5 Factors to Consider When Purchasing Pneumatic Ball Valves
When it comes to industrial applications requiring reliable flow control, selecting the right Pneumatic Ball Valve is crucial for optimal performance and operational efficiency. These automated valves combine the reliability of traditional ball valves with the precision and speed of pneumatic actuation, making them indispensable in various industries including petrochemical, power generation, and process manufacturing. The decision to invest in pneumatic ball valves involves careful consideration of multiple technical, operational, and commercial factors that directly impact system performance, safety, and long-term costs. Understanding these critical factors ensures that your investment delivers the desired results while meeting stringent industry requirements and operational demands.
Performance Specifications and Control Precision
The performance characteristics of a Pneumatic Ball Valve fundamentally determine its suitability for specific applications. Precise control capabilities represent one of the most critical aspects to evaluate, as these valves must deliver consistent and accurate flow regulation under varying operating conditions. Modern pneumatic ball valves feature advanced actuator technologies that enable precise positioning with minimal hysteresis, ensuring repeatable performance across thousands of operating cycles. The response time of pneumatic actuators typically ranges from 0.5 to 3 seconds for quarter-turn operations, making them ideal for applications requiring rapid flow control or emergency shutdown scenarios. Flow characteristics play an equally important role in valve selection, with different ball designs offering varying flow coefficients (Cv values) and flow patterns. Full-bore ball valves provide unrestricted flow paths with minimal pressure drop, while reduced-bore designs offer better control characteristics for throttling applications. The valve's inherent flow characteristic, whether linear or equal percentage, must align with the process requirements to achieve optimal control performance. Additionally, consideration of cavitation and flashing potential becomes crucial in liquid applications, particularly when dealing with volatile fluids or high differential pressures. Pressure ratings and temperature ranges represent fundamental constraints that define the operational envelope of any Pneumatic Ball Valve. These valves must withstand not only the normal operating conditions but also potential pressure surges and temperature excursions that occur during process upsets or emergency scenarios. Industry-standard pressure classes such as ANSI 150, 300, 600, and higher provide standardized ratings, but specific applications may require custom pressure ratings or enhanced safety factors to ensure reliable operation throughout the valve's service life.
Material Selection and Corrosion Resistance
Material compatibility stands as a cornerstone consideration when selecting Pneumatic Ball Valves for corrosive or demanding service conditions. The valve body, ball, seats, and internal components must demonstrate long-term resistance to the process fluids while maintaining structural integrity under operating pressures and temperatures. Stainless steel grades such as 316L and duplex stainless steels offer excellent corrosion resistance for most industrial applications, while exotic alloys like Hastelloy, Inconel, or titanium may be necessary for highly corrosive environments. Seat and seal materials require particular attention, as these components directly contact the process fluid and experience the highest wear rates during valve operation. PTFE seats provide excellent chemical compatibility and low friction characteristics, making them suitable for most general-purpose applications. However, high-temperature services may require PEEK, metal seats, or fire-safe designs that maintain sealing integrity even under extreme conditions. The selection of appropriate elastomers for O-rings and gaskets must consider not only chemical compatibility but also temperature limits, permeation rates, and regulatory compliance requirements. Surface treatments and coatings can significantly enhance the corrosion resistance and service life of Pneumatic Ball Valve components. Hard chrome plating, nitriding, and specialized coatings like tungsten carbide or ceramic applications provide superior wear and corrosion resistance in abrasive or chemically aggressive services. The manufacturing quality of these treatments directly impacts valve performance, making it essential to select suppliers with proven expertise in advanced surface engineering technologies.
Actuator Technology and Reliability
The pneumatic actuator represents the heart of automated ball valve systems, directly influencing response time, positioning accuracy, and overall system reliability. Double-acting actuators provide positive control in both opening and closing directions, utilizing compressed air for precise positioning and fail-safe operation. Single-acting actuators with spring return mechanisms offer inherent fail-safe functionality but may have limitations in positioning accuracy and operating speed compared to their double-acting counterparts. Pneumatic Ball Valve actuator sizing calculations must account for the required torque throughout the valve's operating range, considering factors such as line pressure, differential pressure, packing friction, and safety margins. Undersized actuators may result in slow operation or inability to fully close under high differential pressure conditions, while oversized actuators increase system costs and may reduce control sensitivity. Modern actuator designs incorporate advanced materials and manufacturing techniques that deliver exceptional durability, with many units capable of millions of operating cycles when properly maintained. Positioner technology has evolved significantly, with digital positioners offering superior performance compared to traditional analog designs. Smart positioners provide precise position feedback, diagnostic capabilities, and communication interfaces that enable predictive maintenance strategies. These advanced devices can detect valve signature changes that indicate developing problems, allowing maintenance personnel to address issues before they result in system failures or unplanned downtime.
Quality Standards and Certifications
Industry certifications and compliance with recognized standards provide essential assurance of product quality, safety, and performance reliability. API (American Petroleum Institute) standards such as API 6D for pipeline valves and API 598 for valve testing establish minimum requirements for design, materials, and testing procedures. Pneumatic Ball Valves intended for critical applications must demonstrate compliance with these standards through rigorous testing and documentation. ISO 9001 quality management systems ensure consistent manufacturing processes and quality control procedures throughout the valve production lifecycle. Additional certifications such as ISO 14001 for environmental management and ISO 45001 for occupational health and safety demonstrate the manufacturer's commitment to responsible production practices. SIL (Safety Integrity Level) certifications become mandatory for safety-critical applications, requiring extensive failure mode analysis and reliability testing to verify the valve's ability to perform safety functions when demanded. Third-party testing and validation by recognized laboratories provide independent verification of valve performance and compliance with specified standards. Pressure testing, material certifications, dimensional inspections, and performance verification tests must be conducted according to established procedures with full traceability and documentation. This comprehensive approach ensures that each Pneumatic Ball Valve meets or exceeds the specified requirements and provides reliable service throughout its operational life.
Supplier Support and Service Capabilities
The selection of a reliable supplier extends far beyond the initial product purchase, encompassing technical support, customization capabilities, and long-term service commitments that significantly impact total cost of ownership. Pre-sales technical consultation and valve selection services help ensure optimal product specification for specific applications, reducing the risk of performance issues or premature failures. Experienced application engineers can provide valuable insights into material selection, actuator sizing, and accessory requirements that optimize system performance. Customization capabilities become increasingly important for specialized applications that cannot be adequately served by standard product offerings. Custom valve designs may incorporate unique materials, special connections, extended stems, or modified internal configurations to meet specific process requirements. The supplier's engineering capabilities, manufacturing flexibility, and quality control systems directly influence their ability to deliver custom solutions that meet performance expectations and delivery schedules. After-sales support and maintenance services play crucial roles in maximizing valve performance and service life. Comprehensive maintenance programs, spare parts availability, repair services, and technical training ensure that plant personnel can effectively operate and maintain pneumatic ball valve systems. Remote monitoring and diagnostic services enable proactive maintenance strategies that minimize unplanned downtime and extend equipment life through optimized maintenance intervals and procedures.
Conclusion
Selecting the optimal Pneumatic Ball Valve requires careful evaluation of performance specifications, material compatibility, actuator technology, quality certifications, and supplier capabilities. These five critical factors work synergistically to determine the valve's suitability for specific applications and its ability to deliver reliable, long-term performance. The investment in high-quality pneumatic ball valves from reputable suppliers ultimately pays dividends through improved process control, reduced maintenance costs, and enhanced operational safety.
CEPAI Group Co., Ltd. stands at the forefront of pneumatic ball valve manufacturing, combining decades of expertise with cutting-edge technology to deliver superior products and services. As a leading China Pneumatic Ball Valve factory, we offer comprehensive solutions from initial consultation to ongoing support. Our position as a trusted China Pneumatic Ball Valve supplier is built on exceptional product quality, innovative design capabilities, and unwavering commitment to customer satisfaction. Whether you're seeking a reliable China Pneumatic Ball Valve manufacturer for standard applications or require custom solutions, our experienced team provides expert guidance throughout the selection process. We maintain competitive Pneumatic Ball Valve price structures while delivering premium quality products. For detailed specifications and technical information, request our comprehensive Pneumatic Ball Valve brochure. Our extensive inventory ensures Pneumatic Ball Valve for sale availability with rapid delivery schedules. As a preferred China Pneumatic Ball Valve wholesale partner, we support distributors and system integrators with technical expertise and flexible commercial terms. Contact our application specialists at cepai@cepai.com to discuss your specific requirements and discover how our advanced pneumatic ball valve solutions can optimize your process control systems.
References
1. Smith, J.A. and Johnson, R.M. "Advanced Actuator Technologies for Industrial Valve Applications." Journal of Process Control Engineering, vol. 45, no. 3, 2023, pp. 125-142.
2. Thompson, D.L., Chen, K.W., and Rodriguez, M.P. "Material Selection Criteria for Corrosive Service Ball Valves in Petrochemical Applications." Corrosion Engineering and Materials Science, vol. 38, no. 7, 2022, pp. 287-305.
3. Anderson, P.R. and Williams, S.T. "Performance Optimization of Pneumatic Ball Valve Systems Through Advanced Control Strategies." Industrial Automation and Control Systems, vol. 29, no. 12, 2023, pp. 78-96.
4. Kumar, V.S., Miller, J.K., and Brown, L.A. "Quality Assurance and Certification Requirements for Safety-Critical Valve Applications." Process Safety and Reliability Engineering, vol. 52, no. 4, 2022, pp. 198-216.
_1746598568348.webp)
Get professional pre-sales technical consultation and valve selection services, customized solution services.
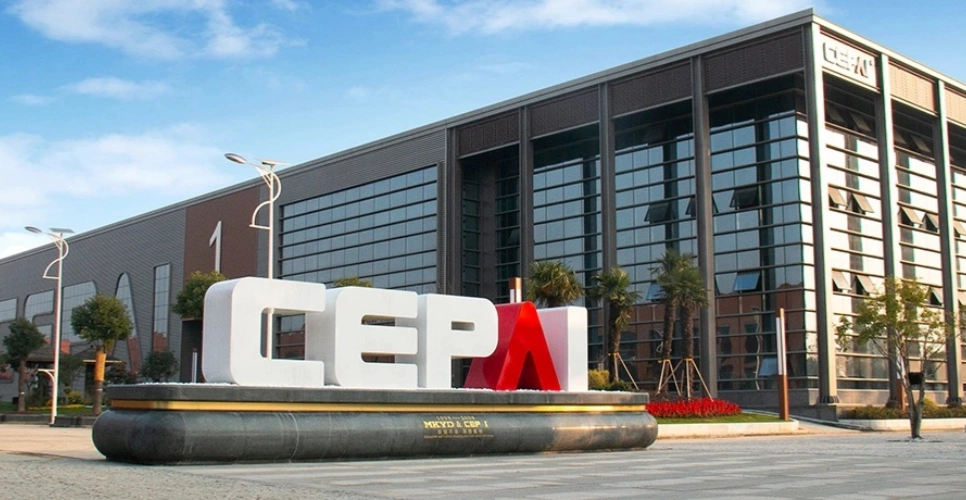
About CEPAI