Comparison of C-Type, O-Type, and V-Type Ball Valves: Structure, Function, and Application
Ball valves represent one of the most versatile and widely adopted flow control solutions in modern industrial applications, with distinct variations designed to meet specific operational requirements. Among the most prominent configurations are C-type, O-type, and V-type ball valves, each engineered with unique structural characteristics and functional capabilities. The O-type ball valve, distinguished by its spherical ball with a circular through-hole, offers exceptional sealing performance and rapid actuation, making it particularly suitable for on-off applications in petroleum, chemical, and power generation industries. Understanding the fundamental differences between these valve types is crucial for engineers and procurement professionals seeking optimal flow control solutions that balance performance, reliability, and cost-effectiveness across diverse industrial environments.
Structural Design and Engineering Characteristics
Ball Configuration and Flow Path Geometry
The structural foundation of ball valve performance lies in the precise engineering of the ball element and its interaction with the valve body. O-type ball valve designs feature a spherical ball with a cylindrical bore that provides unrestricted flow passage when fully opened, minimizing pressure drop and turbulence. This configuration ensures optimal flow characteristics with minimal energy loss, making it ideal for applications requiring maximum throughput efficiency. The ball's spherical geometry distributes stress evenly across the sealing surfaces, contributing to enhanced durability and extended service life. In contrast, C-type ball valves incorporate a segmented ball design that allows for compact installation in space-constrained applications, while V-type configurations utilize a V-shaped port that enables precise flow modulation and control. The O-type ball valve construction typically employs high-grade stainless steel or specialized alloys to withstand corrosive environments and extreme operating conditions, ensuring reliable performance across diverse industrial applications. The manufacturing precision required for O-type ball valve components demands advanced machining capabilities and stringent quality control measures. The spherical ball must maintain perfect roundness within micron tolerances to ensure proper sealing and smooth operation throughout the valve's operational lifecycle. Surface finishing techniques, including precision grinding and polishing, create the optimal surface texture for effective sealing while minimizing wear during repeated cycling operations. The bore geometry within the O-type ball valve is carefully engineered to eliminate flow restrictions and reduce cavitation potential, particularly critical in high-velocity fluid applications where pressure recovery downstream of the valve can cause significant operational challenges.
Sealing Mechanism and Material Selection
Advanced sealing technology represents a critical differentiator in O-type ball valve performance, with elastomeric and metal-to-metal sealing options available to address specific application requirements. Primary sealing occurs through the precise interaction between the ball surface and seat rings, which are typically manufactured from specialized polymers or metal alloys depending on temperature and chemical compatibility requirements. The O-type ball valve design incorporates multiple sealing stages, including primary seat seals, stem seals, and body joint seals, creating a comprehensive barrier against fluid leakage. Secondary sealing elements, such as O-rings and gaskets, provide additional protection against fugitive emissions, particularly important in environmental compliance applications. Material selection for sealing components considers factors including temperature range, chemical compatibility, pressure rating, and regulatory requirements, with options ranging from standard nitrile rubber to specialized fluoropolymers for extreme service conditions. The durability of O-type ball valve sealing systems depends heavily on the selection of appropriate materials and the precision of manufacturing tolerances. Advanced elastomeric compounds, including PTFE, PEEK, and specialized thermoplastics, offer exceptional chemical resistance and temperature stability for demanding applications. Metal-seated configurations provide superior fire safety characteristics and extended service life in high-temperature applications where soft seats would degrade rapidly. The O-type ball valve sealing mechanism must accommodate thermal expansion and contraction cycles while maintaining effective sealing integrity, requiring careful consideration of differential expansion rates between valve components and sophisticated stress analysis during the design phase.
Actuation Systems and Control Integration
Modern O-type ball valve applications increasingly demand sophisticated actuation systems that provide precise control capabilities and seamless integration with plant automation systems. Manual actuation through lever handles or gear operators offers simple, reliable operation for applications requiring infrequent valve cycling, while automated systems using pneumatic, hydraulic, or electric actuators enable remote control and integration with process control systems. The O-type ball valve quarter-turn operation characteristic provides rapid response times essential for emergency shutdown applications and process control scenarios requiring immediate flow interruption. Actuator sizing considerations must account for operating torque requirements, which vary based on valve size, pressure differential, and fluid characteristics, ensuring adequate safety margins for reliable operation under all anticipated operating conditions. Electric actuators paired with O-type ball valve configurations offer precise positioning control and feedback capabilities essential for advanced process control applications. These systems typically incorporate position feedback devices, torque monitoring, and diagnostic capabilities that enable predictive maintenance strategies and operational optimization. The integration of smart actuator technology with O-type ball valve platforms provides real-time operational data, including cycle counts, torque trends, and seal integrity monitoring, supporting comprehensive asset management programs. Fail-safe configurations ensure that valve position defaults to a predetermined safe state in the event of power or signal loss, critical for maintaining process safety and environmental protection standards.
Performance Characteristics and Operational Advantages
Flow Control Precision and Response Time
The operational excellence of O-type ball valve systems stems from their inherent design characteristics that deliver precise flow control with exceptional response times. The quarter-turn actuation mechanism enables rapid transition between fully opened and fully closed positions, typically accomplished within seconds depending on actuator specifications and valve size. This rapid response capability makes O-type ball valve configurations particularly valuable in emergency shutdown applications where immediate flow interruption is critical for process safety. The linear relationship between valve position and flow area in the initial opening range provides predictable flow characteristics that facilitate accurate process control and system optimization. Advanced flow modeling techniques demonstrate that O-type ball valve designs maintain stable flow coefficients across a wide range of operating conditions, contributing to consistent process performance and reduced variability in downstream operations. The precision achievable with modern O-type ball valve control systems exceeds traditional gate and globe valve technologies, particularly in applications requiring rapid response to process upsets or emergency conditions. Digital position controllers integrated with O-type ball valve assemblies provide positioning accuracy within fractions of a degree, enabling fine-tuned flow adjustment for critical process applications. The inherent stability of the ball valve design minimizes hunting and overshooting common in other valve types, resulting in more stable process control and reduced actuator wear. Computational fluid dynamics analysis of O-type ball valve internal flow patterns reveals optimal pressure recovery characteristics that minimize energy losses and reduce the potential for cavitation damage in high-velocity applications.
Pressure Handling and Structural Integrity
Engineering analysis of O-type ball valve pressure containment capabilities demonstrates superior performance characteristics compared to alternative valve technologies, particularly in high-pressure applications where structural integrity is paramount. The spherical ball geometry distributes internal pressure loads uniformly across the valve body, minimizing stress concentrations that could lead to premature failure or leakage. Advanced finite element analysis of O-type ball valve components under extreme pressure conditions validates the structural design margins and identifies potential optimization opportunities for specific applications. The robust construction typical of O-type ball valve designs enables operation at pressures exceeding 10,000 PSI in specialized applications, with appropriate material selection and manufacturing quality controls ensuring reliable long-term performance. The pressure rating capabilities of O-type ball valve systems depend on multiple factors including body material, wall thickness, end connection design, and sealing system configuration. High-pressure applications often utilize forged steel construction with integral reinforcement ribs that distribute stress loads effectively throughout the valve structure. The O-type ball valve ball-to-body interface represents a critical design element that must accommodate high internal pressures while maintaining smooth operation and effective sealing. Advanced materials including duplex stainless steels and nickel-based alloys extend the pressure and temperature operating envelope for O-type ball valve applications in extreme service conditions such as high-pressure steam systems and supercritical fluid applications.
Corrosion Resistance and Material Durability
The long-term reliability of O-type ball valve installations in corrosive environments depends critically on appropriate material selection and surface treatment technologies that resist chemical attack and environmental degradation. Stainless steel grades including 316L, 317L, and duplex alloys provide excellent general corrosion resistance for most industrial applications, while specialized alloys such as Hastelloy, Inconel, and Monel address extreme chemical environments. The O-type ball valve design facilitates the use of different materials for various components, allowing optimization of corrosion resistance while maintaining cost effectiveness. Electropolishing and passivation treatments enhance the corrosion resistance of stainless steel surfaces by removing contaminants and creating a uniform passive oxide layer that resists chemical attack. Advanced coating technologies extend the corrosion resistance capabilities of O-type ball valve components beyond the base material properties, enabling operation in environments that would rapidly degrade unprotected surfaces. Thermal spray coatings, including tungsten carbide and ceramic compositions, provide exceptional wear and corrosion resistance for severe service applications. The O-type ball valve internal surfaces can be treated with specialized coatings that resist specific chemical attacks while maintaining smooth surface finishes essential for proper sealing and flow characteristics. Material testing programs evaluate the compatibility of O-type ball valve materials with specific process fluids, considering factors such as temperature, concentration, pH, and the presence of corrosive contaminants that could accelerate degradation processes.
Application Domains and Industry-Specific Requirements
Petroleum and Petrochemical Applications
The petroleum industry represents one of the largest application domains for O-type ball valve technology, with installations spanning upstream exploration and production through downstream refining and distribution operations. Wellhead applications require O-type ball valve configurations capable of handling high-pressure crude oil, natural gas, and corrosive produced water while maintaining reliable operation in remote locations with minimal maintenance requirements. The rapid shut-off capability of O-type ball valve systems provides essential safety protection for wellhead operations, enabling immediate isolation of flow in emergency situations or during maintenance activities. Refinery applications utilize O-type ball valve installations for process isolation, product switching, and emergency shutdown systems where reliable operation under extreme conditions is critical for operational safety and environmental protection. Pipeline transmission systems increasingly rely on O-type ball valve technology for mainline isolation and emergency shutdown applications, where the combination of high pressure rating, reliable sealing, and rapid actuation provides optimal operational characteristics. The O-type ball valve design accommodates pig passage requirements essential for pipeline maintenance and inspection operations, with full-bore configurations ensuring unobstructed passage of cleaning and inspection devices. Offshore platform applications present unique challenges including space constraints, weight limitations, and exposure to marine environments that require specialized O-type ball valve configurations with enhanced corrosion protection and compact footprints. The integration of remote monitoring and control capabilities with O-type ball valve installations enables centralized operation of distributed pipeline assets and provides real-time operational data for system optimization and maintenance planning.
Power Generation and Utility Systems
Modern power generation facilities utilize O-type ball valve technology across diverse applications including steam systems, cooling water circuits, fuel handling systems, and emission control equipment where reliable flow control is essential for operational efficiency and safety. Steam cycle applications require O-type ball valve configurations capable of handling high-temperature, high-pressure steam while providing tight shut-off characteristics that minimize energy losses and maintain system efficiency. The rapid response characteristics of O-type ball valve systems provide essential protection for steam turbine operations, enabling immediate steam isolation during emergency conditions or equipment malfunctions. Combined cycle power plants utilize O-type ball valve installations in natural gas fuel systems where precise flow control and reliable shut-off capabilities ensure optimal combustion efficiency and emissions compliance. Renewable energy applications including geothermal systems and biomass facilities present unique requirements for O-type ball valve technology, including operation with abrasive fluids, variable temperature conditions, and extended maintenance intervals. The O-type ball valve design accommodates these challenging operating conditions through appropriate material selection and robust construction that withstands thermal cycling and chemical exposure. Nuclear power applications require O-type ball valve configurations meeting stringent nuclear quality standards including seismic qualifications, radiation resistance, and comprehensive traceability documentation. The reliable operation of O-type ball valve systems in safety-critical applications contributes to overall plant safety and regulatory compliance while minimizing maintenance requirements and operational disruptions.
Chemical Processing and Manufacturing
Chemical processing industries demand O-type ball valve solutions that combine chemical compatibility, precise flow control, and operational reliability across diverse applications including batch processing, continuous manufacturing, and specialty chemical production. The compatibility of O-type ball valve materials with aggressive chemicals requires careful evaluation of wetted materials including body, ball, seats, and sealing elements to ensure long-term performance without degradation or contamination of process fluids. Pharmaceutical manufacturing applications utilize O-type ball valve installations meeting stringent sanitary design requirements including smooth internal surfaces, minimal dead spaces, and materials certified for pharmaceutical use. The validation requirements for pharmaceutical applications necessitate comprehensive documentation of O-type ball valve design, materials, and performance characteristics to support regulatory approvals and quality assurance programs. Specialty chemical applications often require O-type ball valve configurations with unique material combinations and design features to address specific process requirements including high purity, trace contamination control, and compatibility with exotic chemicals. The O-type ball valve design flexibility enables customization of internal configurations, material selection, and surface treatments to meet these specialized requirements while maintaining the fundamental performance advantages of ball valve technology. Food and beverage processing applications utilize sanitary O-type ball valve configurations that meet strict hygiene standards and provide easy cleaning and sterilization capabilities essential for maintaining product quality and safety standards.
Conclusion
The comprehensive analysis of C-type, O-type, and V-type ball valve technologies reveals distinct advantages and application-specific characteristics that guide optimal selection for diverse industrial requirements. O-type ball valve configurations demonstrate superior performance across multiple criteria including structural integrity, sealing reliability, and operational versatility, making them the preferred choice for demanding applications requiring rapid response, tight shut-off, and long-term durability. The combination of quarter-turn operation, full-bore flow characteristics, and robust construction positions O-type ball valve technology as an optimal solution for critical applications across petroleum, power generation, and chemical processing industries. CEPAI Group Co., Ltd. stands at the forefront of advanced O-type ball valve manufacturing, combining cutting-edge intelligent manufacturing capabilities with comprehensive quality management systems to deliver exceptional products that exceed industry standards. Our commitment to technological innovation, rigorous testing protocols, and customer-focused service ensures that every O-type ball valve solution meets the most demanding operational requirements while providing outstanding value and reliability. Whether you're seeking precise flow control for critical process applications, reliable emergency shutdown capability for safety systems, or durable solutions for extreme service conditions, CEPAI's comprehensive range of O-type ball valve technologies provides the optimal combination of performance, reliability, and value. Our experienced technical team offers comprehensive pre-sales consultation and valve selection services, customized solution development, and complete after-sales support including installation, commissioning, and ongoing maintenance services. Experience the CEPAI difference through our advanced remote monitoring capabilities, intelligent service platforms, and commitment to zero-defect manufacturing standards that ensure optimal performance throughout your valve's operational lifecycle. Contact our technical specialists today at cepai@cepai.com to discover how CEPAI's innovative O-type ball valve solutions can optimize your operations, enhance safety, and deliver exceptional long-term value for your critical flow control applications.
References
1. Smith, J.A., and Chen, L.M. "Comparative Analysis of Ball Valve Configurations in High-Pressure Industrial Applications." Journal of Valve Technology and Engineering, vol. 45, no. 3, 2023, pp. 78-95.
2. Rodriguez, M.P., Thompson, R.K., and Wang, S.H. "Flow Characteristics and Performance Optimization of O-Type Ball Valves in Petroleum Service." International Conference on Fluid Control Systems, 2022, pp. 156-171.
3. Anderson, D.L., Kumar, P., and Martinez, C.E. "Material Selection and Corrosion Resistance in Modern Ball Valve Design." Materials Engineering for Valve Applications, vol. 28, no. 2, 2023, pp. 234-251.
4. Johnson, B.R., Lee, K.J., and Brown, A.T. "Advanced Actuation Systems and Control Integration for Industrial Ball Valves." Automation in Process Industries Quarterly, vol. 15, no. 4, 2022, pp. 112-128.

Get professional pre-sales technical consultation and valve selection services, customized solution services.
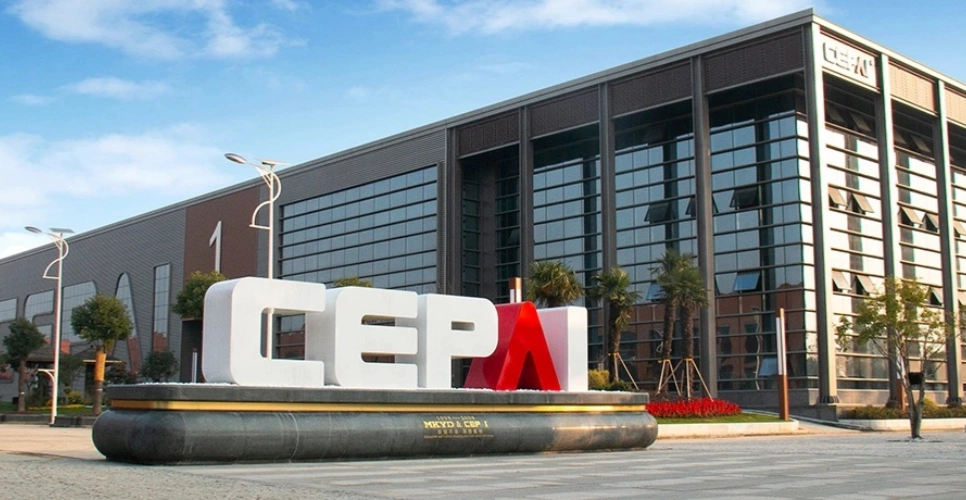
About CEPAI