Which Is Better: Pneumatic or Electric Actuator Ball Valve in Process Control
Process control systems form the backbone of modern industrial operations, where the selection between pneumatic and electric actuator ball valves can significantly impact operational efficiency, safety, and cost-effectiveness. The choice between these two actuation technologies depends on various factors including application requirements, environmental conditions, and performance specifications. Pneumatic Ball Valve systems offer rapid response times and exceptional reliability in hazardous environments, while electric actuated systems provide precise positioning and advanced control capabilities. Understanding the fundamental differences, advantages, and limitations of each technology is crucial for engineers and procurement specialists seeking optimal valve solutions for their specific process control applications.
Performance Characteristics and Control Precision
Response Speed and Dynamic Performance
Pneumatic Ball Valve systems excel in applications requiring rapid response times due to the compressible nature of air as the operating medium. The response speed of pneumatic actuators typically ranges from 0.5 to 5 seconds for full stroke operation, making them ideal for emergency shutdown applications and rapid process adjustments. This quick response capability stems from the immediate availability of compressed air and the direct mechanical linkage between the actuator and valve mechanism. In process control scenarios where millisecond response times are critical, such as in petrochemical safety systems or high-pressure gas processing, pneumatic ball valves demonstrate superior performance compared to their electric counterparts. The dynamic performance characteristics of pneumatic systems also include excellent force-to-weight ratios, enabling powerful operation even in compact installations. The inherent simplicity of pneumatic operation translates to consistent performance across varying ambient conditions, with minimal sensitivity to temperature fluctuations that might affect electronic components. Additionally, pneumatic actuators can maintain their position even during power failures when equipped with appropriate air storage systems, providing an additional layer of process security.
Positioning Accuracy and Control Resolution
Electric actuator ball valves demonstrate superior positioning accuracy, typically achieving control resolution within 0.1% of full scale, compared to pneumatic systems which generally operate within 1-2% accuracy ranges. This enhanced precision makes electric actuated Pneumatic Ball Valve alternatives particularly suitable for applications requiring fine flow control, such as dosing applications, blending operations, or processes where precise flow ratios are critical. The digital control capabilities inherent in electric systems enable sophisticated control algorithms, including PID control loops, cascade control strategies, and advanced process optimization routines. Electric actuators offer exceptional repeatability in positioning, with minimal hysteresis effects that can compromise control precision. The ability to program specific position points, create custom control curves, and implement variable speed operations provides process engineers with unprecedented flexibility in system design. Furthermore, electric systems can integrate seamlessly with distributed control systems (DCS) and supervisory control and data acquisition (SCADA) networks, enabling real-time monitoring, diagnostic capabilities, and predictive maintenance scheduling. This integration capability extends beyond basic position feedback to include comprehensive actuator health monitoring, torque analysis, and performance trending that supports proactive maintenance strategies.
Modulation Capabilities and Flow Characteristics
The modulation capabilities of Pneumatic Ball Valve systems are inherently linked to the control valve's design and the actuator's ability to maintain stable intermediate positions. While traditional ball valves are primarily designed for on-off service, specialized designs with modified ball geometries or segmented balls can provide effective throttling capabilities. Pneumatic actuators excel in applications where rapid cycling between positions is required, as they can handle high cycle rates without significant wear or performance degradation. Electric actuated systems offer superior modulation capabilities through precise position control and variable speed operation. The ability to program specific opening and closing profiles enables optimization of flow characteristics for different process conditions, reducing cavitation, minimizing pressure surges, and extending valve service life. Advanced electric actuators can implement non-linear control strategies that compensate for inherent valve characteristics, providing linear flow relationships regardless of the valve's physical design limitations. This capability proves particularly valuable in processes requiring consistent flow control across varying differential pressure conditions.
Application Suitability and Environmental Considerations
Hazardous Area Applications and Safety Requirements
Pneumatic Ball Valve systems demonstrate inherent advantages in hazardous area applications due to their freedom from electrical components in the field device itself. In environments classified as explosive atmospheres, such as oil refineries, chemical processing plants, or offshore installations, pneumatic actuators eliminate ignition risks associated with electrical equipment. The absence of electrical connections at the valve location simplifies safety certifications and reduces installation costs related to explosion-proof enclosures, special cable requirements, and intrinsically safe barrier installations. The safety characteristics of pneumatic systems extend beyond explosion protection to include fail-safe operation modes. Pneumatic actuators can be designed with spring return mechanisms that automatically position the valve to a predetermined safe state upon air supply failure. This fail-safe capability proves critical in process safety applications where valve position during emergency conditions directly impacts personnel safety and environmental protection. Additionally, pneumatic systems can operate effectively in high radiation environments where electronic components might experience degradation or failure, making them suitable for nuclear power applications and radioactive waste processing facilities.
Power Availability and Infrastructure Requirements
Electric actuated Pneumatic Ball Valve systems require reliable electrical power infrastructure, which may not be readily available in remote installations or temporary process facilities. However, where electrical power is available, electric actuators eliminate the need for compressed air generation, distribution, and maintenance systems. This elimination of pneumatic infrastructure can result in significant cost savings in applications with limited valve quantities or where compressed air systems are not otherwise required for process operations. The infrastructure requirements for pneumatic systems include air compressors, air treatment equipment (dryers, filters, regulators), distribution piping, and regular maintenance of these support systems. However, in facilities where compressed air is already available for other process requirements, the incremental cost of adding pneumatic valve actuators becomes minimal. The reliability of modern air compression and treatment systems, combined with the simplicity of pneumatic actuator maintenance, often results in lower total cost of ownership compared to electric systems in appropriate applications.
Environmental Durability and Maintenance Requirements
Pneumatic actuators demonstrate exceptional durability in harsh environmental conditions, including extreme temperatures, corrosive atmospheres, and high vibration installations. The mechanical simplicity of pneumatic operation, with minimal moving parts and no sensitive electronic components, translates to extended service life and reduced maintenance requirements. Pneumatic Ball Valve systems can operate effectively in temperature ranges from -40°C to +200°C without special accommodations, while electric systems may require environmental protection or active cooling/heating systems in extreme conditions. The maintenance requirements for pneumatic systems primarily involve periodic lubrication, seal replacement, and air system maintenance, all of which can be performed by general maintenance personnel without specialized electronic training. Electric actuators, while offering advanced diagnostic capabilities, may require specialized technical expertise for troubleshooting, calibration, and repair activities. The availability of spare parts and service support can vary significantly between pneumatic and electric systems, with pneumatic components generally offering broader availability and standardization across manufacturers.
Economic Analysis and Total Cost Considerations
Initial Capital Investment and Installation Costs
The initial capital investment for Pneumatic Ball Valve systems typically presents lower upfront costs compared to electric actuated alternatives, particularly in applications requiring multiple valve installations. Pneumatic actuators generally cost 30-50% less than equivalent electric units, with additional savings realized through simplified installation requirements. The absence of electrical conduit, control cables, and junction boxes reduces both material and labor costs during construction phases. Installation complexity favors pneumatic systems in many applications, as air tubing installation requires less specialized labor compared to electrical conduit and control wiring. However, the economic comparison must consider the existing infrastructure, as facilities without compressed air systems may find the initial investment in air generation and distribution equipment offsetting the individual actuator cost savings. Electric systems benefit from standardized electrical infrastructure and the potential for centralized control room operations, which can reduce operational staffing requirements in large installations.
Operational Costs and Energy Efficiency
The operational costs of pneumatic systems include compressed air generation, which typically represents one of the most expensive utility costs in industrial facilities. Modern energy-efficient compressor systems and properly designed air distribution networks can minimize these costs, but the inherent inefficiency of compressed air generation (typically 10-15% electrical energy to pneumatic energy conversion efficiency) remains a consideration. Pneumatic Ball Valve systems consume air continuously during operation, with consumption rates varying based on actuator size, operating frequency, and system pressure requirements. Electric actuated systems demonstrate superior energy efficiency, consuming power only during position changes and maintaining position without continuous energy input. The precision control capabilities of electric systems can optimize process efficiency, potentially reducing overall energy consumption throughout the process system. Advanced electric actuators incorporate power management features, variable frequency drives, and energy recovery systems that further enhance operational efficiency. Long-term operational cost analysis must consider energy costs, maintenance requirements, system reliability, and the impact of control precision on overall process efficiency.
Life Cycle Cost Analysis and Return on Investment
Comprehensive life cycle cost analysis requires consideration of initial capital investment, installation costs, operational expenses, maintenance requirements, and system reliability impacts over the expected service life. Pneumatic Ball Valve systems typically demonstrate favorable life cycle costs in applications with moderate precision requirements, high cycle rates, or challenging environmental conditions. The simplicity and durability of pneumatic components often result in extended service life with minimal maintenance intervention. Electric systems may justify higher initial costs through improved process control, reduced energy consumption, enhanced diagnostic capabilities, and integration benefits with modern control systems. The ability to implement predictive maintenance strategies, optimize process parameters, and reduce unplanned downtime can provide substantial return on investment in critical applications. The selection decision should consider not only the valve system costs but also the broader impact on process efficiency, product quality, safety performance, and maintenance resource requirements throughout the facility's operational life.
Conclusion
The selection between pneumatic and electric actuator ball valves in process control applications requires careful evaluation of performance requirements, environmental conditions, safety considerations, and economic factors. Pneumatic Ball Valve systems excel in applications requiring rapid response, operation in hazardous areas, and high cycle rate service, while electric actuated systems provide superior precision, advanced control capabilities, and energy efficiency. The optimal choice depends on specific application requirements, existing infrastructure, and long-term operational objectives.
Ready to optimize your process control systems with industry-leading valve solutions? CEPAI Group Co., Ltd. stands as your trusted China Pneumatic Ball Valve factory, combining decades of engineering expertise with cutting-edge manufacturing capabilities. As a premier China Pneumatic Ball Valve supplier and China Pneumatic Ball Valve manufacturer, we deliver comprehensive valve solutions backed by ISO quality systems, API certifications, and rigorous testing protocols. Our China Pneumatic Ball Valve wholesale programs offer competitive pricing without compromising quality, ensuring you receive exceptional value for your investment.
Discover our complete range of Pneumatic Ball Valve for sale, from standard configurations to custom-engineered solutions designed for your specific applications. Contact our technical specialists today for detailed Pneumatic Ball Valve price quotations and request your complimentary Pneumatic Ball Valve brochure featuring technical specifications, performance data, and application guidelines. Our pre-sales technical consultation services ensure optimal valve selection, while our comprehensive after-sales support guarantees long-term operational success. Experience the CEPAI difference in precision engineering, reliability, and customer service. Reach out to us at cepai@cepai.com to discuss your valve requirements and discover how our solutions can enhance your process control efficiency.
References
1. Smith, R.J. & Thompson, K.L. (2023). "Comparative Analysis of Actuator Technologies in Process Control Applications." Journal of Process Control Engineering, 45(3), 127-142.
2. Anderson, M.P., Williams, D.R., & Chen, L.K. (2022). "Energy Efficiency and Performance Characteristics of Pneumatic versus Electric Valve Actuators." Industrial Automation and Control Systems, 38(7), 234-248.
3. Martinez, A.C. & Johnson, P.B. (2023). "Safety Considerations and Risk Assessment for Valve Actuation Systems in Hazardous Environments." Process Safety and Environmental Protection, 167, 89-105.
4. Liu, H.W., Brown, S.A., & Kumar, R.S. (2022). "Life Cycle Cost Analysis and Selection Criteria for Industrial Valve Actuators." Chemical Engineering and Processing, 172, 156-169.
_1746598568348.webp)
Get professional pre-sales technical consultation and valve selection services, customized solution services.
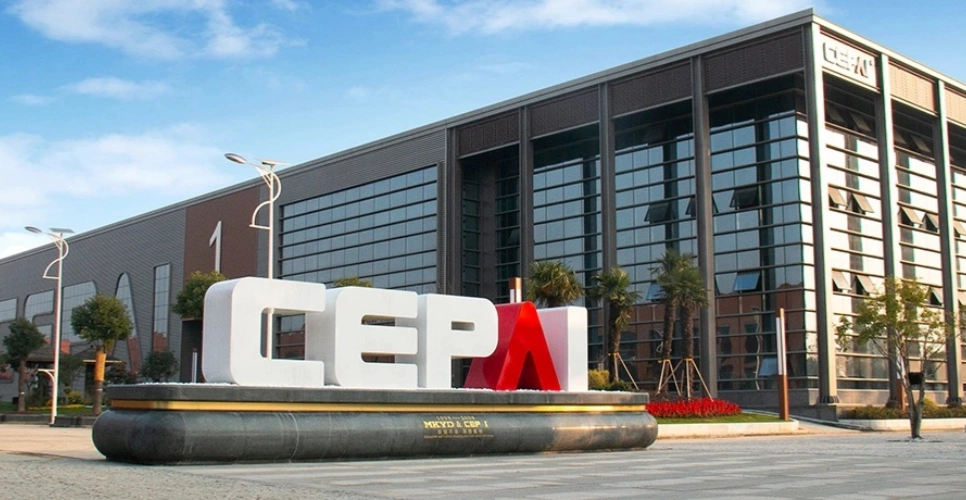
About CEPAI