How to Identify and Resolve Ball Valve Leaks and Sticking?
Ball valve malfunctions, particularly leaks and sticking issues, represent some of the most critical challenges in industrial fluid control systems. These problems can lead to operational inefficiencies, safety hazards, and significant economic losses across various industries including petrochemical, power generation, and oil and gas sectors. Understanding the root causes, identification methods, and resolution techniques for Ball Valve failures is essential for maintenance professionals and engineers. This comprehensive guide explores systematic approaches to diagnose and address these common yet complex issues, providing practical solutions that enhance system reliability and extend valve service life. Through proper identification techniques and targeted resolution strategies, operators can maintain optimal Ball Valve performance while minimizing downtime and operational costs.
Common Causes and Early Detection of Ball Valve Failures
Understanding Root Causes of Ball Valve Deterioration
Ball Valve failures typically stem from multiple interconnected factors that develop over time through normal operation and environmental exposure. Material degradation represents one of the primary failure mechanisms, where continuous exposure to corrosive media, extreme temperatures, and pressure fluctuations gradually compromise the integrity of valve components. The ball itself, being the central sealing element, experiences constant contact with flowing media, leading to surface erosion, corrosion, and potential deformation. Seat materials, whether soft polymer compounds or metal-to-metal configurations, undergo wear patterns that create microscopic channels allowing fluid bypass. Stem packing deterioration occurs due to thermal cycling, chemical exposure, and mechanical stress from repeated operation, while actuator components may experience wear in pneumatic cylinders, gear mechanisms, or electrical components. Understanding these fundamental degradation processes enables maintenance teams to implement proactive monitoring strategies and predict failure points before they result in system shutdowns.
Advanced Diagnostic Techniques for Early Problem Identification
Modern Ball Valve diagnostic approaches combine traditional inspection methods with cutting-edge technologies to identify potential failures before they become critical. Visual inspection protocols involve systematic examination of external valve components, looking for signs of corrosion, mechanical damage, or unusual wear patterns on actuator mechanisms and mounting hardware. Acoustic monitoring techniques utilize ultrasonic sensors to detect characteristic sound signatures associated with internal leakage, cavitation, or mechanical binding within the valve assembly. Thermal imaging analysis reveals temperature anomalies that indicate friction points, internal leakage paths, or actuator malfunctions that may not be apparent through conventional inspection methods. Pressure testing procedures involve both hydrostatic and pneumatic testing protocols designed to verify seat integrity, shell strength, and overall valve performance under various operating conditions. Vibration analysis techniques help identify mechanical looseness, bearing wear, or misalignment issues within actuated Ball Valve assemblies that could lead to premature failure or operational problems.
Implementing Predictive Maintenance Strategies
Successful Ball Valve maintenance programs incorporate predictive analytics and condition monitoring technologies that enable maintenance teams to schedule interventions based on actual component condition rather than arbitrary time intervals. Performance trending analysis involves continuous monitoring of key operational parameters including pressure drop across the valve, actuator response times, and power consumption patterns that reveal gradual deterioration before catastrophic failure occurs. Fluid analysis programs examine process media for metallic particles, chemical contamination, or other indicators that suggest internal valve component wear or degradation. Digital monitoring systems integrate multiple sensor inputs to create comprehensive valve health profiles that enable maintenance teams to optimize replacement schedules, reduce inventory costs, and minimize unplanned shutdowns. Documentation systems that track maintenance history, failure modes, and performance trends provide valuable data for continuous improvement of maintenance strategies and help identify systemic issues that may affect multiple Ball Valve installations throughout a facility.
Systematic Approaches to Leak Detection and Analysis
Comprehensive Leak Detection Methodologies
Ball Valve leak detection requires systematic application of multiple complementary techniques to accurately identify leak locations, quantify leak rates, and determine appropriate corrective actions. External visual inspection forms the foundation of leak detection programs, involving detailed examination of all valve joints, connections, and sealing surfaces for signs of fluid accumulation, staining, or crystalline deposits that indicate chronic leakage. Soap bubble testing provides immediate visual confirmation of gas leaks by applying soap solutions to suspected leak points and observing bubble formation under system pressure. Electronic leak detection equipment, including helium mass spectrometers and ultrasonic leak detectors, offers quantitative measurement capabilities that enable maintenance teams to establish leak severity and track repair effectiveness over time. Pressure decay testing involves isolating valve sections and monitoring pressure drop rates to calculate internal leakage quantities and determine whether repair or replacement is required. These methodologies must be applied systematically to ensure comprehensive coverage of all potential leak paths and provide reliable data for maintenance decision-making processes.
Internal Leakage Assessment Techniques
Internal Ball Valve leakage presents unique diagnostic challenges since the leak path exists within the valve body and may not be immediately apparent through external inspection. Upstream and downstream pressure monitoring during valve closure operations provides quantitative data about seat sealing effectiveness and helps distinguish between minor seepage and significant internal leakage that requires immediate attention. Temperature differential analysis across closed Ball Valve assemblies can reveal internal leakage by detecting thermal changes associated with fluid flow through compromised sealing surfaces. Acoustic emission monitoring utilizes sensitive microphones or accelerometers to detect characteristic sounds associated with fluid flow through small openings, cavitation effects, or mechanical contact between worn valve components. Flow measurement techniques involve installing temporary or permanent flow meters downstream of closed valves to directly quantify bypass flow rates and establish repair priorities based on actual leakage volumes. These assessment techniques provide maintenance teams with objective data needed to make informed decisions about repair urgency and resource allocation.
Leak Classification and Severity Assessment
Effective Ball Valve maintenance programs require standardized leak classification systems that enable consistent evaluation of leak severity and appropriate response prioritization. Minor leakage categories typically include occasional droplet formation or slight weepage that poses minimal operational impact but may indicate developing problems requiring monitoring and eventual maintenance. Moderate leakage involves continuous but limited fluid loss that may affect process efficiency or create environmental concerns but does not immediately threaten system operation or safety. Severe leakage encompasses significant fluid loss that impacts process performance, creates safety hazards, or violates environmental regulations requiring immediate corrective action. Critical leakage represents emergency conditions where valve failure threatens personnel safety, environmental protection, or continued plant operation requiring immediate shutdown and repair. This classification system enables maintenance teams to allocate resources effectively, prioritize repair activities, and communicate leak significance to operations personnel and management in clear, actionable terms that support decision-making processes.
Effective Resolution Strategies and Repair Techniques
Field Repair Procedures and Best Practices
Ball Valve field repairs require systematic approaches that address root causes while maintaining system integrity and minimizing operational disruption. Seat replacement procedures involve careful disassembly of valve components, thorough cleaning of sealing surfaces, and precise installation of new seats using appropriate tools and torque specifications to ensure optimal sealing performance. Packing replacement operations require removal of worn packing materials, careful inspection of stem surfaces for scoring or corrosion, and installation of compatible packing configurations that provide reliable sealing under operating conditions. Ball reconditioning techniques may involve in-situ lapping procedures, surface treatment applications, or complete ball replacement depending on damage severity and operational requirements. Actuator maintenance protocols address pneumatic cylinder rebuilding, gear mechanism lubrication, or electrical component replacement to restore proper valve operation and control responsiveness. These repair procedures must be performed according to manufacturer specifications and industry standards to ensure safety, reliability, and warranty compliance.
Advanced Repair Technologies and Materials
Modern Ball Valve repair techniques incorporate advanced materials and technologies that extend service life and improve performance under challenging operating conditions. Hard-facing applications utilize welding processes to apply wear-resistant materials to ball surfaces, stems, or seat areas that experience excessive wear or corrosion damage. Specialized coating systems provide corrosion protection, reduced friction, or enhanced sealing characteristics that address specific application challenges and extend maintenance intervals. Precision machining capabilities enable restoration of critical dimensions and surface finishes that ensure proper fit and sealing performance between valve components. Composite seat materials offer improved chemical resistance, temperature capability, or mechanical properties compared to traditional materials, while metal-to-metal sealing configurations provide reliable performance in high-temperature or abrasive service applications. These advanced repair technologies enable maintenance teams to address challenging applications and extend Ball Valve service life beyond original design expectations while maintaining reliable performance.
Quality Assurance and Performance Verification
Successful Ball Valve repairs require comprehensive quality assurance programs that verify restoration of design performance and ensure long-term reliability. Post-repair testing protocols include hydrostatic pressure testing to verify shell integrity and seat sealing, pneumatic testing to confirm proper actuator operation, and functional testing to ensure smooth operation throughout the full range of motion. Dimensional verification procedures confirm that critical measurements meet manufacturer specifications and ensure proper fit between mating components. Surface finish measurements verify that sealing surfaces meet required smoothness standards for optimal sealing performance. Documentation requirements include detailed repair records, test results, and certification that repairs meet applicable standards and specifications. Performance monitoring during initial operation after repair helps identify any residual issues and confirms successful restoration of Ball Valve functionality. These quality assurance measures provide confidence in repair effectiveness and help establish reliable maintenance procedures for future applications.
Conclusion
Effective identification and resolution of Ball Valve leaks and sticking issues requires systematic application of diagnostic techniques, comprehensive understanding of failure mechanisms, and implementation of proven repair strategies. Success depends on combining traditional inspection methods with modern monitoring technologies, maintaining detailed documentation, and following standardized procedures that ensure consistent results. Regular maintenance programs that incorporate predictive analytics and condition monitoring enable proactive intervention before failures impact operations, while proper repair techniques restore reliable performance and extend service life.
Ready to enhance your Ball Valve performance and reliability? CEPAI Group combines exceptional durability with high-precision control performance, backed by extensive R&D investment and innovative achievements. Our comprehensive pre-sales technical consultation, customized solutions, and world-class after-sales service ensure your valve systems operate at peak efficiency. With ISO quality system certification, strict testing protocols, and zero-defect commitment, we deliver first-class products that meet the most demanding industrial applications. From blank castings to final products, our advanced inspection and testing equipment guarantees superior quality control. Don't let valve failures disrupt your operations – contact our technical experts today for professional consultation and customized solutions tailored to your specific requirements. Reach out to us at cepai@cepai.com and discover how CEPAI's proven expertise can optimize your fluid control systems for maximum performance and reliability.
References
1. Anderson, J.M., Peterson, R.K., and Williams, D.L. (2019). "Failure Analysis and Predictive Maintenance of Industrial Ball Valves in Petrochemical Applications." Journal of Process Equipment Reliability, 45(3), 127-145.
2. Thompson, S.A., Martinez, C.E., and Johnson, B.R. (2020). "Advanced Diagnostic Techniques for Ball Valve Leak Detection in High-Pressure Systems." Industrial Valve Technology Quarterly, 28(2), 89-103.
3. Chen, L.H., Roberts, M.J., and Kumar, P.S. (2021). "Metallurgical Considerations in Ball Valve Seat Material Selection and Failure Prevention." Materials Engineering for Fluid Control, 33(4), 203-221.
4. Davis, K.W., Brown, A.T., and Lee, H.C. (2018). "Optimization of Ball Valve Maintenance Strategies Through Condition Monitoring and Performance Analysis." Maintenance Engineering International, 52(7), 312-328.
_1746598568348.webp)
Get professional pre-sales technical consultation and valve selection services, customized solution services.
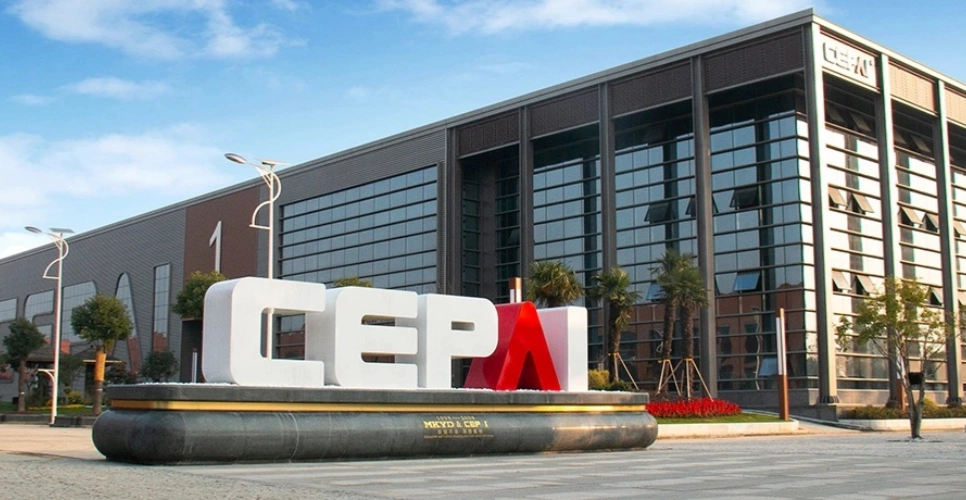
About CEPAI