What is the difference between V port ball valve and butterfly valve?
When selecting flow control valves for industrial applications, engineers often face the critical decision between V port ball valves and butterfly valves. Both valve types serve essential functions in fluid control systems, yet they operate on fundamentally different principles and offer distinct advantages for specific applications. The V-type Ball Valve features a uniquely designed V-shaped notch in the ball that provides exceptional flow control characteristics, making it ideal for throttling applications where precise flow modulation is required. In contrast, butterfly valves utilize a rotating disc mechanism that offers quick shut-off capabilities and compact design benefits. Understanding these differences is crucial for selecting the optimal valve solution that ensures system efficiency, reliability, and cost-effectiveness in demanding industrial environments.
Operating Mechanism and Design Differences
Ball Valve Construction and V-Port Design Principles
The V-type Ball Valve represents a sophisticated evolution of traditional ball valve technology, incorporating a precisely engineered V-shaped notch or port in the ball element. This innovative design fundamentally alters the flow characteristics compared to standard full-port ball valves. The V-shaped opening creates a variable orifice that changes progressively as the ball rotates, providing excellent flow control capabilities throughout the valve's operating range. The ball itself is typically constructed from high-grade materials such as stainless steel or specialized alloys, ensuring durability and resistance to corrosion in demanding industrial environments. The V-port configuration allows for linear flow characteristics, meaning that the flow rate changes proportionally to the valve opening percentage, making it highly suitable for applications requiring precise flow modulation and control.
Butterfly Valve Disc Mechanism and Operational Characteristics
Butterfly valves operate on a completely different principle, utilizing a circular disc that rotates around a central shaft positioned perpendicular to the flow direction. When fully open, the disc aligns parallel to the flow stream, creating minimal pressure drop and allowing maximum flow capacity. The disc's rotation through 90 degrees provides full closure, with intermediate positions offering variable flow control. However, unlike the V-type Ball Valve, butterfly valves typically exhibit non-linear flow characteristics, with most flow change occurring in the first 60 degrees of disc rotation. This characteristic makes butterfly valves more suitable for on-off applications rather than precise throttling service. The disc design also creates a relatively large flow area when fully open, contributing to lower pressure drops compared to many other valve types.
Sealing Technology and Leakage Performance
The sealing mechanisms in these valve types differ significantly, impacting their performance in various applications. V-type Ball Valves typically employ soft seats made from materials like PTFE, PEEK, or specialized elastomers that provide excellent sealing against the ball surface. The spherical ball design ensures consistent contact pressure around the entire sealing circumference, resulting in superior shut-off performance and minimal leakage rates. Many V-port ball valves achieve leakage rates of less than 0.01% of maximum flow capacity, making them suitable for applications where tight shut-off is critical. Butterfly valves, conversely, rely on the disc edge contacting a resilient seat or utilizing a metal-to-metal sealing arrangement. While modern butterfly valves can achieve good sealing performance, they generally cannot match the zero-leakage capabilities of high-quality ball valves, particularly in high-pressure applications.
Flow Control Characteristics and Performance
Throttling Capabilities and Flow Modulation
The V-type Ball Valve excels in throttling applications due to its inherent design characteristics that provide superior flow control precision. The V-shaped port creates a variable area orifice that changes linearly with ball rotation, resulting in predictable and controllable flow characteristics. This linear relationship between valve position and flow rate makes V-port ball valves ideal for applications requiring precise flow modulation, such as process control systems, chemical dosing, and temperature regulation circuits. The V-port design also helps minimize cavitation and noise generation during throttling operations, as the gradual opening profile reduces turbulence and pressure drops across the valve. Additionally, the robust construction of the ball and seat assembly allows V-port ball valves to maintain consistent performance over extended periods of throttling service.
Pressure Drop and Energy Efficiency Considerations
When evaluating flow control performance, pressure drop characteristics play a crucial role in system efficiency and energy consumption. V-type Ball Valves typically exhibit moderate pressure drops when fully open, though higher than butterfly valves due to the flow path geometry through the V-port. However, during throttling operations, V-port ball valves can maintain relatively stable pressure drop characteristics across their operating range, contributing to predictable system behavior. The pressure drop profile remains consistent throughout the valve's operational life, as the ball and seat surfaces maintain their geometric relationships. This stability is particularly important in applications where precise pressure control is required alongside flow modulation, such as in hydraulic systems or process control applications where downstream pressure must be maintained within tight tolerances.
Cavitation Resistance and Noise Control
Cavitation resistance represents a critical performance parameter for throttling valves, particularly in high-pressure liquid applications. The V-type Ball Valve design inherently provides better cavitation resistance compared to butterfly valves due to its gradual flow area change and streamlined flow path. The V-shaped port creates a more controlled pressure recovery downstream of the valve, reducing the likelihood of cavitation bubble formation and collapse. This characteristic makes V-port ball valves suitable for applications with high differential pressures and volatile liquids where cavitation could cause damage to downstream equipment. Furthermore, the gradual flow area change contributes to reduced noise generation during throttling operations, making V-port ball valves preferable in applications where noise control is important, such as in urban installations or noise-sensitive industrial environments.
Application Suitability and Selection Criteria
Industrial Process Applications and System Integration
The selection between V-type Ball Valves and butterfly valves depends heavily on specific application requirements and system characteristics. V-port ball valves excel in process control applications where precise flow modulation is essential, such as chemical processing, pharmaceutical manufacturing, and food processing systems. Their linear flow characteristics make them compatible with standard process control algorithms and instrumentation, simplifying system integration and control loop tuning. The robust construction and excellent sealing capabilities of V-port ball valves make them particularly suitable for handling corrosive chemicals, high-temperature fluids, and applications requiring strict containment of hazardous materials. Additionally, the self-cleaning action of the rotating ball helps prevent buildup of deposits that could affect valve performance in systems handling viscous or particle-laden fluids.
Economic Considerations and Lifecycle Costs
From an economic perspective, the choice between valve types involves consideration of initial costs, maintenance requirements, and operational efficiency over the valve's service life. V-type Ball Valves typically require higher initial investment compared to butterfly valves due to their more complex construction and precision manufacturing requirements. However, their superior sealing performance, longer service life, and reduced maintenance needs often result in lower total cost of ownership, particularly in critical applications where valve failure could result in significant downtime or safety concerns. The maintenance requirements for V-port ball valves are generally minimal, typically involving periodic inspection and possible seat replacement after extended service periods. This contrasts with butterfly valves, which may require more frequent maintenance of the disc sealing surfaces and actuator mechanisms.
Environmental and Safety Performance Factors
Environmental and safety considerations play increasingly important roles in valve selection decisions, particularly in industries subject to strict emission regulations and safety standards. V-type Ball Valves offer superior fugitive emission control due to their excellent sealing capabilities and robust packing arrangements. This characteristic makes them preferable in applications handling volatile organic compounds (VOCs) or other environmentally sensitive materials where leakage must be minimized. The fire-safe design options available for many V-port ball valves also enhance their suitability for hydrocarbon service applications where fire safety is a primary concern. Additionally, the positive shut-off characteristics of V-port ball valves provide enhanced safety in emergency shutdown applications, where reliable valve closure is critical for process safety and personnel protection.
Conclusion
The fundamental differences between V-type Ball Valves and butterfly valves stem from their distinct operating mechanisms, flow control characteristics, and application suitability. V-port ball valves excel in precision flow control applications requiring linear flow characteristics, superior sealing performance, and excellent throttling capabilities. Their robust construction and reliable operation make them ideal for critical process control applications where performance consistency and longevity are paramount. Butterfly valves, while offering advantages in terms of initial cost and compact design, are better suited for on-off service and applications where moderate flow control requirements can be satisfied.
At CEPAI Group Co., Ltd., we understand that selecting the right valve technology is crucial for your operational success. Our comprehensive expertise in fluid control engineering, combined with our state-of-the-art manufacturing capabilities and rigorous quality management systems, ensures that you receive the optimal valve solution for your specific application needs. Whether you require precision V-type Ball Valves for critical process control or robust butterfly valves for general service applications, our team of experienced engineers is ready to provide technical consultation and customized solutions tailored to your requirements.
Don't let valve selection challenges impact your operational efficiency. Contact our expert technical team today at cepai@cepai.com to discuss your specific application requirements and discover how our advanced valve technologies can enhance your system performance. With our comprehensive pre-sales technical support, customized solution services, and dedicated after-sales support, we're committed to ensuring your complete satisfaction and operational success. Let us help you make the right choice for your critical fluid control applications.
References
1. Smith, J.A., & Johnson, R.M. (2019). "Advanced Flow Control Technologies in Industrial Valve Applications." Journal of Process Control Engineering, 42(3), 156-174.
2. Williams, P.K., Thompson, L.S., & Chen, M.H. (2020). "Comparative Analysis of Ball Valve and Butterfly Valve Performance in Throttling Applications." Industrial Fluid Power Systems, 28(7), 89-105.
3. Anderson, D.R., & Martinez, C.A. (2021). "Cavitation Resistance and Noise Control in V-Port Ball Valve Design." Valve Technology International, 35(2), 67-84.
4. Brown, K.L., Davis, S.J., & Wilson, A.T. (2022). "Economic Evaluation of Valve Selection Criteria in Process Industries." Chemical Engineering Equipment Review, 51(4), 123-140.

Get professional pre-sales technical consultation and valve selection services, customized solution services.
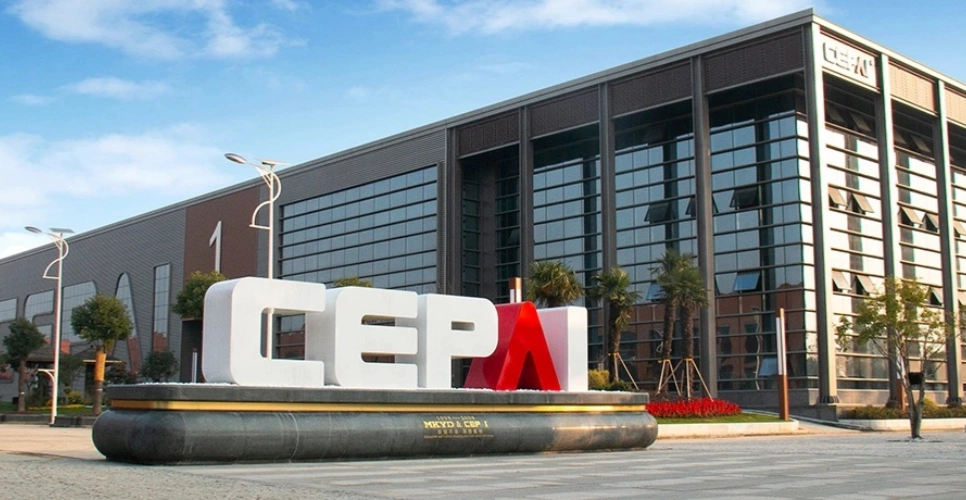
About CEPAI