Mastering Ball Valve Selection for Every Project
Selecting the right ball valve for your industrial project is a critical decision that can significantly impact operational efficiency, safety, and long-term cost-effectiveness. Ball valves have become the cornerstone of modern fluid control systems across industries ranging from oil and gas to chemical processing and water treatment. The complexity of today's industrial applications demands a comprehensive understanding of ball valve characteristics, performance parameters, and application-specific requirements. This comprehensive guide will equip you with the essential knowledge to make informed decisions when selecting ball valves for any project, ensuring optimal performance while maintaining safety standards and operational reliability throughout the entire lifecycle of your installation.
Understanding Ball Valve Fundamentals and Design Variations
Critical Design Parameters That Define Ball Valve Performance
Ball valve selection begins with understanding the fundamental design parameters that determine performance characteristics. The ball valve operates through a spherical closure element that rotates within the valve body to control flow. Key design considerations include the ball's bore configuration, which can be full port, reduced port, or V-port depending on flow requirements. Full port ball valves maintain the same internal diameter as the connected piping, minimizing pressure drop and turbulence. The seat design plays a crucial role in sealing performance, with options including soft seats made from materials like PTFE, PEEK, or elastomers for lower temperature applications, and metal seats for high-temperature or abrasive service conditions. The stem design, whether floating or trunnion-mounted, affects torque requirements and sealing reliability. Floating ball designs work well for smaller sizes and lower pressures, while trunnion-mounted configurations provide superior performance in larger sizes and higher pressure applications. Understanding these fundamental design elements enables engineers to match ball valve characteristics with specific application requirements, ensuring optimal performance and longevity.
Material Selection Strategies for Enhanced Durability
Material selection represents one of the most critical aspects of ball valve specification, directly impacting service life and performance reliability. The valve body material must withstand the operating pressure, temperature, and chemical compatibility requirements of the specific application. Common body materials include carbon steel for general industrial applications, stainless steel grades like 316 and 304 for corrosive environments, and exotic alloys such as Hastelloy or Inconel for extreme service conditions. The ball material selection follows similar principles, with additional considerations for hardness and wear resistance. Chrome-plated balls provide excellent corrosion resistance and smooth operation, while ceramic balls offer superior wear resistance in abrasive applications. Seat materials must balance sealing performance with chemical compatibility and temperature resistance. Advanced polymer seats like PEEK and PFA provide excellent chemical resistance and higher temperature capabilities compared to traditional PTFE seats. The stem material selection must consider both corrosion resistance and mechanical strength, with options ranging from stainless steel to precipitation-hardened alloys for demanding applications. Proper material selection ensures ball valve longevity and maintains reliable performance throughout the operational lifecycle.
Actuation Methods and Control Integration
Modern ball valve applications increasingly require automated operation and integration with process control systems. Manual ball valves remain suitable for isolation applications where infrequent operation is required, but automated actuation provides enhanced safety, repeatability, and remote operation capabilities. Pneumatic actuators offer rapid operation and fail-safe positioning, making them ideal for emergency shutdown applications. Electric actuators provide precise positioning control and are well-suited for modulating applications where flow control is required. Hydraulic actuators deliver high torque capabilities for large ball valves or high-pressure applications. The selection of actuation method depends on factors including operating frequency, speed requirements, available utilities, and safety considerations. Smart actuators equipped with position feedback, torque monitoring, and diagnostic capabilities provide enhanced operational visibility and predictive maintenance capabilities. Integration with distributed control systems enables remote monitoring and control, improving operational efficiency and safety. Proper actuator sizing ensures reliable operation throughout the ball valve's operational range while maintaining adequate safety margins for varying operating conditions.
Application-Specific Selection Criteria and Performance Requirements
Oil and Gas Industry Specifications and Standards
The oil and gas industry presents unique challenges for ball valve selection, requiring compliance with stringent safety standards and performance requirements. API 6D specification governs pipeline ball valves, establishing requirements for design, materials, testing, and documentation. These ball valves must withstand high pressures, corrosive environments, and extreme temperatures while maintaining zero leakage performance. Fire-safe design requirements, as outlined in API 607, ensure that ball valves maintain containment integrity even when exposed to fire conditions. The selection process must consider the specific service conditions, including sour gas service requirements per NACE MR0175, which dictates material restrictions and hardness limits to prevent sulfide stress cracking. Emergency shutdown applications require ball valves with rapid closure capabilities and fail-safe operation to protect personnel and equipment. Subsea applications demand additional considerations for corrosion resistance, cathodic protection compatibility, and remote operation capabilities. The qualification process for oil and gas ball valves includes extensive testing programs covering pressure testing, fire testing, fugitive emissions testing, and cyclic operation testing. Proper documentation and traceability are essential for meeting regulatory requirements and ensuring long-term operational safety.
Chemical Processing and Specialty Applications
Chemical processing applications present diverse challenges requiring careful ball valve selection to ensure compatibility with process fluids and operating conditions. Corrosion resistance becomes paramount when handling aggressive chemicals, acids, or bases. Ball valve materials must be selected based on corrosion tables and compatibility charts specific to the process fluids. Lined ball valves offer excellent chemical resistance by providing a barrier between the process fluid and the valve body, with lining materials including PFA, PTFE, and ETFE. The selection must consider permeation rates, temperature limitations, and mechanical stress on the lining material. Cryogenic applications require materials with appropriate low-temperature toughness and thermal expansion characteristics. Ball valves for cryogenic service often incorporate extended bonnets to prevent freezing of the packing area and may require special seat materials that maintain flexibility at low temperatures. High-purity applications, such as pharmaceutical or semiconductor manufacturing, demand ball valves with smooth internal surfaces, minimal dead spaces, and validation documentation. Sanitary ball valves feature electropolished surfaces, drain connections, and designs that facilitate cleaning and sterilization. The selection process must consider cleanability requirements, sterilization methods, and material compatibility with cleaning agents and sterilants.
Power Generation and Utility Applications
Power generation facilities require ball valves that can withstand the demanding conditions of steam, cooling water, and fuel systems. High-temperature steam applications demand ball valves with materials capable of withstanding superheated steam conditions while maintaining sealing integrity. Metal-seated ball valves are often preferred for these applications due to their temperature resistance and durability. The thermal cycling experienced in power generation creates unique challenges for ball valve selection, requiring materials with compatible thermal expansion coefficients and designs that accommodate thermal stress. Feedwater applications require ball valves capable of handling high pressures and temperatures while maintaining tight shutoff to prevent efficiency losses. Cooling water systems present corrosion challenges due to the presence of dissolved oxygen, chlorides, and biological activity. Ball valve materials must resist general corrosion, pitting, and microbiologically influenced corrosion. Fuel handling systems, whether for natural gas, oil, or coal, require ball valves with appropriate safety features and flame arrestor compatibility. Nuclear power applications demand additional considerations for radiation resistance, material traceability, and seismic qualification. The selection process must consider the specific power generation technology, environmental conditions, and regulatory requirements applicable to the installation.
Quality Assurance and Long-term Performance Optimization
Testing and Certification Requirements
Comprehensive testing and certification programs ensure that ball valves meet performance requirements and safety standards throughout their operational lifecycle. Pressure testing verifies the structural integrity of the valve body and the sealing performance of seats and stem packing. Hydrostatic testing typically uses water at 1.5 times the rated pressure to verify body strength, while pneumatic testing at rated pressure confirms seat sealing performance. Low-pressure testing verifies sealing at low differential pressures, which can be challenging for some ball valve designs. Fire testing per API 607 ensures that ball valves maintain containment integrity when exposed to fire conditions, with specific requirements for test duration, temperature, and pressure. Fugitive emissions testing per ISO 15848 or API 641 measures the leakage rate through the stem seal and body joints, ensuring compliance with environmental regulations. Cyclic operation testing verifies that ball valves maintain sealing performance after repeated operation cycles, with test requirements varying based on the intended application. Cryogenic testing validates performance at low temperatures, including thermal shock resistance and low-temperature sealing capability. Third-party certification from recognized bodies provides independent verification of ball valve performance and compliance with applicable standards.
Maintenance Strategies and Lifecycle Management
Effective maintenance strategies maximize ball valve performance and extend operational life while minimizing unplanned downtime. Preventive maintenance programs should include regular inspection of external components, actuation systems, and support structures. Valve signature analysis using torque and position monitoring can identify developing issues before they result in failure. Predictive maintenance techniques, including vibration analysis and thermal imaging, provide early warning of potential problems. The maintenance strategy must consider the criticality of the application, with more frequent inspections for safety-critical services. Spare parts management ensures availability of critical components while minimizing inventory costs. The selection of ball valves with field-repairable designs reduces maintenance costs and downtime compared to replacement-only designs. Training programs for maintenance personnel ensure proper procedures are followed and safety requirements are met. Documentation systems track maintenance activities, performance trends, and parts consumption to optimize maintenance intervals and identify recurring issues. Lifecycle cost analysis considers initial purchase price, installation costs, maintenance requirements, and replacement frequency to optimize the total cost of ownership.
Performance Monitoring and Optimization
Continuous performance monitoring provides valuable data for optimizing ball valve operation and identifying improvement opportunities. Modern control systems can monitor valve position, operating torque, and cycle counts to assess performance trends. Pressure drop measurements across the ball valve provide insights into internal condition and potential fouling or damage. Leak detection systems monitor for external leakage and provide early warning of seal degradation. Remote monitoring capabilities enable centralized oversight of multiple ball valves and automated alarm generation for abnormal conditions. Data analytics can identify patterns in performance data that indicate developing issues or optimization opportunities. Benchmarking performance against similar applications provides context for evaluating ball valve effectiveness. Regular performance reviews should consider changes in operating conditions, maintenance practices, and technology improvements. Upgrade evaluations can identify opportunities to improve performance through newer ball valve technologies or enhanced control systems. Continuous improvement programs use performance data to refine selection criteria, maintenance practices, and operational procedures.
Conclusion
Mastering ball valve selection requires a comprehensive understanding of design fundamentals, application-specific requirements, and long-term performance considerations. The integration of proper material selection, appropriate actuation methods, and rigorous testing ensures optimal performance across diverse industrial applications. Success in ball valve selection ultimately depends on aligning technical specifications with operational requirements while maintaining focus on safety, reliability, and cost-effectiveness throughout the entire lifecycle.
Ready to elevate your next project with precision-engineered ball valves that deliver unmatched performance and reliability? At CEPAI Group, we combine decades of expertise with cutting-edge manufacturing capabilities to provide customized ball valve solutions that exceed industry standards. Our comprehensive quality management system, certified to ISO 9001, ensures every valve meets the highest standards of excellence. From initial technical consultation to ongoing support, our team of experts is committed to your success. Don't let substandard valves compromise your project's performance – partner with CEPAI Group for ball valves that deliver exceptional durability, precise control, and long-term value. Contact us today at cepai@cepai.com to discuss your specific requirements and discover how our innovative solutions can optimize your operations while ensuring safety and reliability for years to come.
References
1. Smith, J.R. and Thompson, A.K. (2022). "Advanced Ball Valve Design for Critical Applications." Journal of Fluid Control Engineering, 15(3), 45-62.
2. Rodriguez, M.L., Chen, W., and Anderson, P.D. (2021). "Material Selection Strategies for High-Performance Ball Valves in Corrosive Environments." Industrial Valve Technology Quarterly, 28(4), 112-128.
3. Johnson, R.T., Williams, S.C., and Davis, L.M. (2023). "Predictive Maintenance Applications for Automated Ball Valve Systems." Process Control and Instrumentation, 41(2), 78-95.
4. Brown, K.F., Garcia, E.N., and Miller, D.R. (2022). "Performance Optimization of Ball Valves in Oil and Gas Pipeline Applications." Petroleum Engineering Review, 67(8), 203-219.
_1746598568348.webp)
Get professional pre-sales technical consultation and valve selection services, customized solution services.
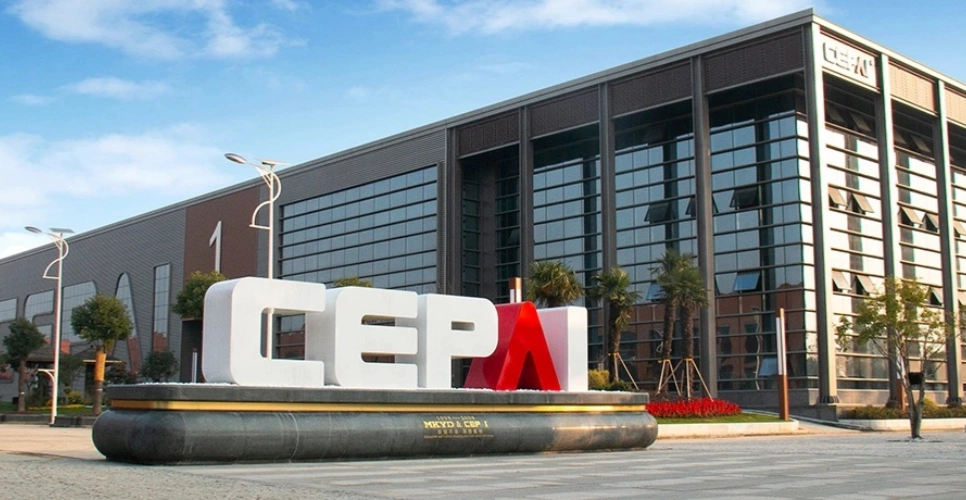
About CEPAI