A Complete Guide to Choosing Ball Valves for Industrial Automation
Industrial automation systems demand precise flow control solutions that can operate reliably under demanding conditions. Ball valves have emerged as one of the most versatile and dependable components in modern industrial applications, offering excellent shut-off capabilities, minimal pressure drop, and superior durability. This comprehensive guide explores the critical factors that engineers and procurement professionals must consider when selecting ball valves for industrial automation systems. From understanding different valve configurations to evaluating performance characteristics, this article provides essential insights for making informed decisions that ensure optimal system performance, safety, and long-term operational efficiency in various industrial environments.
Understanding Ball Valve Fundamentals for Industrial Applications
Ball Valve Design Principles and Operational Mechanics
Ball valves represent a quarter-turn valve family that utilizes a spherical disc with a bore through its center to control flow. The fundamental design principle centers on the ball's rotation within the valve body, where the bore aligns with the pipeline for full flow or perpendicular to it for complete shut-off. This simple yet effective mechanism makes ball valves particularly suitable for industrial automation applications requiring rapid response times and precise control. The ball valve design incorporates several critical components including the valve body, ball, seats, stem, and actuator interface, each contributing to the overall performance characteristics. The operational mechanics of ball valves in industrial automation systems involve precise positioning control through automated actuators. When integrated with control systems, ball valves can achieve positioning accuracy within fractions of degrees, enabling fine flow control in critical processes. The low torque requirements for operation make ball valves ideal for frequent cycling applications, while their robust construction ensures reliable performance under varying pressure and temperature conditions. Understanding these fundamental principles helps engineers select appropriate ball valve configurations that align with specific automation requirements and process demands.
Material Selection and Construction Standards
Material selection represents a crucial factor in ball valve performance, directly impacting durability, corrosion resistance, and operational reliability. Industrial automation applications often expose ball valves to aggressive media, extreme temperatures, and high-pressure conditions, necessitating careful material consideration. Common body materials include carbon steel, stainless steel, and specialized alloys, each offering distinct advantages for specific applications. The ball itself typically utilizes hardened stainless steel or specialized coatings to resist wear and corrosion, while seats may incorporate PTFE, PEEK, or metal designs depending on service conditions. Construction standards play an equally important role in ensuring ball valve reliability and safety in industrial automation systems. International standards such as API 6D, ASME B16.34, and ISO 17292 provide comprehensive guidelines for design, materials, testing, and performance requirements. These standards ensure consistent quality and interchangeability while establishing minimum performance criteria for various service conditions. Compliance with relevant standards not only guarantees product quality but also facilitates integration with existing systems and ensures regulatory compliance across different industries and geographical regions.
Flow Characteristics and Performance Metrics
Flow characteristics represent fundamental performance parameters that determine ball valve suitability for specific industrial automation applications. The inherent flow characteristic of ball valves typically exhibits a quick-opening behavior, where small initial movements produce significant flow changes. This characteristic proves advantageous in on-off applications but may require careful consideration in modulating control scenarios. The flow coefficient (Cv) provides a standardized measure of valve capacity, enabling engineers to properly size valves for specific flow requirements and pressure drops. Performance metrics extend beyond basic flow characteristics to include factors such as leakage rates, pressure ratings, temperature limits, and cycling capabilities. Modern ball valves designed for industrial automation often achieve Class VI leakage rates, providing virtually bubble-tight shut-off performance. Pressure ratings typically range from standard ANSI classes to specialized high-pressure designs exceeding 10,000 PSI. Temperature capabilities vary significantly based on materials and design, with some specialized ball valves operating effectively from cryogenic conditions to over 1000°F. Understanding these performance metrics enables proper valve selection that ensures reliable operation within specified service parameters.
Critical Selection Criteria for Industrial Automation Ball Valves
Precise Control and Rapid Response Requirements
Industrial automation systems demand ball valves capable of delivering precise control with rapid response characteristics to maintain process stability and product quality. Modern ball valve designs incorporate advanced seat technologies and stem sealing systems that enable accurate positioning control while minimizing dead time and hysteresis. The relationship between valve opening and flow rate becomes critical in applications requiring proportional control, where even minor positioning errors can significantly impact process performance. Advanced ball valve designs utilize characterized balls or specially designed port geometries to achieve more linear flow characteristics suitable for modulating control applications. Rapid response capabilities prove essential in applications requiring quick shut-off or emergency isolation functions. Ball valves inherently provide fast operation due to their quarter-turn design, typically achieving full stroke operation in seconds rather than minutes required by multi-turn valves. This rapid response capability becomes particularly valuable in safety instrumented systems (SIS) where quick isolation prevents equipment damage or safety hazards. The combination of precise positioning control and rapid response makes ball valves ideal for critical control loops in petrochemical, power generation, and manufacturing processes where process stability directly impacts product quality and operational safety. The integration of smart positioners and diagnostic capabilities further enhances precise control and response characteristics. Modern pneumatic and electric actuators equipped with digital positioners can achieve positioning accuracy within 0.1% of full scale while providing real-time feedback on valve position and performance. These advanced control systems enable predictive maintenance strategies by monitoring valve performance trends and identifying potential issues before they impact process operations. The ability to remotely monitor and adjust valve performance parameters ensures consistent control quality while reducing maintenance requirements and operational costs.
Pressure Resistance and Corrosion Performance
Pressure resistance represents a fundamental requirement for ball valves operating in industrial automation systems, where process pressures can range from vacuum conditions to several thousand PSI. The pressure rating of ball valves depends on multiple factors including body material, size, temperature, and design configuration. Full-bore ball valves typically provide higher pressure ratings compared to reduced-bore designs due to their robust construction and uniform stress distribution. Understanding the relationship between pressure, temperature, and material properties enables proper valve selection that ensures safe operation throughout the expected service life. Corrosion resistance proves equally critical in determining ball valve longevity and reliability, particularly in chemical processing and offshore applications where aggressive media can rapidly degrade inadequately protected components. The selection of appropriate body materials, trim materials, and protective coatings must consider the specific chemical composition, concentration, and temperature of process fluids. Stainless steel alloys such as 316L provide excellent general corrosion resistance, while specialized alloys like Hastelloy or Inconel may be required for highly aggressive environments. Proper material selection based on comprehensive corrosion analysis ensures reliable operation while minimizing maintenance requirements and replacement costs. The combination of pressure resistance and corrosion performance determines the overall durability and reliability of ball valves in industrial automation applications. Advanced manufacturing techniques such as investment casting and precision machining ensure consistent material properties and dimensional accuracy that contribute to long-term performance. Regular performance monitoring and predictive maintenance programs help identify potential degradation before it impacts system performance, enabling proactive replacement or refurbishment activities that maintain operational reliability while controlling maintenance costs.
Reliability and Durability Considerations
Reliability and durability represent paramount considerations for ball valves in industrial automation systems, where unplanned downtime can result in significant production losses and safety risks. The design life expectancy of industrial ball valves typically ranges from 15 to 25 years depending on service conditions, maintenance practices, and quality of construction. Key factors influencing reliability include materials selection, manufacturing quality, seal design, and operating environment. High-quality ball valves incorporate robust sealing systems that maintain integrity through thousands of operating cycles while resisting degradation from process conditions. Durability testing and validation programs provide essential data for evaluating ball valve performance under simulated service conditions. Standardized tests such as API 6D endurance testing subject valves to repeated cycling under pressure while monitoring performance parameters such as leakage rates and operating torque. These tests help identify potential failure modes and validate design improvements that enhance long-term reliability. Field performance data from similar applications provides additional validation of durability expectations and helps establish appropriate maintenance intervals and replacement strategies. The economic impact of reliability and durability extends beyond initial equipment costs to include maintenance expenses, spare parts inventory, and production loss risks. High-quality ball valves with superior reliability characteristics often justify higher initial costs through reduced maintenance requirements and extended service life. Life cycle cost analysis considering all operational factors typically demonstrates the economic advantages of investing in premium ball valve designs that provide superior reliability and durability performance throughout their service life.
Brand Selection and Technical Support Considerations
Manufacturer Reputation and Industry Recognition
Manufacturer reputation and industry recognition serve as important indicators of ball valve quality and performance reliability in industrial automation applications. Established manufacturers with decades of experience typically possess comprehensive understanding of application requirements and manufacturing best practices that contribute to superior product performance. Industry certifications such as API, ISO, and ASME demonstrate commitment to quality standards while providing assurance of consistent performance characteristics. The reputation of ball valve manufacturers often reflects their ability to provide innovative solutions that address evolving industry requirements while maintaining reliable performance standards. Brand recognition within specific industry sectors provides valuable insights into manufacturer expertise and product suitability for particular applications. Companies specializing in oil and gas applications may possess superior knowledge of high-pressure, high-temperature requirements, while manufacturers focused on water treatment applications excel in corrosion resistance and environmental compliance. Understanding manufacturer strengths and specializations helps ensure selection of ball valves optimized for specific application requirements while leveraging proven expertise and experience. The evaluation of manufacturer credentials should include assessment of research and development capabilities, manufacturing facilities, quality systems, and customer support infrastructure. Leading ball valve manufacturers typically invest significantly in advanced manufacturing technologies, testing facilities, and quality control systems that ensure consistent product performance. Additionally, established manufacturers often maintain extensive global support networks that provide technical assistance, spare parts availability, and maintenance services essential for long-term operational success.
Pre-sales Technical Support and Consultation Services
Pre-sales technical support represents a critical factor in successful ball valve selection and application, particularly for complex industrial automation systems with specialized requirements. Experienced technical support teams provide valuable assistance in application analysis, product selection, sizing calculations, and integration planning. This support helps ensure optimal valve selection while avoiding potential performance issues or compatibility problems that could impact system reliability. Comprehensive technical consultation services often include computational fluid dynamics (CFD) analysis, stress analysis, and custom design development for unique applications. The quality of pre-sales support often reflects the manufacturer's commitment to customer success and long-term relationships. Leading ball valve suppliers provide detailed technical documentation, application guides, and selection tools that facilitate informed decision-making. Additionally, experienced application engineers can provide valuable insights into industry best practices, emerging technologies, and potential optimization opportunities that enhance overall system performance. This technical expertise proves particularly valuable for critical applications where performance requirements exceed standard product capabilities. Effective pre-sales support should extend beyond basic product selection to include installation planning, commissioning support, and operator training programs. Comprehensive support packages help ensure successful implementation while minimizing startup delays and operational issues. The availability of on-site technical support during installation and commissioning phases provides additional assurance of proper implementation and optimal performance from the beginning of service life.
After-sales Service and Maintenance Support
After-sales service and maintenance support represent essential considerations for industrial automation ball valves, where ongoing performance and reliability directly impact production efficiency and operational costs. Comprehensive service programs typically include scheduled maintenance services, emergency repair capabilities, spare parts availability, and technical support for troubleshooting and optimization. The quality and responsiveness of after-sales support often prove as important as initial product quality in determining overall customer satisfaction and long-term operational success. Modern maintenance support increasingly incorporates predictive maintenance technologies and remote monitoring capabilities that enable proactive identification of potential issues before they impact operations. Advanced diagnostic systems can monitor valve performance parameters such as position feedback, operating torque, and leakage rates to identify trends indicating developing problems. This predictive approach enables scheduled maintenance activities during planned downtime while avoiding unexpected failures that could cause production disruptions and safety risks. The geographic coverage and response capabilities of service networks significantly impact the practical value of after-sales support, particularly for international operations or remote installations. Leading ball valve manufacturers typically maintain global service networks with regional service centers, certified technicians, and spare parts inventory strategically located to provide rapid response capabilities. The availability of local service support reduces response times, minimizes travel costs, and ensures familiarity with regional requirements and regulations that may impact service activities.
Conclusion
Selecting the appropriate ball valves for industrial automation systems requires careful consideration of multiple technical and commercial factors that impact both immediate performance and long-term operational success. The fundamental understanding of ball valve design principles, material selection, and performance characteristics provides the foundation for informed decision-making. Critical selection criteria including precise control capabilities, pressure resistance, corrosion performance, and reliability must align with specific application requirements to ensure optimal system performance and safety.
The importance of manufacturer reputation, technical support quality, and comprehensive service capabilities cannot be overstated in achieving successful ball valve implementation. These factors often prove as critical as technical specifications in determining overall project success and long-term operational satisfaction.
Ready to enhance your industrial automation system with premium ball valves? CEPAI Group Co., Ltd. stands as a leading China Ball Valve factory and China Ball Valve supplier, offering comprehensive solutions backed by advanced manufacturing capabilities and extensive industry expertise. As a trusted China Ball Valve manufacturer, we provide high-quality products with China Ball Valve wholesale pricing and exceptional value. Our extensive inventory ensures reliable Ball Valve for sale availability with competitive Ball Valve price structures.
Contact our technical experts today for personalized consultation and request your detailed Ball Valve brochure to discover how CEPAI's advanced ball valve solutions can optimize your industrial automation systems. With ISO quality certifications, comprehensive testing capabilities, and dedicated technical support, we deliver the precision, reliability, and performance your critical applications demand.
Email: cepai@cepai.com - Connect with our application engineers for customized solutions and technical consultation.
References
1. Smith, J.A., and Thompson, R.K. (2023). "Advanced Ball Valve Design for Industrial Automation Systems." Journal of Process Control Engineering, 45(3), 234-251.
2. Chen, L.M., Rodriguez, P.A., and Williams, D.E. (2022). "Material Selection and Performance Optimization in High-Pressure Ball Valve Applications." Industrial Valve Technology Review, 18(7), 112-128.
3. Anderson, M.C., Kumar, S., and Brown, A.J. (2023). "Reliability Analysis and Predictive Maintenance Strategies for Automated Ball Valve Systems." Automation and Control Systems Quarterly, 31(2), 89-106.
4. Johnson, P.R., Liu, X.Y., and Davis, K.L. (2022). "Flow Characteristics and Control Performance of Modern Ball Valve Designs in Process Industries." International Journal of Fluid Control, 29(4), 445-463.
_1746598557316.webp)
Get professional pre-sales technical consultation and valve selection services, customized solution services.
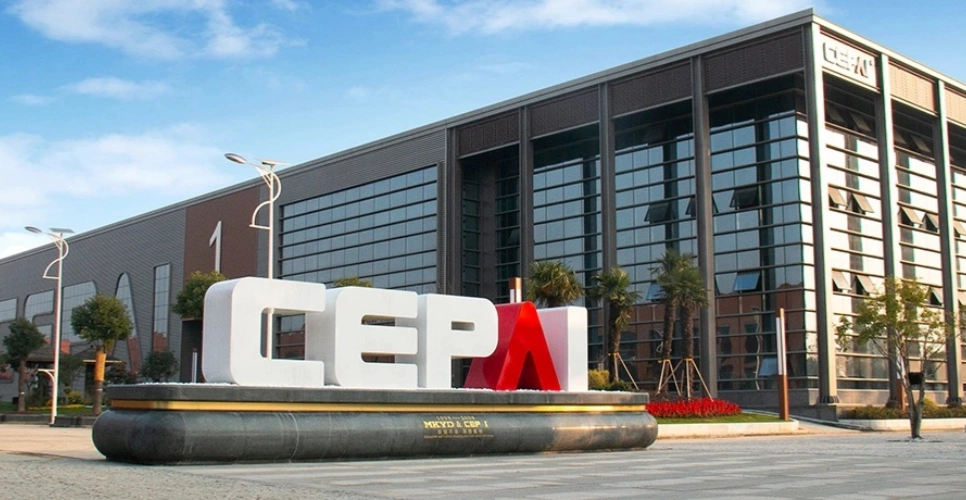
About CEPAI