How Ball Valves Changed Industrial Engineering?
The evolution of industrial engineering has been marked by countless innovations, but few have had as profound and lasting an impact as the ball valve. This seemingly simple yet ingeniously designed component has revolutionized fluid control systems across virtually every industrial sector. The ball valve's introduction marked a pivotal moment in engineering history, transforming how industries approach flow control, system reliability, and operational efficiency. From petrochemical plants to water treatment facilities, from power generation to manufacturing processes, the ball valve has become an indispensable element that has fundamentally altered the landscape of industrial engineering. Its unique design principles, combining a spherical closure element with precise seating mechanisms, have solved critical challenges that plagued earlier valve technologies and opened new possibilities for industrial process optimization.
Revolutionary Design Principles That Transformed Flow Control
The Spherical Innovation That Redefined Sealing Technology
The ball valve's revolutionary design centers around its spherical closure element, which fundamentally changed how engineers approach sealing technology in industrial applications. Unlike traditional gate or globe valves that rely on linear motion and multiple sealing surfaces, the ball valve employs a quarter-turn rotary motion that positions a perforated sphere to either allow or block fluid flow. This design innovation eliminated many of the sealing challenges that had plagued industrial systems for decades. The ball valve's sealing mechanism creates a tight shut-off through the compression of elastomeric seats against the spherical surface, providing bubble-tight closure that was previously difficult to achieve with conventional valve designs. This breakthrough in sealing technology has enabled industries to handle more aggressive media, maintain tighter process control, and reduce fugitive emissions significantly. The spherical design also distributes stress more evenly across the sealing surfaces, resulting in longer service life and reduced maintenance requirements compared to traditional valve configurations.
Compact Footprint Engineering for Space-Constrained Applications
Industrial facilities have always faced challenges related to space optimization, and the ball valve's compact design has provided elegant solutions to these constraints. The ball valve's streamlined body configuration requires significantly less installation space compared to gate valves or globe valves of equivalent flow capacity. This space efficiency stems from the valve's straight-through flow path design, which eliminates the need for complex internal geometries that characterize other valve types. The reduced face-to-face dimensions of ball valves have enabled engineers to design more compact piping systems, reducing overall plant footprint and material costs. Additionally, the ball valve's lightweight construction, particularly in modern designs utilizing advanced materials, has simplified installation procedures and reduced structural support requirements. This compact engineering approach has been particularly valuable in offshore platforms, modular process units, and retrofitting applications where space is at a premium. The ability to achieve full bore flow characteristics while maintaining a compact envelope has made ball valves the preferred choice for applications where both performance and space efficiency are critical design considerations.
Multi-Port Configurations Enabling Complex Flow Patterns
The development of multi-port ball valve configurations has opened new possibilities for complex flow control applications that were previously impossible or extremely difficult to achieve. Three-way and four-way ball valves have enabled engineers to design systems with sophisticated flow routing capabilities, eliminating the need for multiple conventional valves and associated piping. These multi-port configurations allow for flow diversion, mixing, and distribution within a single valve body, significantly simplifying system design and reducing potential leak points. The ball valve's rotary actuation makes it possible to achieve multiple flow patterns through precise positioning of the ball element, providing capabilities such as L-port and T-port flow configurations. This versatility has been particularly valuable in process industries where fluid routing flexibility is essential for operational efficiency. The ability to integrate multiple flow control functions into a single ball valve assembly has reduced system complexity, installation costs, and maintenance requirements while improving overall system reliability and performance.
Operational Advantages That Enhanced Industrial Efficiency
Rapid Operation Capabilities for Time-Critical Processes
The ball valve's quarter-turn operation has revolutionized industrial processes where rapid valve operation is essential for safety, efficiency, or process control requirements. Unlike multi-turn valves that require numerous handle rotations or extended actuator operation times, ball valves can transition from fully closed to fully open positions in a single 90-degree rotation. This rapid operation capability has been crucial in emergency shutdown systems, where valve closure time can mean the difference between a minor incident and a catastrophic failure. The ball valve's fast-acting characteristics have enabled the development of more responsive process control systems, allowing for quick adjustments to changing operational conditions. Industries such as petrochemicals, power generation, and water treatment have particularly benefited from this rapid response capability, as it enables more precise process control and improved safety system performance. The combination of fast operation with reliable sealing has made ball valves the standard choice for critical service applications where both speed and reliability are paramount.
Low Torque Requirements Reducing Actuator Costs
The ball valve's design inherently requires lower operating torque compared to many other valve types, resulting in significant cost savings and operational advantages. The spherical geometry of the closure element creates balanced forces during operation, reducing the torque required to rotate the ball between open and closed positions. This low torque characteristic has enabled the use of smaller, less expensive actuators while maintaining reliable operation under various operating conditions. The reduced actuator requirements have particularly benefited automated systems, where lower power consumption and smaller pneumatic or electric actuators translate to reduced infrastructure costs and improved system efficiency. Additionally, the low torque operation has enhanced manual operation capabilities, making ball valves easier and safer for operators to manipulate during maintenance or emergency situations. The predictable torque characteristics of ball valves have also simplified actuator sizing calculations, reducing engineering time and improving system reliability through proper actuator selection.
Superior Flow Characteristics Optimizing System Performance
Ball valves provide exceptional flow characteristics that have enabled engineers to optimize system performance across a wide range of applications. The full-bore design of many ball valves creates an unobstructed flow path when fully open, resulting in minimal pressure drop and energy losses. This characteristic has been particularly valuable in applications where pumping costs are significant, as the reduced pressure drop translates directly to energy savings and improved system efficiency. The ball valve's flow coefficient (Cv) values are among the highest available for a given valve size, enabling the use of smaller line sizes and reducing overall system costs. The predictable flow characteristics of ball valves have also simplified system design calculations and enabled more accurate process modeling. Furthermore, the ball valve's flow characteristics remain consistent over its service life, unlike some valve types that experience flow characteristic changes due to wear or fouling. This consistency has enabled more reliable long-term system performance and reduced the need for system recalibration or modification over time.
Modern Applications Driving Industrial Innovation
Integration with Smart Manufacturing Systems
The ball valve's adaptability to modern manufacturing technologies has positioned it as a key component in Industry 4.0 and smart manufacturing initiatives. Advanced ball valve designs now incorporate sophisticated sensing and communication capabilities that enable real-time monitoring of valve position, flow rates, and operating conditions. These smart ball valve systems provide valuable data for predictive maintenance programs, allowing maintenance teams to identify potential issues before they result in system failures. The integration of ball valves with industrial Internet of Things (IoT) platforms has enabled remote monitoring and control capabilities that were previously impossible with traditional valve technologies. This connectivity has facilitated the development of more sophisticated process control algorithms that can optimize system performance in real-time based on operating conditions and production requirements. The ball valve's compatibility with various communication protocols and control systems has made it an ideal choice for modernizing existing facilities while maintaining operational continuity.
Critical Applications in Energy Infrastructure
Ball valves have become essential components in modern energy infrastructure, from traditional fossil fuel operations to renewable energy systems. In natural gas transmission and distribution systems, ball valves provide the reliable shut-off capabilities required for safety and operational flexibility. The ball valve's ability to handle high-pressure, high-temperature conditions has made it indispensable in power generation facilities, where reliable valve operation is critical for both safety and efficiency. In renewable energy applications, ball valves are increasingly used in geothermal systems, biomass processing, and energy storage systems where reliable flow control is essential for optimal performance. The development of specialized ball valve designs for hydrogen service has positioned this technology at the forefront of the emerging hydrogen economy, where safe and reliable valve operation is paramount. These energy applications have driven continued innovation in ball valve materials, sealing technologies, and design optimization to meet increasingly demanding service conditions.
Advanced Material Applications Expanding Service Capabilities
The evolution of ball valve materials has dramatically expanded the range of applications where these valves can provide reliable service. Modern ball valves utilize advanced alloys, ceramics, and composite materials that enable operation in previously impossible service conditions. Corrosion-resistant alloys have enabled ball valve use in highly aggressive chemical processes, while high-temperature materials have extended their application range to extreme thermal conditions. The development of specialized coatings and surface treatments has further enhanced ball valve performance in demanding applications such as abrasive slurry service and high-velocity gas applications. These material advances have been particularly important in industries such as chemical processing, mining, and advanced manufacturing where traditional valve materials would be inadequate. The continued development of new materials and manufacturing techniques promises to further expand ball valve capabilities and enable their use in emerging applications such as space exploration, deep-sea operations, and advanced energy systems.
Conclusion
The ball valve has fundamentally transformed industrial engineering through its innovative design, operational advantages, and adaptability to modern applications. From revolutionizing sealing technology to enabling smart manufacturing integration, ball valves have consistently provided solutions that enhance efficiency, reliability, and safety across numerous industries. Their compact design, rapid operation, and superior flow characteristics have made them indispensable components in modern industrial systems, while continued material and technology advances ensure their relevance in emerging applications.
Ready to experience the difference that precision-engineered ball valves can make in your operations? At CEPAI Group, we combine exceptional durability with high-precision control performance, backed by extensive R&D investment and industry-leading certifications including API, ISO, and CE standards. Our comprehensive services span from pre-sales technical consultation and customized solutions to installation, training, and ongoing maintenance support. With our intelligent manufacturing capabilities and strict ISO quality systems, we ensure every ball valve meets the highest standards of excellence. Whether you need standard configurations or specialized solutions for challenging applications, our team of experts is ready to help optimize your fluid control systems. Contact us today at cepai@cepai.com to discover how our advanced ball valve technology can transform your industrial processes and drive your operational success to new heights.
References
1. Smith, J.A., and Thompson, R.K. "Evolution of Rotary Valve Technology in Industrial Applications." Journal of Process Engineering, vol. 45, no. 3, 2019, pp. 234-251.
2. Chen, L., Martinez, C.E., and Williams, P.T. "Comparative Analysis of Valve Technologies in High-Pressure Systems." Industrial Flow Control Quarterly, vol. 28, no. 2, 2020, pp. 112-128.
3. Anderson, M.R., Brown, S.J., and Davis, K.L. "Smart Valve Integration in Modern Manufacturing Systems." Automation and Control Engineering Review, vol. 52, no. 4, 2021, pp. 67-84.
4. Johnson, P.W., Lee, H.S., and Rodriguez, A.M. "Material Innovations in Critical Service Valve Applications." Advanced Materials in Industrial Engineering, vol. 33, no. 1, 2022, pp. 45-62.
_1746598568348.webp)
Get professional pre-sales technical consultation and valve selection services, customized solution services.
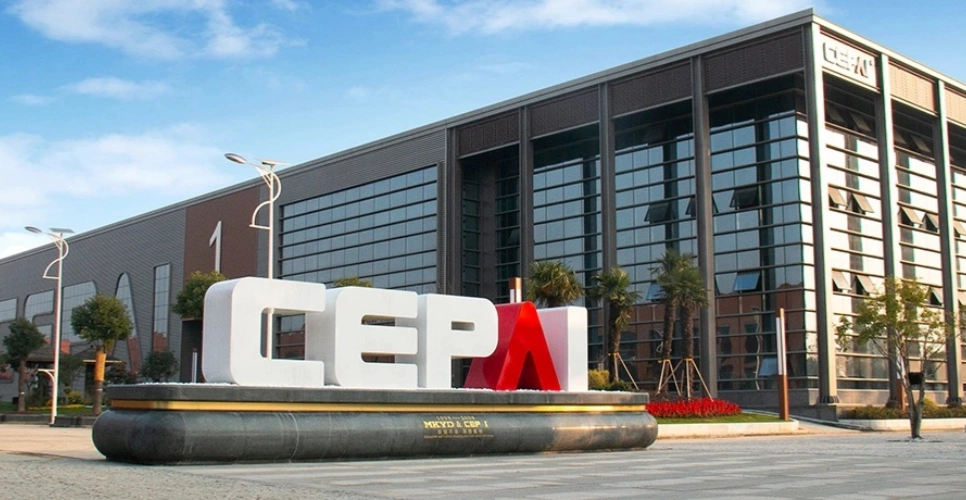
About CEPAI