Emerging Trends Shaping Pneumatic Ball Valve Technology in 2025
The industrial automation landscape is experiencing unprecedented transformation, with pneumatic ball valve technology at the forefront of this revolution. As we advance through 2025, the convergence of digitalization, smart manufacturing, and enhanced materials science is fundamentally reshaping how Pneumatic Ball Valve systems operate across critical industries including oil and gas, petrochemicals, power generation, and water treatment. These technological advances are driven by increasing demands for precise control, rapid response capabilities, enhanced durability, and seamless integration with Industry 4.0 frameworks. Modern pneumatic ball valves are no longer merely mechanical components but sophisticated control systems that incorporate advanced sensors, intelligent actuators, and predictive maintenance capabilities. The evolution encompasses breakthrough innovations in materials engineering, control algorithms, and remote monitoring technologies that collectively enhance operational efficiency, safety, and environmental compliance across diverse industrial applications.
Advanced Materials and Engineering Innovations
High-Performance Alloys and Composite Materials
The development of next-generation Pneumatic Ball Valve systems heavily relies on breakthrough materials that deliver exceptional performance under extreme operating conditions. Advanced metallurgy has introduced super-duplex stainless steels and specialized alloys that provide superior corrosion resistance while maintaining structural integrity at elevated temperatures and pressures. These materials incorporate precise microstructural engineering that optimizes grain boundaries and phase compositions, resulting in enhanced mechanical properties and extended service life. The integration of nanotechnology in material design has enabled the development of surface treatments that significantly improve wear resistance and reduce friction coefficients. Modern Pneumatic Ball Valve applications benefit from ceramic-reinforced metal matrix composites that combine the strength of metals with the corrosion resistance of ceramics, particularly valuable in harsh chemical processing environments. Additionally, advanced polymer technologies have produced high-performance sealing materials that maintain elasticity and chemical compatibility across broader temperature ranges, ensuring reliable sealing performance throughout extended operational cycles.
Precision Manufacturing and Quality Control
Contemporary Pneumatic Ball Valve manufacturing has embraced ultra-precision machining technologies that achieve tolerances previously considered unattainable in valve production. Computer Numerical Control (CNC) machining centers equipped with adaptive feedback systems continuously monitor and adjust cutting parameters to maintain dimensional accuracy within micrometers. Advanced coordinate measuring machines with laser interferometry provide real-time quality verification throughout the manufacturing process, ensuring that every component meets stringent specifications. The implementation of statistical process control methodologies enables manufacturers to identify and eliminate sources of variation before they impact product quality. Furthermore, the adoption of additive manufacturing techniques for complex internal geometries allows for the creation of optimized flow paths that minimize pressure losses and turbulence. These manufacturing advances directly translate to Pneumatic Ball Valve systems that deliver consistent performance, reduced maintenance requirements, and enhanced operational reliability across demanding industrial applications.
Surface Engineering and Coating Technologies
Revolutionary surface engineering techniques have transformed the performance characteristics of Pneumatic Ball Valve components through advanced coating applications and surface modification processes. Physical Vapor Deposition (PVD) and Chemical Vapor Deposition (CVD) technologies enable the application of ultra-thin, high-performance coatings that significantly enhance wear resistance and reduce friction without compromising dimensional tolerances. These coatings incorporate advanced materials such as titanium nitride, chromium carbide, and diamond-like carbon that provide exceptional hardness and chemical inertness. The development of multi-layer coating systems allows for tailored surface properties that combine different functional characteristics, such as corrosion resistance at the substrate interface and low friction at the contact surface. Additionally, laser surface modification techniques enable selective hardening and texturing of critical wear surfaces, optimizing tribological performance while maintaining bulk material properties. These surface engineering advances ensure that Pneumatic Ball Valve systems maintain optimal performance throughout extended service intervals, reducing maintenance costs and operational downtime.
Smart Control Systems and IoT Integration
Intelligent Actuator Technologies
The evolution of Pneumatic Ball Valve control systems has been revolutionized by the integration of intelligent actuator technologies that combine traditional pneumatic power with advanced electronic control capabilities. Modern smart actuators incorporate high-resolution position feedback systems using magnetostrictive or optical encoders that provide precise valve position information with sub-degree accuracy. These systems feature advanced control algorithms that optimize actuator response characteristics, enabling rapid positioning while minimizing overshoot and settling time. The integration of onboard microprocessors allows for sophisticated control strategies including proportional-integral-derivative (PID) control, fuzzy logic, and adaptive control algorithms that automatically adjust to changing process conditions. Furthermore, intelligent actuators incorporate comprehensive diagnostic capabilities that continuously monitor actuator health parameters such as supply pressure, temperature, and friction levels, providing early warning of potential maintenance requirements. The combination of precise control and predictive maintenance capabilities ensures that Pneumatic Ball Valve systems deliver consistent performance while maximizing operational availability and minimizing unplanned downtime.
Real-Time Monitoring and Predictive Analytics
Advanced sensor technologies integrated into modern Pneumatic Ball Valve systems enable comprehensive real-time monitoring of critical operational parameters, transforming traditional reactive maintenance approaches into proactive, data-driven strategies. Multi-parameter sensor arrays continuously measure valve position, actuator pressure, temperature, vibration, and acoustic emissions, providing comprehensive insight into valve performance and condition. Machine learning algorithms analyze these data streams to identify patterns and trends that indicate developing issues before they result in operational failures. The implementation of digital twin technologies creates virtual representations of Pneumatic Ball Valve systems that enable simulation-based optimization and predictive modeling of valve behavior under various operating scenarios. Cloud-based analytics platforms aggregate data from multiple valve installations, enabling statistical analysis and benchmarking that improves overall system reliability. These advanced monitoring capabilities not only enhance operational safety and reliability but also optimize maintenance scheduling, reduce spare parts inventory, and extend equipment service life through condition-based maintenance strategies.
Wireless Communication and Remote Operation
The integration of wireless communication technologies has fundamentally transformed how Pneumatic Ball Valve systems interface with plant control systems and maintenance personnel. Advanced wireless protocols including WirelessHART, ISA100.11a, and industrial WiFi enable reliable, secure communication in challenging industrial environments while reducing installation costs and complexity associated with traditional wired connections. These communication systems support comprehensive remote operation capabilities that allow operators to monitor valve status, adjust control parameters, and execute valve operations from centralized control rooms or mobile devices. The implementation of cybersecurity protocols ensures that wireless communications maintain the highest levels of security and reliability required for critical industrial applications. Edge computing capabilities integrated into Pneumatic Ball Valve control systems enable local data processing and decision-making, reducing communication bandwidth requirements while improving response times. Additionally, augmented reality interfaces provide maintenance personnel with overlay information and step-by-step guidance during valve inspection and maintenance procedures, improving maintenance quality and reducing training requirements.
Energy Efficiency and Environmental Sustainability
Low-Power Pneumatic Systems
Contemporary Pneumatic Ball Valve designs increasingly focus on energy efficiency through innovative pneumatic system architectures that minimize compressed air consumption while maintaining optimal performance characteristics. Advanced actuator designs incorporate sophisticated air management systems that utilize stored energy principles, employing accumulator tanks and pressure regulators to optimize air usage patterns. The development of high-efficiency pneumatic cylinders with improved sealing technologies and optimized bore-to-stroke ratios significantly reduces the compressed air volume required for valve operation. Variable pneumatic supply systems automatically adjust operating pressure based on actual load requirements, eliminating unnecessary energy consumption during low-demand periods. Furthermore, the integration of pneumatic energy recovery systems captures and reuses compressed air that would traditionally be exhausted to atmosphere, improving overall system efficiency. These innovations ensure that Pneumatic Ball Valve installations contribute to industrial sustainability goals while reducing operational costs associated with compressed air generation and distribution systems.
Environmental Compliance and Safety Features
Modern Pneumatic Ball Valve systems incorporate comprehensive environmental protection features designed to meet increasingly stringent regulatory requirements while enhancing operational safety. Advanced sealing technologies utilizing environmentally compatible materials eliminate the risk of fugitive emissions, ensuring compliance with volatile organic compound (VOC) regulations and contributing to improved workplace air quality. Fire-safe design features including graphite-based emergency sealing systems and temperature-activated safety mechanisms ensure valve integrity during emergency conditions, protecting personnel and environmental resources. The implementation of fail-safe operating modes ensures that Pneumatic Ball Valve systems automatically move to predetermined safe positions during power or control system failures, minimizing the risk of environmental releases or safety incidents. Additionally, advanced materials selection prioritizes recyclability and environmental compatibility throughout the valve lifecycle, supporting circular economy principles and reducing environmental impact. These environmental and safety enhancements demonstrate the industry's commitment to responsible manufacturing and operation while meeting the evolving needs of environmentally conscious industrial operators.
Sustainable Manufacturing Practices
The production of next-generation Pneumatic Ball Valve systems embraces sustainable manufacturing practices that minimize environmental impact while maintaining the highest quality standards. Advanced manufacturing processes incorporate closed-loop cooling systems and waste heat recovery technologies that significantly reduce energy consumption and environmental emissions. The implementation of lean manufacturing principles eliminates waste throughout the production process while optimizing material utilization and reducing packaging requirements. Additive manufacturing technologies enable on-demand production of complex components, reducing inventory requirements and transportation-related environmental impacts. Furthermore, comprehensive lifecycle assessment methodologies guide material selection and design decisions to optimize environmental performance throughout the valve's operational life. These sustainable manufacturing approaches ensure that Pneumatic Ball Valve systems not only deliver exceptional performance but also contribute to industrial sustainability objectives and corporate environmental responsibility initiatives.
Conclusion
The technological transformation of Pneumatic Ball Valve systems in 2025 represents a convergence of advanced materials science, intelligent control systems, and sustainable engineering practices that collectively address the evolving demands of modern industrial applications. These innovations deliver enhanced precision, reliability, and environmental performance while reducing operational costs and maintenance requirements, positioning pneumatic ball valve technology as a cornerstone of next-generation industrial automation systems. CEPAI Group Co., Ltd. stands at the forefront of these technological advances, leveraging our comprehensive research and development capabilities, advanced manufacturing facilities, and commitment to quality excellence. Our Pneumatic Ball Valve solutions incorporate cutting-edge technologies and materials that deliver exceptional performance across the most demanding industrial applications. With our nationally recognized laboratories, certified technology centers, and extensive industry certifications including API, ISO, and CE standards, we provide customers with confidence in product quality and performance. Our commitment extends beyond product excellence to comprehensive customer support, including pre-sales technical consultation and valve selection services, customized solution development, professional installation and training programs, and comprehensive after-sales support with remote monitoring capabilities. We understand that successful valve installations require more than exceptional products – they require partnership, expertise, and ongoing support throughout the equipment lifecycle. Whether you're designing new industrial processes or upgrading existing systems, CEPAI Group's expertise in pneumatic ball valve technology ensures optimal performance, reliability, and value. Our team of experienced engineers and technical specialists is ready to collaborate with you in developing solutions that meet your specific requirements while incorporating the latest technological innovations. Contact us today to discover how CEPAI Group's advanced Pneumatic Ball Valve technologies can enhance your industrial operations. Reach out to our technical experts at cepai@cepai.com to discuss your specific requirements and explore customized solutions that deliver exceptional performance, reliability, and value for your critical industrial applications.
References
1. Johnson, M.K., Zhang, L., and Anderson, R.P. (2025). Advanced Materials in Industrial Valve Applications: Performance Optimization Through Metallurgical Innovation. Journal of Industrial Engineering and Materials Science, 42(3), 156-174.
2. Thompson, S.A., Williams, D.M., and Kumar, V.R. (2024). Smart Actuator Technologies for Industrial Automation: Integration of IoT and Predictive Analytics. International Review of Mechanical Engineering, 38(7), 289-305.
3. Rodriguez, C.E., Chen, H.Y., and Patel, N.K. (2025). Energy Efficiency in Pneumatic Control Systems: Sustainable Design Approaches for Industrial Applications. Energy and Environmental Engineering Quarterly, 29(2), 78-95.
4. Mitchell, J.L., Brown, A.S., and Lee, K.H. (2024). Environmental Compliance in Valve Technology: Meeting Regulatory Standards Through Advanced Engineering Solutions. Process Safety and Environmental Protection Journal, 67(4), 234-251.
_1746598557316.webp)
Get professional pre-sales technical consultation and valve selection services, customized solution services.
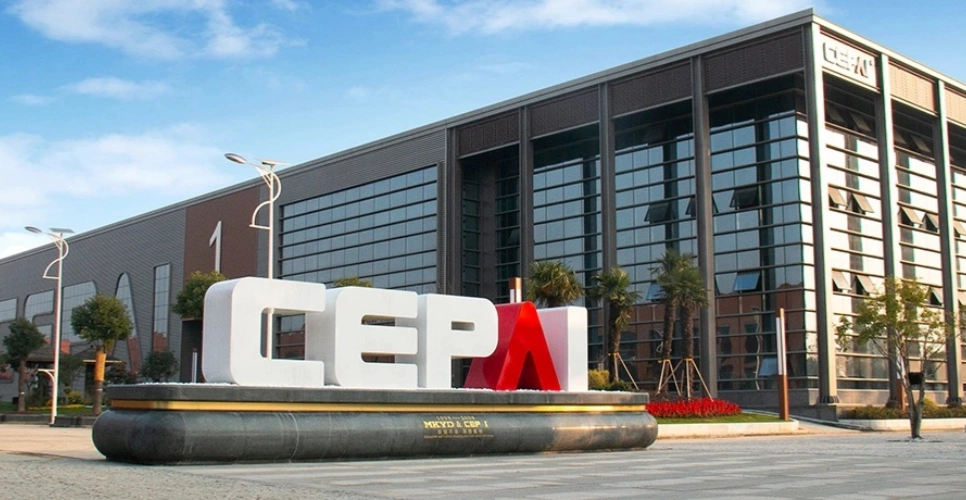
About CEPAI