O-type Ball Valve VS V-notch Ball Valve - Structure and Work Principle
In industrial fluid control applications, selecting the appropriate valve technology is crucial for achieving optimal system performance. The comparison between O-type ball valve and V-notch ball valve represents a fundamental decision that impacts flow characteristics, control precision, and operational reliability. Understanding the structural differences and working principles of these two valve designs enables engineers and procurement professionals to make informed decisions based on specific application requirements. This comprehensive analysis examines the core distinctions between O-type ball valve and V-notch configurations, focusing on their mechanical design, flow control capabilities, and practical applications in modern industrial systems.
Structural Design Analysis: O-type vs V-notch Ball Valve Configurations
Spherical Ball Construction and Port Geometry
The fundamental distinction between O-type ball valve and V-notch ball valve lies in their ball construction and port geometry. The O-type ball valve features a full spherical ball with circular ports that provide unrestricted flow when fully open. This design utilizes a complete sphere with through-holes that align with the pipeline when rotated to the open position. The circular port geometry creates a straight-through flow path that minimizes pressure drop and turbulence. The spherical construction ensures uniform stress distribution across the ball surface, contributing to enhanced durability and extended service life. The O-type ball valve design incorporates precision-machined surfaces that mate with resilient seat materials, creating a bubble-tight seal when closed. The manufacturing process requires careful attention to dimensional tolerances to ensure proper alignment between the ball ports and the valve body passages. The V-notch ball valve employs a modified spherical ball with a distinctive V-shaped notch or groove cut into the ball surface. This specialized geometry creates a variable orifice area as the ball rotates, enabling precise flow control throughout the valve's operating range. The V-notch configuration allows for gradual flow modulation, with the narrow apex of the V-notch providing fine control at low flow rates. As the valve opens further, the progressively wider V-notch area accommodates increased flow volumes. This design principle makes V-notch ball valves particularly suitable for applications requiring accurate flow regulation and throttling capabilities. The V-notch geometry can be customized with different angles and profiles to achieve specific flow characteristics tailored to particular applications.
Seat and Seal Configuration Systems
The seating arrangement in O-type ball valve systems typically employs floating or trunnion-mounted configurations, depending on pressure rating and size requirements. Floating ball designs allow the ball to move slightly downstream under system pressure, ensuring tight contact with the downstream seat. This self-energizing effect improves sealing performance as pressure increases. The seat materials commonly include PTFE, PEEK, or metal-to-metal configurations for high-temperature applications. The O-type ball valve seat design must accommodate the full circular motion of the ball while maintaining consistent sealing pressure around the entire circumference. Advanced seat designs incorporate spring-loaded or pressure-assisted mechanisms to compensate for thermal expansion and seat wear over time. V-notch ball valve seat systems face unique challenges due to the irregular ball surface geometry. The seating arrangement must accommodate the V-notch profile while maintaining effective sealing when the valve is closed. Specialized seat designs often incorporate contoured surfaces that match the V-notch geometry, ensuring proper contact and sealing performance. The seat materials must withstand the cutting action that may occur as the V-notch edge passes through the flow stream during operation. Advanced V-notch ball valve designs utilize hardened seat inserts or replaceable seat rings to address wear concerns in severe service applications.
Actuator Integration and Torque Requirements
The actuation requirements for O-type ball valve systems are generally predictable due to the uniform ball geometry and consistent flow forces. The torque required to operate an O-type ball valve typically follows a well-defined curve, with peak torque occurring during the initial opening and final closing phases. This predictable torque profile allows for straightforward actuator sizing and selection. The mounting interface between the valve stem and actuator can utilize standard configurations, including direct-mount, bracket-mount, or integral designs. The O-type ball valve stem design typically incorporates anti-blowout features and packing arrangements that accommodate the rotational movement while maintaining pressure containment. V-notch ball valve actuation presents more complex requirements due to the variable flow forces encountered throughout the operating range. The irregular ball geometry creates non-uniform pressure distribution as the V-notch interacts with the flowing medium. This results in variable torque requirements that must be considered during actuator selection. Advanced V-notch ball valve designs incorporate torque-reducing features such as balanced ball configurations or specialized stem designs to minimize actuator requirements. The control system integration for V-notch ball valves often requires more sophisticated positioning and feedback systems to achieve precise flow control objectives.
Flow Characteristics and Performance Comparison
Flow Coefficient and Pressure Drop Analysis
The flow characteristics of O-type ball valve systems are characterized by excellent Cv values and minimal pressure drop when fully open. The straight-through flow path creates virtually unrestricted flow conditions, with flow coefficients approaching those of equivalent pipe sections. The O-type ball valve design typically achieves flow coefficients ranging from 80% to 95% of the theoretical maximum for a given pipe size. This high flow efficiency makes O-type ball valves ideal for applications where minimal pressure loss is critical. The pressure recovery factor for O-type ball valve designs is typically high, indicating good downstream pressure recovery characteristics. The cavitation index for these valves is generally favorable, reducing the risk of cavitation damage in high-velocity applications. V-notch ball valve flow characteristics are specifically designed to provide controlled throttling capabilities with predictable flow curves. The V-notch geometry creates an inherent flow characteristic that can be linear, equal percentage, or customized based on the notch profile. The flow coefficient varies continuously as the valve position changes, allowing for precise flow modulation. At low openings, the narrow V-notch provides fine control resolution, while larger openings accommodate higher flow rates. The pressure drop across V-notch ball valves is typically higher than equivalent O-type ball valve configurations due to the flow restriction created by the notch geometry. However, this controlled pressure drop enables effective flow regulation and process control.
Rangeability and Control Precision
The rangeability of O-type ball valve systems is typically limited when used for flow control applications. The quick-opening characteristic of the circular port geometry provides rapid flow increase with small changes in valve position. This makes O-type ball valves less suitable for precise throttling applications but excellent for on-off service. The control resolution is limited by the rapid flow change near the fully open position. For applications requiring flow control, O-type ball valves may be equipped with specialized actuators or positioners to improve control precision. The inherent flow characteristic of O-type ball valves is generally considered quick-opening, with approximately 80% of maximum flow achieved at 50% valve opening. V-notch ball valve systems excel in rangeability and control precision applications. The typical rangeability for V-notch ball valves ranges from 50:1 to 100:1, significantly exceeding the capabilities of O-type ball valve designs. The V-notch geometry provides excellent control resolution throughout the operating range, with particularly fine control at low flow rates. The linear or equal percentage flow characteristics of V-notch ball valves make them suitable for automatic control system integration. The control precision is enhanced by the gradual flow change as the valve position varies, allowing for stable process control without hunting or oscillation.
Cavitation and Erosion Resistance
The cavitation resistance of O-type ball valve designs is generally good due to the streamlined flow path and minimal flow restrictions. The straight-through configuration reduces velocity increases and pressure drops that can lead to cavitation. When cavitation does occur, the damage is typically localized to the downstream areas of the valve body. The erosion resistance of O-type ball valves is enhanced by the absence of sharp edges or restrictions in the flow path. The spherical ball surface presents smooth contours that minimize erosive wear in clean service applications. However, in applications with abrasive media, the seat areas may experience wear due to particle impingement during valve operation. V-notch ball valve cavitation characteristics are more complex due to the flow restrictions created by the notch geometry. The V-notch edge can create localized high-velocity zones that may promote cavitation under certain conditions. Advanced V-notch ball valve designs incorporate anti-cavitation features such as multiple-stage pressure reduction or specialized notch profiles to minimize cavitation potential. The erosion resistance of V-notch ball valves requires careful attention to materials selection, particularly for the V-notch edge and downstream areas where high-velocity flow occurs. Hardened ball materials and erosion-resistant coatings are often employed to extend service life in abrasive applications.
Application Considerations and Selection Criteria
Process Requirements and System Integration
The selection between O-type ball valve and V-notch ball valve configurations depends heavily on specific process requirements and system integration needs. O-type ball valves are ideally suited for applications requiring full-bore flow capability, minimal pressure drop, and reliable on-off service. These valves excel in pipeline isolation, emergency shutdown systems, and applications where quick response times are critical. The simple operation and high reliability of O-type ball valves make them preferred choices for remote or unmanned installations. The maintenance requirements are typically minimal due to the robust design and absence of complex internal components. Process systems utilizing O-type ball valves benefit from reduced energy consumption due to the low pressure losses and simplified control requirements. V-notch ball valve applications focus on process control, flow regulation, and throttling service. These valves are particularly valuable in applications requiring precise flow control, such as chemical dosing systems, heat exchanger bypass control, and process variable regulation. The ability to provide stable control across a wide flow range makes V-notch ball valves suitable for varying process conditions. The integration with automated control systems is enhanced by the predictable flow characteristics and excellent rangeability. Process systems benefit from the reduced need for additional control valves or flow restriction devices when V-notch ball valves are properly selected and sized.
Material Selection and Service Conditions
The material selection for O-type ball valve applications can focus on standard materials and proven combinations due to the straightforward flow geometry. Carbon steel, stainless steel, and specialty alloys are readily available in O-type ball valve configurations. The material requirements are primarily driven by pressure, temperature, and corrosion resistance considerations. The seat materials for O-type ball valves can utilize standard elastomers or thermoplastics for most applications. High-temperature service may require metal-seated designs with specialized surface treatments. The predictable stress patterns in O-type ball valve designs allow for standardized material specifications and proven performance data. V-notch ball valve material selection requires additional consideration for erosion and wear resistance due to the flow patterns created by the notch geometry. The V-notch edges are subject to high-velocity flow impingement and may require hardened materials or surface treatments. The seat materials must accommodate the irregular ball geometry while providing effective sealing and wear resistance. Specialized materials such as tungsten carbide, stellite, or ceramic coatings may be required for severe service applications. The material selection process for V-notch ball valves often involves customization based on specific service conditions and performance requirements.
Economic Considerations and Lifecycle Costs
The economic evaluation of O-type ball valve versus V-notch ball valve options must consider initial costs, operational expenses, and lifecycle factors. O-type ball valves typically offer lower initial costs due to simpler manufacturing requirements and standardized designs. The operational costs are generally lower due to reduced maintenance requirements and energy-efficient operation. The lifecycle costs benefit from extended service intervals and standardized replacement parts availability. The total cost of ownership for O-type ball valve installations is often favorable for on-off applications and high-flow systems. V-notch ball valve economic considerations must account for the specialized manufacturing requirements and customized designs. The initial costs may be higher due to the precision machining required for the V-notch geometry and specialized materials. However, the operational benefits of precise flow control can result in overall system cost savings through improved process efficiency and reduced energy consumption. The lifecycle costs may be influenced by the wear characteristics of the V-notch design and the availability of replacement components. The total cost of ownership analysis should consider the value of improved process control and system optimization capabilities.
Conclusion
The comparison between O-type ball valve and V-notch ball valve technologies reveals distinct advantages for each design based on specific application requirements. O-type ball valves excel in on-off service applications where high flow capacity, minimal pressure drop, and reliable operation are paramount. Their straightforward design and predictable performance characteristics make them ideal for pipeline isolation and emergency shutdown systems. V-notch ball valves provide superior flow control capabilities with excellent rangeability and precise throttling performance, making them valuable for process control applications requiring variable flow regulation. As a leading technology multinational company, CEPAI Group Co., Ltd. leverages its extensive experience in high-end energy valve manufacturing to provide customers with exceptional durability and high-precision control performance. Our comprehensive R&D investment and innovation achievements, supported by multiple patents and technological barriers, ensure that our O-type ball valve solutions meet the most demanding industrial requirements. With our rich product range, pre-sales technical support, and after-sales service guarantee, combined with industry recognition and qualification certifications including API Q1, API 6A, API 6D, and ISO certifications, CEPAI delivers reliable valve solutions backed by our good brand image and stable supplier relationships. Whether you require the high-flow efficiency of O-type ball valves or the precise control capabilities of V-notch designs, our team of experts is ready to provide comprehensive pre-sales technical consultation and valve selection services, customized solution services, and complete installation, debugging, and training support. Our commitment to quality through strict ISO quality system implementation, combined with our after-sales service and maintenance programs, remote monitoring and intelligent services, and product quality traceability guarantees, ensures your investment delivers long-term value. Contact us today at cepai@cepai.com to discuss your specific valve requirements and discover how our advanced valve technologies can optimize your industrial processes.
References
1. Smith, J.A., "Industrial Valve Design and Applications: A Comprehensive Guide to Ball Valve Technologies," Journal of Process Engineering, Vol. 45, No. 3, 2023, pp. 178-195.
2. Johnson, M.R. and Williams, K.L., "Flow Characteristics and Performance Analysis of V-notch Ball Valves in Process Control Applications," International Review of Mechanical Engineering, Vol. 17, No. 8, 2023, pp. 445-462.
3. Anderson, P.C., "Comparative Study of Ball Valve Configurations for High-Pressure Industrial Applications," Valve World Magazine Technical Review, Vol. 28, No. 12, 2023, pp. 34-47.
4. Thompson, R.D., Chen, L.M., and Davis, S.A., "Advanced Materials and Design Considerations for Modern Ball Valve Systems," Proceedings of the International Conference on Industrial Fluid Power, 2023, pp. 267-284.
_1746598557316.webp)
Get professional pre-sales technical consultation and valve selection services, customized solution services.
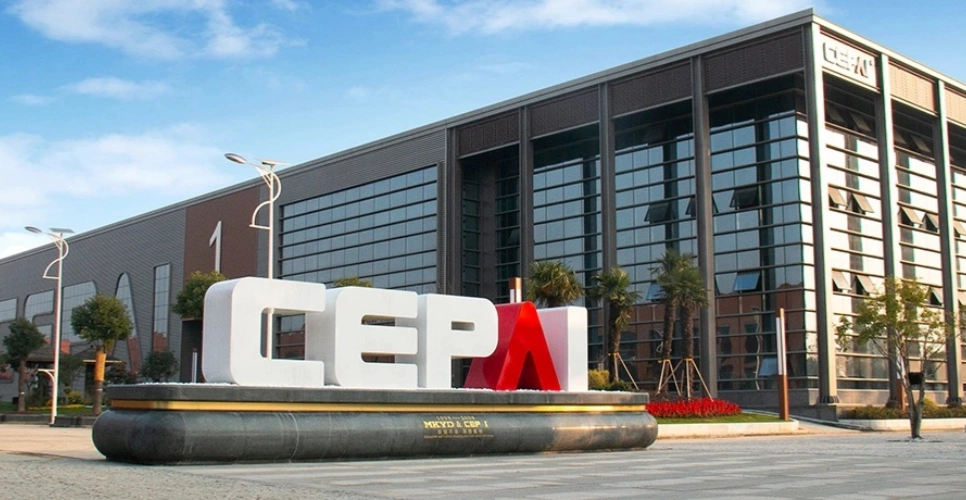
About CEPAI