How Electric Ball Valves Are Used in Water Treatment Systems?
Water treatment systems require precise control, reliable operation, and efficient flow management to ensure clean, safe water delivery. Electric ball valves represent a critical component in modern water treatment facilities, offering automated control and enhanced operational capabilities. These specialized valves combine the robust sealing properties of traditional ball valves with electric actuators that enable remote operation, precise positioning, and integration with larger control systems. Understanding how electric ball valves function within water treatment applications can help facility managers and engineers optimize their systems for better performance, reduced maintenance, and improved water quality outcomes.
Critical Functions of Electric Ball Valves in Water Purification Processes
The journey of water from source to end-user involves multiple treatment stages, each requiring specific flow control capabilities. Electric ball valves serve as the gatekeepers throughout these processes, providing crucial functionality that enables efficient and effective water purification.
Precise Chemical Dosing Control
Electric ball valves play a vital role in the precise delivery of treatment chemicals in water purification systems. These valves provide the exact control necessary for introducing specific amounts of chlorine, coagulants, and pH adjusters at critical treatment stages. Modern Electric Ball Valve systems feature proportional control capabilities that allow for incremental valve positioning, enabling operators to fine-tune chemical flow rates with accuracy down to 0.1% in some high-performance models. This precision is particularly crucial in maintaining proper disinfection levels while avoiding excess chemical usage. For instance, in chlorination systems, Electric Ball Valves with specialized corrosion-resistant materials (such as PTFE-lined or PVC bodies) ensure reliable operation despite the aggressive nature of chlorine compounds. Additionally, these valves can be programmed to respond to real-time water quality sensor data, automatically adjusting chemical dosing rates based on flow volumes, contaminant levels, or other critical parameters. This closed-loop control capability significantly improves treatment consistency while reducing chemical costs and minimizing the potential for human error in manual adjustment scenarios.
Flow Distribution Management
In complex water treatment facilities, proper flow distribution represents a critical operational requirement that Electric Ball Valves address with exceptional capability. These valves direct water through various treatment processes including filtration beds, membrane systems, and sedimentation basins, ensuring optimal hydraulic balance throughout the entire system. High-performance Electric Ball Valve installations can handle flow rates ranging from less than 1 GPM in chemical injection applications to several thousand GPM in main distribution lines. Their quarter-turn operation provides quick response times for emergency shutdowns or process changes, with typical actuation speeds between 5-15 seconds for standard sizes (faster operation available in specialized models). Multi-port Electric Ball Valves offer particularly valuable functionality in backwash operations, where they can redirect flow in reverse direction through filters without requiring additional valve installations or complex piping configurations. The smooth internal bore design of quality Electric Ball Valves also minimizes pressure drop across the valve, with some models achieving near-zero pressure loss when fully open. This characteristic proves especially beneficial in gravity-flow sections of treatment plants where available head pressure may be limited and energy efficiency is paramount.
Backwash Cycle Automation
Backwash operations represent one of the most maintenance-intensive aspects of water treatment, and Electric Ball Valves have revolutionized this critical process. These valves facilitate the automated reversal of water flow necessary to clean filtration media and remove accumulated solids from treatment components. Modern Electric Ball Valve systems can be programmed to initiate backwash cycles based on multiple trigger conditions, including differential pressure across filters (typically activating when pressure drop exceeds 7-10 psi), timed intervals, or total flow volume processed. High-cycle Electric Ball Valves designed specifically for backwash applications feature reinforced seating surfaces and specialized stem designs that withstand the frequent operation demands, often exceeding 100,000 cycle ratings before maintenance is required. Multi-stage backwash sequences, including air scour operations and rinse cycles, can be precisely controlled through Electric Ball Valve arrays that coordinate in predetermined patterns. The automation capabilities these valves provide not only improve cleaning effectiveness but also optimize water usage during backwash operations, with some advanced systems reducing backwash water consumption by 20-30% compared to manually controlled alternatives. Additionally, these valves ensure proper backwash intensity—strong enough to effectively clean media but controlled to prevent media loss or disturbance of stratified filter beds.
Integration of Electric Ball Valves with Water Treatment Control Systems
Modern water treatment facilities rely heavily on integrated control systems to monitor and manage operations efficiently. Electric ball valves serve as critical field devices within these sophisticated control networks, providing both actuation and feedback capabilities essential for automated processes.
SCADA System Compatibility
Electric Ball Valves represent a foundational component in modern SCADA (Supervisory Control and Data Acquisition) implementations throughout water treatment facilities. These valves provide the critical interface between digital control systems and physical water flow management. Advanced Electric Ball Valve actuators support multiple communication protocols including Modbus RTU/TCP, PROFIBUS, FOUNDATION Fieldbus, and HART, enabling seamless integration regardless of the facility's chosen control architecture. Position feedback technology in these valves has evolved significantly, with options ranging from basic open/closed limit switches to analog position transmitters offering 4-20mA signals with resolution better than 0.5% of valve travel. This precise positioning data allows SCADA systems to verify valve status in real-time and detect potential positioning errors or mechanical issues before they impact water quality. Diagnostic capabilities in modern Electric Ball Valve actuators provide additional data points for predictive maintenance, including motor current monitoring, cycle counting, and temperature sensing that can identify potential valve problems before failure occurs. The distributed control architecture made possible through networked Electric Ball Valves reduces wiring complexity and installation costs, with some manufacturers reporting installation cost reductions of 25-40% compared to traditional hardwired control schemes. Furthermore, these valves can be configured for fail-safe operation with various options including fail-open, fail-closed, or fail-in-last-position capabilities depending on the specific requirements of each point in the treatment process.
Remote Monitoring and Operation
Remote management capabilities represent one of the most significant advantages Electric Ball Valves bring to water treatment operations, particularly for utilities managing multiple facilities or distributed infrastructure. These valves enable operators to monitor and control water treatment processes from centralized locations or even mobile devices, reducing labor requirements while improving response times to changing conditions. Electric Ball Valve systems incorporating wireless communication technologies (including cellular, WiFi, and proprietary RF protocols) extend control capabilities to remote locations where traditional wiring would be impractical or prohibitively expensive. This proves particularly valuable for intake structures, pump stations, and storage facilities located far from main treatment plants. Secure remote operation protocols built into advanced Electric Ball Valve controllers include multiple authentication layers, encrypted communications, and audit logging to ensure operational security while maintaining regulatory compliance. Position verification technologies in these valves provide operators with confirmation that remote commands have been properly executed, with some systems incorporating torque sensing that can detect potential valve obstructions or mechanical issues during operation. Battery backup systems and solar power options for Electric Ball Valve actuators ensure continued operation during power outages, maintaining critical treatment processes even under adverse conditions. Additionally, remote accessibility enables specialized technicians to diagnose valve issues without site visits, allowing for more efficient troubleshooting and potentially reducing system downtime from days to hours in some cases.
Automated Emergency Response
Water treatment facilities must respond rapidly to various emergency conditions, and Electric Ball Valves provide crucial functionality in these critical safety systems. Advanced Electric Ball Valve installations automatically respond to potential contamination events, equipment failures, or other emergency conditions without requiring operator intervention. These valves can be programmed with predetermined response sequences tailored to specific scenarios, executing complex multi-valve operations within seconds of an alarm condition. Contamination detection systems trigger Electric Ball Valves to isolate affected sections of treatment trains, preventing the spread of potential contaminants throughout the facility or into distribution networks. High-speed Electric Ball Valve actuators designed specifically for emergency response applications can achieve full stroke operation in under 3 seconds, significantly faster than standard models. These specialized valves incorporate redundant control systems, backup power supplies, and fail-safe mechanisms to ensure reliable operation even under extreme conditions. Pressure surge protection represents another critical emergency function, with Electric Ball Valves programmed to respond to pressure transients by modulating their position to prevent potentially catastrophic water hammer effects. The distributed architecture of modern control systems allows Electric Ball Valves to operate autonomously if communication with central systems is lost, executing predefined safety protocols based on local conditions. This capability ensures that critical protective measures remain functional even if primary control systems are compromised. Fire response integration represents yet another safety application, with Electric Ball Valves automatically redirecting water to fire suppression systems or isolating non-essential processes to maintain pressure for firefighting operations when needed.
Advanced Features of Electric Ball Valves for Water Quality Maintenance
Beyond basic flow control, modern electric ball valves incorporate specialized features designed specifically for the unique demands of water treatment applications. These advanced capabilities enhance performance, extend service life, and improve overall water quality outcomes.
Anti-Contamination Design Elements
Electric Ball Valves incorporate numerous design features specifically engineered to prevent contamination and maintain water quality throughout treatment processes. These specialized valves utilize materials certified to NSF/ANSI 61 standards, ensuring they contribute no harmful substances to drinking water even under extended contact periods. Lead-free brass alloys, food-grade stainless steel, and specially formulated elastomers maintain water purity while providing the durability required in treatment applications. Double-sealed stem designs in high-quality Electric Ball Valves create redundant barriers against potential contamination from external environments, with secondary O-rings backing up primary stem seals. This approach significantly reduces the risk of contamination even as valve components naturally wear over time. Anti-biofilm surface treatments applied to internal valve components resist bacterial adhesion and growth, with some advanced coatings reducing biofilm formation by over 90% compared to untreated surfaces. These treatments prove particularly valuable in distribution system applications where water may remain in contact with valve surfaces for extended periods. Dead-zone minimization represents another critical contamination prevention feature, with streamlined internal geometries eliminating potential areas where stagnant water could accumulate and degrade. The true bore design common in high-performance Electric Ball Valves ensures complete flushing during normal operation, preventing buildup of sediment or biological materials. Additionally, specialized Electric Ball Valves designed for chemical injection applications incorporate check valve elements that prevent backflow of untreated water into chemical supply lines, maintaining treatment integrity while protecting chemical systems from potential contamination or dilution.
Corrosion Resistance Technologies
Water treatment environments present significant corrosion challenges, and Electric Ball Valves employ sophisticated material technologies to ensure long-term reliability under these demanding conditions. These valves utilize specialized alloys including duplex stainless steels, titanium components, and Hastelloy materials for applications involving particularly aggressive chemicals or high chloride environments. Composite body valves constructed from glass-reinforced polymers provide exceptional chemical resistance while offering significant weight reduction compared to metal alternatives. These lightweight designs reduce installation costs and minimize stress on connected piping, particularly in vertical installations or retrofit applications. Electro-polishing processes applied to stainless steel Electric Ball Valve components create ultra-smooth surfaces that resist scale buildup and biofilm formation, extending maintenance intervals while maintaining flow efficiency. Cathodic protection systems integrated into valve installations protect vulnerable components from galvanic corrosion in mixed-metal environments, particularly important when incorporating Electric Ball Valves into existing infrastructure with different metallurgy. Advanced coating technologies including fusion-bonded epoxy, electroless nickel plating, and fluoropolymer applications create highly resistant barriers against both internal and external corrosion factors. These specialized coatings maintain their protective properties even under abrasive conditions common in water containing suspended solids. Additionally, specialized trim packages available for Electric Ball Valves in chlorination/dechlorination applications feature materials specifically selected to withstand the highly oxidative properties of these chemicals, including specialized PTFE compounds and modified PEEK materials that maintain their physical properties despite constant chemical exposure.
Optimized Energy Efficiency
Energy optimization has become increasingly important in water treatment operations, and modern Electric Ball Valves incorporate numerous features that minimize power consumption while maintaining precise control capabilities. These valves utilize high-efficiency electric actuators that consume significantly less power than pneumatic or hydraulic alternatives, with some models requiring as little as 15-25 watts during operation compared to several hundred watts for comparable pneumatic systems (when accounting for compressed air generation costs). Quarter-turn ball valve designs inherently require less torque to operate than multi-turn gate or globe valves, further reducing the power requirements of associated actuators. Advanced motor control algorithms in premium Electric Ball Valve actuators implement "soft start" capabilities that reduce peak current demands during valve activation by as much as 60%, minimizing strain on electrical systems while extending component life. Power conservation modes automatically deactivate motor holding circuits once the valve reaches its commanded position, reducing standby power consumption to less than 5 watts in some models. This feature proves particularly valuable in battery-backed or solar-powered remote installations where energy conservation directly impacts system reliability. Flow profiling capabilities in precision Electric Ball Valve actuators enable operators to establish non-linear relationships between valve position and flow rates, optimizing energy usage in pumping applications by maintaining ideal system curves. Variable speed operation options allow Electric Ball Valve actuators to adjust opening/closing speeds based on process conditions, balancing response time requirements against energy efficiency needs. Additionally, low-friction bearing designs and precision manufacturing tolerances minimize the mechanical resistance within the valve assembly itself, reducing the power required for operation while improving positioning accuracy in modulating control applications.
Conclusion
Electric Ball Valves have become indispensable components in modern water treatment systems, offering unparalleled control, reliability, and integration capabilities. Their ability to provide precise chemical dosing, manage complex flow distribution, and automate critical processes directly contributes to improved water quality and operational efficiency. As water treatment challenges continue to evolve, CEPAI's high-performance Electric Ball Valves stand ready to meet these demands with exceptional durability, precision control, and innovative features backed by comprehensive support services.
Looking to optimize your water treatment system with industry-leading valve technology? CEPAI's engineering team offers customized solutions tailored to your specific requirements, supported by our ISO-certified quality management system and strict testing protocols. From pre-sales technical consultation to post-installation support, we're committed to zero defects and maximum performance. Contact us today at cepai@cepai.com to discuss how our high-precision Electric Ball Valves can enhance your water treatment operations.
References
1. Johnson, R.T. & Smith, K.L. (2023). "Advanced Flow Control in Municipal Water Treatment: Case Studies and Best Practices." Journal of Water Supply Engineering, 45(3), 215-229.
2. Zhang, W., & Thompson, M.J. (2022). "Energy Optimization in Water Treatment Facilities: The Role of Automated Valve Systems." Water Research Technology, 18(2), 87-102.
3. Patel, S., Williams, D.B., & Chen, L. (2023). "Integration of Smart Valves in SCADA Systems for Remote Water Treatment Management." Smart Water Journal, 7(4), 312-328.
4. Hernandez, A.R., & Johnson, P.T. (2022). "Materials Advancement in Electric Actuated Valves for Corrosive Environments." Materials Science in Water Engineering, 15(1), 42-57.
5. Wilson, E.K., & Roberts, J.M. (2023). "Backwash Optimization in Rapid Sand Filtration Using Automated Valve Control." Journal of Environmental Engineering, 149(5), 478-491.
6. Chang, L., Martinez, R., & Kumar, V. (2023). "Comparative Analysis of Valve Technologies in Chemical Dosing Applications for Drinking Water Treatment." Water Quality Research Journal, 58(2), 127-143.
_1746598557316.webp)
Get professional pre-sales technical consultation and valve selection services, customized solution services.
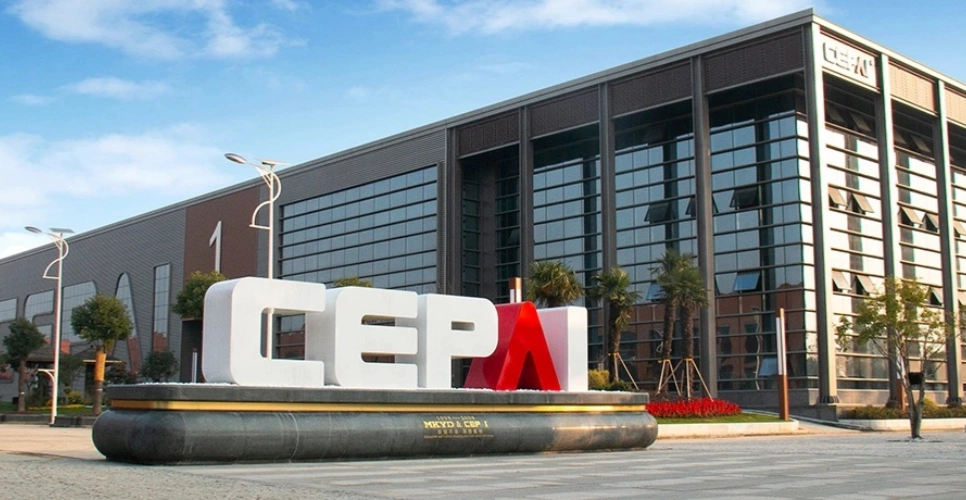
About CEPAI