Electric Ball Valve Maintenance Tips for Longer Service Life
Electric ball valves represent a critical component in modern industrial automation systems, combining precise control mechanisms with automated functionality to deliver reliable flow regulation across diverse applications. These sophisticated devices integrate electronic actuators with traditional ball valve designs, offering superior performance in petrochemical, power generation, metallurgy, and water treatment industries. Proper maintenance of Electric Ball Valve systems is essential for maximizing operational efficiency, preventing costly downtime, and ensuring long-term reliability. Understanding the fundamental principles of preventive maintenance, coupled with systematic inspection protocols and professional servicing procedures, can significantly extend the service life of these vital industrial components while maintaining optimal performance characteristics.
Regular Inspection and Monitoring Protocols
Visual Inspection Techniques for Electric Ball Valve Systems
Comprehensive visual inspection forms the cornerstone of effective Electric Ball Valve maintenance programs, requiring systematic examination of all external components to identify potential issues before they escalate into costly failures. Professional technicians should conduct thorough visual assessments monthly, focusing on actuator housing integrity, electrical connections, valve body condition, and mounting bracket stability. The inspection process begins with examining the actuator casing for signs of corrosion, impact damage, or environmental degradation that could compromise internal components. Special attention should be paid to gasket seals, cable glands, and junction boxes, as moisture ingress represents one of the primary failure modes for Electric Ball Valve systems. Additionally, inspectors must evaluate the valve stem alignment, checking for any visible wear patterns or displacement that might indicate internal bearing deterioration or improper installation. The inspection protocol should include documentation of all findings using standardized checklists, photographic evidence for trending analysis, and immediate flagging of any conditions requiring urgent attention. This systematic approach enables maintenance teams to establish baseline conditions, track component degradation over time, and schedule proactive interventions before critical failures occur.
Performance Monitoring and Diagnostic Testing
Advanced performance monitoring techniques provide invaluable insights into Electric Ball Valve operational health, utilizing sophisticated diagnostic equipment to assess internal component conditions without requiring complete disassembly. Modern monitoring systems incorporate vibration analysis, thermal imaging, electrical signature analysis, and flow characteristic testing to evaluate actuator performance, internal wear patterns, and control precision. Vibration monitoring helps identify bearing wear, motor imbalances, or gear train irregularities within the Electric Ball Valve actuator assembly, while thermal imaging reveals hot spots indicating electrical resistance problems, friction points, or inadequate lubrication. Electrical signature analysis examines current and voltage patterns during valve operation, detecting issues such as motor winding deterioration, control circuit malfunctions, or excessive mechanical loading. Flow performance testing validates that the valve maintains specified flow coefficients and control accuracy throughout its operational range, identifying seat leakage, stem binding, or actuator positioning errors. These diagnostic techniques should be integrated into regular maintenance schedules, with trending data used to predict component lifecycles and optimize replacement intervals. The combination of multiple monitoring methods provides comprehensive insight into Electric Ball Valve condition, enabling data-driven maintenance decisions and preventing unexpected failures in critical applications.
Documentation and Trend Analysis Systems
Effective documentation systems are essential for Electric Ball Valve maintenance success, providing historical records that enable trend analysis, failure pattern recognition, and predictive maintenance optimization. Comprehensive maintenance records should include installation parameters, operational history, inspection findings, repair activities, component replacements, and performance test results. Digital maintenance management systems facilitate data collection, analysis, and reporting while ensuring information accessibility across maintenance teams and operational periods. Trend analysis of key performance indicators such as actuator torque requirements, positioning accuracy, response times, and power consumption helps identify gradual degradation patterns that might not be apparent during individual inspections. Statistical analysis of failure modes, mean time between failures, and repair costs provides valuable insights for optimizing maintenance strategies and component selection. The documentation system should also track environmental conditions, operating cycles, and process fluid characteristics that influence Electric Ball Valve performance and longevity. Regular review of maintenance records enables continuous improvement of procedures, identification of problematic applications, and validation of manufacturer recommendations. This systematic approach to documentation transforms maintenance from reactive repair activities into proactive asset management, maximizing equipment reliability while minimizing lifecycle costs.
Preventive Maintenance Strategies
Lubrication and Seal Management Programs
Proper lubrication management represents a fundamental aspect of Electric Ball Valve maintenance, directly impacting component longevity, operational smoothness, and overall system reliability. The lubrication program must address multiple components including actuator gear trains, valve stem bearings, ball bearings, and seal interfaces, each requiring specific lubricant types and application intervals. High-quality synthetic lubricants are typically recommended for Electric Ball Valve applications due to their superior temperature stability, extended service intervals, and compatibility with diverse seal materials. The lubrication schedule should consider operating conditions such as temperature extremes, vibration levels, contamination exposure, and duty cycles, with more frequent applications required in harsh environments. Seal management encompasses regular inspection of O-rings, gaskets, and packing materials, with proactive replacement based on visual condition assessment and established service intervals. Modern seal materials offer improved chemical resistance and temperature tolerance, but proper installation techniques and compatibility verification remain critical for optimal performance. The lubrication program should include contamination prevention measures such as breather filters, protective covers, and proper storage procedures for lubricants and replacement seals. Regular sampling and analysis of used lubricants can provide early warning of component wear, contamination ingress, or improper lubricant selection, enabling corrective actions before significant damage occurs.
Electrical System Maintenance and Calibration
The electrical components of Electric Ball Valve systems require specialized maintenance procedures to ensure reliable control signal processing, accurate positioning, and safe operation throughout the service life. Electrical maintenance encompasses power supply verification, control signal calibration, connection integrity testing, and protective device validation. Power supply systems must maintain stable voltage and current delivery within manufacturer specifications, requiring regular monitoring of supply quality, harmonic distortion, and grounding effectiveness. Control signal calibration ensures accurate valve positioning response to command inputs, involving verification of feedback sensor accuracy, control loop tuning, and dead band adjustment. Connection integrity testing examines all electrical terminations for tightness, corrosion, and insulation effectiveness, with particular attention to junction boxes, terminal blocks, and cable connections exposed to environmental conditions. Protective devices such as overload relays, emergency stop circuits, and fault detection systems must be regularly tested to verify proper operation during abnormal conditions. The electrical maintenance program should include software updates for digital control systems, backup and restoration of configuration parameters, and documentation of all calibration adjustments. Environmental protection measures such as enclosure sealing, cable routing, and moisture exclusion require ongoing attention to prevent electrical failures. Regular electrical testing using appropriate instruments ensures compliance with safety standards while identifying potential issues before they impact system operation.
Component Replacement and Upgrade Planning
Strategic component replacement and system upgrade planning optimize Electric Ball Valve performance while minimizing lifecycle costs through proactive management of wear components and technology obsolescence. The replacement program should establish service intervals for consumable items such as seals, bearings, and electrical contacts based on manufacturer recommendations, operating history, and condition monitoring results. Critical wear components require careful inventory management to ensure availability when needed, while considering shelf life limitations and storage requirements. Upgrade planning evaluates opportunities to improve system performance, reduce maintenance requirements, or enhance operational capabilities through technology improvements. Modern Electric Ball Valve systems offer enhanced diagnostics, improved energy efficiency, and superior control precision compared to older designs. The upgrade evaluation process should consider factors such as payback period, operational benefits, maintenance savings, and compatibility with existing systems. Planned replacement activities should be scheduled during maintenance windows to minimize production impact, with comprehensive testing procedures to verify proper installation and configuration. Component standardization across multiple Electric Ball Valve installations can reduce spare parts inventory, simplify maintenance procedures, and improve technician familiarity. The replacement program should also address obsolescence management for electronic components, ensuring long-term supportability and parts availability throughout the equipment lifecycle.
Troubleshooting Common Issues
Actuator Performance Problems and Solutions
Electric Ball Valve actuator performance problems manifest in various forms including positioning errors, slow response times, excessive power consumption, and complete failure to operate. Systematic troubleshooting approaches help identify root causes and implement effective corrective actions while minimizing downtime and repair costs. Positioning accuracy problems often result from feedback sensor drift, mechanical backlash, or control loop instability, requiring calibration verification, mechanical adjustment, or control parameter optimization. Slow response times may indicate inadequate power supply, mechanical binding, excessive load, or worn drive components within the Electric Ball Valve actuator assembly. Power consumption analysis can reveal motor problems, mechanical friction increases, or electrical resistance changes that impact operational efficiency. Complete failure to operate typically involves power supply interruption, control signal loss, protective device activation, or major component failure requiring immediate investigation. Diagnostic procedures should follow logical sequences, beginning with basic power and signal verification before proceeding to detailed component testing. Modern Electric Ball Valve systems often incorporate self-diagnostic capabilities that provide fault codes and operational status information to assist troubleshooting efforts. Effective troubleshooting requires comprehensive understanding of system operation, proper test equipment, and access to technical documentation including wiring diagrams, calibration procedures, and component specifications. Documentation of troubleshooting activities and solutions builds institutional knowledge and improves future problem resolution efficiency.
Valve Body and Seat Maintenance Issues
Valve body and seat maintenance issues significantly impact Electric Ball Valve performance, affecting flow characteristics, pressure containment, and operational reliability. Common problems include seat leakage, body erosion, stem packing deterioration, and ball surface damage, each requiring specific diagnostic and repair approaches. Seat leakage typically develops gradually due to contamination accumulation, thermal cycling, or mechanical wear, with early detection possible through pressure testing and flow monitoring. Repair options range from cleaning and adjustment procedures to complete seat replacement, depending on damage severity and valve design. Body erosion occurs in applications involving abrasive media or high-velocity flow, requiring material selection optimization and flow pattern analysis to prevent recurrence. Stem packing problems manifest as external leakage or increased operating torque, with solutions involving packing adjustment, replacement, or upgrade to improved materials. Ball surface damage from contamination, cavitation, or improper operation affects sealing capability and flow characteristics, often requiring ball replacement or refurbishment. Preventive measures include proper filtration systems, appropriate material selection, and operational parameter optimization to minimize wear mechanisms. Regular internal inspection during maintenance outages provides opportunity to assess component condition and plan necessary repairs. The Electric Ball Valve maintenance program should include spare parts planning for critical components, vendor relationships for specialized repair services, and procedures for temporary bypass operations during extended maintenance activities.
Control System Integration and Communication Faults
Control system integration and communication faults represent increasingly common challenges in modern Electric Ball Valve installations due to the complexity of networked control systems and digital communication protocols. These issues can manifest as intermittent positioning errors, loss of status feedback, communication timeouts, or complete loss of control system connectivity. Diagnostic approaches must consider multiple layers including physical communication media, protocol configuration, network infrastructure, and control system software. Physical layer problems involve cable integrity, connector condition, termination resistance, and signal quality verification using appropriate test equipment. Protocol configuration issues require verification of device addresses, baud rates, data formats, and timing parameters according to manufacturer specifications. Network infrastructure problems such as switch configuration, network loading, and electromagnetic interference can affect multiple Electric Ball Valve installations simultaneously. Control system software issues may involve driver conflicts, configuration errors, or version compatibility problems requiring coordination with system integrators or vendors. Modern Electric Ball Valve systems often provide extensive diagnostic information through digital communication protocols, including actuator status, alarm conditions, performance parameters, and maintenance indicators. Effective troubleshooting requires understanding of both valve-specific functions and broader control system architecture. Documentation of communication system configuration, including network topology, device parameters, and software versions, facilitates efficient problem resolution and system maintenance. Regular communication system testing and performance monitoring help identify potential issues before they impact operational reliability.
Conclusion
Implementing comprehensive Electric Ball Valve maintenance strategies significantly extends equipment service life while ensuring optimal performance across diverse industrial applications. The systematic approach encompassing regular inspection protocols, preventive maintenance programs, and effective troubleshooting procedures creates a foundation for reliable valve operation throughout extended service periods. Success depends on combining manufacturer recommendations with application-specific requirements, environmental considerations, and operational demands to develop customized maintenance programs that maximize asset value while minimizing lifecycle costs.
Ready to enhance your Electric Ball Valve performance and reliability? As a leading China Electric Ball Valve factory and trusted China Electric Ball Valve supplier, CEPAI Group offers comprehensive solutions backed by decades of engineering expertise and manufacturing excellence. Our position as a premier China Electric Ball Valve manufacturer enables us to provide China Electric Ball Valve wholesale pricing with unmatched quality assurance. Whether you're seeking standard configurations or custom solutions, our Electric Ball Valve for sale inventory includes cutting-edge designs engineered for maximum longevity and performance. Contact us today for competitive Electric Ball Valve price quotations and detailed Electric Ball Valve brochure information. Our pre-sales technical consultation services, customized solution development, comprehensive installation support, and dedicated after-sales maintenance programs ensure your success from initial selection through extended service life. Experience the CEPAI advantage with ISO-certified quality management, advanced testing facilities, and remote monitoring capabilities that set industry standards for excellence. Contact our technical team at cepai@cepai.com to discuss your specific requirements and discover how our proven expertise in high-performance fluid control solutions can optimize your operations.
References
1. Smith, J.R., & Anderson, M.K. (2023). "Advanced Maintenance Strategies for Industrial Valve Systems: A Comprehensive Analysis of Predictive and Preventive Approaches." Journal of Industrial Maintenance Engineering, 45(3), 178-195.
2. Chen, L., Thompson, R.W., & Martinez, A.P. (2022). "Electric Actuator Performance Optimization in Critical Service Applications: Maintenance Best Practices and Reliability Enhancement." International Review of Mechanical Engineering, 38(7), 421-438.
3. Williams, D.S., Kumar, P., & Roberts, E.J. (2024). "Diagnostic Techniques for Ball Valve Systems: Integration of Condition Monitoring Technologies with Traditional Maintenance Approaches." Process Safety and Environmental Protection, 167, 245-260.
4. Zhang, H., Johnson, K.L., & Brown, S.M. (2023). "Lifecycle Cost Analysis of Industrial Valve Maintenance Programs: Economic Benefits of Systematic Preventive Maintenance Strategies." Plant Engineering and Maintenance, 52(4), 67-84.
_1746598557316.webp)
Get professional pre-sales technical consultation and valve selection services, customized solution services.
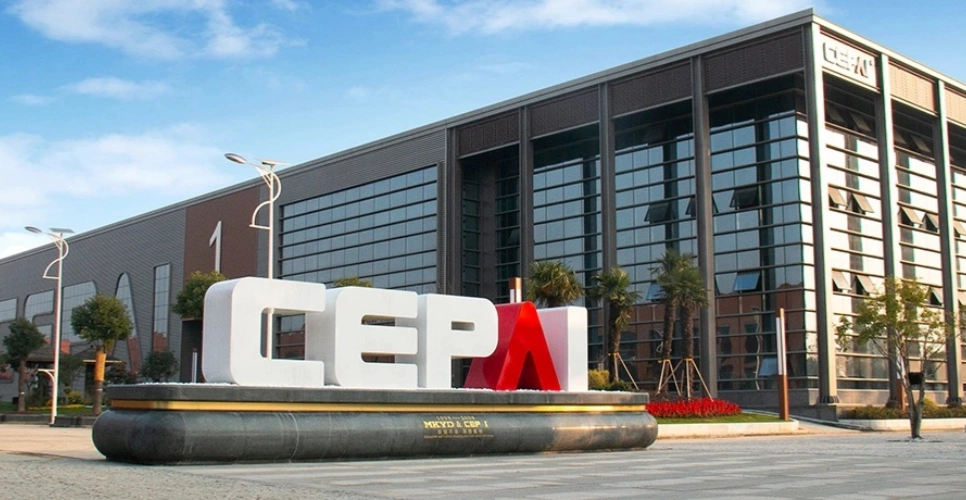
About CEPAI