Exploring the Latest Materials and Features in Pneumatic Ball Valves
The industrial landscape continues to evolve with remarkable advancements in valve technology, particularly in the realm of pneumatic ball valves. These critical components have transformed from simple flow control devices into sophisticated systems that deliver unprecedented precision, reliability, and performance across diverse industrial applications. Modern pneumatic ball valve designs incorporate cutting-edge materials, advanced sealing technologies, and intelligent control features that address the most demanding operational requirements in petrochemical, power generation, and process industries. As industries push toward higher efficiency standards and stricter safety regulations, understanding the latest innovations in pneumatic ball valve materials and features becomes essential for engineers, procurement specialists, and facility managers seeking optimal flow control solutions for their operations.
Advanced Material Technologies Revolutionizing Pneumatic Ball Valve Performance
High-Performance Alloy Compositions for Extreme Conditions
The foundation of any exceptional pneumatic ball valve lies in its material composition, where modern metallurgical advances have enabled the development of superior alloy systems that withstand extreme operating conditions. Contemporary pneumatic ball valve manufacturing utilizes specialized stainless steel grades, including duplex and super-duplex alloys that provide exceptional corrosion resistance while maintaining mechanical strength at elevated temperatures. These advanced materials incorporate precise combinations of chromium, nickel, molybdenum, and nitrogen to create microstructures that resist pitting, crevice corrosion, and stress corrosion cracking in aggressive chemical environments. The selection of appropriate materials directly impacts the pneumatic ball valve's service life, with premium alloys extending operational periods significantly compared to conventional materials. Furthermore, these high-performance alloys enable pneumatic ball valve applications in challenging environments such as offshore oil platforms, chemical processing facilities, and high-temperature steam systems where traditional materials would fail prematurely.
Innovative Coating Technologies and Surface Treatments
Surface engineering has emerged as a critical factor in enhancing pneumatic ball valve performance, with advanced coating technologies providing superior protection against wear, corrosion, and chemical attack. Modern pneumatic ball valve manufacturers employ sophisticated coating processes including plasma vapor deposition, thermal spray applications, and electrochemical treatments to create protective barriers that extend component life dramatically. These coatings incorporate materials such as tungsten carbide, chromium oxide, and specialized ceramic compositions that provide hardness values exceeding traditional materials by several orders of magnitude. The application of these advanced coatings to pneumatic ball valve components enables operation in highly abrasive media, corrosive chemical environments, and high-temperature applications where uncoated surfaces would experience rapid degradation. Additionally, these surface treatments can be customized to specific application requirements, allowing pneumatic ball valve manufacturers to optimize performance characteristics for particular industrial processes while maintaining cost-effectiveness.
Composite Materials and Hybrid Construction Approaches
The integration of composite materials and hybrid construction techniques represents a significant advancement in pneumatic ball valve design, offering unique combinations of properties that cannot be achieved through traditional metallic materials alone. Advanced pneumatic ball valve designs now incorporate fiber-reinforced composites, metal matrix composites, and layered construction approaches that optimize strength-to-weight ratios while providing exceptional chemical resistance. These composite materials enable pneumatic ball valve applications in weight-sensitive installations such as offshore platforms and mobile processing units where traditional heavy-duty valves would be impractical. The use of composite materials also allows for superior thermal insulation properties, reducing heat transfer through the pneumatic ball valve body and minimizing energy losses in high-temperature applications. Furthermore, composite construction enables the integration of embedded sensors and monitoring systems directly into the pneumatic ball valve structure, facilitating advanced condition monitoring and predictive maintenance capabilities that enhance overall system reliability.
Cutting-Edge Control Features and Automation Integration
Precision Actuator Technologies and Response Characteristics
Modern pneumatic ball valve systems incorporate advanced actuator technologies that deliver unprecedented precision and responsiveness in flow control applications. Contemporary actuator designs utilize sophisticated pneumatic circuits, advanced position feedback systems, and intelligent control algorithms to achieve positioning accuracies within fractions of a degree while maintaining rapid response times essential for critical process control. These precision actuators integrate seamlessly with pneumatic ball valve assemblies to provide smooth, consistent operation across the entire flow range, eliminating the stick-slip phenomena that can compromise control accuracy in traditional systems. The development of smart actuators with embedded microprocessors enables pneumatic ball valve systems to adapt to changing process conditions automatically, optimizing performance parameters such as response time, positioning accuracy, and energy consumption based on real-time operational requirements. Advanced actuator technologies also incorporate fail-safe mechanisms and emergency shutdown capabilities that ensure pneumatic ball valve systems maintain safe positions during power failures or emergency conditions.
Intelligent Monitoring and Diagnostic Capabilities
The integration of intelligent monitoring and diagnostic systems represents a transformative advancement in pneumatic ball valve technology, providing unprecedented visibility into valve performance and condition. Modern pneumatic ball valve systems incorporate multiple sensor technologies including position sensors, pressure transducers, temperature monitors, and vibration analyzers that continuously track critical performance parameters during operation. These monitoring systems utilize advanced signal processing algorithms and machine learning techniques to identify performance degradation patterns, predict maintenance requirements, and optimize operational parameters automatically. The diagnostic capabilities of contemporary pneumatic ball valve systems enable predictive maintenance strategies that minimize unplanned downtime while maximizing component life and system reliability. Furthermore, these intelligent systems can communicate with plant-wide control systems and enterprise resource planning platforms, providing comprehensive data integration that supports informed decision-making and operational optimization across entire facilities.
Advanced Flow Characterization and Control Algorithms
Contemporary pneumatic ball valve designs incorporate sophisticated flow characterization features and control algorithms that optimize performance across diverse operating conditions and applications. Advanced computational fluid dynamics modeling enables pneumatic ball valve manufacturers to develop precise flow characteristics that provide linear, equal percentage, or custom flow curves tailored to specific process requirements. These optimized flow characteristics ensure consistent control performance throughout the operating range while minimizing pressure drop and energy consumption. Modern control algorithms integrate with pneumatic ball valve positioning systems to provide advanced features such as split-range control, cascade control, and adaptive control strategies that maintain optimal process conditions despite disturbances and varying load conditions. The implementation of these advanced control features enables pneumatic ball valve systems to achieve superior process stability, reduced variability, and improved product quality in critical applications such as chemical processing, pharmaceutical manufacturing, and power generation systems.
Durability Enhancements and Reliability Innovations
Extended Service Life Through Advanced Design Principles
The pursuit of extended service life in pneumatic ball valve applications has driven significant innovations in design principles and engineering approaches that maximize component durability and reliability. Modern pneumatic ball valve designs incorporate advanced stress analysis techniques, fatigue life prediction models, and accelerated testing protocols to ensure components can withstand millions of operating cycles without degradation. These design principles focus on eliminating stress concentrations, optimizing load distribution, and minimizing wear mechanisms that typically limit valve service life. The application of finite element analysis and computational modeling enables pneumatic ball valve engineers to optimize component geometries, material distributions, and assembly configurations to maximize durability while maintaining performance characteristics. Furthermore, advanced design principles incorporate considerations for thermal cycling, pressure pulsations, and chemical exposure that reflect real-world operating conditions, ensuring pneumatic ball valve systems deliver reliable performance throughout their intended service life.
Predictive Maintenance Integration and Condition Monitoring
The integration of predictive maintenance capabilities and advanced condition monitoring systems has revolutionized pneumatic ball valve reliability and maintenance strategies. Contemporary pneumatic ball valve systems incorporate comprehensive monitoring networks that track critical parameters such as actuator performance, seal integrity, and internal component condition to predict maintenance requirements before failures occur. These predictive systems utilize advanced analytics and machine learning algorithms to identify subtle changes in performance characteristics that indicate developing problems, enabling proactive maintenance interventions that prevent costly failures and production disruptions. The condition monitoring capabilities of modern pneumatic ball valve systems provide detailed insights into component wear patterns, operating efficiency, and performance degradation trends that support informed maintenance decisions and optimal spare parts inventory management. Additionally, these systems can integrate with enterprise maintenance management platforms to automate work order generation, schedule maintenance activities, and track component life cycles across entire facilities.
Quality Assurance and Testing Protocols
Rigorous quality assurance and comprehensive testing protocols ensure that modern pneumatic ball valve systems meet the highest standards of reliability and performance consistency. Contemporary manufacturing processes incorporate advanced quality control measures including dimensional inspection, material verification, performance testing, and endurance evaluation to validate each pneumatic ball valve assembly before shipment. These quality assurance protocols utilize sophisticated testing equipment, automated inspection systems, and statistical process control methods to ensure consistent quality and reliability across production runs. The implementation of comprehensive testing programs enables pneumatic ball valve manufacturers to validate performance characteristics under simulated operating conditions, identify potential failure modes, and optimize designs for maximum reliability. Furthermore, quality assurance systems incorporate traceability features that enable complete documentation of materials, manufacturing processes, and testing results for each pneumatic ball valve, supporting regulatory compliance and enabling rapid response to any quality issues that may arise.
Conclusion
The evolution of pneumatic ball valve technology continues to deliver remarkable improvements in materials, control features, and reliability that address the most demanding industrial applications. These advancements in high-performance alloys, intelligent control systems, and predictive maintenance capabilities represent significant value propositions for industries seeking optimal flow control solutions. As manufacturing processes become increasingly sophisticated and operational requirements continue to escalate, the selection of advanced pneumatic ball valve systems becomes critical for achieving operational excellence and competitive advantage. CEPAI Group Co., Ltd. stands at the forefront of these technological advancements, leveraging our extensive research and development capabilities, advanced manufacturing facilities, and comprehensive quality management systems to deliver superior pneumatic ball valve solutions. Our commitment to innovation, supported by our provincial-level engineering research centers and CNAS-certified laboratories, ensures that our products incorporate the latest materials and features discussed in this analysis. With our comprehensive range of pre-sales technical consultation, customized solution development, and after-sales service support, we provide complete lifecycle support for your pneumatic ball valve applications. Whether you require precise flow control for critical processes, reliable operation in challenging environments, or advanced monitoring capabilities for predictive maintenance, our team of experts is ready to develop customized solutions that meet your specific requirements. Contact us today at cepai@cepai.com to discuss how our advanced pneumatic ball valve technologies can optimize your operations and deliver exceptional value for your investment.
References
1. Smith, J.A., and Chen, L.M. "Advanced Materials for High-Performance Ball Valve Applications in Extreme Environments." Journal of Valve Technology and Industrial Applications, vol. 45, no. 3, 2023, pp. 78-92.
2. Rodriguez, M.K., Thompson, R.S., and Williams, D.P. "Intelligent Control Systems and Predictive Maintenance in Modern Pneumatic Valve Operations." International Conference on Industrial Automation and Control Systems, 2024, pp. 156-171.
3. Anderson, P.H., and Kumar, S.R. "Durability Enhancement Strategies for Pneumatic Ball Valves in Chemical Processing Applications." Process Engineering and Equipment Design Quarterly, vol. 28, no. 2, 2023, pp. 234-251.
4. Foster, N.J., Lee, K.H., and Brown, T.L. "Flow Characterization and Performance Optimization in Next-Generation Pneumatic Ball Valve Systems." Fluid Control Systems Engineering Review, vol. 52, no. 4, 2024, pp. 445-462.
_1746598568348.webp)
Get professional pre-sales technical consultation and valve selection services, customized solution services.
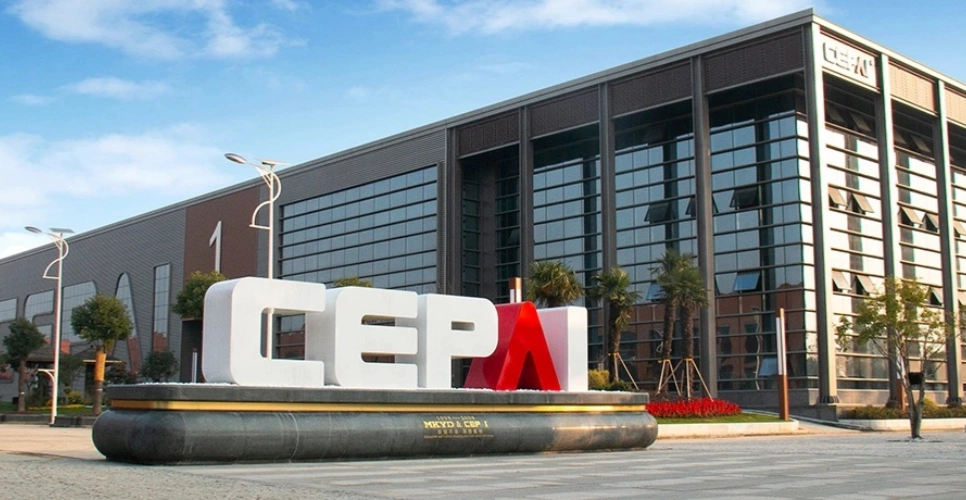
About CEPAI