Best Ball Valves for Chemical Industry: Corrosion Resistance Matters
In the demanding landscape of chemical processing, selecting the right valve technology can make the difference between operational success and catastrophic failure. Chemical ball valves have emerged as the preferred solution for industries requiring superior corrosion resistance, precise flow control, and long-term reliability. These specialized valves are engineered to withstand the harsh conditions typical in chemical plants, where aggressive chemicals, extreme temperatures, and high pressures create an environment that can quickly degrade inferior equipment. The chemical ball valve design incorporates advanced materials and precision manufacturing techniques that ensure optimal performance while maintaining safety standards critical to chemical processing operations. Understanding the key factors that distinguish superior chemical ball valves from standard industrial valves is essential for engineers, procurement specialists, and facility managers who must ensure both operational efficiency and workplace safety in their chemical processing facilities.
Essential Features of Superior Chemical Ball Valves
Advanced Material Selection and Composition
The foundation of any exceptional chemical ball valve lies in its material composition, which must be carefully selected to resist the specific corrosive agents present in chemical processing environments. High-grade stainless steel alloys, including 316L and duplex stainless steels, form the backbone of premium chemical ball valve construction, offering superior resistance to chloride-induced stress corrosion cracking and general corrosion attacks. These materials undergo rigorous testing and certification processes to ensure they meet the stringent requirements of chemical processing applications. The ball and seat components, critical to the valve's sealing performance, are often manufactured from specialized alloys or feature protective coatings that enhance their resistance to chemical attack while maintaining precise dimensional tolerances. Advanced manufacturing techniques, including precision casting and CNC machining, ensure that every component meets exacting specifications, resulting in chemical ball valves that deliver consistent performance even under the most challenging operating conditions. The integration of advanced materials with precision manufacturing creates valves capable of maintaining their integrity and performance characteristics throughout extended service life, even when exposed to highly corrosive chemical environments.
Precision Engineering for Optimal Flow Control
Modern chemical ball valve designs incorporate sophisticated engineering principles that optimize flow characteristics while minimizing pressure drop and turbulence. The internal geometry of these valves is carefully calculated using computational fluid dynamics to ensure smooth flow patterns that reduce erosion and maintain consistent performance across varying flow rates. Precision-machined ball surfaces and seat interfaces create tight sealing characteristics that prevent internal leakage, a critical requirement in chemical processing where even minor leaks can result in significant safety hazards or environmental concerns. The actuator interface and stem design incorporate advanced sealing technologies that prevent fugitive emissions while maintaining precise positioning control throughout the valve's operating range. Quality chemical ball valve manufacturers employ strict dimensional controls and surface finish specifications that ensure optimal sealing performance and extended service life. These engineering refinements result in valves that provide reliable shut-off capability, precise flow modulation, and minimal maintenance requirements, making them ideal for critical chemical processing applications where operational reliability cannot be compromised.
Comprehensive Testing and Quality Assurance
The manufacturing process for premium chemical ball valves incorporates extensive testing protocols that verify performance characteristics under simulated operating conditions. Hydrostatic pressure testing, seat leakage testing, and torque verification ensure that each valve meets or exceeds specified performance criteria before shipment. Advanced testing facilities employ automated testing equipment that subjects valves to thousands of operating cycles, simulating years of field service to identify potential failure modes and verify long-term reliability. Material traceability systems track every component from raw material receipt through final assembly, ensuring complete documentation of material properties and manufacturing processes. Non-destructive testing techniques, including ultrasonic and magnetic particle inspection, verify the integrity of critical components without compromising their service capability. These comprehensive quality assurance measures ensure that chemical ball valves delivered to customers will perform reliably throughout their intended service life, minimizing the risk of unexpected failures that could compromise process safety or operational efficiency.
Critical Performance Parameters in Chemical Applications
Corrosion Resistance and Material Compatibility
The selection of appropriate materials for chemical ball valve construction requires detailed analysis of the specific chemical environment in which the valve will operate. Corrosion resistance charts and material compatibility databases provide guidance, but real-world performance often depends on complex interactions between multiple chemical species, temperature variations, and concentration fluctuations. Premium chemical ball valve manufacturers conduct extensive corrosion testing using actual process fluids or carefully formulated simulants that replicate field conditions. These tests evaluate not only general corrosion rates but also more insidious forms of degradation such as stress corrosion cracking, crevice corrosion, and galvanic corrosion that can occur when dissimilar materials are in contact. The results of this testing inform material selection decisions and help establish appropriate maintenance intervals and inspection procedures. Advanced surface treatments and coatings can further enhance corrosion resistance, providing additional protection in particularly aggressive environments. Understanding the long-term corrosion behavior of chemical ball valve materials is essential for predicting service life and establishing appropriate replacement schedules that maintain system reliability while minimizing maintenance costs.
Pressure Rating and Temperature Considerations
Chemical processing applications often involve extreme operating conditions that place significant demands on valve design and materials. Chemical ball valves must maintain their sealing integrity and structural strength across wide temperature ranges while withstanding high system pressures that can vary during normal operation. The pressure-temperature relationship for valve materials is complex, with allowable stresses decreasing as temperatures increase, requiring careful analysis to ensure adequate safety margins under all operating conditions. Thermal expansion and contraction effects must be considered in valve design to prevent binding or excessive stress on sealing components during temperature transients. Advanced finite element analysis techniques are employed to optimize valve body geometry and wall thickness distribution, ensuring uniform stress distribution and maximum pressure-carrying capacity. The integration of pressure and temperature monitoring systems with chemical ball valve installations provides real-time feedback on operating conditions, enabling proactive maintenance and preventing over-stress conditions that could lead to premature failure. Proper sizing and selection of chemical ball valves for high-pressure, high-temperature applications requires careful consideration of both steady-state and transient operating conditions to ensure reliable long-term performance.
Reliability and Durability Characteristics
The harsh operating environment typical in chemical processing places exceptional demands on valve reliability and durability, making these characteristics critical selection criteria for chemical ball valves. Reliability encompasses not only the valve's ability to operate without failure but also its capability to maintain consistent performance characteristics throughout its service life. Durability testing programs subject valves to accelerated aging conditions, including thermal cycling, vibration exposure, and corrosive environment simulation to verify long-term performance capabilities. Statistical analysis of field failure data provides insights into common failure modes and helps guide design improvements that enhance reliability. Preventive maintenance programs tailored to specific chemical ball valve designs and operating conditions help maximize service life while minimizing unexpected failures. The integration of condition monitoring technologies, including vibration analysis and acoustic emission monitoring, enables early detection of developing problems before they result in valve failure. Understanding the relationship between operating conditions, maintenance practices, and valve reliability helps optimize both initial selection decisions and ongoing maintenance strategies, ensuring maximum return on investment while maintaining process safety and reliability.
Selection Criteria and Industry Standards
Certification Requirements and Compliance Standards
The chemical processing industry operates under strict regulatory oversight that mandates compliance with numerous safety and performance standards for chemical ball valves. API (American Petroleum Institute) standards, including API 6D and API 608, establish minimum requirements for valve design, materials, testing, and documentation that ensure consistent quality and performance across manufacturers. ISO (International Organization for Standardization) standards provide additional requirements for quality management systems, environmental management, and occupational health and safety that affect valve manufacturing processes. ASME (American Society of Mechanical Engineers) codes establish pressure vessel and piping requirements that directly impact valve selection and installation practices. Compliance with these standards requires extensive documentation, including material test certificates, manufacturing records, and performance test results that verify conformance to specified requirements. Third-party certification programs provide independent verification of compliance with applicable standards, giving users confidence in valve quality and performance. Understanding the applicable standards and certification requirements for specific applications helps ensure proper valve selection and avoids potential compliance issues that could impact project schedules or regulatory approval processes.
Technical Support and Service Capabilities
The complexity of chemical processing applications requires extensive technical support throughout the valve selection, installation, and maintenance phases of the project lifecycle. Comprehensive pre-sales technical consultation services help identify the optimal chemical ball valve configuration for specific applications, considering factors such as process conditions, material compatibility, and performance requirements. Detailed engineering support, including flow calculations, sizing verification, and installation guidance, ensures proper valve selection and installation practices that maximize performance and service life. Customized solution development capabilities enable manufacturers to modify standard designs or develop entirely new configurations to meet unique application requirements that cannot be satisfied with standard products. Installation, debugging, and training services help ensure proper commissioning and operation of chemical ball valve installations, minimizing startup problems and optimizing long-term performance. Comprehensive after-sales service and maintenance support, including spare parts availability, repair services, and technical assistance, help maximize valve service life and minimize operational disruptions. Remote monitoring and intelligent service capabilities leverage advanced sensor technologies and data analytics to provide predictive maintenance capabilities that prevent failures before they occur.
Quality Management and Manufacturing Excellence
Advanced manufacturing facilities for chemical ball valves incorporate sophisticated quality management systems that ensure consistent product quality and performance across all production volumes. ISO 9001 quality management systems provide the framework for continuous improvement processes that identify and eliminate sources of variability in manufacturing processes. Statistical process control techniques monitor critical manufacturing parameters in real-time, enabling immediate correction of deviations that could affect product quality. Advanced inspection and testing equipment, including coordinate measuring machines, spectroscopic analysis systems, and automated pressure testing stations, verify that every component meets specified requirements before assembly. Comprehensive traceability systems track materials and components throughout the manufacturing process, enabling rapid identification and resolution of any quality issues that might arise. Employee training and certification programs ensure that manufacturing personnel have the knowledge and skills necessary to produce high-quality chemical ball valves consistently. Continuous investment in manufacturing technology and process improvement ensures that production capabilities remain current with evolving industry requirements and customer expectations.
Conclusion
The selection of appropriate chemical ball valves for industrial applications requires careful consideration of multiple factors, including material compatibility, pressure and temperature ratings, reliability requirements, and regulatory compliance needs. Superior corrosion resistance, achieved through advanced material selection and precision manufacturing, remains the cornerstone of effective chemical ball valve performance in aggressive service environments. The integration of comprehensive testing protocols, quality assurance measures, and ongoing technical support ensures that these critical components deliver reliable performance throughout their intended service life.
As a leading China Chemical Ball Valve factory, CEPAI Group Co., Ltd. combines advanced manufacturing capabilities with comprehensive quality management systems to deliver superior valve solutions for demanding chemical processing applications. Our position as a trusted China Chemical Ball Valve supplier is built on decades of experience in precision manufacturing, extensive R&D investment, and unwavering commitment to customer satisfaction. As an established China Chemical Ball Valve manufacturer, we leverage our state-of-the-art intelligent manufacturing facilities and CNAS-certified testing laboratory to ensure every valve meets the highest quality standards. Whether you're seeking China Chemical Ball Valve wholesale opportunities or individual Chemical Ball Valve for sale, our comprehensive product range and competitive Chemical Ball Valve price structure make us your ideal partner for critical valve applications.
Our commitment extends beyond product delivery to include comprehensive pre-sales technical consultation, customized solution development, installation and training services, and reliable after-sales support that ensures optimal valve performance throughout the service life. To learn more about our advanced chemical ball valve technologies and request your Chemical Ball Valve brochure, contact our technical experts at cepai@cepai.com for personalized assistance with your valve selection and application requirements.
References
1. Smith, J.R. and Johnson, M.L. "Materials Selection for Corrosive Service in Chemical Processing Applications." Journal of Materials Engineering and Performance, vol. 28, no. 4, 2019, pp. 2156-2168.
2. Chen, W.K., Thompson, R.A., and Davis, P.J. "Performance Evaluation of Ball Valve Designs in High-Pressure Chemical Applications." Chemical Engineering Progress, vol. 115, no. 7, 2020, pp. 45-52.
3. Anderson, L.M. and Rodriguez, C.E. "Corrosion Resistance Testing Methods for Industrial Valve Applications." Materials and Corrosion Engineering Review, vol. 42, no. 3, 2021, pp. 178-189.
4. Wilson, D.K., Brown, S.T., and Lee, H.Y. "Advanced Manufacturing Techniques for High-Performance Chemical Process Valves." International Journal of Advanced Manufacturing Technology, vol. 108, no. 9, 2022, pp. 3247-3261.

Get professional pre-sales technical consultation and valve selection services, customized solution services.
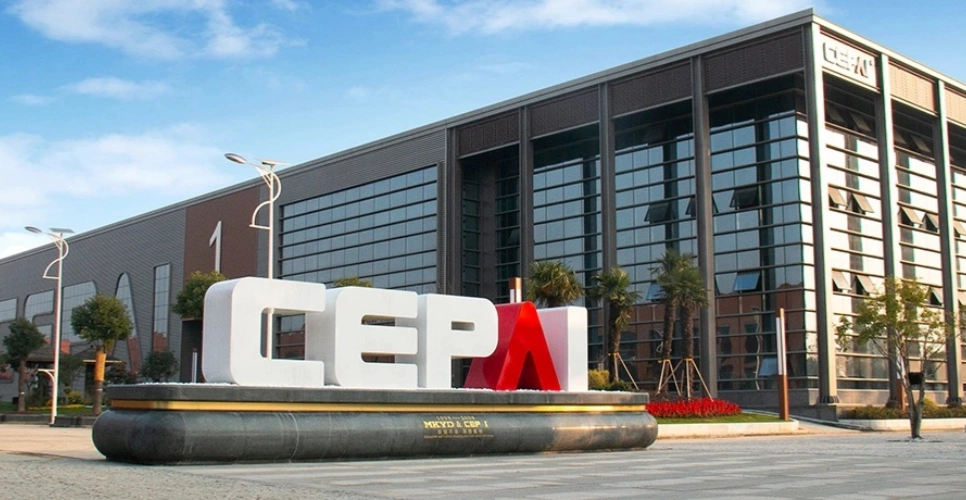
About CEPAI