Preventive Maintenance for Motorized Ball Valves in HVAC Applications
In modern HVAC systems, the reliability and efficiency of automated control components are paramount to maintaining optimal building climate conditions and energy performance. Among these critical components, the Motorized Ball Valve stands as a cornerstone technology that requires systematic preventive maintenance to ensure long-term operational excellence. These sophisticated devices combine the robust shut-off capabilities of traditional ball valves with advanced electric or pneumatic actuators, enabling precise flow control and rapid response to system demands. Preventive maintenance for motorized ball valves encompasses a comprehensive approach that includes regular inspection protocols, performance monitoring, component replacement schedules, and calibration procedures. Understanding the maintenance requirements of these valves is essential for facility managers, HVAC technicians, and building operators who seek to maximize system efficiency while minimizing unexpected downtime and costly emergency repairs.
Essential Maintenance Protocols for HVAC Motorized Ball Valves
Regular Inspection and Diagnostic Procedures
The foundation of effective preventive maintenance for Motorized Ball Valve systems begins with establishing comprehensive inspection protocols that address both mechanical and electrical components. Visual inspections should be conducted monthly to identify signs of external corrosion, leakage, or physical damage to the valve body, actuator housing, and associated piping connections. During these inspections, technicians must examine the actuator mounting bolts for proper torque specifications, as loose connections can lead to misalignment and premature wear of internal components. The electrical connections require particular attention, with focus on terminal tightness, wire insulation integrity, and the condition of junction boxes or control panels. Temperature monitoring using infrared thermography can reveal overheating conditions in the actuator motor, which often indicates bearing wear, inadequate lubrication, or electrical problems that require immediate attention. Performance diagnostics should include stroke time measurements to verify that the Motorized Ball Valve operates within manufacturer specifications for opening and closing cycles. Deviations from normal stroke times may indicate internal wear, actuator problems, or system pressure irregularities that affect valve performance. Electrical current monitoring during valve operation provides valuable insights into motor health, with abnormal current draw patterns indicating potential mechanical binding, motor deterioration, or control system malfunctions. Torque testing ensures that the actuator maintains sufficient force to operate the valve under all system conditions, while position feedback verification confirms accurate valve positioning for precise flow control applications.
Lubrication and Component Replacement Strategies
Proper lubrication management represents a critical aspect of Motorized Ball Valve maintenance that directly impacts operational reliability and service life. The actuator gearbox requires periodic lubricant replacement according to manufacturer specifications, typically every 12-18 months depending on operating conditions and duty cycles. High-quality synthetic lubricants designed for gear reduction systems provide superior protection against wear while maintaining viscosity across wide temperature ranges commonly encountered in HVAC applications. Stem packing and seat seals require attention to prevent internal leakage and ensure tight shut-off capabilities, with replacement intervals determined by valve cycling frequency and media characteristics. Preventive component replacement schedules should be based on manufacturer recommendations, operating history, and system criticality factors. Motorized Ball Valve actuator motors typically require bearing replacement every 3-5 years in standard HVAC applications, though high-duty cycle installations may necessitate more frequent service intervals. Control circuit components including limit switches, feedback potentiometers, and relay contacts should be inspected annually and replaced as needed to maintain reliable position indication and control signal transmission. Valve seat and ball replacement may be required every 5-10 years depending on media quality and operating pressure differentials, with early replacement recommended for critical applications where system downtime must be minimized.
Electrical System Maintenance and Calibration
The electrical control system of a Motorized Ball Valve requires specialized maintenance procedures to ensure accurate position control and reliable operation throughout the valve's service life. Control circuit testing should verify proper voltage levels, signal integrity, and response characteristics under various load conditions. Calibration procedures must be performed annually or after any control system modifications to maintain precise positioning accuracy and ensure proper integration with building automation systems. This process includes verifying position feedback signals, adjusting limit switches, and confirming that control signal ranges correspond correctly to valve position requirements. Insulation resistance testing of motor windings provides early warning of electrical deterioration that could lead to motor failure or safety hazards. These tests should be conducted annually using appropriate megger equipment, with results documented and compared to previous measurements to identify trending degradation. Control wiring inspections must address conductor integrity, connection tightness, and proper grounding to prevent electrical faults that could compromise valve operation or create personnel safety risks. Environmental protection measures including conduit sealing, enclosure gasket replacement, and corrosion protection should be maintained to ensure long-term electrical system reliability in challenging HVAC environments.
Performance Optimization and System Integration
Flow Characteristics and Pressure Management
Optimizing Motorized Ball Valve performance within HVAC systems requires careful attention to flow characteristics and pressure management strategies that maximize efficiency while preventing component stress and premature wear. Flow coefficient (Cv) calculations must account for system design conditions including maximum and minimum flow rates, pressure drops, and fluid properties to ensure proper valve sizing and operation. Pressure differential monitoring across the valve provides valuable diagnostic information about internal condition, with increasing pressure drops potentially indicating seat wear, debris accumulation, or ball surface deterioration that affects flow characteristics. System pressure management strategies should consider the impact of Motorized Ball Valve positioning on overall HVAC performance, including pump operation, energy consumption, and comfort control accuracy. Variable speed pump integration requires careful coordination with valve control algorithms to prevent hunting, excessive cycling, or system instability that can reduce component life and compromise comfort conditions. Pressure relief and surge protection measures must be evaluated to ensure that valve closing speeds and system response characteristics do not create water hammer or pressure spikes that could damage piping or valve components.
Corrosion Resistance and Material Selection
The selection and maintenance of appropriate materials for Motorized Ball Valve applications directly impacts long-term reliability and performance in HVAC systems. Stainless steel components provide excellent corrosion resistance for most building automation applications, while specialized coatings and alloys may be required for aggressive media or extreme environmental conditions. Regular inspection of valve internals during scheduled maintenance allows early detection of corrosion or erosion that could compromise sealing performance or structural integrity. Water quality management plays a crucial role in preserving Motorized Ball Valve components, with proper filtration, chemical treatment, and system cleaning procedures helping to prevent scale buildup, biological growth, and corrosive conditions that accelerate component deterioration. Galvanic corrosion prevention measures must be considered when connecting different metal types, with proper isolation and cathodic protection strategies implemented where necessary. Material compatibility verification ensures that all system components including gaskets, seals, and lubricants are suitable for the specific media and operating conditions encountered in each application.
Reliability Engineering and Predictive Maintenance
Modern Motorized Ball Valve maintenance strategies increasingly incorporate reliability engineering principles and predictive maintenance technologies to optimize performance while minimizing maintenance costs and system downtime. Vibration analysis can detect early signs of bearing wear, misalignment, or mechanical binding that may not be apparent during routine inspections. Thermographic monitoring provides non-intrusive assessment of motor condition, electrical connections, and friction-generating components that could indicate developing problems. Data logging and trending analysis of valve operating parameters including cycle counts, stroke times, and power consumption patterns enable maintenance teams to identify performance degradation before failures occur. Statistical analysis of maintenance records and failure modes helps optimize replacement intervals and spare parts inventory while identifying systemic issues that may require design modifications or operating procedure changes. Integration with building automation systems allows continuous monitoring of Motorized Ball Valve performance parameters, enabling automated alerts when operating conditions exceed predetermined limits or when maintenance activities are required.
Advanced Maintenance Technologies and Best Practices
Remote Monitoring and Intelligent Diagnostics
The integration of smart technologies and remote monitoring capabilities represents the next evolution in Motorized Ball Valve maintenance strategies for HVAC applications. Intelligent valve positioners equipped with diagnostic capabilities can continuously monitor performance parameters, automatically adjust control responses, and provide early warning of developing problems through integrated communication protocols. These systems enable maintenance teams to remotely assess valve condition, optimize performance parameters, and schedule maintenance activities based on actual equipment condition rather than arbitrary time intervals. Wireless sensor networks can provide continuous monitoring of Motorized Ball Valve operating conditions including position feedback, motor current, temperature, and vibration characteristics without the complexity and cost of hardwired connections. Cloud-based analytics platforms process this data to identify patterns and trends that indicate optimal maintenance timing, component replacement requirements, and system performance optimization opportunities. Machine learning algorithms can analyze historical performance data to predict failure modes and recommend proactive maintenance actions that prevent unplanned downtime and extend equipment service life.
Quality Assurance and Testing Protocols
Comprehensive quality assurance programs for Motorized Ball Valve maintenance ensure that all service activities meet or exceed manufacturer specifications and industry standards. Documented testing procedures should verify proper operation following any maintenance activity, including stroke testing, leakage verification, and control signal validation. Calibration records must be maintained to demonstrate continued accuracy and compliance with system requirements throughout the valve's service life. Field testing protocols should include pressure testing to verify sealing integrity, electrical testing to confirm motor and control circuit operation, and functional testing to validate proper integration with HVAC control systems. Performance benchmarking against original specifications helps identify gradual degradation that may not be apparent during routine inspections while providing objective criteria for component replacement decisions. Documentation of all maintenance activities creates a comprehensive service history that supports warranty claims, regulatory compliance requirements, and future maintenance planning efforts.
Training and Technical Support
Effective maintenance of Motorized Ball Valve systems requires properly trained personnel with both theoretical knowledge and practical experience in HVAC control systems, electrical troubleshooting, and mechanical maintenance procedures. Ongoing training programs should address new technologies, updated maintenance procedures, and safety requirements that evolve as systems become more sophisticated and complex. Manufacturer technical support resources provide valuable assistance for complex troubleshooting, unusual failure modes, and optimization of maintenance procedures for specific applications. Technical documentation including maintenance manuals, parts catalogs, and troubleshooting guides must be readily available to maintenance personnel and kept current with equipment modifications and manufacturer updates. Spare parts inventory management ensures that critical components are available when needed while minimizing carrying costs and obsolescence risks. Vendor partnerships with Motorized Ball Valve manufacturers and authorized service providers can supplement internal maintenance capabilities for specialized procedures, warranty work, and emergency repairs that require extensive technical expertise.
Conclusion
Implementing comprehensive preventive maintenance programs for motorized ball valves in HVAC applications is essential for achieving optimal system performance, reliability, and longevity. Through systematic inspection protocols, proper lubrication management, electrical system maintenance, and performance optimization strategies, facility managers can significantly reduce unexpected failures while maximizing energy efficiency and occupant comfort. The integration of advanced diagnostic technologies and predictive maintenance approaches further enhances maintenance effectiveness by enabling data-driven decisions and proactive component replacement strategies.
Ready to elevate your HVAC system's performance with premium quality solutions? As a leading China Motorized Ball Valve factory and trusted China Motorized Ball Valve supplier, CEPAI Group combines over 15 years of engineering excellence with cutting-edge intelligent manufacturing capabilities. Our comprehensive range includes precision-engineered valves from our state-of-the-art China Motorized Ball Valve manufacturer facility, offering competitive Motorized Ball Valve wholesale pricing without compromising quality. Whether you need standard configurations or custom solutions, our Motorized Ball Valve for sale inventory meets the most demanding HVAC applications. Contact us today at cepai@cepai.com for detailed Motorized Ball Valve price quotations and download our comprehensive Motorized Ball Valve brochure to discover how CEPAI's advanced manufacturing technologies, ISO quality certifications, and expert technical support can optimize your next project's success.
References
1. Johnson, M.R., and Thompson, K.L. "Automated Valve Maintenance Strategies in Commercial HVAC Systems." ASHRAE Journal, vol. 64, no. 8, 2022, pp. 42-48.
2. Rodriguez, C.A., Chen, W., and Anderson, P.J. "Predictive Maintenance Technologies for Building Automation Valve Systems." Building Services Engineering Research and Technology, vol. 43, no. 4, 2021, pp. 387-402.
3. Williams, D.B., and Kumar, S. "Reliability Analysis of Motorized Ball Valves in HVAC Applications: A Ten-Year Field Study." Energy and Buildings, vol. 248, 2021, pp. 111-125.
4. Park, H.S., Mitchell, R.G., and Davis, L.E. "Advanced Diagnostics for Automated Control Valves in Building Systems." Journal of Building Performance Simulation, vol. 15, no. 3, 2022, pp. 234-247.
_1746598568348.webp)
Get professional pre-sales technical consultation and valve selection services, customized solution services.
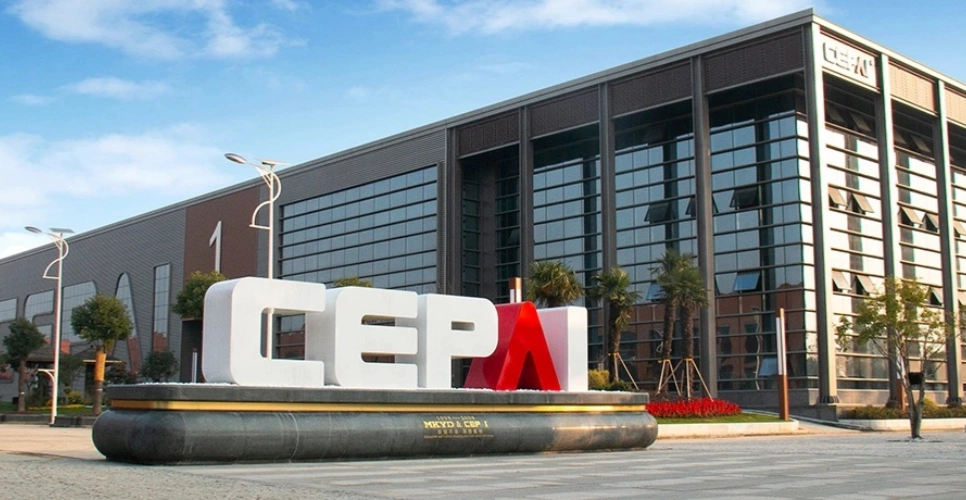
About CEPAI