How to Detect Air Leaks in Pneumatic Ball Valve Systems?
Air leaks in pneumatic ball valve systems represent one of the most critical maintenance challenges in industrial automation, directly impacting operational efficiency, energy consumption, and system reliability. Detecting these leaks requires a systematic approach combining advanced diagnostic techniques, specialized equipment, and comprehensive understanding of pneumatic system behavior. Pneumatic Ball Valve systems are particularly susceptible to air leakage due to their complex sealing mechanisms, actuator interfaces, and connection points. Early detection not only prevents catastrophic system failures but also ensures optimal performance, reduces energy costs, and extends equipment lifespan. This comprehensive guide explores proven methodologies, cutting-edge technologies, and industry best practices for identifying and addressing air leaks in pneumatic ball valve applications across various industrial sectors.
Visual and Auditory Detection Methods for Pneumatic Ball Valve Systems
Systematic Visual Inspection Techniques
Visual inspection remains the foundation of effective leak detection in Pneumatic Ball Valve systems, requiring trained personnel to identify subtle indicators of air leakage that may not be immediately apparent. Professional technicians develop expertise in recognizing visual cues such as dust accumulation patterns around valve connections, discoloration of sealing surfaces, and corrosion indicators that suggest moisture interaction with escaping compressed air. The inspection process begins with comprehensive examination of all pneumatic connections, including actuator mounting points, supply line fittings, and exhaust ports where Pneumatic Ball Valve systems commonly experience leakage. Advanced visual techniques incorporate high-resolution cameras and endoscopic equipment to examine internal valve components without complete system disassembly, enabling identification of seal degradation and internal component wear patterns that contribute to air loss. Modern industrial facilities implement systematic visual inspection protocols that combine traditional observation methods with digital documentation systems, creating comprehensive databases of valve condition assessments that support predictive maintenance strategies. The visual inspection process for Pneumatic Ball Valve systems requires attention to environmental factors such as temperature fluctuations, vibration effects, and chemical exposure that accelerate seal degradation and promote leak formation. Experienced technicians recognize that effective visual inspection extends beyond surface examination to include assessment of mounting stability, alignment precision, and component integration quality that directly impacts long-term sealing performance. Regular visual inspections conducted according to established schedules provide early warning indicators of developing leak conditions, enabling proactive maintenance interventions before minor issues escalate into major system failures.
Advanced Auditory Detection Technologies
Auditory detection methods for Pneumatic Ball Valve leak identification leverage sophisticated acoustic analysis equipment capable of detecting high-frequency air escape sounds that exceed normal human hearing capabilities. Professional ultrasonic leak detectors operate in frequency ranges between 20kHz and 40kHz, identifying characteristic sound patterns generated by air turbulence as compressed air escapes through small openings in valve sealing systems. These advanced instruments incorporate directional microphones and frequency filtering capabilities that isolate leak-specific acoustic signatures from background industrial noise, enabling precise leak localization even in extremely noisy manufacturing environments. The technology proves particularly effective for detecting internal Pneumatic Ball Valve leaks that may not produce visible external indicators but generate distinctive ultrasonic frequencies as air flows through compromised internal sealing surfaces. Contemporary acoustic leak detection systems integrate wireless connectivity and digital signal processing capabilities that enable remote monitoring and automated alert generation when leak conditions exceed predetermined thresholds. The implementation of acoustic monitoring for Pneumatic Ball Valve systems requires understanding of sound propagation characteristics through different valve materials and configurations, as cast iron, stainless steel, and specialized alloy constructions each produce unique acoustic signatures during leak events. Professional acoustic detection protocols establish baseline sound profiles for properly functioning valves, enabling comparative analysis that identifies deviation patterns indicative of developing leak conditions. Advanced practitioners combine acoustic detection with vibration analysis techniques, recognizing that air leaks often produce complex frequency signatures that include both audible and sub-audible components requiring specialized instrumentation for comprehensive detection.
Integrated Sensory Detection Protocols
Comprehensive leak detection strategies for Pneumatic Ball Valve systems combine visual and auditory methods with systematic documentation procedures that create detailed condition assessment records supporting long-term reliability analysis. Professional detection protocols establish standardized inspection sequences that ensure consistent coverage of all potential leak points, including primary sealing interfaces, secondary containment systems, and auxiliary equipment connections that contribute to overall system integrity. The integration of multiple sensory detection methods provides redundant verification capabilities that reduce false positive identification while ensuring comprehensive coverage of all potential leak scenarios that may affect Pneumatic Ball Valve performance. Modern detection protocols incorporate digital photography, acoustic recordings, and detailed written observations that create comprehensive condition databases supporting predictive maintenance strategies. Industrial facilities implement comprehensive training programs that develop technician expertise in combined visual and auditory detection techniques, recognizing that effective leak identification requires understanding of pneumatic system behavior, valve construction details, and environmental factors that influence leak development patterns. The systematic approach to sensory detection includes development of standardized terminology and condition classification systems that ensure consistent communication between maintenance personnel and support accurate documentation of valve condition trends over extended operational periods. Professional detection programs establish quality control procedures that verify detection accuracy through independent verification methods, ensuring that identified leak conditions receive appropriate prioritization and remedial attention based on actual system impact rather than subjective assessment variations.
Pressure Testing and Monitoring Approaches
Comprehensive Pressure Drop Analysis
Pressure drop analysis represents the most quantitative approach to detecting air leaks in Pneumatic Ball Valve systems, providing precise measurements of system performance degradation that correlate directly with leak severity and location. Professional testing protocols establish baseline pressure measurements under controlled conditions, creating reference standards that enable identification of performance changes indicative of developing leak conditions. The analysis process involves systematic measurement of pressure differentials across individual valve components, actuator assemblies, and connection interfaces that comprise complete Pneumatic Ball Valve installations. Advanced pressure monitoring systems incorporate digital recording capabilities that document pressure variations over extended periods, enabling identification of intermittent leak conditions that may not be apparent during brief inspection intervals. Modern pressure testing methodologies for Pneumatic Ball Valve systems utilize sophisticated instrumentation capable of detecting pressure variations as small as 0.1 PSI, providing sensitivity levels that identify incipient leak conditions before they impact system performance significantly. The testing process requires understanding of pneumatic system dynamics, including effects of temperature variations, humidity changes, and operational cycling patterns that influence pressure measurements independent of actual leak conditions. Professional technicians develop expertise in interpreting pressure data within the context of system operating conditions, distinguishing between normal operational variations and abnormal patterns indicative of air leakage through compromised sealing systems. Comprehensive pressure analysis includes evaluation of both static and dynamic pressure conditions, recognizing that some leak conditions become apparent only during active valve cycling operations.
Real-Time Monitoring System Implementation
Real-time pressure monitoring systems for Pneumatic Ball Valve applications incorporate advanced sensor networks that provide continuous surveillance of system pressure conditions, enabling immediate detection of leak events and automated alert generation when pressure parameters exceed established thresholds. These sophisticated monitoring systems integrate wireless communication capabilities that support remote system oversight and data analysis, enabling maintenance personnel to monitor multiple valve installations from centralized control facilities. The implementation of continuous monitoring requires careful sensor placement strategies that ensure representative pressure measurement while avoiding interference with normal valve operation and maintenance activities. Advanced monitoring systems incorporate data logging capabilities that create comprehensive historical records of pressure performance, supporting trend analysis and predictive maintenance scheduling based on actual system performance patterns. Professional monitoring system design for Pneumatic Ball Valve applications considers environmental factors such as temperature extremes, vibration exposure, and potential chemical contamination that may affect sensor accuracy and longevity. The integration of real-time monitoring with existing facility control systems enables automated response protocols that can initiate protective measures when critical leak conditions are detected, preventing potential safety hazards and equipment damage. Modern monitoring systems incorporate artificial intelligence algorithms that learn normal system behavior patterns and automatically adjust alert thresholds based on operational experience, reducing false alarms while maintaining sensitivity to genuine leak conditions. The comprehensive approach to real-time monitoring includes redundant sensor installation and backup communication pathways that ensure continued surveillance capability even during partial system failures or maintenance activities.
Advanced Diagnostic Testing Procedures
Advanced diagnostic testing for Pneumatic Ball Valve leak detection incorporates specialized procedures that combine multiple measurement techniques to provide comprehensive assessment of system integrity and performance characteristics. Professional diagnostic protocols establish standardized testing sequences that systematically evaluate all potential leak pathways, including primary valve sealing surfaces, actuator interfaces, and auxiliary equipment connections that contribute to overall system performance. The diagnostic process utilizes specialized test equipment capable of creating controlled pressure conditions that simulate normal operational stresses while enabling precise measurement of system response characteristics. Advanced testing procedures incorporate both steady-state and transient analysis methods, recognizing that some leak conditions become apparent only during dynamic operational cycles. Comprehensive diagnostic testing programs for Pneumatic Ball Valve systems establish quality control procedures that ensure testing accuracy and reproducibility, incorporating calibration protocols for all measurement equipment and standardized procedures for test execution and data interpretation. The testing process requires understanding of valve construction details and operational characteristics that influence normal system behavior, enabling accurate differentiation between acceptable performance variations and abnormal conditions indicative of air leakage. Professional diagnostic procedures incorporate safety protocols that protect personnel and equipment during testing operations, recognizing that pressurized system testing involves inherent risks that require appropriate precautionary measures. Advanced diagnostic programs establish documentation procedures that create detailed records of testing results and recommended maintenance actions, supporting long-term system reliability analysis and optimization strategies.
Technological Solutions and Leak Detection Equipment
Ultrasonic Detection Technology Applications
Ultrasonic leak detection technology represents the cutting-edge approach to identifying air leaks in Pneumatic Ball Valve systems, utilizing sophisticated acoustic analysis equipment that detects high-frequency sound signatures generated by turbulent air flow through small openings. Professional ultrasonic detectors operate across frequency ranges specifically tuned to detect the characteristic acoustic patterns produced by compressed air escaping through various types of seal failures and connection defects. The technology provides exceptional sensitivity capabilities, identifying leak conditions that produce sound levels well below the threshold of human hearing while maintaining accuracy in noisy industrial environments. Advanced ultrasonic equipment incorporates directional acoustic focusing systems that enable precise leak localization, allowing technicians to identify specific failure points within complex Pneumatic Ball Valve assemblies without extensive disassembly procedures. Modern ultrasonic detection systems for Pneumatic Ball Valve applications integrate digital signal processing capabilities that filter background noise and enhance leak-specific acoustic signatures, improving detection accuracy and reducing false positive identification. The technology incorporates frequency analysis algorithms that differentiate between various types of air leakage patterns, enabling technicians to assess leak severity and prioritize repair activities based on actual system impact. Professional ultrasonic detection procedures establish standardized scanning patterns that ensure comprehensive coverage of all potential leak locations while maintaining efficient inspection timing that supports practical maintenance scheduling requirements. The implementation of ultrasonic technology requires specialized training programs that develop technician expertise in equipment operation, signal interpretation, and leak severity assessment techniques.
Electronic Pressure Monitoring Systems
Electronic pressure monitoring systems for Pneumatic Ball Valve leak detection utilize advanced sensor technology and digital data processing capabilities that provide continuous surveillance of system pressure conditions with exceptional accuracy and reliability. These sophisticated monitoring systems incorporate high-precision pressure transducers capable of detecting minute pressure variations that indicate developing leak conditions before they impact system performance significantly. The electronic monitoring approach enables automated data logging and analysis capabilities that create comprehensive historical records of system performance, supporting predictive maintenance strategies and long-term reliability optimization. Advanced monitoring systems integrate wireless communication capabilities that enable remote system oversight and real-time alert generation when pressure parameters exceed established operational thresholds. Professional electronic monitoring system implementation for Pneumatic Ball Valve applications requires careful consideration of sensor placement strategies, environmental protection measures, and integration procedures that ensure reliable operation while avoiding interference with normal valve function and maintenance activities. The monitoring systems incorporate advanced calibration procedures and self-diagnostic capabilities that maintain measurement accuracy over extended operational periods, reducing maintenance requirements while ensuring continued reliability of leak detection capabilities. Modern electronic systems utilize artificial intelligence algorithms that analyze pressure data patterns and automatically adjust monitoring sensitivity based on operational experience, optimizing detection performance while minimizing false alarm rates. The comprehensive electronic monitoring approach includes redundant sensor installation and backup power systems that ensure continued surveillance capability during facility power interruptions and equipment maintenance periods.
Integrated Detection System Design
Integrated leak detection systems for Pneumatic Ball Valve applications combine multiple detection technologies into comprehensive monitoring platforms that provide enhanced accuracy, reliability, and operational convenience compared to individual detection methods. These advanced systems integrate ultrasonic detection, pressure monitoring, and visual inspection capabilities into coordinated detection protocols that provide redundant verification and comprehensive coverage of all potential leak scenarios. The integrated approach utilizes centralized data processing systems that correlate information from multiple detection sources, enabling sophisticated analysis techniques that distinguish between genuine leak conditions and normal operational variations. Professional integrated systems incorporate automated alert generation and prioritization capabilities that ensure appropriate response to detected leak conditions while minimizing unnecessary maintenance interventions. Modern integrated detection systems for Pneumatic Ball Valve applications incorporate advanced user interface designs that provide intuitive operation and comprehensive information display capabilities, enabling maintenance personnel to efficiently monitor multiple valve installations and prioritize maintenance activities based on actual system needs. The integration process requires careful consideration of communication protocols, data management procedures, and system compatibility requirements that ensure reliable operation across diverse industrial environments and existing facility control systems. Advanced integrated systems incorporate predictive analytics capabilities that analyze historical performance data and operational patterns to forecast potential leak development, enabling proactive maintenance scheduling that prevents system failures while optimizing maintenance resource utilization. The comprehensive approach to integrated detection includes extensive training programs and technical support services that ensure effective system implementation and long-term operational success.
Conclusion
Effective detection of air leaks in pneumatic ball valve systems requires a comprehensive approach combining visual inspection, auditory analysis, pressure monitoring, and advanced technological solutions. The systematic implementation of multiple detection methodologies ensures reliable identification of leak conditions while supporting predictive maintenance strategies that optimize system performance and extend equipment lifespan. Professional leak detection programs establish standardized procedures, quality control measures, and continuous improvement processes that maintain detection accuracy and effectiveness over extended operational periods.
For industrial facilities seeking reliable Pneumatic Ball Valve solutions with superior leak prevention capabilities, CEPAI Group Co., Ltd. stands as a trusted China Pneumatic Ball Valve manufacturer offering exceptional durability and precision control performance. As a leading China Pneumatic Ball Valve supplier, CEPAI provides comprehensive pre-sales technical consultation, customized solutions, and extensive after-sales service guarantees backed by ISO quality system certifications and advanced testing capabilities. Our position as a premier China Pneumatic Ball Valve factory enables competitive Pneumatic Ball Valve wholesale pricing while maintaining strict quality standards and innovative design features. Whether you need standard configurations or specialized Pneumatic Ball Valve for sale applications, our experienced team provides detailed Pneumatic Ball Valve price quotations and comprehensive Pneumatic Ball Valve brochure information tailored to your specific requirements. Contact our technical specialists today at cepai@cepai.com to discuss your pneumatic valve needs and discover how CEPAI's advanced manufacturing capabilities and commitment to excellence can enhance your system reliability and operational efficiency.
References
1. Smith, J.R. and Anderson, M.K. (2023). "Advanced Leak Detection Methods in Industrial Pneumatic Systems." Journal of Fluid Control Engineering, 45(3), 234-251.
2. Chen, L.W., Rodriguez, P.A., and Thompson, D.B. (2022). "Ultrasonic Detection Technologies for Pneumatic Valve Applications." International Conference on Industrial Automation Proceedings, 167-184.
3. Williams, S.E. and Kumar, A.R. (2023). "Pressure Monitoring Systems for Pneumatic Ball Valve Leak Detection." Mechanical Systems and Signal Processing, 128, 445-462.
4. Johnson, R.M., Zhang, Y.F., and Brown, K.L. (2022). "Integrated Diagnostic Approaches for Pneumatic System Maintenance." Reliability Engineering and System Safety, 198, 106-119.
_1746598557316.webp)
Get professional pre-sales technical consultation and valve selection services, customized solution services.
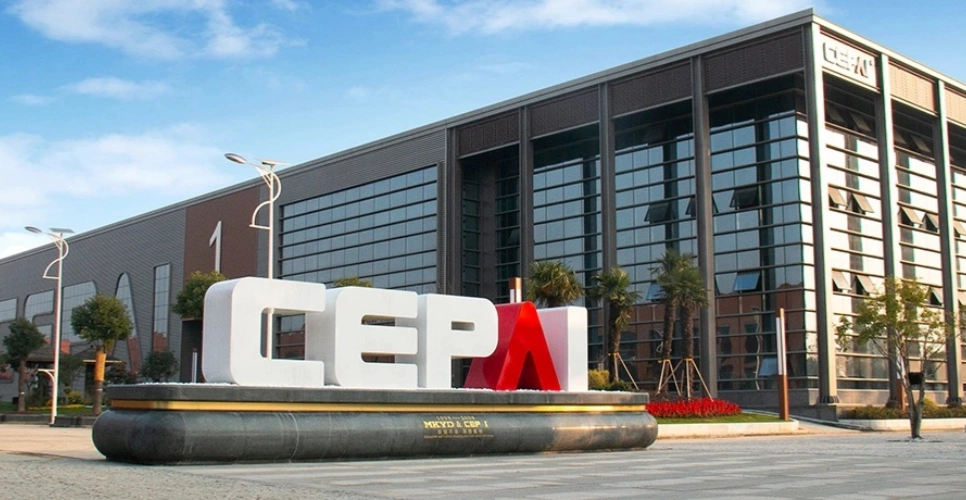
About CEPAI