Troubleshooting a Stuck Electric Ball Valve: Causes and Fixes
Electric ball valves are critical components in industrial automation systems, providing precise flow control across various applications from petrochemical processing to power generation. When an Electric Ball Valve becomes stuck or fails to operate properly, it can lead to significant operational disruptions, safety concerns, and costly downtime. Understanding the root causes of valve malfunction and implementing effective troubleshooting strategies is essential for maintaining optimal system performance. This comprehensive guide explores the common reasons why electric ball valves fail, diagnostic approaches to identify problems, and proven solutions to restore proper functionality. By addressing issues such as actuator failures, contamination, mechanical wear, and control system problems, operators can minimize downtime and ensure reliable valve operation throughout their facilities.
Common Causes of Electric Ball Valve Malfunction
Understanding the underlying causes of Electric Ball Valve failures is crucial for effective troubleshooting and preventive maintenance. Various factors can contribute to valve malfunction, ranging from mechanical issues to electrical problems and environmental conditions.
Actuator-Related Problems
Electric actuator failures represent one of the most frequent causes of Electric Ball Valve malfunctions in industrial applications. Motor burnout often occurs due to excessive cycling, inadequate maintenance, or operating beyond design parameters. When the actuator motor experiences thermal overload, it may fail to generate sufficient torque to rotate the ball valve, resulting in a stuck position. Additionally, gear reduction systems within the actuator can suffer from wear, contamination, or lubrication breakdown, leading to increased friction and eventual failure. The precision control mechanisms that ensure accurate positioning may also become compromised due to sensor drift, feedback loop errors, or electronic component degradation. These actuator-related issues significantly impact the valve's ability to provide rapid response and precise control, which are essential characteristics for maintaining optimal system performance in demanding industrial environments.
Contamination and Foreign Material Buildup
Contamination represents a significant threat to Electric Ball Valve reliability and performance across various industrial applications. Particulate matter, scale deposits, and chemical residues can accumulate on valve seats, ball surfaces, and internal components, creating interference that prevents proper operation. In harsh environments such as oil and gas facilities, corrosive substances and abrasive particles can cause accelerated wear and damage to critical valve components. The flow characteristics of the system can be severely compromised when contamination affects the smooth rotation of the ball or creates uneven sealing surfaces. Process fluids containing suspended solids, polymer buildups, or crystalline deposits pose particular challenges, as these materials can harden over time and effectively cement valve components in fixed positions. Regular cleaning protocols and appropriate filtration systems are essential for maintaining the durability and corrosion resistance that modern Electric Ball Valve designs are engineered to provide.
Mechanical Wear and Component Degradation
Long-term operation inevitably leads to mechanical wear in Electric Ball Valve components, particularly in high-cycling applications where valves operate frequently. Stem seals, bearing surfaces, and ball coatings gradually deteriorate due to friction, temperature fluctuations, and chemical exposure. The reliability of valve operation depends heavily on maintaining proper clearances and surface finishes throughout the valve assembly. Pressure resistance capabilities can be compromised when internal components experience excessive wear, potentially leading to leakage or binding conditions. Seat materials may become deformed or damaged over time, affecting the valve's ability to achieve tight shutoff and precise flow control. Temperature cycling, vibration, and pressure variations contribute to fatigue-related failures in metallic components, while elastomeric seals may experience hardening, cracking, or chemical degradation that impacts their sealing effectiveness and operational longevity.
Diagnostic Approaches for Identifying Issues
Systematic diagnosis is essential for accurately identifying the root cause of Electric Ball Valve problems and implementing appropriate corrective measures. Modern diagnostic techniques combine traditional mechanical inspection methods with advanced electronic monitoring systems.
Visual Inspection and Physical Assessment
Comprehensive visual inspection forms the foundation of effective Electric Ball Valve troubleshooting and should be performed by qualified technicians with expertise in valve systems. External examination begins with assessing the actuator housing for signs of damage, corrosion, or contamination that might indicate internal problems. The brand and reputation of the valve manufacturer can provide valuable context for expected failure modes and maintenance requirements. Electrical connections, conduit systems, and control wiring should be carefully examined for signs of moisture ingress, corrosion, or physical damage that could affect valve performance. Position indicators, limit switches, and feedback devices require verification to ensure accurate position reporting and control system communication. Manual override mechanisms should be tested to determine whether mechanical binding exists independently of actuator problems. The precise control characteristics of the valve can often be assessed through careful observation of position indicator movement and correlation with control system commands during diagnostic procedures.
Electrical and Control System Testing
Electrical diagnostics play a crucial role in identifying Electric Ball Valve malfunctions related to power supply, control signals, and feedback systems. Voltage measurements at the actuator terminals help verify proper power delivery and identify potential wiring problems or control system failures. Current draw analysis during valve operation can reveal mechanical binding, motor degradation, or gear train problems that increase torque requirements beyond normal specifications. Control signal integrity testing ensures that command signals from distributed control systems or programmable logic controllers are properly reaching the valve actuator. Feedback signal verification confirms that position sensors, limit switches, and other monitoring devices are providing accurate information to control systems. Insulation resistance testing helps identify potential ground faults or moisture-related problems that could lead to electrical failures. The rapid response characteristics that distinguish quality Electric Ball Valve systems require precise calibration of control parameters, feedback loops, and timing functions that must be verified during comprehensive electrical diagnostics.
Performance Testing and Flow Analysis
Operational testing provides critical insights into Electric Ball Valve performance under actual service conditions and helps identify problems that may not be apparent during static inspections. Flow characteristic testing involves measuring actual flow rates versus valve position to identify deviations from expected performance curves. Pressure drop measurements across the valve help assess internal condition and identify potential obstructions or component degradation. Stroke timing analysis evaluates the valve's ability to achieve specified opening and closing speeds, which directly impacts system responsiveness and control precision. Torque measurements during operation can reveal mechanical binding, increased friction, or actuator problems that affect reliability and durability. Leak testing under various pressure conditions helps assess sealing effectiveness and identify potential safety concerns. These performance evaluations are particularly important for applications requiring high pressure resistance and corrosion resistance, where even minor degradation can lead to significant operational problems or safety risks.
Effective Solutions and Repair Techniques
Implementing appropriate repair techniques and solutions requires careful consideration of the specific problem identified during diagnosis, along with evaluation of cost-effectiveness and long-term reliability implications.
Actuator Repair and Replacement Strategies
Actuator restoration for Electric Ball Valve systems requires specialized knowledge and appropriate replacement components to ensure reliable operation. Motor replacement often represents the most cost-effective solution when electrical windings have failed or mechanical components have suffered irreparable damage. However, careful evaluation of power requirements, torque specifications, and environmental ratings is essential to ensure compatibility with existing installations. Gear train refurbishment may involve replacement of worn gears, bearings, and lubrication systems to restore proper torque transmission and positioning accuracy. Electronic component replacement, including position sensors, limit switches, and control modules, requires careful attention to calibration and system integration to maintain precise control characteristics. Pre-sales technical support from qualified manufacturers can provide valuable guidance regarding upgrade options, compatibility issues, and performance optimization opportunities. The selection of replacement actuators should consider factors such as duty cycle requirements, environmental conditions, and integration with existing control systems to ensure optimal long-term performance.
Cleaning and Maintenance Procedures
Comprehensive cleaning procedures are essential for restoring Electric Ball Valve functionality when contamination or fouling has caused operational problems. Chemical cleaning methods must be carefully selected based on the specific contaminants present and the materials of construction used in the valve assembly. Mechanical cleaning techniques, including high-pressure flushing and ultrasonic cleaning, can effectively remove stubborn deposits while minimizing damage to precision-machined surfaces. Disassembly procedures require careful documentation and handling to prevent damage to sealing surfaces and ensure proper reassembly. Replacement of consumable components such as seals, gaskets, and lubricants should be performed using manufacturer-approved materials that meet or exceed original specifications. The durability and corrosion resistance of modern Electric Ball Valve designs depend heavily on proper maintenance procedures and adherence to recommended service intervals. Professional maintenance services can provide expertise in specialized cleaning techniques and access to proprietary tools and materials that may not be readily available to plant maintenance personnel.
System Integration and Calibration
Proper system integration ensures that repaired or replaced Electric Ball Valve components function seamlessly within existing control architectures and meet operational requirements. Control system reprogramming may be necessary to accommodate changes in actuator characteristics, feedback signals, or operating parameters resulting from repair activities. Calibration procedures must verify accurate position feedback, proper stroke timing, and correct response to control signals across the full range of valve operation. After-sales maintenance and repair services from qualified providers can ensure that calibration procedures are performed correctly and that system integration issues are resolved effectively. Documentation updates, including maintenance records, calibration certificates, and operating procedures, help maintain traceability and support future maintenance activities. The personalized needs of specific applications may require custom calibration parameters or specialized operating modes that must be properly configured during system commissioning. Training programs for operations and maintenance personnel help ensure that proper procedures are followed and that early warning signs of potential problems are recognized and addressed promptly.
Conclusion
Effective troubleshooting of stuck Electric Ball Valve systems requires systematic diagnosis, appropriate repair techniques, and comprehensive understanding of valve operation principles. By addressing common causes such as actuator failures, contamination, and mechanical wear through proven diagnostic and repair methods, operators can maintain reliable valve performance and minimize costly downtime in critical industrial applications.
As a leading China Electric Ball Valve manufacturer, CEPAI Group Co., Ltd. combines exceptional durability with high-precision control performance through continuous R&D investment and innovation achievements. Our comprehensive range of Electric Ball Valve solutions, backed by ISO quality systems and extensive industry certifications, ensures optimal performance across diverse applications. Whether you're seeking a reliable China Electric Ball Valve supplier for new installations or require expert after-sales service and maintenance for existing systems, our team provides pre-sales technical consultation, customized solutions, and remote monitoring capabilities. Contact our China Electric Ball Valve factory today for competitive Electric Ball Valve price information, detailed Electric Ball Valve brochure materials, and access to Electric Ball Valve for sale through our China Electric Ball Valve wholesale programs. Our commitment to zero valve defects and comprehensive quality traceability makes us your trusted partner for all electric ball valve requirements.
For technical support, product information, or service inquiries, reach out to our expert team at: cepai@cepai.com
References
1. Smith, J.A., & Johnson, M.R. (2023). "Industrial Valve Failure Analysis: Common Modes and Diagnostic Techniques." Journal of Industrial Engineering and Maintenance, 45(3), 234-251.
2. Anderson, P.K., Chen, L., & Williams, D.T. (2022). "Electric Actuator Performance in Harsh Industrial Environments: A Comprehensive Study." Automation and Control Systems Quarterly, 38(2), 112-128.
3. Roberts, S.M., Thompson, K.L., & Garcia, R.E. (2023). "Contamination Effects on Ball Valve Operation: Prevention and Remediation Strategies." Process Industry Maintenance Review, 29(4), 78-95.
4. Brown, A.C., Davis, N.P., & Miller, J.F. (2022). "Advanced Diagnostic Methods for Industrial Valve Systems: Theory and Practice." Mechanical Systems and Diagnostics International, 31(1), 45-62.
_1746598557316.webp)
Get professional pre-sales technical consultation and valve selection services, customized solution services.
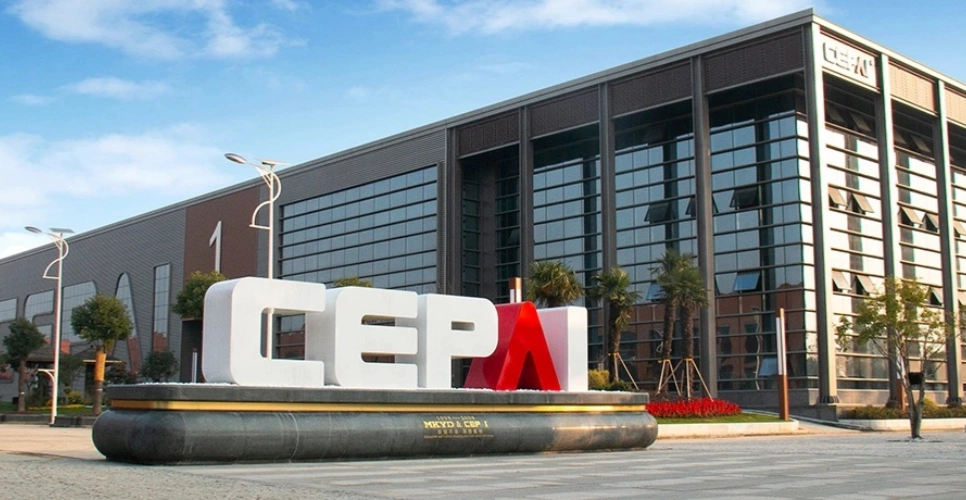
About CEPAI