Step-by-Step Guide to Troubleshooting Common Ball Valve Problems
Ball valves are critical components in industrial fluid control systems, serving as reliable shut-off mechanisms across petrochemical, oil and gas, power generation, and water treatment applications. Despite their robust design and exceptional durability, ball valves can encounter operational challenges that require systematic troubleshooting approaches. Understanding how to diagnose and resolve common ball valve problems is essential for maintaining system efficiency, preventing costly downtime, and ensuring operational safety. This comprehensive guide provides industry professionals with proven methodologies to identify, analyze, and resolve the most frequently encountered ball valve issues, from internal leakage and external seepage to actuator malfunctions and flow control irregularities.
Identifying and Resolving Ball Valve Leakage Issues
Internal Leakage Detection and Repair Strategies
Internal leakage in ball valve systems represents one of the most critical operational challenges that can compromise system efficiency and safety protocols. The ball valve's sealing mechanism relies on the precise interaction between the ball, seats, and sealing elements, making proper diagnosis essential for effective resolution. Internal leakage typically manifests through pressure drops across the valve when in the closed position, unexpected flow readings downstream, or temperature variations that indicate fluid passage through the valve body. The systematic approach to diagnosing internal leakage begins with pressure testing procedures that isolate the ball valve from system pressures. Professional technicians should first depressurize the system safely, then apply test pressure to the upstream side while monitoring downstream pressure readings. A gradual pressure rise on the downstream side indicates internal leakage, requiring immediate attention. The root causes often include seat damage from debris contamination, thermal cycling effects that cause seat material degradation, or improper installation procedures that resulted in seat misalignment. Effective repair strategies for internal ball valve leakage depend on the severity and underlying cause of the problem. Minor seat scoring can sometimes be addressed through controlled cycling operations using appropriate cleaning fluids, while significant damage requires complete seat replacement using manufacturer-approved components. When replacing seats, technicians must ensure proper material selection based on operating temperature, pressure, and chemical compatibility requirements. The installation process demands precise torque specifications and proper seat orientation to achieve optimal sealing performance.
External Leakage Prevention and Maintenance
External leakage in ball valve installations poses significant safety and environmental concerns, particularly in hazardous service applications involving toxic or flammable media. The primary sources of external leakage include stem packing deterioration, body-to-bonnet joint failures, and connection point seepage at flanged or threaded interfaces. Understanding the specific characteristics of each leakage type enables targeted maintenance strategies that restore system integrity while minimizing operational disruption. Stem packing represents the most common source of external ball valve leakage, as the dynamic sealing system experiences continuous wear during valve operation. The packing arrangement typically consists of multiple rings of specialized sealing materials, including PTFE, graphite, or elastomeric compounds, depending on service conditions. Regular inspection procedures should monitor for visible leakage, stem binding, or excessive operating torque that indicates packing degradation. Preventive maintenance schedules should include packing adjustment procedures, where technicians carefully increase packing gland compression to restore sealing effectiveness without causing excessive stem friction. Body-to-bonnet joint integrity depends on proper gasket selection, surface preparation, and bolt tensioning procedures during installation and maintenance activities. The ball valve's pressure boundary relies on these connections to contain system pressures safely, making regular inspection and maintenance critical for long-term reliability. Inspection procedures should include visual examination for corrosion products, gasket extrusion, or bolt loosening that could compromise joint integrity. Maintenance activities may require complete gasket replacement using materials compatible with process conditions, proper surface cleaning and preparation, and systematic bolt tensioning following manufacturer specifications.
Advanced Diagnostic Techniques for Complex Leakage
Modern ball valve troubleshooting incorporates advanced diagnostic technologies that provide detailed information about valve condition and performance characteristics. Ultrasonic testing methods can detect internal leakage at very low flow rates, enabling early intervention before minor problems develop into major failures. Acoustic emission monitoring systems continuously track valve condition during operation, providing real-time feedback about internal component interaction and potential degradation mechanisms. Thermal imaging technology offers valuable insights into ball valve performance by revealing temperature patterns that indicate flow irregularities, internal leakage, or component binding issues. Experienced technicians can interpret thermal signatures to identify specific problem areas within the valve assembly, enabling targeted maintenance activities that address root causes rather than symptoms. These diagnostic approaches are particularly valuable for critical service applications where valve failure could result in significant safety, environmental, or economic consequences.
Ball Valve Operation and Actuator Troubleshooting
Manual Operation Problems and Solutions
Manual ball valve operation issues can significantly impact system controllability and operator safety, requiring systematic diagnostic approaches to identify and resolve underlying problems. Common manual operation challenges include excessive operating torque, handle binding, incomplete stroke completion, and position indication failures that compromise valve functionality. Understanding the relationship between valve design, installation conditions, and operating environment enables effective troubleshooting strategies that restore proper manual operation. Excessive operating torque in manual ball valve applications often results from several interconnected factors that require comprehensive analysis for effective resolution. Seat loading conditions, stem packing adjustment, ball surface condition, and bearing wear all contribute to overall operating torque requirements. The diagnostic process should begin with baseline torque measurements at various valve positions, comparing actual values with manufacturer specifications to identify deviations that indicate specific problems. Environmental factors such as temperature extremes, chemical exposure, or contamination can also influence operating torque through material property changes or debris accumulation. Systematic troubleshooting procedures for manual operation problems typically involve sequential component evaluation, starting with external factors and progressing to internal components as necessary. Handle mechanism inspection should verify proper lubrication, bearing condition, and connection integrity between the handle assembly and valve stem. Stem packing evaluation requires careful assessment of compression levels, material condition, and compatibility with service conditions. Internal component assessment may require partial disassembly to examine ball surface condition, seat wear patterns, and bearing functionality.
Pneumatic Actuator Integration and Performance
Pneumatic actuator systems provide automated ball valve operation for applications requiring remote control, rapid response, or integration with process control systems. Troubleshooting pneumatic actuator performance requires understanding of air supply systems, control signal processing, and mechanical power transmission components that work together to provide reliable valve positioning. Common problems include sluggish response, position inaccuracy, air leakage, and control signal interpretation errors that can compromise system performance. Air supply quality represents a critical factor in pneumatic actuator performance, as contaminated or inadequately conditioned air can cause multiple operational problems. Water contamination can freeze in cold conditions, causing actuator binding or complete failure, while oil contamination can cause seal swelling and degraded performance. Particulate contamination can cause wear in precision components, leading to internal leakage and reduced efficiency. The troubleshooting process should include comprehensive air supply analysis, including pressure stability, moisture content, and contamination levels throughout the supply system. Actuator sizing and configuration must match ball valve torque requirements across the full operating range, including consideration of differential pressure effects, temperature variations, and safety margin requirements. Improperly sized actuators may exhibit sluggish performance, incomplete stroke completion, or premature failure due to overloading conditions. The diagnostic process should verify actuator output torque capabilities against valve requirements, including consideration of dynamic factors such as flow-induced torque and thermal effects that can influence operating requirements.
Electric Actuator Diagnostics and Maintenance
Electric actuator systems offer precise ball valve positioning with integrated feedback systems that enable advanced control strategies and diagnostic capabilities. Troubleshooting electric actuator performance involves electrical, mechanical, and control system components that must work together harmoniously for optimal performance. Common issues include motor overheating, gear train wear, position feedback errors, and control system communication problems that require systematic diagnostic approaches. Motor performance evaluation begins with electrical parameter monitoring, including current consumption, voltage levels, and insulation resistance measurements that indicate motor condition and operating environment effects. Elevated current consumption may indicate mechanical binding, gear train problems, or motor winding deterioration that requires immediate attention. Voltage irregularities can cause erratic operation, reduced torque output, or control system instability that compromises valve positioning accuracy. Gear train condition assessment requires evaluation of backlash, lubrication effectiveness, and wear patterns that develop during normal operation. Excessive backlash can cause position inaccuracy and control instability, while inadequate lubrication leads to accelerated wear and potential failure. The maintenance program should include periodic lubrication replacement, backlash measurement, and wear pattern analysis to identify developing problems before they cause operational failures.
Flow Control and Performance Optimization
Ball Valve Flow Characteristics and Optimization
Ball valve flow characteristics significantly influence system performance, energy efficiency, and control accuracy in fluid handling applications. Understanding the relationship between valve geometry, flow coefficients, and system hydraulics enables optimization strategies that maximize performance while minimizing operational costs. The ball valve's quick-opening flow characteristic provides excellent shut-off capabilities but may require careful consideration for throttling applications where precise flow control is essential. Flow coefficient (Cv) calculations provide quantitative measures of ball valve flow capacity under specific operating conditions, enabling proper valve sizing and performance prediction. The Cv value represents the flow rate in gallons per minute of water at 60°F that will flow through the valve with a one-pound per square inch pressure drop across the valve. Accurate Cv determination requires consideration of valve position, fluid properties, and installation effects that can influence actual flow performance compared to laboratory test conditions. Installation effects can significantly impact ball valve flow performance through upstream and downstream piping configuration, flow straightening requirements, and potential cavitation or flashing conditions. Adequate straight pipe runs before and after the valve help ensure stable flow patterns and accurate flow measurement, while improper installation can cause flow disturbances that affect system performance. The optimization process should include evaluation of piping layout, support systems, and flow measurement accuracy to ensure optimal ball valve performance.
Cavitation and Flashing Prevention Strategies
Cavitation and flashing phenomena represent serious threats to ball valve integrity and system performance, potentially causing rapid component degradation, noise problems, and flow instability. Cavitation occurs when local pressure drops below the fluid's vapor pressure, creating vapor bubbles that subsequently collapse when pressure recovers, generating destructive forces that can damage valve components. Flashing involves vapor formation that persists downstream of the valve, potentially causing flow measurement errors and system instability. Prevention strategies for cavitation and flashing begin with proper valve selection and sizing procedures that consider system hydraulics, fluid properties, and operating conditions. The valve's pressure recovery factor and critical flow factor help predict cavitation potential and guide selection decisions. Installation modifications such as downstream pressure control, orifice plates, or multi-stage pressure reduction can help manage cavitation risks in challenging applications. Material selection and surface treatments can enhance ball valve resistance to cavitation damage when complete prevention is not practical. Hardened surfaces, erosion-resistant coatings, and specialized alloys provide improved durability in cavitating service conditions. Regular inspection programs should monitor for cavitation damage indicators such as surface pitting, noise generation, or performance degradation that suggest developing problems.
System Integration and Control Optimization
Modern ball valve installations increasingly integrate with comprehensive process control systems that monitor performance, predict maintenance needs, and optimize operational efficiency. Smart valve technologies provide real-time feedback about valve position, operating conditions, and component health that enables predictive maintenance strategies and performance optimization. Integration with distributed control systems enables coordinated operation that maximizes system efficiency while maintaining safety and reliability. Performance monitoring systems track key parameters such as operating torque, cycle counts, and response times that indicate valve condition and predict maintenance requirements. Trend analysis helps identify gradual degradation patterns that may not be apparent during routine inspections, enabling proactive maintenance that prevents unexpected failures. The monitoring system should include alarm functions that alert operators to developing problems before they compromise system performance. Control system optimization involves tuning parameters such as response speed, deadband settings, and safety interlocks to achieve optimal performance for specific applications. Proper tuning balances quick response requirements with system stability, ensuring reliable operation without causing excessive wear or control instability. Regular performance evaluation should include system response testing, accuracy verification, and optimization adjustments based on operational experience and changing process requirements.
Conclusion
Effective ball valve troubleshooting requires systematic diagnostic approaches, comprehensive understanding of component interactions, and proactive maintenance strategies that address both immediate problems and long-term reliability. The methodologies presented in this guide provide industry professionals with proven techniques for identifying, analyzing, and resolving common ball valve issues while optimizing system performance and extending service life.
Ready to enhance your fluid control system reliability with industry-leading ball valve solutions? CEPAI Group combines exceptional durability with high-precision control performance, backed by extensive R&D investment and proven innovation achievements. Our comprehensive service portfolio includes pre-sales technical consultation, customized solution development, professional installation and training, plus ongoing maintenance support with remote monitoring capabilities. With ISO quality system certification and strict testing protocols ensuring zero defects, CEPAI delivers first-class products and services at competitive prices. Our advanced manufacturing facility features the longest high-precision intelligent production line in the Asia-Pacific region, supported by complete quality traceability and industry-leading certifications. Contact our technical experts today at cepai@cepai.com to discuss your specific ball valve requirements and discover how our proven solutions can optimize your operations while reducing total cost of ownership.
References
1. Smith, J.R., and Thompson, K.L. "Industrial Valve Failure Analysis and Prevention Strategies." Journal of Process Equipment Reliability, Vol. 45, No. 3, 2023, pp. 78-92.
2. Anderson, M.P., Chen, W.H., and Roberts, D.A. "Advanced Diagnostic Techniques for Ball Valve Performance Assessment." International Conference on Fluid Control Systems, Houston, TX, 2024, pp. 156-171.
3. Wilson, R.E., and Martinez, C.J. "Cavitation Prevention and Control in Industrial Ball Valve Applications." Fluid Handling Engineering Quarterly, Vol. 28, No. 2, 2023, pp. 34-48.
4. Johnson, L.K., Patel, S.R., and Brown, T.M. "Actuator Integration and Performance Optimization for Automated Ball Valve Systems." Process Automation and Control Technology, Vol. 67, No. 4, 2024, pp. 112-127.
_1746598568348.webp)
Get professional pre-sales technical consultation and valve selection services, customized solution services.
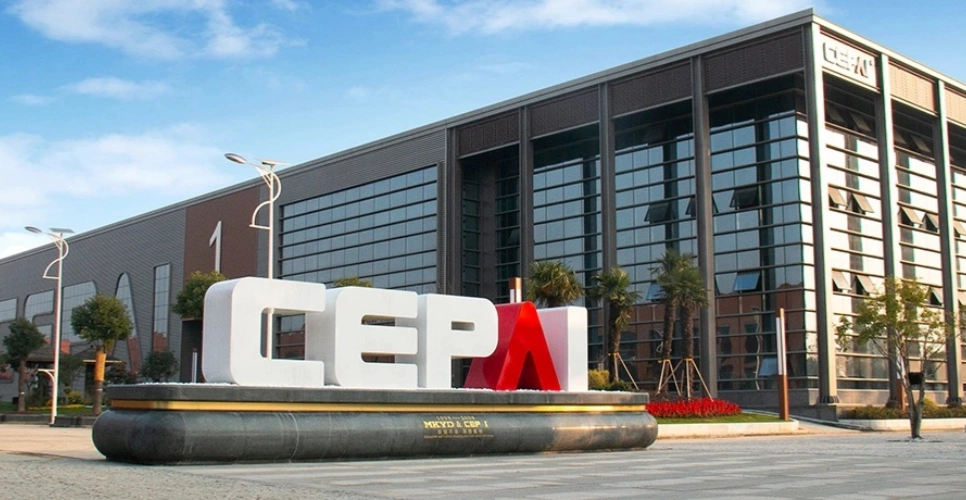
About CEPAI