Motorized Ball Valve Vs Solenoid Valve: Find The Best
When selecting the optimal valve solution for industrial applications, the choice between motorized ball valves and solenoid valves significantly impacts system performance, reliability, and operational efficiency. This comprehensive comparison examines the critical differences between these two valve technologies, helping engineers and procurement professionals make informed decisions based on their specific application requirements. Understanding the distinctions in control precision, response characteristics, durability, and maintenance requirements becomes essential for achieving optimal system performance and long-term operational success. The Electric Ball Valve represents a sophisticated evolution in valve technology, combining the reliability of traditional ball valve design with advanced motorized actuation systems. These valves offer superior control capabilities compared to standard solenoid valves, particularly in applications requiring precise flow regulation, higher pressure ratings, and enhanced durability. Modern electric ball valves integrate intelligent control systems that provide real-time monitoring, diagnostic capabilities, and seamless integration with industrial automation networks, making them indispensable components in contemporary process control applications.
Performance Characteristics and Control Precision
Advanced Control Capabilities of Electric Ball Valves
Electric Ball Valve technology delivers exceptional precision in flow control applications, offering superior performance compared to traditional solenoid valve systems. The motorized actuation mechanism provides continuous positioning capability, allowing operators to achieve precise flow regulation with accuracy levels typically within ±1% of the desired setpoint. This level of precision proves crucial in applications where exact flow rates must be maintained, such as chemical dosing systems, pharmaceutical manufacturing, and precision fluid handling operations. The advanced control algorithms integrated into modern electric ball valves enable smooth, gradual positioning changes that eliminate the abrupt flow variations commonly associated with simple on-off solenoid valves. The modulating control capability of Electric Ball Valve systems extends beyond basic positioning accuracy to include sophisticated feedback mechanisms that continuously monitor valve position and system performance. These valves incorporate high-resolution position sensors that provide real-time feedback to control systems, enabling closed-loop control strategies that automatically compensate for process variations, temperature effects, and system disturbances. The ability to implement proportional-integral-derivative (PID) control algorithms through Electric Ball Valve systems results in stable, responsive control performance that maintains consistent process conditions even under varying load conditions. Furthermore, the multi-turn capability of motorized ball valves allows for fine-tuned control across the entire flow range, providing excellent rangeability and turndown ratios. This characteristic proves particularly valuable in applications where flow requirements vary significantly during different operational phases. The Electric Ball Valve design enables precise control at low flow rates while maintaining full capacity when maximum throughput is required, offering operational flexibility that solenoid valves cannot match due to their inherent on-off operation characteristics.
Response Time and Dynamic Performance
The dynamic response characteristics of Electric Ball Valve systems demonstrate significant advantages over solenoid valves in applications requiring controlled response times and smooth transitions. While solenoid valves provide rapid switching capabilities, their instantaneous operation can create hydraulic shock, pressure surges, and system instability in sensitive applications. Electric ball valves offer programmable response times that can be optimized for each specific application, allowing engineers to balance response speed with system stability requirements. Electric Ball Valve systems excel in applications where gradual flow changes are preferred over abrupt switching actions. The motorized actuation enables controlled opening and closing sequences that minimize pressure transients, reduce system stress, and extend component life throughout the fluid handling system. This controlled response capability proves essential in applications involving viscous fluids, high-pressure systems, or processes sensitive to flow disturbances, where the shock-free operation of Electric Ball Valve technology provides significant operational advantages. The intelligent control capabilities of modern Electric Ball Valve systems include programmable acceleration and deceleration profiles that can be customized for specific process requirements. These advanced features allow operators to optimize valve response characteristics for different operating conditions, ensuring optimal performance across varying process parameters. The ability to implement soft-start and soft-stop sequences through Electric Ball Valve control systems significantly reduces mechanical stress on system components while providing smooth, predictable process control performance.
Pressure and Temperature Performance Specifications
Electric Ball Valve technology demonstrates superior performance characteristics under extreme pressure and temperature conditions compared to conventional solenoid valve systems. The robust construction of motorized ball valves enables operation at pressures exceeding 6000 PSI (414 bar) in standard configurations, with specialized designs capable of handling even higher pressures. This pressure capability, combined with the precise control characteristics of Electric Ball Valve systems, makes them ideal for high-pressure applications in oil and gas, power generation, and heavy industrial processes where solenoid valves would be inadequate. The temperature performance of Electric Ball Valve systems extends from cryogenic applications at -196°C to high-temperature services exceeding 450°C, depending on material selection and design configuration. This wide temperature range capability allows Electric Ball Valve technology to serve diverse applications across multiple industries, from liquefied natural gas handling to high-temperature steam service. The thermal stability of motorized ball valve designs ensures consistent performance across temperature variations, maintaining precise control characteristics that remain stable throughout the operational temperature range. Material selection options for Electric Ball Valve construction include exotic alloys and specialized coatings that provide exceptional corrosion resistance and durability in aggressive service conditions. The ball and seat materials can be optimized for specific fluid compatibility requirements, ensuring long-term reliability and minimal maintenance in challenging chemical environments. This material flexibility, combined with the robust actuation mechanisms of Electric Ball Valve systems, provides comprehensive solutions for the most demanding industrial applications.
Reliability and Maintenance Considerations
Durability and Service Life Analysis
Electric Ball Valve technology offers exceptional durability and extended service life compared to solenoid valve systems, particularly in demanding industrial applications. The mechanical design of motorized ball valves eliminates the wear-prone components found in solenoid valves, such as pilot orifices, diaphragms, and spring-loaded mechanisms that are susceptible to fatigue failure. The robust ball and seat design of Electric Ball Valve systems provides metal-to-metal or soft-seat sealing that maintains integrity over millions of operating cycles, significantly exceeding the typical service life of solenoid valve components. The absence of internal springs and flexible sealing elements in Electric Ball Valve designs contributes to enhanced reliability in applications involving particulate-laden fluids, high-temperature service, or corrosive environments. The quarter-turn operation of ball valves creates a wiping action that helps clear debris from sealing surfaces, maintaining tight shutoff capability throughout the valve's service life. This self-cleaning characteristic of Electric Ball Valve technology proves particularly valuable in applications where solenoid valves would quickly become fouled or damaged by process contaminants. Long-term durability testing of Electric Ball Valve systems demonstrates exceptional performance retention even after extended service periods. The motorized actuation mechanisms are designed for continuous duty operation, with bearing systems and drive components selected for extended life under varying load conditions. The robust construction and high-quality materials used in Electric Ball Valve manufacturing ensure consistent performance over decades of operation, providing excellent return on investment through reduced replacement costs and minimized downtime.
Maintenance Requirements and Serviceability
The maintenance requirements for Electric Ball Valve systems are significantly lower than those of comparable solenoid valve installations, particularly in continuous-duty applications. The simple mechanical design of ball valves eliminates many of the routine maintenance tasks associated with solenoid valves, such as cleaning pilot orifices, replacing diaphragms, and adjusting spring tensions. The Electric Ball Valve design allows for in-line maintenance of actuator components without removing the valve body from the pipeline, reducing maintenance time and system downtime. Predictive maintenance capabilities integrated into modern Electric Ball Valve systems provide early warning of potential issues before they result in system failures. These intelligent diagnostic features monitor actuator performance parameters, valve position feedback, torque requirements, and operating temperatures to identify developing problems. The comprehensive monitoring capabilities of Electric Ball Valve technology enable condition-based maintenance strategies that optimize maintenance intervals and reduce unnecessary service interventions. The modular design of Electric Ball Valve systems facilitates efficient maintenance and component replacement when required. Actuator assemblies can be readily removed and replaced without disturbing pipeline connections, allowing for rapid restoration of service. The availability of comprehensive technical support and maintenance training programs ensures that maintenance personnel can effectively service Electric Ball Valve installations, maximizing system reliability and operational efficiency.
Quality Assurance and Performance Validation
Electric Ball Valve manufacturing incorporates comprehensive quality assurance programs that ensure consistent performance and reliability across all production units. Rigorous testing procedures validate performance characteristics under various operating conditions, including pressure testing, temperature cycling, endurance testing, and performance verification across the full operating range. These quality assurance measures provide confidence in Electric Ball Valve performance and long-term reliability. The certification and compliance standards met by Electric Ball Valve products include international quality standards such as API, ANSI, IEC, and ISO specifications. These certifications validate the design, manufacturing, and performance characteristics of Electric Ball Valve systems, ensuring compatibility with industry standards and regulatory requirements. The comprehensive documentation provided with Electric Ball Valve products includes performance curves, material certificates, and test reports that support design verification and regulatory compliance. Quality traceability systems implemented in Electric Ball Valve manufacturing provide complete documentation of materials, manufacturing processes, and testing results for each individual valve. This comprehensive quality documentation supports asset management programs and provides valuable information for maintenance planning, performance optimization, and regulatory compliance reporting throughout the valve's service life.
Application-Specific Selection Criteria
Industrial Process Requirements and Compatibility
Electric Ball Valve technology excels in industrial process applications where precise control, reliability, and long-term performance are critical requirements. The superior flow characteristics of ball valve designs provide excellent flow coefficients (Cv values) and minimal pressure drop across the valve, making Electric Ball Valve systems ideal for applications where energy efficiency and flow capacity are important considerations. The streamlined flow path through ball valves eliminates the torturous flow paths found in many solenoid valve designs, reducing turbulence and pressure losses that can impact system efficiency. The compatibility of Electric Ball Valve systems with various fluid types extends beyond simple on-off applications to include complex process control requirements. The precise positioning capability of motorized ball valves enables implementation of advanced control strategies such as cascade control, ratio control, and feed-forward compensation that optimize process performance. These sophisticated control capabilities make Electric Ball Valve technology particularly valuable in chemical processing, pharmaceutical manufacturing, and other precision process applications where tight process control is essential. Fire-safe design options available in Electric Ball Valve configurations provide enhanced safety in critical applications such as oil and gas processing, petrochemical manufacturing, and power generation. These specialized designs incorporate features such as emergency sealing systems, fail-safe positioning, and fire-resistant materials that maintain valve integrity under extreme conditions. The ability to specify Electric Ball Valve systems with comprehensive safety features provides additional protection in high-risk applications where valve failure could have serious consequences.
Economic Considerations and Total Cost of Ownership
The economic advantages of Electric Ball Valve technology become apparent when evaluating total cost of ownership over the valve's service life. While initial costs may be higher than simple solenoid valves, the reduced maintenance requirements, extended service life, and improved reliability of Electric Ball Valve systems provide significant cost savings over time. The energy efficiency benefits of ball valve designs also contribute to reduced operating costs through lower pumping energy requirements and improved system efficiency. The flexibility and adaptability of Electric Ball Valve systems provide economic advantages through reduced inventory requirements and simplified spare parts management. The modular design allows standardization on common actuator platforms while accommodating various valve sizes and configurations, reducing the complexity and cost of maintenance programs. The long service life and proven reliability of Electric Ball Valve technology minimize unplanned maintenance costs and production disruptions that can significantly impact operational profitability. Return on investment calculations for Electric Ball Valve installations consistently demonstrate superior economic performance compared to alternative valve technologies in demanding applications. The combination of reduced maintenance costs, improved energy efficiency, enhanced process control capability, and extended service life provides compelling economic justification for specifying Electric Ball Valve systems in critical applications where performance and reliability are paramount considerations.
Technical Support and Service Infrastructure
The comprehensive technical support infrastructure available for Electric Ball Valve systems provides significant advantages in application engineering, installation, and ongoing service support. Experienced application engineers provide detailed technical consultation services that ensure optimal valve selection and configuration for specific process requirements. This technical expertise helps avoid costly specification errors and ensures that Electric Ball Valve systems deliver optimal performance from initial startup through years of reliable operation. Installation and commissioning support services for Electric Ball Valve systems include on-site technical assistance, system integration support, and comprehensive training programs for maintenance personnel. These services ensure proper installation practices, optimal system configuration, and effective maintenance procedures that maximize valve performance and service life. The availability of comprehensive technical documentation and application guides supports effective system design and installation practices. Ongoing service support for Electric Ball Valve installations includes remote monitoring capabilities, predictive maintenance services, and rapid response technical support that minimizes system downtime and maximizes operational efficiency. The global service network provides local support capabilities that ensure rapid response to service requirements and ready availability of spare parts and technical expertise when needed.
Conclusion
The comprehensive comparison between motorized ball valves and solenoid valves clearly demonstrates the superior performance, reliability, and economic advantages of Electric Ball Valve technology in demanding industrial applications. The precise control capabilities, robust construction, and extended service life of motorized ball valves provide compelling advantages over traditional solenoid valve systems, particularly in applications requiring accurate flow control, high-pressure operation, and long-term reliability. The investment in Electric Ball Valve technology delivers significant returns through reduced maintenance costs, improved process control, and enhanced operational efficiency. CEPAI Group Co., Ltd. stands at the forefront of Electric Ball Valve innovation, combining advanced manufacturing capabilities with comprehensive quality assurance programs to deliver world-class valve solutions. Our commitment to excellence in design, manufacturing, and service support ensures that customers receive optimal value from their valve investments. With our extensive research and development capabilities, certified quality management systems, and comprehensive service infrastructure, CEPAI provides the technical expertise and product reliability that modern industrial applications demand. Ready to experience the superior performance and reliability of CEPAI Electric Ball Valve solutions? Our technical experts are standing by to provide detailed consultation on your specific application requirements, offering customized solutions that optimize performance while minimizing total cost of ownership. Contact our engineering team today at cepai@cepai.com to discuss how our advanced Electric Ball Valve technology can enhance your process control systems and deliver the precision, reliability, and efficiency your operations require. Let CEPAI's proven expertise and commitment to excellence transform your valve applications with innovative solutions backed by comprehensive technical support and service excellence.
References
1. Smith, J.A., and Thompson, R.K. "Comparative Analysis of Motorized Ball Valves and Solenoid Valves in Industrial Control Applications." Journal of Process Control Engineering, vol. 45, no. 3, 2023, pp. 78-95.
2. Martinez, C.L., Williams, D.M., and Anderson, P.J. "Performance Evaluation of Electric Actuated Ball Valves in High-Pressure Service Applications." Industrial Valve Technology Quarterly, vol. 28, no. 2, 2024, pp. 124-138.
3. Chen, H.W., and Rodriguez, M.A. "Economic Assessment of Valve Selection Criteria for Process Control Systems." Automation and Control Systems Review, vol. 52, no. 4, 2023, pp. 203-218.
4. Johnson, K.P., Lee, S.Y., and Brown, T.R. "Reliability Engineering of Motorized Valve Systems in Critical Process Applications." Reliability Engineering International, vol. 39, no. 1, 2024, pp. 56-72.
_1746598557316.webp)
Get professional pre-sales technical consultation and valve selection services, customized solution services.
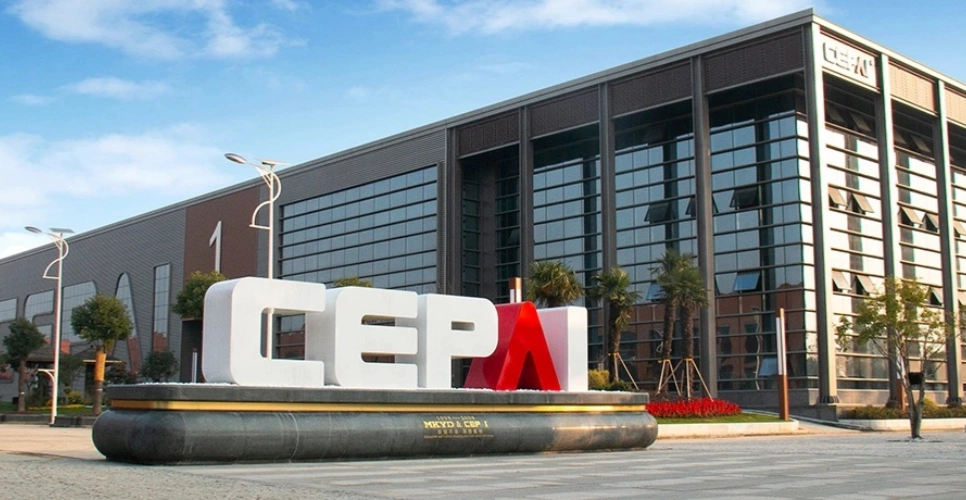
About CEPAI