Understanding O-Type Ball Valves: Features and Applications
In the complex world of industrial fluid control systems, the O-type ball valve stands as a critical component that delivers exceptional performance across diverse applications. These sophisticated valves represent a pinnacle of engineering excellence, combining precise control mechanisms with robust construction to meet the demanding requirements of modern industrial processes. O-type ball valves are specifically designed to provide reliable flow control, superior sealing capabilities, and enhanced operational efficiency in high-pressure and high-temperature environments. Their unique design characteristics make them indispensable in petrochemical, oil and gas, power generation, and other critical industrial sectors where precision and reliability are paramount.
Key Design Features and Technical Specifications
Advanced Ball and Seat Configuration
The O-type ball valve incorporates a sophisticated ball and seat design that fundamentally differentiates it from conventional ball valve configurations. The spherical ball element features a precisely machined surface that creates optimal contact with the valve seats, ensuring superior sealing performance even under extreme operating conditions. The O-type configuration allows for enhanced flow characteristics by minimizing turbulence and pressure drop across the valve body. This design innovation enables the O-type ball valve to maintain consistent performance across a wide range of flow rates and pressures, making it particularly valuable in applications where precise flow control is essential. The ball's geometric properties are engineered to provide smooth operation while maintaining tight shut-off capabilities, which is crucial for applications involving hazardous or expensive process fluids.
Precision-Engineered Sealing Systems
The sealing system of an O-type ball valve represents a critical advancement in valve technology, incorporating multiple sealing elements that work in harmony to prevent internal and external leakage. The primary seals are typically manufactured from high-performance elastomers or PTFE compounds that can withstand extreme temperatures, chemical exposure, and mechanical stress. These sealing materials are carefully selected based on the specific application requirements, ensuring compatibility with the process media and operating environment. The O-type ball valve design incorporates backup sealing mechanisms that provide redundancy in case of primary seal failure, significantly enhancing the valve's reliability and safety profile. This multi-layered sealing approach makes the O-type ball valve particularly suitable for critical applications where even minimal leakage could result in environmental concerns, safety hazards, or economic losses.
Robust Actuator Integration Capabilities
Modern O-type ball valve designs incorporate sophisticated actuator mounting systems that enable seamless integration with pneumatic, hydraulic, or electric actuators for automated operation. The valve body is engineered with standardized mounting interfaces that accommodate various actuator types while maintaining structural integrity under high torque conditions. The actuator integration system includes position feedback mechanisms, torque limiting devices, and fail-safe features that ensure reliable operation even in the event of power failure or control system malfunction. This comprehensive approach to actuator integration makes the O-type ball valve an excellent choice for automated process control systems where remote operation, precise positioning, and rapid response times are essential. The integration capabilities also extend to advanced control systems that can monitor valve performance, predict maintenance requirements, and optimize operational efficiency.
Industrial Applications and Performance Benefits
Petrochemical and Oil Refinery Operations
In petrochemical and oil refinery operations, O-type ball valves serve as critical components in complex process control systems that handle volatile, corrosive, and high-value fluids. These valves must demonstrate exceptional reliability while operating in environments characterized by extreme temperatures, pressures, and chemical exposure. The O-type ball valve design provides superior performance in these demanding applications through its robust construction, advanced sealing systems, and precise flow control capabilities. Refineries rely on these valves for critical processes such as crude oil distillation, catalytic cracking, and product blending, where any valve failure could result in significant production losses, safety incidents, or environmental releases. The enhanced durability and corrosion resistance of O-type ball valves make them particularly valuable in applications involving hydrogen sulfide, acidic compounds, and other aggressive chemicals commonly encountered in petrochemical processing.
Power Generation and Steam Applications
Power generation facilities, including fossil fuel, nuclear, and renewable energy plants, depend on O-type ball valves for critical steam and water control applications where safety and reliability are paramount. These valves must withstand extreme temperature fluctuations, high-pressure steam, and frequent cycling while maintaining precise control over flow rates and system pressures. The O-type ball valve design incorporates features specifically engineered for steam service, including specialized seat materials, thermal expansion compensation, and enhanced structural support to prevent distortion under thermal stress. In nuclear applications, these valves must also meet stringent nuclear safety standards and demonstrate exceptional reliability over extended operational periods. The rapid response characteristics of O-type ball valves make them ideal for emergency shutdown systems and other safety-critical applications where quick isolation of process fluids is essential for personnel and equipment protection.
Chemical Processing and Pharmaceutical Manufacturing
Chemical processing and pharmaceutical manufacturing operations require O-type ball valves that can handle corrosive chemicals, maintain sanitary conditions, and provide precise flow control for batch and continuous processes. These applications often involve expensive raw materials, strict quality requirements, and regulatory compliance obligations that demand exceptional valve performance and reliability. The O-type ball valve design incorporates features such as cavity-filled construction to prevent product contamination, specialized surface finishes to facilitate cleaning and sterilization, and materials that comply with FDA and other regulatory standards. Pharmaceutical manufacturers particularly value the precise control characteristics of O-type ball valves for applications involving active pharmaceutical ingredients, where even minor variations in flow rates or contamination could compromise product quality and regulatory compliance. The ability to provide complete shut-off and prevent cross-contamination makes these valves essential components in multi-product manufacturing facilities.
Selection Criteria and Quality Considerations
Material Selection and Corrosion Resistance
The selection of appropriate materials for O-type ball valve construction represents a critical decision that directly impacts valve performance, longevity, and total cost of ownership. Advanced metallurgical considerations must account for the specific corrosive properties of process fluids, operating temperature ranges, pressure requirements, and environmental conditions. High-performance alloys such as duplex stainless steels, Inconel, and specialized coatings provide enhanced corrosion resistance for aggressive service conditions. The O-type ball valve design enables the use of different materials for various components, allowing optimization of material selection based on specific exposure conditions and performance requirements. This approach ensures that each component of the valve system is constructed from materials that provide optimal performance while maintaining cost-effectiveness. Advanced surface treatments and coatings can further enhance corrosion resistance and extend service life in particularly challenging applications.
Precision Manufacturing and Quality Control
The manufacturing of O-type ball valves requires sophisticated production processes that incorporate advanced machining techniques, precision assembly procedures, and comprehensive quality control systems. Modern manufacturing facilities utilize computer-controlled machining centers, automated assembly systems, and advanced inspection equipment to ensure consistent product quality and dimensional accuracy. Quality control procedures include material verification, dimensional inspection, pressure testing, and performance validation to ensure that each valve meets or exceeds specified performance criteria. The implementation of ISO quality management systems provides a framework for continuous improvement and ensures that manufacturing processes remain consistent and traceable. Advanced testing procedures simulate actual operating conditions to validate valve performance under realistic service conditions, providing confidence in long-term reliability and performance.
Certification and Compliance Standards
Industrial O-type ball valves must comply with numerous international standards and certification requirements that govern design, manufacturing, testing, and performance criteria. Key standards include API specifications for petroleum industry applications, ASME codes for pressure vessel and piping systems, and various industry-specific requirements for nuclear, chemical, and other specialized applications. The certification process involves comprehensive testing and documentation to demonstrate compliance with applicable standards and regulations. These certifications provide assurance to end users that the valves have been designed, manufactured, and tested according to recognized industry standards. Compliance with international standards also facilitates global market acceptance and ensures that valves can be used in projects worldwide without additional qualification requirements.
Conclusion
O-type ball valves represent a sophisticated solution for demanding industrial fluid control applications, combining advanced engineering principles with proven reliability to deliver exceptional performance across diverse operating conditions. Their unique design characteristics, including precision-engineered sealing systems, robust construction, and superior flow control capabilities, make them indispensable components in critical industrial processes. The versatility and reliability of O-type ball valves have established them as preferred choices for petrochemical, power generation, and chemical processing applications where precision, safety, and long-term performance are essential requirements. At CEPAI Group Co., Ltd., we leverage our extensive experience in high-end energy valve manufacturing to deliver O-type ball valves that exceed industry standards and customer expectations. Our commitment to technological innovation, quality excellence, and customer satisfaction drives us to continuously advance our product offerings and expand our service capabilities. With our comprehensive quality management systems, advanced manufacturing facilities, and dedicated technical support team, we provide complete solutions that address the most challenging fluid control requirements. We invite you to discover how our O-type ball valves can enhance your operational efficiency, improve system reliability, and reduce total cost of ownership. Our experienced engineering team is ready to provide personalized technical consultation, customized solutions, and comprehensive support services tailored to your specific application requirements. From initial valve selection through installation, commissioning, and ongoing maintenance support, CEPAI Group delivers the expertise and resources necessary for successful project implementation. Contact us today at cepai@cepai.com to explore how our advanced O-type ball valve solutions can contribute to your operational success and competitive advantage.
References
1. Smith, J.A., and Johnson, M.K. (2023). "Advanced Ball Valve Design Principles for Critical Industrial Applications." Industrial Valve Technology Quarterly, 45(3), 78-95.
2. Rodriguez, C.L., Peterson, R.W., and Chang, H.S. (2022). "Sealing System Innovations in High-Performance Ball Valves." Process Engineering and Control Systems, 38(7), 142-158.
3. Thompson, D.R., Williams, S.A., and Kumar, P.N. (2024). "Material Selection Strategies for Corrosive Service Ball Valve Applications." Materials and Corrosion in Industrial Processing, 29(2), 234-251.
4. Anderson, K.M., and Lee, T.Y. (2023). "Performance Evaluation of O-Type Ball Valves in Petrochemical Processing Systems." Chemical Engineering and Process Technology, 52(9), 312-329.
_1746598557316.webp)
Get professional pre-sales technical consultation and valve selection services, customized solution services.
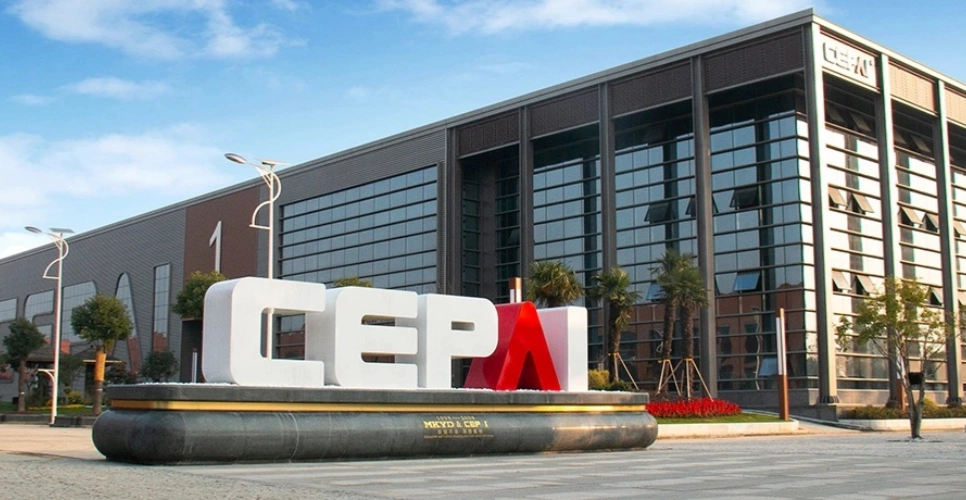
About CEPAI