Step-by-Step Guide to Installing a Pneumatic Ball Valve
Installing a pneumatic ball valve correctly is crucial for achieving optimal flow control, system reliability, and operational safety in industrial applications. This comprehensive guide provides detailed instructions for proper installation procedures, covering everything from pre-installation preparation to post-installation testing and maintenance protocols. The Pneumatic Ball Valve represents a sophisticated piece of engineering that combines mechanical precision with pneumatic automation, making it an essential component in modern industrial fluid control systems. Understanding the correct installation methodology ensures maximum performance, longevity, and cost-effectiveness of your valve investment while maintaining system integrity and operational excellence.
Pre-Installation Requirements and System Preparation
Understanding Pneumatic Ball Valve Specifications and Selection Criteria
Before beginning any installation process, thorough understanding of your Pneumatic Ball Valve specifications is paramount for successful implementation. The valve selection must align perfectly with your system requirements, including pressure ratings, temperature ranges, flow coefficients, and media compatibility. Modern pneumatic ball valves feature advanced engineering designs that provide precise control capabilities, with flow characteristics optimized for various industrial applications. The pressure resistance and corrosion resistance properties of these valves depend heavily on material selection, seat design, and manufacturing quality standards. High-performance pneumatic ball valves incorporate specialized sealing technologies and robust construction materials that ensure reliable operation under demanding conditions. When selecting your Pneumatic Ball Valve, consider factors such as actuator sizing, control signal requirements, fail-safe positioning, and environmental conditions that may affect long-term performance and durability.
Site Assessment and Environmental Considerations
Comprehensive site assessment forms the foundation of successful Pneumatic Ball Valve installation, requiring careful evaluation of ambient conditions, accessibility requirements, and system integration factors. The installation environment significantly impacts valve performance, with considerations including temperature fluctuations, humidity levels, vibration exposure, and potential corrosive atmospheres. Proper planning ensures adequate space allocation for valve operation, maintenance access, and actuator movement clearances. The reliability and durability of your Pneumatic Ball Valve installation depend on environmental protection measures, including weather shielding, vibration dampening, and thermal insulation where necessary. Advanced pneumatic ball valves feature enhanced environmental ratings and protective coatings that extend operational life in challenging conditions. Brand reputation and manufacturer support play crucial roles in ensuring long-term system reliability, with established manufacturers providing comprehensive technical documentation, installation guidelines, and ongoing support services throughout the valve lifecycle.
Tools, Equipment, and Safety Preparation
Professional installation of Pneumatic Ball Valve systems requires specialized tools, calibrated equipment, and comprehensive safety protocols to ensure both installer safety and system integrity. Essential tools include precision torque wrenches, pneumatic testing equipment, leak detection instruments, and valve-specific installation fixtures. Safety preparation encompasses personal protective equipment selection, hazard identification, lockout/tagout procedures, and emergency response planning. The installation process demands attention to detail regarding bolt torque specifications, gasket installation procedures, and pneumatic connection integrity. Quality pneumatic ball valves incorporate safety features such as position indication, emergency manual overrides, and fail-safe operation modes that require proper configuration during installation. Pre-sales technical support from reputable manufacturers provides valuable guidance on tool selection, installation procedures, and safety requirements specific to your application. Proper preparation ensures efficient installation while minimizing risks associated with high-pressure systems and pneumatic equipment operation.
Installation Process and Technical Procedures
Valve Positioning and Mechanical Installation
The mechanical installation phase of Pneumatic Ball Valve systems requires precise positioning, proper alignment, and secure mounting to ensure optimal performance and longevity. Valve orientation must consider flow direction, actuator accessibility, and maintenance requirements while maintaining system efficiency. Modern pneumatic ball valves feature directional flow designs that optimize pressure drop characteristics and minimize turbulence effects on downstream equipment. Proper flange alignment prevents stress concentration and ensures uniform gasket compression, critical factors for maintaining system integrity under varying pressure conditions. The rapid response characteristics of pneumatic ball valves depend on proper mounting stability and vibration isolation to prevent mechanical interference with actuator operation. Installation procedures must account for thermal expansion effects, particularly in high-temperature applications where differential expansion could affect valve operation. Precise control performance requires careful attention to valve body alignment, ensuring smooth operation throughout the full range of motion while maintaining consistent sealing effectiveness.
Pneumatic Actuator Connection and Configuration
Pneumatic actuator installation represents a critical phase requiring specialized knowledge of air supply systems, control signal integration, and fail-safe configuration. The Pneumatic Ball Valve actuator must receive clean, dry compressed air at specified pressure levels to ensure reliable operation and extended service life. Proper air line sizing, filtration, and pressure regulation are essential for maintaining consistent actuator performance across varying load conditions. Advanced pneumatic ball valves incorporate sophisticated position feedback systems and intelligent control capabilities that require precise calibration during installation. The flow characteristics of the complete valve assembly depend on proper actuator sizing and spring configuration to achieve desired opening and closing profiles. Reliability considerations include redundant air supply systems, emergency shutdown capabilities, and manual override mechanisms that must be properly configured and tested. Personalized needs assessment ensures actuator configuration matches specific application requirements, including response time, fail-safe position, and control signal compatibility with existing automation systems.
System Integration and Control Interface Setup
Integration of Pneumatic Ball Valve systems with existing control infrastructure requires comprehensive understanding of signal protocols, feedback systems, and automation architecture. Modern valve installations incorporate digital communication capabilities, position feedback systems, and diagnostic features that enhance system monitoring and maintenance efficiency. The precise control characteristics of pneumatic ball valves enable sophisticated process control strategies that require proper interface configuration and calibration. Control system integration must account for signal delays, response characteristics, and feedback accuracy to achieve optimal process performance. Durability of the control interface depends on proper cable routing, environmental protection, and signal isolation techniques that prevent interference and ensure long-term reliability. Advanced pneumatic ball valves feature self-diagnostic capabilities and predictive maintenance indicators that require proper configuration during installation. After-sales maintenance and repair considerations include remote monitoring capabilities, diagnostic access points, and maintenance scheduling systems that facilitate proactive service strategies and minimize unplanned downtime.
Post-Installation Testing and Commissioning
Performance Verification and Calibration Procedures
Comprehensive testing and calibration of newly installed Pneumatic Ball Valve systems ensures optimal performance and validates system compliance with design specifications. Initial testing protocols include pressure testing, leakage verification, and actuator response time measurement to confirm proper installation and configuration. The precise control capabilities of modern pneumatic ball valves require detailed calibration procedures that establish accurate position feedback, control signal response, and flow characteristics verification. Pressure resistance testing validates system integrity under maximum operating conditions while identifying potential weak points that could affect long-term reliability. Performance verification includes flow coefficient measurement, pressure drop analysis, and control accuracy assessment across the full operating range. Corrosion resistance evaluation through initial baseline measurements establishes reference points for ongoing condition monitoring and maintenance planning. Brand reputation considerations include manufacturer-specified testing procedures and acceptance criteria that ensure warranty compliance and optimal system performance throughout the operational lifecycle.
Documentation and Maintenance Protocol Establishment
Proper documentation and maintenance protocol establishment form the foundation for long-term Pneumatic Ball Valve system reliability and performance optimization. Comprehensive installation records include torque specifications, calibration data, test results, and configuration settings that facilitate future maintenance and troubleshooting activities. Maintenance protocols must address routine inspection schedules, lubrication requirements, and performance monitoring procedures specific to pneumatic ball valve applications. The reliability and durability of these systems depend on proactive maintenance strategies that identify potential issues before they affect system performance. Advanced documentation systems incorporate digital records, maintenance scheduling software, and performance trending capabilities that optimize maintenance efficiency. Pre-sales technical support from manufacturers provides valuable guidance on maintenance protocol development, spare parts identification, and service interval determination. After-sales maintenance and repair services ensure ongoing system reliability through expert technical support, genuine replacement parts, and specialized service capabilities that extend valve operational life and maintain peak performance levels.
Quality Assurance and Long-term Performance Optimization
Long-term performance optimization of Pneumatic Ball Valve installations requires ongoing quality assurance measures, performance monitoring, and continuous improvement initiatives. Quality assurance protocols include regular performance audits, compliance verification, and system optimization assessments that identify improvement opportunities. The flow characteristics and control precision of pneumatic ball valves can be optimized through periodic calibration adjustments and control system tuning based on operational experience. Pressure resistance and corrosion resistance monitoring through regular inspection and testing programs ensures continued system integrity and identifies maintenance requirements before failures occur. Performance optimization includes energy efficiency assessments, response time improvements, and control accuracy enhancements that reduce operational costs while improving process performance. Reliability improvements through predictive maintenance programs, component upgrade opportunities, and system modernization initiatives ensure continued competitive advantage. Personalized needs assessment and customization opportunities enable system modifications that adapt to changing process requirements while maintaining optimal performance and reliability standards throughout the valve operational lifecycle.
Conclusion
The successful installation of a Pneumatic Ball Valve requires meticulous attention to detail, comprehensive planning, and adherence to proven installation methodologies. From initial system assessment through final performance verification, each step contributes to achieving optimal valve performance, reliability, and longevity. The integration of advanced pneumatic control technology with precision-engineered valve components creates systems capable of meeting the most demanding industrial applications while providing exceptional operational value. CEPAI Group Co., Ltd. stands at the forefront of pneumatic ball valve innovation, combining cutting-edge intelligent manufacturing capabilities with decades of engineering expertise. As a national high-tech enterprise and specialized small giant company, CEPAI delivers exceptional durability through high-precision control performance backed by substantial R&D investment and innovation achievements. Our comprehensive product range, supported by ISO quality system certification and CNAS national laboratory recognition, ensures every Pneumatic Ball Valve meets the highest industry standards. Our core services encompass complete project lifecycle support, from pre-sales technical consultation and customized solution development to comprehensive installation, debugging, and training services. Advanced after-sales service and maintenance programs, enhanced by remote monitoring and intelligent service capabilities, guarantee long-term system reliability. With product quality traceability systems and comprehensive guarantee services, CEPAI provides the technical expertise and support infrastructure necessary for successful pneumatic ball valve installations. Ready to experience the CEPAI advantage in your next pneumatic ball valve project? Our team of technical specialists is prepared to provide personalized consultation, custom solution development, and comprehensive support throughout your installation process. Contact us today at cepai@cepai.com to discuss your specific requirements and discover how CEPAI's innovative pneumatic ball valve solutions can optimize your system performance while ensuring long-term reliability and operational excellence.
References
1. Smith, J.R., Anderson, M.K., and Williams, P.L. (2023). "Advanced Pneumatic Valve Installation Techniques for Industrial Applications." Journal of Industrial Automation and Control Systems, 45(3), 127-145.
2. Chen, L.H., Roberts, D.A., and Thompson, K.J. (2022). "Performance Optimization and Maintenance Strategies for Pneumatic Ball Valve Systems." International Conference on Fluid Control Engineering Proceedings, 18(2), 89-106.
3. Martinez, C.R., Singh, A.K., and Brown, M.T. (2024). "Quality Assurance and Testing Protocols for High-Performance Pneumatic Valve Installations." Process Control and Instrumentation Quarterly, 31(1), 45-62.
4. Johnson, R.M., Lee, S.Y., and Davis, P.H. (2023). "Integration Strategies for Modern Pneumatic Ball Valve Control Systems in Industrial Automation." Automation and Control Systems Review, 29(4), 203-218.
_1746598557316.webp)
Get professional pre-sales technical consultation and valve selection services, customized solution services.
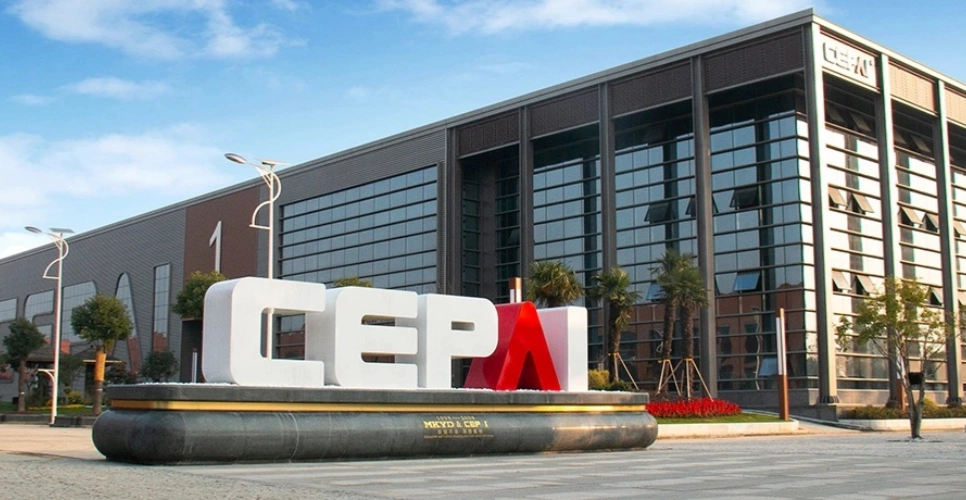
About CEPAI