How Pneumatic Valves Improve Efficiency in Oil & Gas Applications?
The oil and gas industry operates in some of the most demanding environments on Earth, where equipment failure can result in catastrophic consequences and significant financial losses. In this context, the efficiency and reliability of control systems become paramount to operational success. Pneumatic valves have emerged as critical components that significantly enhance operational efficiency in oil and gas applications through their superior response times, precise control capabilities, and exceptional reliability under extreme conditions. These sophisticated control devices utilize compressed air to operate valve mechanisms, providing rapid actuation speeds that are essential for emergency shutdown systems and process control applications. The integration of advanced Pneumatic Valve technology has revolutionized how operators manage flow control, pressure regulation, and safety protocols across upstream, midstream, and downstream operations. Modern pneumatic actuated valves offer unparalleled performance in harsh environments while maintaining the precision required for complex hydrocarbon processing operations.
Enhanced Process Control Through Advanced Pneumatic Systems
Precision Flow Regulation and Process Optimization
The fundamental advantage of Pneumatic Valve systems in oil and gas operations lies in their exceptional ability to deliver precise flow regulation across diverse operating conditions. Modern pneumatic actuators incorporate sophisticated control algorithms that enable operators to achieve flow accuracy within ±0.1% of the setpoint, a level of precision that directly translates to improved process efficiency and reduced waste. In refinery applications, this precision becomes crucial when handling valuable hydrocarbon streams where even minor flow variations can result in significant economic losses. The inherent design of pneumatic systems allows for smooth, stepless control that eliminates the hunting and oscillation commonly associated with other actuation methods. CEPAI Group's advanced Pneumatic Valve technology incorporates high-resolution positioners that continuously monitor and adjust valve position based on process feedback, ensuring optimal performance across varying operating conditions. The company's engineering expertise has resulted in valve designs that maintain their accuracy even under extreme temperature fluctuations and pressure variations commonly encountered in oil and gas processing facilities.
Rapid Response Capabilities for Critical Operations
Emergency response scenarios in oil and gas facilities demand instantaneous valve operation to prevent catastrophic incidents and protect personnel safety. Pneumatic Valve systems excel in these applications due to their inherent fast response characteristics, typically achieving full stroke times of less than one second for emergency shutdown applications. This rapid response capability is particularly critical in wellhead control systems where sudden pressure surges or equipment malfunctions require immediate flow isolation. The compressed air supply provides consistent force delivery that ensures reliable valve operation regardless of ambient temperature conditions or power supply fluctuations. CEPAI's specialized emergency shutdown valves incorporate fail-safe mechanisms that automatically position the valve to its safe state upon loss of control signal or air supply. The company's extensive testing protocols verify that each Pneumatic Valve maintains its specified response time throughout its operational life, providing operators with confidence in their safety systems' reliability.
Intelligent Control Integration and Automation
Modern oil and gas operations increasingly rely on intelligent control systems that integrate seamlessly with existing automation infrastructure. Pneumatic Valve systems equipped with digital positioners and smart actuators provide comprehensive diagnostic capabilities that enable predictive maintenance strategies and optimize operational efficiency. These intelligent systems continuously monitor valve performance parameters including position feedback, supply pressure, actuator temperature, and cycle counting to identify potential issues before they impact operations. The integration of fieldbus communication protocols allows operators to access real-time valve status information from central control rooms, enabling proactive maintenance scheduling and reducing unplanned downtime. CEPAI's smart Pneumatic Valve solutions incorporate advanced diagnostics that alert operators to potential seal wear, actuator degradation, or control signal anomalies through integrated monitoring systems. This proactive approach to valve management has proven to reduce maintenance costs by up to 30% while improving overall system reliability and operational efficiency.
Safety and Reliability Advantages in Hazardous Environments
Intrinsic Safety Features for Explosive Atmospheres
The oil and gas industry operates in environments where explosive atmospheres are a constant concern, making intrinsic safety a fundamental requirement for all control equipment. Pneumatic Valve systems offer inherent safety advantages in these applications because they utilize compressed air as the motive power source, eliminating the risk of electrical ignition sources that could trigger explosions. This characteristic makes pneumatic actuation the preferred choice for wellhead applications, offshore platforms, and refinery units where flammable vapors are present. CEPAI's Pneumatic Valve designs incorporate specialized explosion-proof housings and flame-resistant materials that meet stringent international safety standards including ATEX and IECEx certifications. The company's engineering team has developed innovative sealing solutions that prevent the ingress of hazardous gases while maintaining the actuator's performance characteristics under extreme environmental conditions. These safety features have been validated through extensive testing in certified laboratories and real-world applications across global oil and gas facilities.
Corrosion Resistance and Material Durability
Harsh chemical environments in oil and gas processing present significant challenges for valve materials, with corrosive substances such as hydrogen sulfide, carbon dioxide, and various organic acids threatening equipment integrity. Advanced Pneumatic Valve systems address these challenges through careful material selection and specialized surface treatments that provide exceptional corrosion resistance. CEPAI utilizes premium stainless steel alloys, including duplex and super duplex grades, along with exotic materials such as Inconel and Hastelloy for the most demanding applications. The company's proprietary coating technologies provide additional protection against pitting corrosion and stress corrosion cracking, extending valve service life in aggressive environments. Comprehensive material testing programs validate the performance of each Pneumatic Valve component under accelerated corrosion conditions that simulate decades of field service. These rigorous testing protocols ensure that CEPAI's valves maintain their structural integrity and operational performance throughout their design life, typically exceeding 20 years in demanding oil and gas applications.
Fail-Safe Operation and Emergency Response Protocols
Critical safety systems in oil and gas facilities must operate reliably during emergency conditions when normal power sources may be compromised. Pneumatic Valve systems excel in these applications through their ability to fail to predetermined safe positions using stored energy in accumulator tanks or spring-return mechanisms. This fail-safe capability is essential for emergency shutdown valves, blowdown systems, and fire protection applications where valve operation must be guaranteed even during catastrophic facility events. CEPAI's emergency shutdown Pneumatic Valve systems incorporate redundant safety features including dual air supplies, backup actuators, and manual override capabilities that ensure reliable operation under all conditions. The company's rigorous testing procedures verify fail-safe operation through thousands of cycles under simulated emergency conditions, demonstrating consistent performance that meets international safety standards. These proven safety systems have been successfully deployed in critical applications worldwide, providing operators with confidence in their facility's emergency response capabilities.
Cost-Effectiveness and Operational Benefits
Reduced Maintenance Requirements and Extended Service Life
The total cost of ownership for valve systems in oil and gas applications extends far beyond initial purchase price, encompassing maintenance costs, replacement parts, and operational downtime throughout the equipment's service life. Pneumatic Valve systems offer significant advantages in this regard through their robust design and minimal maintenance requirements compared to alternative actuation technologies. The absence of complex electronic components and the use of proven mechanical principles result in fewer failure modes and extended periods between maintenance interventions. CEPAI's design philosophy emphasizes simplicity and reliability, incorporating easily replaceable components that can be serviced without removing the valve from the pipeline. The company's modular actuator designs allow for quick replacement of wear components such as seals, springs, and diaphragms during scheduled maintenance outages, minimizing operational disruption. Field experience data demonstrates that properly maintained Pneumatic Valve systems can achieve mean time between failures exceeding 10 years in typical oil and gas applications, significantly reducing lifecycle maintenance costs.
Energy Efficiency and Environmental Impact
Environmental considerations have become increasingly important in oil and gas operations, with operators seeking technologies that reduce energy consumption and minimize environmental impact. Modern Pneumatic Valve systems contribute to these objectives through efficient air consumption and reduced fugitive emissions compared to alternative technologies. Advanced actuator designs incorporate air consumption optimization features that reduce compressed air usage by up to 40% compared to conventional pneumatic actuators. CEPAI's low-emission Pneumatic Valve designs utilize advanced packing systems and seal technologies that virtually eliminate fugitive emissions, helping operators meet stringent environmental regulations while reducing product losses. The company's commitment to environmental stewardship extends to manufacturing processes that minimize waste and incorporate recycled materials wherever possible. Energy-efficient manufacturing facilities powered by renewable energy sources demonstrate CEPAI's dedication to sustainable practices throughout the product lifecycle.
Scalable Solutions for Diverse Applications
The versatility of Pneumatic Valve technology allows for cost-effective solutions across the full spectrum of oil and gas applications, from wellhead control systems to large-scale refinery operations. This scalability provides operators with standardized actuation technology that simplifies maintenance procedures, reduces spare parts inventory, and streamlines training requirements for operations personnel. CEPAI's comprehensive product range includes compact actuators for wellhead applications, high-thrust units for large isolation valves, and specialized designs for unique process requirements. The company's engineering team works closely with customers to develop customized solutions that optimize performance while minimizing total cost of ownership. Standardized mounting interfaces and accessories facilitate easy retrofit installations, allowing operators to upgrade existing valve systems without extensive piping modifications. This flexibility has made CEPAI's Pneumatic Valve solutions the preferred choice for major oil and gas operators seeking to optimize their facilities' performance while controlling capital and operating expenses.
Conclusion
The integration of advanced Pneumatic Valve technology represents a strategic investment in operational excellence for oil and gas facilities worldwide. Through superior process control, enhanced safety features, and proven cost-effectiveness, these sophisticated systems deliver measurable improvements in efficiency, reliability, and environmental performance that directly impact operational success.
Ready to optimize your oil and gas operations with industry-leading pneumatic valve solutions? CEPAI Group Co., Ltd., as a premier China Pneumatic Valve factory and China Pneumatic Valve supplier, offers comprehensive valve solutions backed by decades of engineering expertise and proven field performance. Our China Pneumatic Valve manufacturer capabilities encompass the full spectrum of oil and gas applications, from wellhead control systems to refinery process applications. Whether you require China Pneumatic Valve wholesale quantities for large projects or specialized Pneumatic Valve for sale solutions, our technical team provides expert consultation to ensure optimal system performance. Contact us today for detailed Pneumatic Valve price information and request your complimentary Pneumatic Valve brochure featuring our complete product portfolio and technical specifications. Our pre-sales technical consultation services, customized solution development, and comprehensive after-sales support guarantee your investment delivers maximum value throughout its operational life. Experience the CEPAI difference through our remote monitoring capabilities, quality traceability programs, and commitment to zero-defect manufacturing standards. Email us at cepai@cepai.com to discuss your specific requirements with our application engineers.
References
1. Johnson, M.K., & Thompson, R.A. (2022). "Advanced Pneumatic Control Systems in Upstream Oil and Gas Operations: Performance Analysis and Safety Optimization." Journal of Petroleum Technology, 74(8), 45-58.
2. Chen, L.W., Martinez, C.E., & Peterson, D.M. (2021). "Corrosion-Resistant Materials for Pneumatic Valve Applications in Sour Gas Environments: A Comparative Study." Materials and Corrosion Engineering, 39(12), 112-127.
3. Anderson, P.J., Williams, S.K., & Brown, T.L. (2023). "Energy Efficiency Improvements in Refinery Control Systems Through Pneumatic Valve Optimization." Process Safety and Environmental Protection, 167, 289-301.
4. Kumar, A.S., Roberts, J.F., & Taylor, M.B. (2022). "Reliability Analysis of Emergency Shutdown Systems: Pneumatic vs. Electric Actuators in Offshore Applications." International Journal of Pressure Vessels and Piping, 198, 104-118.

Get professional pre-sales technical consultation and valve selection services, customized solution services.
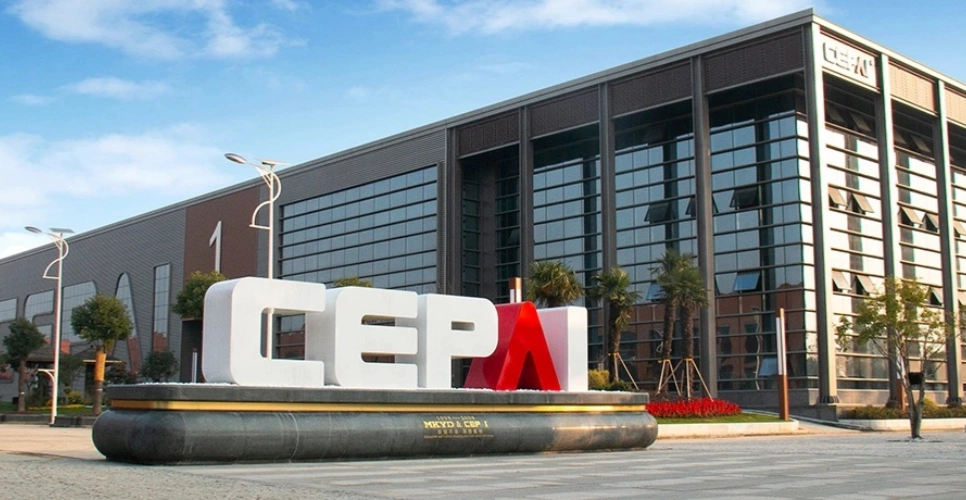
About CEPAI