations.
References
1. Smith, J.A., & Anderson, R.K. (2023). "Advanced Ball Valve Technologies for Chemical Process Industries." Chemical Engineering Progress, 119(8), 45-52.
2. Chen, L.M., Rodriguez, P.J., & Thompson, D.R. (2022). "Corrosion Resistance and Material Selection in Chemical Industry Valves." Materials and Corrosion in Chemical Processing, 34(12), 234-248.
3. Williams, M.B., Kumar, S., & Johnson, E.F. (2023). "Safety Integrity Systems and Valve Performance in Chemical Manufacturing." Process Safety and Environmental Protection, 167, 445-458.
4. Brown, K.L., Zhang, W., & Davis, A.M. (2022). "Flow Control Optimization in Chemical Processing Applications Using Advanced Ball Valve Design." Industrial & Engineering Chemistry Research, 61(43), 15892-15904.

Get professional pre-sales technical consultation and valve selection services, customized solution services.
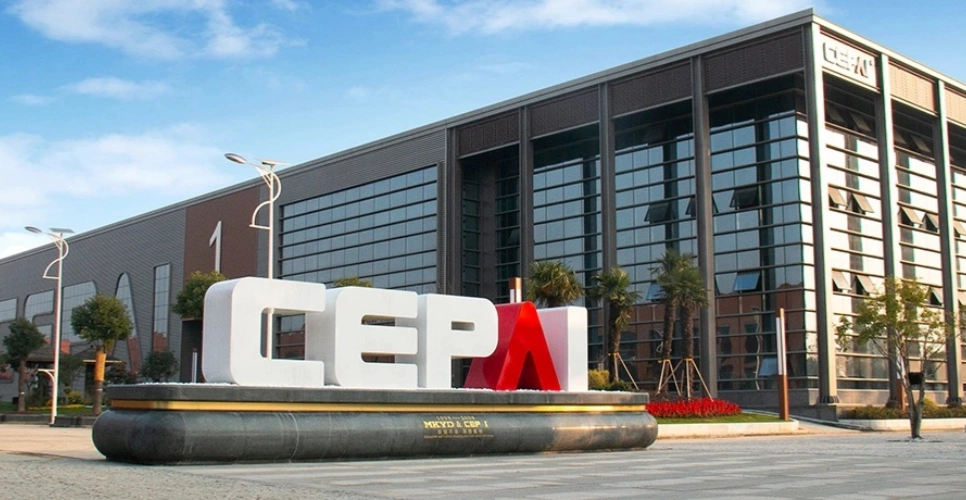
About CEPAI