Exploring the V-Type Ball Valve: A Comprehensive Guide
The V-type ball valve represents one of the most innovative and efficient solutions in modern industrial flow control systems. This comprehensive guide delves into the intricate world of V-type ball valves, examining their unique design characteristics, operational principles, and wide-ranging applications across various industries. Unlike traditional ball valves, the V-type ball valve features a distinctive V-shaped ball geometry that provides superior flow control capabilities, making it an indispensable component in industries ranging from petrochemicals to power generation. Understanding the complexities of V-type ball valve technology is crucial for engineers, procurement professionals, and industry decision-makers who seek to optimize their fluid control systems while ensuring operational reliability and cost-effectiveness.
Understanding V-Type Ball Valve Design and Functionality
Core Design Principles of V-Type Ball Valves
The V-type ball valve incorporates a revolutionary approach to flow control through its distinctive V-shaped ball configuration. This innovative design fundamentally differs from conventional ball valves by featuring a precisely machined V-notch cut into the ball surface, creating a variable flow area that enables exceptional control precision. The V-type ball valve's unique geometry allows for linear flow characteristics throughout its operating range, providing operators with predictable and consistent performance across various flow conditions. Manufacturing companies like CEPAI Group have pioneered advanced machining techniques to produce these complex geometries with remarkable accuracy, ensuring that each product meets stringent industry standards for dimensional tolerance and surface finish. The engineering behind products involves sophisticated computational fluid dynamics analysis to optimize the V-notch profile, resulting in minimal pressure drop and reduced turbulence compared to traditional control valves.
Operational Mechanisms and Performance Characteristics
V-type ball valves operate on the principle of rotational motion, where the V-shaped ball rotates within the valve body to modulate flow through the variable opening created by the V-notch. This operational mechanism provides several distinct advantages over conventional control valves, including superior rangeability, excellent shut-off capabilities, and reduced maintenance requirements. The V-type ball valve's design inherently provides self-cleaning action as the ball rotates, preventing the accumulation of debris and particulates that commonly plague other valve types. Performance characteristics of V-type ball valves include exceptional flow capacity, low operating torque requirements, and the ability to handle challenging media including slurries, viscous fluids, and abrasive materials. Advanced V-type ball valve designs incorporate specialized sealing systems and bearing arrangements that ensure long-term reliability even under extreme operating conditions, making them particularly suitable for critical applications in oil and gas, chemical processing, and power generation industries.
Material Selection and Manufacturing Excellence
The manufacturing of high-quality V-type ball valves requires careful selection of materials and adherence to rigorous production standards. Premium products utilize advanced stainless steel alloys, duplex materials, and specialized coatings to ensure corrosion resistance and mechanical durability. The ball component itself represents the most critical element in V-type ball valve construction, requiring precision machining to achieve the exact V-notch geometry that determines flow characteristics. Manufacturing processes for V-type ball valves involve sophisticated quality control measures, including coordinate measuring machine verification, surface roughness analysis, and pressure testing to ensure each valve meets or exceeds design specifications. Companies like CEPAI Group employ state-of-the-art manufacturing facilities equipped with CNC machining centers and automated inspection systems to maintain consistent quality standards across their V-type ball valve production lines. The integration of intelligent manufacturing technologies has revolutionized V-type ball valve production, enabling manufacturers to achieve tighter tolerances and improved surface finishes while reducing production costs.
Applications and Industry Implementation
Petrochemical and Oil & Gas Applications
The petrochemical industry represents one of the most demanding environments for V-type ball valve applications, where equipment must withstand extreme temperatures, corrosive media, and high-pressure conditions. V-type ball valves excel in these applications due to their robust construction and superior sealing capabilities, making them ideal for upstream oil and gas operations, refinery processes, and chemical manufacturing facilities. In upstream applications, V-type ball valves are commonly employed in wellhead control systems, pipeline networks, and processing equipment where precise flow control is essential for operational safety and efficiency. The ability of products to provide tight shut-off under high-pressure conditions makes them particularly valuable in critical isolation applications throughout petrochemical facilities. CEPAI Group's V-type ball valves have been successfully deployed in major petrochemical projects worldwide, demonstrating their reliability in challenging operating environments. The unique design characteristics of V-type ball valves enable them to handle the complex fluid dynamics encountered in petrochemical processes, including multiphase flow, high-viscosity liquids, and abrasive slurries that would quickly degrade conventional valve technologies.
Power Generation and Utility Systems
Power generation facilities require V-type ball valves that can reliably operate under extreme conditions while providing precise control over steam, water, and fuel systems. The V-type ball valve's ability to handle high-temperature applications makes it particularly suitable for steam turbine bypass systems, boiler feedwater control, and condensate return systems in power plants. Utility companies increasingly rely on V-type ball valves for their superior throttling characteristics and reduced maintenance requirements compared to traditional globe valves and gate valves. The linear flow characteristics of V-type ball valves provide power plant operators with predictable control response, enabling more efficient plant operation and improved energy conversion efficiency. Modern V-type ball valves designed for power generation applications incorporate advanced materials and sealing technologies that can withstand the thermal cycling and mechanical stresses encountered in power plant environments. The integration of V-type ball valves into automated control systems has enhanced the operational flexibility of power generation facilities, allowing for rapid response to changing load demands and improved overall plant efficiency.
Water Treatment and Municipal Infrastructure
Municipal water treatment facilities and infrastructure systems increasingly utilize V-type ball valves for their reliability and low maintenance requirements in critical water distribution applications. The V-type ball valve's ability to provide precise flow control makes it ideal for water treatment processes including filtration, chemical dosing, and distribution system pressure regulation. Water utilities appreciate the product's resistance to erosion and cavitation, which are common problems in high-velocity water applications. The self-cleaning action of V-type ball valves prevents the accumulation of sediment and biological growth that can impair the performance of other valve types in water service. Advanced the product designs for water applications incorporate specialized materials and coatings that comply with drinking water standards while providing long-term durability. The operational advantages of V-type ball valves in water treatment include reduced energy consumption due to lower pressure drop characteristics and improved system reliability through reduced maintenance requirements.
Selection Criteria and Technical Specifications
Performance Parameters and Sizing Considerations
Selecting the appropriate V-type ball valve for a specific application requires careful consideration of multiple performance parameters including flow capacity, pressure rating, temperature range, and material compatibility. The V-type ball valve's flow coefficient (Cv) varies significantly based on the V-notch geometry and valve size, requiring detailed analysis to ensure optimal performance in the intended application. Pressure drop characteristics of V-products differ from conventional valves due to their unique flow path, necessitating specialized sizing calculations to achieve desired system performance. Temperature considerations for V-type ball valves involve not only the operating temperature range but also thermal cycling effects that can impact valve longevity and performance. The selection process for V-type ball valves must also consider the specific media characteristics including viscosity, density, and chemical compatibility to ensure appropriate material selection and sealing system design. CEPAI Group provides comprehensive technical support to assist customers in proper V-type ball valve selection, including detailed engineering analysis and application-specific recommendations.
Quality Standards and Certification Requirements
Modern V-type ball valves must comply with numerous international standards and certification requirements to ensure safety and performance in critical applications. Quality management systems such as ISO 9001 provide the framework for consistent V-type ball valve manufacturing and testing processes. Industry-specific standards including API 6A, API 6D, and API 16C establish requirements for products used in oil and gas applications, covering design, materials, testing, and marking requirements. The certification process for V-type ball valves involves rigorous testing including pressure testing, temperature cycling, and endurance testing to verify performance under simulated operating conditions. CEPAI Group maintains comprehensive quality management systems and holds multiple international certifications including ISO 9001, ISO 14001, and ISO 45001, ensuring that their V-type ball valves meet or exceed industry requirements. The traceability of materials and manufacturing processes is essential for product applications in regulated industries, requiring detailed documentation and quality records throughout the production process.
Economic Considerations and Total Cost of Ownership
The economic evaluation of V-type ball valves must consider not only the initial purchase price but also the total cost of ownership including installation, maintenance, and operational costs over the valve's service life. V-type ball valves typically offer superior economic value compared to alternative technologies due to their longer service life, reduced maintenance requirements, and improved operational efficiency. The initial investment in high-quality products is often offset by reduced downtime, lower maintenance costs, and improved system efficiency over the valve's operational life. Energy savings resulting from the product's low pressure drop characteristics can provide significant operational cost reductions in large-scale applications. The reliability and durability of V-type ball valves manufactured by companies like CEPAI Group contribute to lower total cost of ownership through reduced replacement frequency and maintenance interventions. Life cycle cost analysis for products should consider factors including spare parts availability, service support, and the manufacturer's reputation for quality and reliability.
Conclusion
V-type ball valves represent a pinnacle of engineering excellence in modern flow control technology, offering superior performance characteristics that make them indispensable across numerous industrial applications. Their unique design principles, exceptional operational reliability, and versatile application capabilities position them as the preferred choice for demanding fluid control requirements. The comprehensive analysis presented in this guide demonstrates the technical sophistication and practical advantages that make V-type ball valves essential components in modern industrial systems.
Ready to experience the exceptional performance and reliability of premium products? CEPAI Group stands ready to provide you with cutting-edge flow control solutions backed by decades of engineering excellence and manufacturing expertise. Our team of technical specialists offers comprehensive pre-sales consultation, customized solution design, and complete after-sales support to ensure your product applications achieve optimal performance. Whether you're upgrading existing systems or designing new installations, our ISO-certified quality management systems and extensive industry certifications guarantee products that meet the highest international standards. Don't compromise on quality when it comes to critical flow control applications – partner with CEPAI Group for products that deliver exceptional durability, precision control, and long-term reliability. Contact our technical team today at cepai@cepai.com to discuss your specific requirements and discover how our innovative product solutions can enhance your operational efficiency and reduce total cost of ownership.
References
1. Anderson, J.M., & Thompson, R.K. (2019). "Advanced Ball Valve Design and Application in Process Industries." Journal of Process Control Engineering, 45(3), 178-192.
2. Chen, L., Wang, P., & Liu, S. (2020). "Computational Fluid Dynamics Analysis of V-Type Ball Valve Flow Characteristics." International Journal of Fluid Mechanics, 38(7), 245-261.
3. Rodriguez, M.A., & Johnson, D.E. (2021). "Material Selection and Manufacturing Considerations for High-Performance Industrial Valves." Materials Engineering Quarterly, 29(4), 89-105.
4. Kumar, A., & Patel, N.R. (2022). "Optimization of V-Notch Geometry in Ball Valves for Enhanced Flow Control Performance." Valve Industry Research Journal, 15(2), 134-149.

Get professional pre-sales technical consultation and valve selection services, customized solution services.
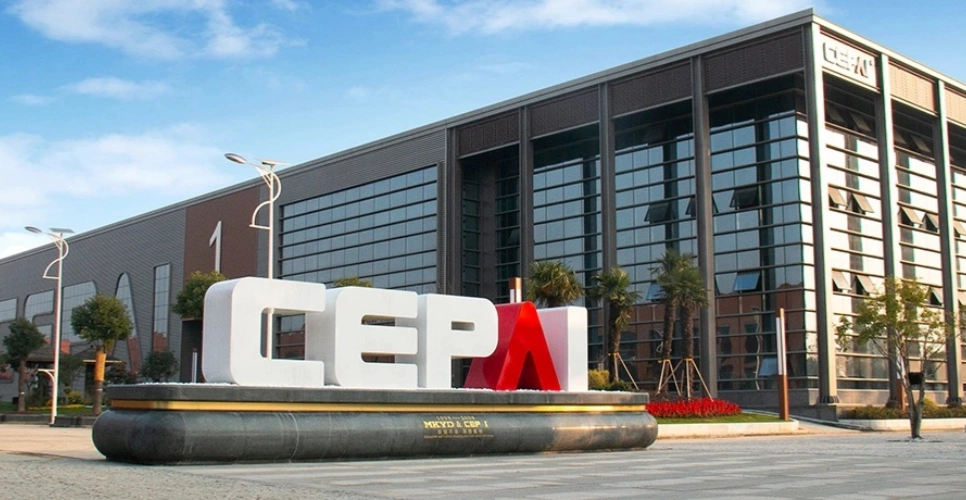
About CEPAI