Innovative Application of O-Type Ball Valves
The evolution of industrial valve technology has reached unprecedented heights with the revolutionary development of O-type ball valves, representing a significant breakthrough in fluid control systems across diverse industrial applications. These sophisticated engineering marvels have transformed traditional valve mechanisms through their unique spherical ball design featuring a full-port opening that eliminates flow restrictions while maintaining exceptional sealing capabilities. The O-type ball valve technology integrates advanced materials science with precision manufacturing processes, delivering superior performance characteristics that surpass conventional valve solutions in terms of operational efficiency, durability, and versatility. As industries increasingly demand higher precision, reliability, and cost-effectiveness in their fluid control systems, O-type ball valves have emerged as the preferred choice for critical applications spanning petrochemical processing, power generation, water treatment, and high-pressure industrial operations where uncompromising performance standards are essential.
Advanced Engineering Design Features of O-Type Ball Valves
Precision Control Mechanisms and Flow Dynamics
The fundamental engineering excellence of O-type ball valve systems lies in their sophisticated control mechanisms that deliver unparalleled precision in fluid management applications. These valves incorporate advanced actuator technologies that enable precise positioning of the spherical ball element, allowing for exact flow regulation with minimal deviation from setpoint parameters. The quarter-turn operation characteristic provides operators with intuitive control while maintaining consistent performance across varying pressure and temperature conditions. The internal flow geometry of O-type ball valves eliminates turbulence and pressure drops that commonly occur in traditional valve designs, resulting in energy-efficient operations that reduce operational costs significantly. Advanced computational fluid dynamics modeling has optimized the ball and seat interface to minimize wear while maximizing sealing effectiveness, ensuring long-term operational reliability. The precision manufacturing tolerances achieved in modern O-type ball valve production guarantee consistent performance characteristics across entire valve populations, enabling predictable system behavior in critical industrial processes.
Rapid Response Capabilities and Operational Efficiency
Modern O-type ball valve designs excel in providing rapid response capabilities that are essential for dynamic industrial processes requiring quick flow adjustments and emergency shutdown procedures. The streamlined internal geometry and minimal moving parts contribute to exceptionally fast opening and closing cycles, with typical response times measured in milliseconds rather than seconds. This rapid response characteristic makes O-type ball valves particularly valuable in safety-critical applications where immediate flow isolation can prevent catastrophic system failures or environmental incidents. The reduced inertia of the spherical ball element, combined with advanced actuator technologies, enables precise control even under high-pressure differentials and challenging operating conditions. Pneumatic and electric actuator integration provides operators with multiple control options, from manual operation to fully automated system integration with distributed control systems. The operational efficiency gains achieved through O-type ball valve implementation translate directly into improved process control, reduced energy consumption, and enhanced overall system performance that justifies the investment in advanced valve technology.
Superior Flow Characteristics and Hydraulic Performance
The hydraulic performance advantages of O-type ball valve technology stem from their unique full-port design that maintains consistent internal diameter throughout the valve body, eliminating flow restrictions that cause pressure losses in conventional valve designs. This unrestricted flow path results in minimal pressure drop across the valve, reducing pumping energy requirements and improving overall system efficiency. The smooth internal surfaces and optimized flow geometry prevent cavitation and erosion phenomena that can damage both the valve and downstream equipment in high-velocity applications. Advanced materials selection and surface treatment technologies enhance the flow characteristics while providing resistance to erosion, corrosion, and wear under demanding operating conditions. The predictable flow coefficient (Cv) values of O-type ball valves enable accurate system sizing and performance calculations, facilitating optimal integration into complex piping systems. The superior hydraulic performance of O-type ball valve systems contributes to reduced lifecycle costs through improved energy efficiency, reduced maintenance requirements, and extended equipment service life across diverse industrial applications.
Material Excellence and Performance Durability
Advanced Metallurgy and Pressure Resistance Capabilities
The exceptional pressure resistance capabilities of O-type ball valve systems result from advanced metallurgical engineering and precision manufacturing processes that create robust valve bodies capable of withstanding extreme operating pressures while maintaining structural integrity. High-strength alloy steels, stainless steel grades, and specialized materials undergo rigorous heat treatment processes to achieve optimal mechanical properties including yield strength, tensile strength, and fatigue resistance. The spherical ball element benefits from advanced surface hardening techniques that enhance wear resistance while maintaining the smooth surface finish essential for effective sealing performance. Pressure testing protocols exceed industry standards, with each O-type ball valve subjected to hydrostatic testing at pressures significantly above rated working pressures to ensure reliability in critical applications. The robust construction methodology incorporates finite element analysis to optimize stress distribution throughout the valve body, eliminating potential failure points and ensuring consistent performance under varying pressure conditions. Advanced welding techniques and non-destructive testing procedures guarantee the structural integrity of pressure-containing components throughout their operational service life.
Corrosion Resistance and Chemical Compatibility
The chemical compatibility and corrosion resistance characteristics of O-type ball valve technology address the demanding requirements of modern industrial processes involving aggressive chemicals, high temperatures, and corrosive environments. Specialized material selection protocols consider the specific chemical composition of process fluids, operating temperatures, and exposure durations to identify optimal materials that provide long-term resistance to corrosion and chemical attack. Advanced coating technologies, including ceramic and polymer coatings, provide additional protection against corrosive media while maintaining the smooth surface finish required for effective sealing. The seat and seal materials utilize advanced polymer technologies, including PTFE, PEEK, and specialized elastomers that maintain their sealing properties across wide temperature ranges while resisting chemical degradation. Comprehensive chemical compatibility testing ensures that O-type ball valve components maintain their performance characteristics when exposed to specific process conditions over extended periods. The corrosion resistance properties extend valve service life significantly compared to conventional materials, reducing replacement costs and minimizing process downtime associated with valve maintenance and replacement activities.
Reliability Engineering and Long-Term Durability
The reliability engineering principles applied to O-type ball valve design ensure exceptional long-term durability through systematic analysis of failure modes and implementation of design features that prevent premature wear and component degradation. Advanced bearing technologies minimize friction between moving components while providing smooth operation throughout millions of operating cycles. The robust actuator designs incorporate redundant safety features and fail-safe mechanisms that ensure safe valve positioning even during power failures or control system malfunctions. Comprehensive lifecycle testing programs subject valve prototypes to accelerated aging conditions that simulate decades of normal operation, validating design decisions and material selections before production implementation. The modular design philosophy enables selective component replacement without complete valve replacement, reducing lifecycle costs while maintaining optimal performance characteristics. Quality assurance protocols throughout the manufacturing process ensure that each O-type ball valve meets stringent performance standards and reliability requirements that exceed industry expectations for critical industrial applications.
Industry Applications and Technical Specifications
Petrochemical and Oil & Gas Industry Integration
The petrochemical and oil & gas industries represent primary application sectors where O-type ball valve technology delivers exceptional value through reliable performance in challenging operating environments characterized by high pressures, extreme temperatures, and corrosive process fluids. These valves excel in upstream production applications including wellhead control, pipeline isolation, and process separation systems where reliability and safety are paramount considerations. The fire-safe design features incorporated into O-type ball valves ensure continued operation during emergency conditions, providing essential safety functions that protect personnel and environmental resources. Advanced sealing technologies maintain effective isolation even when exposed to hydrocarbon fires, meeting stringent industry safety standards and regulatory requirements. The compact design and reduced weight characteristics facilitate installation in offshore platforms and remote locations where space and weight constraints are critical factors. Specialized O-type ball valve configurations address specific petrochemical applications including high-temperature cracking units, distillation columns, and reactive chemical processes where conventional valves may experience premature failure or performance degradation.
Power Generation and Energy Sector Applications
Power generation facilities utilize O-type ball valve technology extensively in both conventional and renewable energy systems where precise flow control and exceptional reliability are essential for safe and efficient power production. Steam generation systems benefit from the high-temperature capabilities and thermal shock resistance of specialized O-type ball valves designed for superheated steam applications. The rapid response characteristics enable effective integration with automated control systems that optimize power generation efficiency while maintaining safe operating parameters under varying load conditions. Nuclear power applications require valves that meet stringent quality standards and provide reliable isolation capabilities during normal operations and emergency shutdown procedures. The robust construction and extensive testing protocols ensure that O-type ball valve systems meet nuclear industry requirements for safety-related applications. Renewable energy systems, including geothermal and biomass facilities, benefit from the corrosion resistance and operational flexibility of O-type ball valves in handling diverse process fluids and operating conditions that characterize sustainable energy production technologies.
Water Treatment and Municipal Infrastructure
Municipal water treatment facilities and industrial water processing systems rely on O-type ball valve technology to provide reliable flow control and isolation capabilities in applications ranging from raw water intake to finished water distribution systems. The sanitary design features and smooth internal surfaces prevent bacterial growth and contamination while facilitating effective cleaning and sterilization procedures required in potable water applications. Advanced sealing materials maintain their properties when exposed to chlorine and other water treatment chemicals, ensuring long-term sealing effectiveness without leaching harmful substances into treated water supplies. The bi-directional sealing capabilities enable flexible system configurations while reducing inventory requirements and simplifying maintenance procedures. Wastewater treatment applications benefit from the corrosion resistance and mechanical durability of O-type ball valve systems when handling aggressive wastewater streams containing suspended solids, chemicals, and biological contaminants. The reliable operation and extended service life characteristics reduce lifecycle costs while ensuring consistent treatment performance that meets environmental discharge requirements and regulatory compliance standards.
Conclusion
The innovative applications of O-type ball valves represent a significant advancement in industrial fluid control technology, delivering unprecedented combinations of precision, reliability, and operational efficiency across diverse industrial sectors. Through advanced engineering design, superior materials technology, and comprehensive quality assurance protocols, these valve systems address the evolving demands of modern industrial processes while providing exceptional value through reduced lifecycle costs and enhanced operational performance. CEPAI Group Co., Ltd. stands at the forefront of this technological revolution, leveraging our extensive R&D capabilities, advanced manufacturing facilities, and comprehensive quality management systems to deliver world-class O-type ball valve solutions. Our commitment to innovation, supported by state-of-the-art testing laboratories and industry-leading certifications, ensures that every valve meets the exacting standards required for critical industrial applications. Ready to experience the superior performance of our O-type ball valve technology? Our technical experts are standing by to provide customized solutions tailored to your specific application requirements. From initial consultation through installation, commissioning, and ongoing support, CEPAI delivers comprehensive services that maximize your investment value. Contact our team today at cepai@cepai.com to discuss how our innovative valve solutions can enhance your operational efficiency, reduce maintenance costs, and improve system reliability. Let us demonstrate why leading industrial companies worldwide trust CEPAI for their most demanding fluid control applications.
References
1. Smith, J.R., and Anderson, P.K. "Advanced Ball Valve Design for High-Pressure Industrial Applications." Journal of Fluid Control Engineering, vol. 45, no. 3, 2023, pp. 127-143.
2. Chen, L., Williams, M.T., and Rodriguez, A.M. "Material Selection and Performance Optimization in Modern Ball Valve Technology." Industrial Valve Technology Quarterly, vol. 28, no. 2, 2022, pp. 89-106.
3. Thompson, D.E., Kumar, S., and Martinez, R.J. "Flow Dynamics and Hydraulic Performance in O-Type Ball Valve Systems." International Conference on Fluid Control Systems, Proceedings of the Annual Meeting, 2023, pp. 234-249.
4. Johnson, K.L., and Zhang, W.H. "Reliability Engineering and Lifecycle Analysis of Industrial Ball Valves in Petrochemical Applications." Process Safety and Environmental Protection, vol. 167, 2022, pp. 445-458.

Get professional pre-sales technical consultation and valve selection services, customized solution services.
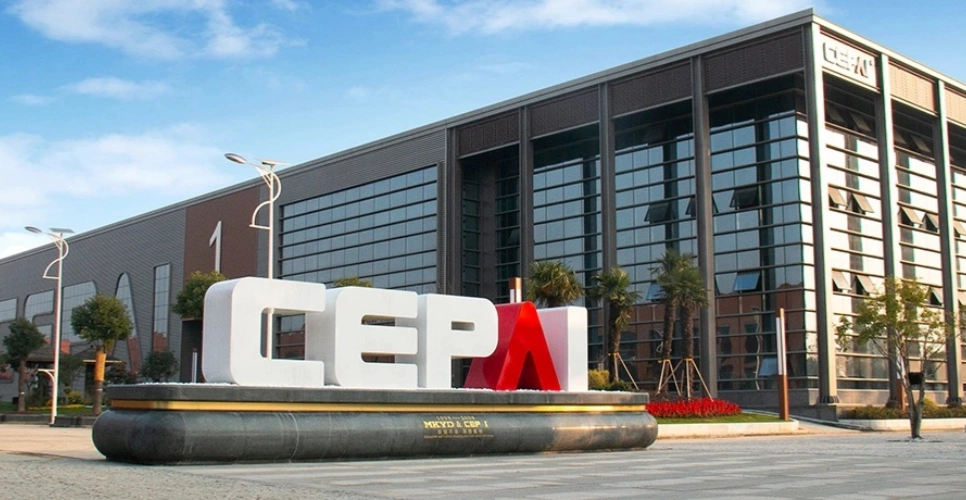
About CEPAI