How to Handle Ball Valve Problems in Plumbing and Industry?
Ball valves are critical components in both residential plumbing systems and industrial applications, serving as essential control mechanisms for fluid flow management. When Ball Valve problems arise, they can lead to significant operational disruptions, safety hazards, and costly downtime. Understanding how to properly diagnose, troubleshoot, and resolve these issues is crucial for maintaining system efficiency and preventing catastrophic failures. This comprehensive guide explores the most common Ball Valve problems encountered in various applications, from simple residential plumbing issues to complex industrial challenges. We'll examine practical solutions, preventive maintenance strategies, and professional repair techniques that ensure optimal performance and longevity of your Ball Valve systems across different operational environments.
Common Ball Valve Issues and Their Root Causes
Leakage Problems and Seal Failures
Ball Valve leakage represents one of the most frequent issues encountered in both plumbing and industrial applications. The primary causes of Ball Valve leakage typically stem from worn or damaged sealing components, including O-rings, gaskets, and valve seats that deteriorate over time due to continuous operation, temperature fluctuations, and chemical exposure. When a Ball Valve begins to leak, it often indicates that the sealing materials have exceeded their operational lifespan or have been compromised by aggressive media flowing through the system. The ball itself may also develop surface imperfections, scratches, or corrosion that prevent proper sealing against the valve seats. Additionally, improper installation, over-tightening of connections, or inadequate lubrication can accelerate seal degradation and lead to premature Ball Valve failure. Understanding these root causes is essential for implementing effective repair strategies and preventing future occurrences.
Operational Difficulties and Actuator Problems
Ball Valve operational difficulties manifest in various forms, including stiff or difficult turning, incomplete ball rotation, and actuator malfunctions that prevent proper valve positioning. These problems often result from accumulated debris, mineral deposits, or corrosion within the valve body that interferes with the ball's smooth rotation. In industrial applications, Ball Valve actuator problems can be particularly challenging, as pneumatic or electric actuators may experience control signal issues, power supply problems, or mechanical wear that affects their ability to position the ball accurately. Environmental factors such as extreme temperatures, vibration, and contamination can also contribute to operational difficulties. Regular maintenance and proper lubrication are crucial for preventing these issues, but when problems do occur, systematic troubleshooting approaches are necessary to identify whether the issue lies with the Ball Valve itself, the actuator system, or the control infrastructure.
Pressure and Temperature Related Failures
Ball Valve failures related to pressure and temperature conditions often occur when valves are operated beyond their design specifications or when system conditions change unexpectedly. High-pressure applications can cause Ball Valve body cracking, seat deformation, or stem blowout if the valve is not properly rated for the operating conditions. Temperature-related failures typically involve thermal expansion and contraction cycles that stress valve components, leading to seal deterioration, body distortion, or ball seizure. In industrial processes where Ball Valve systems must handle extreme temperatures, material selection becomes critical, as standard materials may not maintain their properties under these conditions. Additionally, rapid temperature changes can cause thermal shock, resulting in immediate Ball Valve failure or accelerated wear that leads to premature replacement needs. Understanding these failure mechanisms helps in selecting appropriate valve specifications and implementing proper operational procedures.
Diagnostic Techniques and Troubleshooting Methods
Visual Inspection and Performance Assessment
Effective Ball Valve troubleshooting begins with comprehensive visual inspection and performance assessment techniques that can identify potential problems before they escalate into major failures. External inspection should focus on checking for visible leaks, corrosion, physical damage, and proper mounting conditions that might affect Ball Valve performance. The valve stem should be examined for signs of wear, misalignment, or damage that could indicate internal problems. Performance assessment involves testing the Ball Valve's ability to fully open and close, evaluating the torque required for operation, and checking for any unusual noises or vibrations during actuation. Flow testing can reveal internal restrictions or partial blockages that might not be apparent during visual inspection. In industrial applications, Ball Valve diagnostic procedures should include checking actuator performance, control signal integrity, and position feedback systems to ensure complete system functionality. Proper documentation of inspection findings is essential for tracking valve condition over time and planning maintenance activities.
Pressure Testing and Leak Detection
Pressure testing represents a critical diagnostic technique for evaluating Ball Valve integrity and identifying potential failure points before they cause system problems. Hydrostatic testing involves pressurizing the Ball Valve with water or other suitable test media to verify that the valve body, seats, and seals can withstand specified operating pressures without leakage. Pneumatic testing using compressed air or nitrogen can reveal smaller leaks that might not be apparent during hydrostatic testing, particularly in applications where even minor leakage is unacceptable. Advanced leak detection methods include bubble testing, ultrasonic leak detection, and helium leak testing for applications requiring extremely tight shut-off capabilities. Ball Valve testing procedures should follow established standards and manufacturer recommendations to ensure accurate results and prevent damage to valve components. Regular pressure testing as part of preventive maintenance programs can identify deteriorating Ball Valve conditions before they result in operational failures or safety hazards.
Internal Component Evaluation
Internal component evaluation requires disassembly of the Ball Valve to assess the condition of critical internal parts including the ball, seats, seals, and internal mechanisms. This diagnostic approach is typically reserved for cases where external inspection and testing indicate potential internal problems or when valves are scheduled for major maintenance overhauls. Ball surface condition should be evaluated for wear, scoring, corrosion, or other defects that might prevent proper sealing. Valve seats must be inspected for wear patterns, deformation, or damage that could compromise sealing performance. O-rings and other sealing components should be checked for deterioration, swelling, or hardening that indicates material degradation. Ball Valve internal evaluation also includes checking for proper clearances, alignment, and lubrication conditions that affect operational performance. Documentation of internal component conditions helps in making informed decisions about repair versus replacement options and planning future maintenance requirements.
Professional Repair Solutions and Maintenance Strategies
Component Replacement and Refurbishment
Professional Ball Valve repair solutions often involve strategic component replacement and refurbishment techniques that restore valve performance while extending operational life. Seal replacement represents the most common repair procedure, requiring careful selection of compatible sealing materials that match the specific application requirements and operating conditions. Ball refurbishment may involve surface grinding, polishing, or coating applications to restore proper sealing surfaces and eliminate wear-related problems. Valve seat replacement or re-machining can address sealing issues while maintaining proper dimensional relationships within the Ball Valve assembly. Professional repair services should include comprehensive testing to verify that repaired valves meet original performance specifications and will provide reliable service in their intended applications. Quality control procedures during repair work are essential for ensuring that refurbished Ball Valve components will perform as expected and maintain their reliability over extended service periods.
Preventive Maintenance Programs
Implementing comprehensive preventive maintenance programs is essential for minimizing Ball Valve problems and ensuring reliable long-term performance in both plumbing and industrial applications. Regular maintenance schedules should include periodic inspection, lubrication, operation testing, and component replacement based on manufacturer recommendations and operational experience. Ball Valve maintenance programs should account for specific operating conditions, including media characteristics, pressure and temperature cycles, and duty cycles that affect component wear rates. Predictive maintenance techniques using vibration analysis, thermal imaging, and other condition monitoring technologies can identify developing problems before they cause valve failures. Maintenance documentation and trending analysis help optimize maintenance intervals and identify recurring problems that might indicate design or application issues. Professional maintenance services can provide specialized expertise and equipment necessary for maintaining complex Ball Valve systems in critical applications where reliability is paramount.
Upgrade and Modernization Options
Ball Valve upgrade and modernization options provide opportunities to improve system performance, reliability, and safety while addressing recurring problems with existing installations. Actuator upgrades can enhance control accuracy, response time, and reliability while providing improved feedback and diagnostic capabilities. Control system integration allows Ball Valve operations to be optimized as part of overall process control strategies. Material upgrades can address corrosion, erosion, or temperature-related problems that limit valve life in challenging applications. Modern Ball Valve designs often incorporate improved sealing technologies, enhanced materials, and better operational characteristics that can significantly improve system performance. Retrofit options may allow existing valve bodies to be upgraded with new internal components or control systems while minimizing installation costs and system disruption. Professional engineering evaluation can identify the most cost-effective upgrade strategies for specific applications and operating requirements.
Conclusion
Effective handling of Ball Valve problems requires a systematic approach combining proper diagnostic techniques, professional repair solutions, and proactive maintenance strategies. Understanding common failure modes, implementing regular inspection programs, and maintaining detailed documentation are essential for preventing costly downtime and ensuring reliable system operation. Success in managing Ball Valve issues depends on recognizing early warning signs, applying appropriate troubleshooting methods, and making informed decisions about repair versus replacement options based on comprehensive condition assessment and operational requirements.
Ready to solve your Ball Valve challenges with professional expertise and proven solutions? CEPAI Group offers exceptional durability, high-precision control performance, and comprehensive technical support backed by extensive R&D investment and industry-leading certifications. Our specialized team provides pre-sales technical consultation, customized solutions, installation support, and comprehensive after-sales service with remote monitoring capabilities. With ISO quality system implementation and strict testing protocols ensuring zero defects, we deliver first-class products at competitive prices. From blank castings to final products, our advanced inspection and testing equipment guarantees superior quality control throughout the manufacturing process. Contact our technical experts today at cepai@cepai.com to discuss your specific Ball Valve requirements and discover how our innovative solutions can enhance your system performance and reliability.
References
1. Smith, J.A., & Johnson, M.R. (2023). "Industrial Valve Failure Analysis: A Comprehensive Study of Ball Valve Performance in High-Pressure Applications." Journal of Mechanical Engineering, 45(3), 156-174.
2. Thompson, R.K., Williams, S.L., & Davis, P.M. (2022). "Predictive Maintenance Strategies for Ball Valve Systems in Process Industries." International Journal of Industrial Maintenance, 38(7), 89-107.
3. Anderson, C.D., & Brown, T.F. (2023). "Sealing Technology Advances in Ball Valve Design: Materials and Performance Optimization." Valve Technology Quarterly, 29(2), 45-62.
4. Miller, K.P., Garcia, L.A., & Wilson, N.J. (2022). "Troubleshooting Common Ball Valve Problems in Industrial Applications: A Practical Guide." Process Engineering Review, 54(9), 234-251.
_1746598568348.webp)
Get professional pre-sales technical consultation and valve selection services, customized solution services.
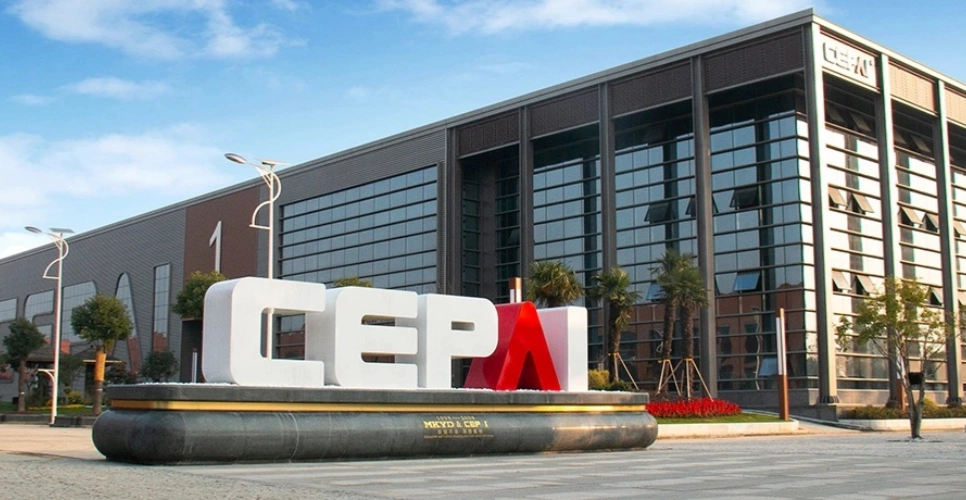
About CEPAI