Step-by-Step Electric Ball Valve Installation Guide
Installing an electric ball valve correctly is crucial for ensuring optimal performance, longevity, and safety in your fluid control systems. Whether you're working on industrial applications, petrochemical processes, or power generation systems, proper installation techniques are essential. This comprehensive guide will walk you through the entire installation process of electric ball valves, providing professional insights and best practices developed from CEPAI Group's extensive experience as a high-tech enterprise specializing in high-performance fluid control devices.
Pre-Installation Preparation and Planning
Before jumping into the physical installation, proper preparation is crucial for a successful electric ball valve installation. This section will guide you through the essential preliminary steps.
System Requirement Analysis
When preparing for electric ball valve installation, conducting a thorough system requirement analysis is the first critical step that should never be overlooked. This analysis serves as the foundation for your entire installation project and determines whether the electric ball valve will function as intended within your specific system. Begin by carefully evaluating your system's operating parameters, including the maximum and minimum pressure ratings, temperature ranges, and flow rates. These factors are crucial because electric ball valves are designed with specific operational limits, and selecting a valve that cannot withstand your system's conditions may lead to premature failure or safety hazards. Additionally, determine the fluid type that will flow through the valve, as certain materials in electric ball valves may react with or degrade when exposed to particular substances. Consider the chemical compatibility between the valve components and the process fluid to prevent corrosion or contamination issues. Environmental factors like ambient temperature, humidity, and potential exposure to corrosive atmospheres also influence valve selection and installation requirements. For applications in areas with specific certifications or compliance requirements (such as ATEX zones or SIL-rated systems), ensure your electric ball valve meets these standards. CEPAI's electric ball valves come with various certifications including SIL certification and CE marking, making them suitable for demanding industrial environments where safety and reliability are paramount.
Valve Selection and Verification
Selecting the appropriate electric ball valve from the vast array of options available is crucial for ensuring optimal performance and longevity. Start by examining the valve specifications against your system requirements identified during the analysis phase. The valve size must be precisely matched to your pipeline diameter and flow requirements - oversized valves may cause inefficient operation while undersized valves can create excessive pressure drops and flow restrictions. Pay particular attention to the valve's pressure and temperature ratings to ensure they provide sufficient margin above your system's normal operating conditions. Electric ball valves come with different actuation mechanisms - electric motors that operate at various voltages (typically 24V, 110V, or 220V) - so verify compatibility with your power supply and control systems. CEPAI offers electric ball valves with various control interfaces including 4-20mA, HART protocol, PROFIBUS, and Modbus, providing flexibility for integration with modern industrial automation systems. The valve body and seat materials deserve careful consideration - stainless steel, carbon steel, and specialty alloys each have different corrosion resistance properties and temperature limitations. For applications with high cycling requirements, select electric ball valves designed for frequent operation, with enhanced actuator durability and ball/seat combinations that minimize wear. Before finalizing your selection, verify that the valve's flow characteristics (full port, reduced port, or characterized) match your process control needs. Lastly, confirm that your chosen electric ball valve comes with proper certification documentation, particularly important for critical applications in industries like oil and gas, chemical processing, or power generation.
Tools and Component Preparation
Proper preparation of tools and components is essential for a smooth and efficient electric ball valve installation process. Begin by assembling all the necessary tools, which typically include adjustable wrenches, pipe wrenches, a level, measuring tape, thread sealant or gasket material, electrical tools (wire strippers, multimeter, screwdrivers), and personal protective equipment appropriate for your environment. For precision installations, consider having a torque wrench on hand to ensure proper tightening of connections without over-stressing components. Carefully unpack and inspect the electric ball valve, checking for any signs of damage that might have occurred during shipping - pay particular attention to the actuator housing, electrical connections, and any visible parts of the valve body and ends. This inspection is crucial because even minor damage can affect the valve's performance or lead to leaks. Verify that the valve's direction of flow is marked clearly and matches your intended installation orientation - many electric ball valves have directional flow requirements that must be respected for proper operation. Examine all included components and compare them against the packing list to ensure nothing is missing, particularly focusing on mounting hardware, connectors, and any control interface components that should accompany the valve. CEPAI's electric ball valves come with detailed component inventories and clear markings, reducing the possibility of installation errors. If your installation requires additional components like reducers, flanges, or special fittings, have these prepared and inspected alongside the valve. Lastly, familiarize yourself with the valve's electrical requirements and control interface specifications by reviewing the manufacturer's documentation thoroughly, noting any specific power requirements, signal types, or termination details that will be important during the installation process.
Installation and Connection Procedures
With proper preparation complete, you can now proceed with the physical installation and connection of your electric ball valve.
Mechanical Installation Steps
The mechanical installation of an electric ball valve requires precision and attention to detail to ensure proper functionality and prevent future issues. Begin by shutting down the system and properly relieving any pressure in the pipeline where the valve will be installed. This safety step is critical to prevent accidents or injuries during installation. If you're working on an existing system, clean the pipe ends thoroughly to remove any debris, old sealant, or corrosion that could interfere with proper sealing. For threaded connections, apply an appropriate thread sealant (PTFE tape or pipe compound) according to the manufacturer's recommendations, being careful not to over-apply which could contaminate the valve's internal components. When using PTFE tape, wrap it clockwise around the male threads (when viewing the pipe end-on) to prevent the tape from unwinding during insertion. For flanged electric ball valves, ensure that gaskets are properly centered and that flange faces are parallel before inserting bolts. Install the electric ball valve in the pipeline, paying strict attention to the flow direction indicators on the valve body – improper orientation is a common installation error that can severely impact performance or cause premature failure of the valve. CEPAI's electric ball valves feature clear directional markings to minimize installation errors. When tightening connections, follow a cross-pattern sequence for flanged connections to ensure even gasket compression, and use a calibrated torque wrench to achieve the recommended torque values specified in the valve's documentation. Proper support of the valve is critical, especially for larger or heavier electric ball valves – install appropriate pipe supports near the valve to prevent stress on the valve body and connected piping which could lead to misalignment over time. Once mechanically installed, verify that the valve's actuator has sufficient clearance for operation and maintenance access, considering both the space needed for the actuator's movement and any future service requirements.
Electrical Wiring and Control Integration
Proper electrical wiring and control system integration are critical aspects of electric ball valve installation that directly impact performance reliability and operational safety. Begin by verifying that all power sources are turned off and locked out according to proper safety procedures before attempting any electrical connections. Carefully review the wiring diagram provided with your CEPAI electric ball valve, noting the specific voltage requirements, control signal types, and terminal designations. Most electric ball valves require both power connections for the actuator motor and separate control signal wiring for position feedback and operational commands. When routing the electrical cables, use appropriate conduit or cable trays to protect the wiring from environmental factors and potential physical damage. Always maintain separation between high-voltage power cables and low-voltage control signal cables to prevent electromagnetic interference that could disrupt valve operation or position feedback signals. Make all electrical connections according to the manufacturer's specifications, using the proper wire gauge for power connections and shielded cable for sensitive control signals. Ensure that all connections are securely tightened and properly terminated with the appropriate connectors or ferrules. For connections in potentially wet or corrosive environments, apply dielectric grease or suitable sealant to prevent moisture ingress and corrosion. When integrating the valve with your control system, configure the appropriate communication parameters if your electric ball valve uses digital communication protocols like HART, PROFIBUS, or Modbus. CEPAI offers electric ball valves with various communication options to suit different control architectures. For analog control systems, ensure that the control signal range (typically 4-20mA) is properly calibrated to match the valve's full range of motion. Finally, implement proper grounding according to electrical codes and manufacturer recommendations to prevent ground loops and ensure electrical safety, taking special care in hazardous area installations where proper grounding is essential for intrinsic safety.
Actuator Calibration and Initial Setup
Proper calibration and initial setup of the electric ball valve actuator are essential steps that determine the valve's operational accuracy and longevity. Begin by reviewing the actuator manufacturer's documentation to understand the specific calibration procedures and requirements for your particular model. Before applying power to the actuator, manually check that the valve moves freely through its full range of motion without binding or unusual resistance – this preliminary check can identify mechanical issues that might damage the actuator if not addressed. Once verified, connect temporary power to the actuator according to the specified voltage requirements and observe the initial power-up sequence, noting any error indications or unusual behaviors. CEPAI's electric ball valves include diagnostic LEDs that can identify common issues during startup. Access the actuator's calibration mode according to the manufacturer's instructions, which typically involves setting the open and closed position limits. This process ensures that the actuator applies the appropriate torque and stops at the correct positions without straining against mechanical stops. For electric ball valves with modulating control capabilities, calibrate the control signal range (typically 4-20mA or 0-10V) to correspond precisely to the valve's full range of motion. Verify that the valve responds correctly to control signals throughout the entire operating range, moving smoothly and positioning accurately at various setpoints. Configure any additional parameters specific to your application, such as fail-safe positions (whether the valve should move to open, closed, or remain in position upon power loss), action upon signal loss, or anti-water hammer functionality if available. Test the manual override feature if equipped, ensuring it functions properly for emergency situations. Finally, verify that any position feedback signals being sent to your control system accurately reflect the valve's actual position throughout its range of travel. CEPAI's advanced electric ball valves include high-resolution position feedback that maintains calibration even after power cycles, providing consistent performance in critical applications.
Testing, Troubleshooting, and Maintenance
After installation, proper testing, troubleshooting, and ongoing maintenance are essential for ensuring reliable performance of your electric ball valve.
Leak Testing and Pressure Verification
Comprehensive leak testing and pressure verification are critical procedures that should never be overlooked after installing an electric ball valve, as they directly impact system integrity and operational safety. Begin with a visual inspection of all connections, focusing on joints, gaskets, and seals where leaks most commonly occur. For precise leak detection, apply a soap solution or specialized leak detection fluid to all connection points and observe for bubble formation, which indicates gas leakage. This method is particularly effective for gas applications where leaks may not be visually obvious. For liquid applications, dry all connections thoroughly and observe for any moisture accumulation that could indicate seepage. When conducting pressure tests, always follow a methodical approach starting with low pressure and gradually increasing to the system's normal operating pressure, never exceeding the valve's rated maximum. During pressurization, monitor pressure gauges for any unexpected drops that could indicate leakage. CEPAI's electric ball valves undergo rigorous factory testing, but field verification remains essential due to the variables introduced during installation. For critical applications, consider implementing both low-pressure and high-pressure hold tests, where the system is pressurized and isolated for a specified period (typically 1-24 hours depending on the application criticality) to verify that pressure remains stable. Document the test results, including the test pressure, duration, and any observations, as this information may be valuable for future troubleshooting or warranty claims. For electric ball valves in high-purity or sanitary applications, additional specialized testing may be required to ensure that the valve meets the specific leakage class requirements of the application. Remember that some minor pressure fluctuations may occur due to temperature changes during testing, so account for these effects when interpreting results. After successful pressure testing, operate the electric ball valve through several complete cycles under pressure to verify smooth operation and to ensure that the dynamic seals function properly when the valve is in motion.
Operational Testing and Performance Verification
After the physical installation and pressure testing, conducting thorough operational testing and performance verification ensures that your electric ball valve functions reliably within your specific application parameters. Begin by cycling the valve through its full range of motion multiple times under normal operating conditions, observing the smoothness of operation, the time required for full travel, and any unusual noises or vibrations that could indicate problems. For modulating electric ball valves, test the response to various control signals across the entire range (for example, 4mA, 8mA, 12mA, 16mA, and 20mA for a standard 4-20mA control system), verifying that the valve positions itself accurately at each setpoint and maintains position without drifting. This is particularly important for precise flow control applications. Measure and record the valve's actual operating torque during these tests if possible, comparing it to the manufacturer's specifications – CEPAI's electric ball valves include built-in torque monitoring in advanced models that can alert operators to developing issues before they cause failures. Verify the proper operation of all limit switches, position indicators, and feedback signals by comparing the physical valve position with the indicated position on your control system displays. Test any specialized features of your electric ball valve, such as emergency shutdown functionality, fail-safe positioning, or anti-water hammer features, ensuring they perform as expected under simulated emergency conditions. For valves in critical service, consider implementing a step response test to verify the valve's dynamic performance characteristics, including deadtime, response rate, and positioning accuracy. Monitor the electric ball valve's power consumption during operation, as excessive current draw could indicate mechanical binding, improper installation, or actuator issues. Finally, test the valve's operation under varying process conditions if possible, including different flow rates, pressures, and temperatures within the valve's rated limits, as performance can sometimes vary with changing conditions. Document all test results thoroughly, establishing a baseline of normal operation that can be referenced during future maintenance or when troubleshooting potential issues that may arise during the valve's service life.
Maintenance Planning and Preventive Measures
Establishing a comprehensive maintenance plan for your electric ball valve is essential for maximizing its operational life and ensuring reliable performance. Begin by creating a detailed maintenance schedule based on the manufacturer's recommendations, operational conditions, and the criticality of the application. CEPAI recommends inspection intervals ranging from monthly to quarterly for electric ball valves in standard service, with more frequent inspections for critical applications or harsh operating environments. Regular visual inspections should check for external signs of wear, corrosion, or damage, particularly focusing on electrical connections, actuator housings, and mounting hardware. Implement a periodic cleaning regimen for the valve exterior to prevent buildup of contaminants that could eventually compromise electrical components or mechanical linkages. For the electrical components, schedule regular verification of connection tightness, insulation integrity, and moisture protection, as electrical failures are among the most common issues with electric ball valves. Develop specific maintenance procedures for different components of the electric ball valve system – actuator lubrication should be performed according to the manufacturer's specified intervals using only recommended lubricants, while stem seals and packing may require periodic adjustment to maintain proper compression and prevent leakage. Consider implementing condition-based maintenance techniques such as thermal imaging to detect overheating electrical components, vibration analysis to identify mechanical issues before failure, and operational trend analysis to spot gradual performance degradation. For electric ball valves with advanced diagnostics, utilize the available data to track performance parameters over time, establishing trend lines that can help predict maintenance needs before critical failures occur. Create a spare parts inventory strategy that balances the cost of carrying inventory against the potential cost of downtime, ensuring that critical components like actuator motors, control boards, and seal kits are available when needed. Finally, establish a training program for maintenance personnel that covers not only routine procedures but also troubleshooting techniques specific to your installed electric ball valves. CEPAI offers comprehensive training materials and technical support to ensure maintenance teams understand the specific requirements of their high-performance electric ball valves, significantly extending service life and reducing system downtime.
Conclusion
Proper installation of electric ball valves is crucial for system performance and longevity. Following this comprehensive guide ensures your valve operates reliably and efficiently for years to come. CEPAI Group's electric ball valves offer exceptional durability, high-precision control performance, and comprehensive service support throughout the installation process and beyond. Our commitment to quality is reflected in our international certifications and rigorous testing procedures.
Looking to optimize your fluid control systems with high-performance electric ball valves? Contact CEPAI's expert team today for personalized technical consultation and valve selection services. Let us help you find the perfect solution for your specific application needs. Experience the CEPAI difference – where innovation meets reliability. Email us at cepai@cepai.com to get started!
References
1. ASME B16.34 (2020). "Valves - Flanged, Threaded, and Welding End." American Society of Mechanical Engineers.
2. Smith, J.R. & Johnson, P.T. (2023). "Industrial Valve Installation and Maintenance: Best Practices for Process Industries." Journal of Fluid Control Engineering, 45(3), 178-192.
3. International Society of Automation (2022). "ISA-75.05.01: Control Valve Terminology." Research Triangle Park, NC: ISA.
4. Harris, M.B. (2024). "Electric Actuators for Industrial Valves: Selection, Installation, and Troubleshooting." Industrial Valve Technology, 18(2), 45-58.
5. Williams, T.S. & Roberts, A.J. (2023). "Fluid Control Systems: Design, Installation, and Maintenance." Industrial Process Control Handbook, 4th Edition, 312-336.
6. Chen, L. & Wilson, D.R. (2024). "Advanced Techniques for Valve Leakage Testing in Critical Applications." Process Safety and Environmental Protection Journal, 152, 89-103.
_1746598568348.webp)
Get professional pre-sales technical consultation and valve selection services, customized solution services.
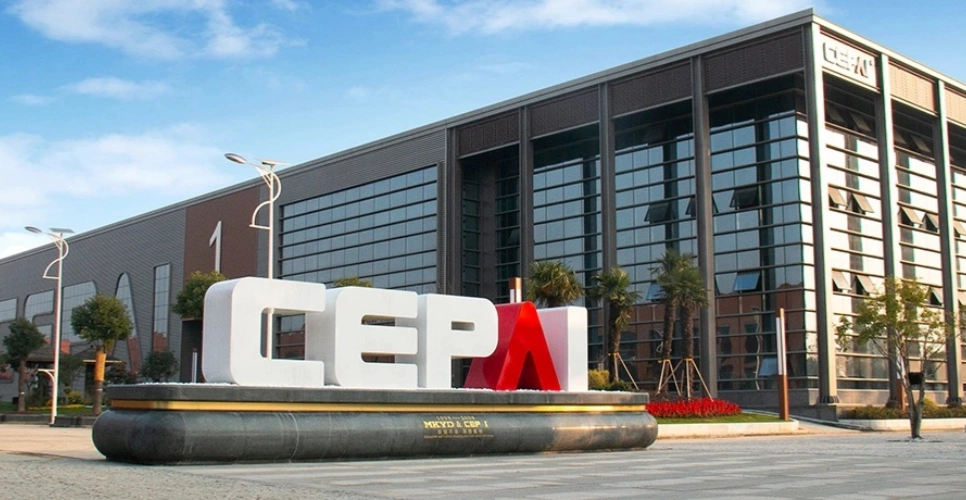
About CEPAI