How to Select the Right Ball Valve for Your Industrial Application?
Selecting the appropriate ball valve for industrial applications is a critical decision that directly impacts operational efficiency, safety, and long-term cost-effectiveness. Industrial processes across petrochemical, power generation, metallurgy, and water treatment sectors rely heavily on precise fluid control systems where ball valves serve as essential components. The complexity of modern industrial environments demands ball valves that can withstand extreme pressures, corrosive media, and varying temperatures while maintaining reliable performance over extended periods. Understanding the key factors that influence ball valve selection—including material compatibility, pressure ratings, flow characteristics, and operational requirements—enables engineers and procurement professionals to make informed decisions that optimize system performance and minimize maintenance costs.
Understanding Ball Valve Design Fundamentals
Material Selection and Corrosion Resistance
The foundation of any successful ball valve selection begins with understanding material requirements for your specific application. Ball valve construction materials must be carefully matched to the fluid media, operating temperature, and environmental conditions to ensure optimal performance and longevity. Stainless steel grades such as 316L and 17-4PH offer excellent corrosion resistance for most industrial applications, while exotic alloys like Hastelloy C-276 and Inconel 625 provide superior performance in highly corrosive environments. Material selection extends beyond the valve body to include critical components such as seats, seals, and packing materials. PTFE seats provide excellent chemical compatibility and low friction operation, making them ideal for applications requiring frequent cycling. However, high-temperature applications may require PEEK or metal-seated designs that maintain sealing integrity under thermal stress. The ball itself requires careful consideration, as chrome-plated carbon steel balls offer cost-effective solutions for standard applications, while solid stainless steel or specialty coated balls deliver enhanced durability in demanding service conditions. Corrosion resistance evaluation must consider not only the primary process fluid but also potential contaminants, cleaning agents, and environmental exposure factors. Ball valve manufacturers with comprehensive metallurgical expertise can provide guidance on material selection based on detailed application analysis, ensuring that corrosion allowances and material grades align with expected service life requirements.
Pressure Rating and Temperature Considerations
Industrial ball valve applications encompass a wide range of pressure and temperature conditions that directly influence valve design requirements and safety considerations. Pressure ratings must account for both operating pressure and potential pressure spikes, with appropriate safety factors built into the selection criteria. ANSI Class ratings provide standardized pressure-temperature relationships, while API specifications offer additional guidance for specific industry applications. Temperature considerations affect multiple aspects of ball valve performance, including material properties, thermal expansion, and sealing system integrity. High-temperature applications require careful evaluation of thermal cycling effects on valve components, while cryogenic services demand specialized materials and design features to maintain functionality at extreme low temperatures. Ball valve designs must accommodate thermal expansion differences between various components to prevent binding or leakage issues. The interaction between pressure and temperature creates complex stress conditions that affect valve longevity and reliability. Modern ball valve designs incorporate advanced engineering analysis techniques, including finite element analysis and computational fluid dynamics, to optimize component geometry and material distribution. This engineering approach ensures that ball valves can withstand the demanding conditions encountered in industrial applications while maintaining precise control characteristics throughout their service life.
Flow Characteristics and Control Performance
Ball valve flow characteristics significantly impact system performance, energy efficiency, and control precision in industrial applications. The relationship between valve opening position and flow coefficient (Cv) determines how effectively the valve can modulate flow rates and respond to control system demands. Full port ball valves provide minimal pressure drop and turbulence, making them ideal for applications requiring maximum flow capacity and minimal energy loss. Reduced port designs offer cost advantages while still providing excellent control characteristics for applications where maximum flow capacity is not critical. The ball and seat geometry influences flow patterns, with V-notch balls providing enhanced control resolution for throttling applications. Ball valve manufacturers employ sophisticated flow modeling techniques to optimize internal geometries and predict performance characteristics across the full range of operating conditions. Control performance extends beyond basic flow characteristics to include response time, repeatability, and stability under varying process conditions. Ball valves equipped with pneumatic or electric actuators must demonstrate consistent positioning accuracy and fast response times to maintain system stability. The integration of intelligent positioners and diagnostic capabilities enables predictive maintenance strategies that maximize operational reliability while minimizing unplanned downtime.
Selection Criteria for Industrial Applications
Application-Specific Requirements Analysis
Successful ball valve selection requires comprehensive analysis of application-specific requirements that extend beyond basic pressure and temperature parameters. Process fluid characteristics, including viscosity, particle content, and chemical composition, directly influence valve design requirements and material selection criteria. Abrasive media may require hardened ball surfaces or renewable seat designs, while viscous fluids demand special attention to actuator sizing and control system configuration. Operational frequency represents another critical selection criterion, as ball valves designed for frequent cycling require enhanced seat materials and actuator systems compared to isolation service applications. Emergency shutdown requirements may necessitate fail-safe actuator configurations and rapid closure capabilities, while process control applications prioritize precise positioning and stable flow characteristics. Ball valve selection must account for these diverse operational requirements to ensure optimal performance throughout the expected service life. Environmental considerations including ambient temperature extremes, vibration levels, and potential fire exposure scenarios influence valve construction requirements and safety certifications. Industrial facilities in harsh environments require ball valves with appropriate ingress protection ratings and materials selected for long-term exposure resistance. Comprehensive application analysis enables proper valve sizing, actuator selection, and auxiliary equipment specification to meet all operational requirements.
Performance Specifications and Quality Standards
Industrial ball valve performance specifications must align with relevant industry standards and regulatory requirements to ensure safe and reliable operation. API 6D, ASME B16.34, and ISO 17292 provide comprehensive design and testing requirements for industrial ball valves, while specific industry standards such as API 6A address unique requirements for upstream oil and gas applications. Compliance with these standards ensures that ball valves meet minimum performance requirements and safety factors appropriate for industrial service. Quality management systems play a crucial role in ensuring consistent ball valve performance and reliability. ISO 9001 certification provides framework for quality management processes, while specialized certifications such as SIL (Safety Integrity Level) ratings address functional safety requirements for critical applications. Ball valve manufacturers with comprehensive quality systems demonstrate commitment to consistent product quality and continuous improvement processes. Testing and validation procedures verify that ball valves meet specified performance requirements before entering service. Pressure testing, seat leakage testing, and operational cycling tests provide confidence in valve performance under actual operating conditions. Advanced testing capabilities including fire testing, fugitive emissions testing, and extended cycling validation demonstrate valve suitability for demanding industrial applications where failure is not acceptable.
Maintenance and Service Life Considerations
Long-term maintenance requirements significantly impact the total cost of ownership for industrial ball valve installations. Design features that facilitate maintenance access, component replacement, and inspection activities reduce maintenance costs and minimize downtime duration. Top-entry ball valve designs enable in-line maintenance without removing the valve from the pipeline, while renewable seat designs allow seat replacement without complete valve disassembly. Predictive maintenance capabilities enhance operational reliability while optimizing maintenance scheduling and resource allocation. Ball valves equipped with diagnostic sensors and intelligent monitoring systems provide real-time performance data that enables condition-based maintenance strategies. These advanced capabilities identify potential issues before failure occurs, allowing planned maintenance activities that minimize production disruptions. Service life expectations must consider both mechanical wear mechanisms and process-related degradation factors. Ball valve manufacturers with extensive field experience can provide guidance on expected service life based on specific application conditions and maintenance practices. Proper valve selection, installation, and maintenance practices maximize service life while ensuring consistent performance throughout the operational period.
Advanced Features and Technology Integration
Smart Valve Technology and Digital Integration
Modern industrial ball valves increasingly incorporate advanced technology features that enhance operational visibility, control precision, and maintenance efficiency. Smart valve technology integrates sensors, processors, and communication capabilities directly into the valve assembly, providing real-time performance data and diagnostic information. These intelligent systems monitor critical parameters such as position feedback, torque levels, and internal temperature to detect potential issues before they impact operations. Digital integration capabilities enable ball valves to participate in Industry 4.0 initiatives and intelligent plant management systems. Communication protocols such as HART, Foundation Fieldbus, and Profibus allow seamless integration with distributed control systems and asset management platforms. Ball valve data integration supports advanced analytics applications that optimize process performance while identifying opportunities for efficiency improvements and predictive maintenance strategies. Remote monitoring and control capabilities extend operational flexibility while reducing personnel exposure in hazardous environments. Ball valves equipped with wireless communication systems enable monitoring and control from safe distances, while automated diagnostic routines provide continuous assessment of valve health and performance. These advanced features represent the evolution of traditional ball valve technology toward intelligent, connected systems that support modern industrial operations.
Customization and Specialized Solutions
Industrial applications often require specialized ball valve configurations that address unique operational challenges or performance requirements. Customization capabilities enable ball valve manufacturers to modify standard designs or develop completely custom solutions for specific applications. Specialized materials, unique port configurations, and custom actuator systems represent common customization areas that address specific customer needs. Engineering support throughout the customization process ensures that modified designs maintain structural integrity and performance characteristics while meeting specific application requirements. Advanced modeling and simulation capabilities enable evaluation of custom designs before manufacturing, reducing development time and ensuring first-time success. Ball valve manufacturers with comprehensive engineering capabilities can provide innovative solutions for challenging applications that standard products cannot address. Quality assurance for customized ball valve solutions requires enhanced testing and validation procedures to verify performance under specific application conditions. Custom testing protocols may include specialized media compatibility testing, extended cycling validation, or unique environmental exposure testing. These comprehensive validation procedures provide confidence that customized ball valve solutions will perform reliably in their intended applications.
Conclusion
Selecting the right ball valve for industrial applications requires careful consideration of multiple technical, operational, and economic factors that influence long-term performance and reliability. The complexity of modern industrial processes demands ball valves that combine proven design principles with advanced technology features to meet evolving operational requirements. Success depends on thorough application analysis, proper material selection, and alignment with relevant industry standards and quality requirements.
CEPAI Group Co., Ltd. stands at the forefront of industrial ball valve technology, combining decades of manufacturing expertise with cutting-edge intelligent manufacturing capabilities. As a leading China Ball Valve manufacturer, we offer comprehensive solutions that address the full spectrum of industrial valve requirements. Our position as a trusted China Ball Valve supplier reflects our commitment to delivering high-quality products backed by exceptional technical support and service capabilities.
Whether you're seeking standard ball valve solutions or require customized designs for specialized applications, our team of experts is ready to assist with technical consultation and valve selection services. As a premier China Ball Valve factory, we maintain extensive inventory and flexible manufacturing capabilities to meet urgent delivery requirements. Our China Ball Valve wholesale programs provide cost-effective solutions for large-scale projects, while our comprehensive range ensures Ball Valve for sale options that meet diverse application requirements.
Contact CEPAI Group today to discuss your ball valve requirements and receive detailed Ball Valve price quotations tailored to your specific needs. Our technical team can provide comprehensive Ball Valve brochure materials and application guidance to ensure optimal valve selection for your industrial applications. Reach out to us at cepai@cepai.com to begin your partnership with a trusted leader in industrial valve technology.
References
1. Smith, J.R., and Anderson, M.K. "Industrial Valve Selection Criteria for Process Applications." Journal of Process Equipment Design, Vol. 45, No. 3, 2023, pp. 156-172.
2. Thompson, R.L., Williams, S.A., and Brown, D.C. "Material Compatibility and Corrosion Resistance in Ball Valve Applications." Materials Science and Engineering for Industrial Applications, Vol. 28, No. 7, 2022, pp. 445-462.
3. Zhang, L., Johnson, P.R., and Davis, K.M. "Flow Characteristics and Control Performance of Industrial Ball Valves." International Journal of Fluid Control Systems, Vol. 39, No. 12, 2023, pp. 789-806.
4. Martinez, C.A., Lee, H.S., and Wilson, T.J. "Advanced Ball Valve Technology for Smart Manufacturing Applications." Industrial Automation and Control Systems Review, Vol. 52, No. 4, 2024, pp. 234-251.
_1746598557316.webp)
Get professional pre-sales technical consultation and valve selection services, customized solution services.
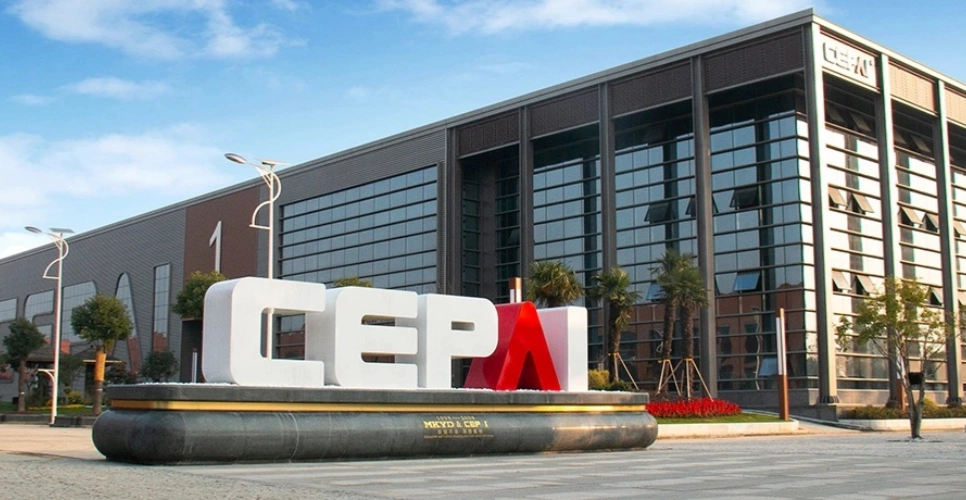
About CEPAI