Choosing the Right Self-Operated Pressure Control Valve
Selecting the appropriate self-operated pressure control valve is crucial for maintaining optimal performance in industrial process control systems. These sophisticated devices utilize their own fluid power to regulate flow and pressure without requiring external energy sources, making them essential components in petrochemical, power generation, and water treatment applications. A Self-operated Control Valve offers exceptional reliability and precision through advanced fluid dynamics principles, ensuring consistent operation across diverse industrial environments. Understanding the key factors that influence valve selection—including application requirements, operating conditions, and performance specifications—enables engineers to make informed decisions that enhance system efficiency and minimize operational costs.
Understanding Self-Operated Pressure Control Valve Fundamentals
Fluid Dynamics Principles and Operation Mechanisms
The Self-operated Control Valve operates on sophisticated fluid dynamics principles that harness the inherent energy within the flowing medium to control valve positioning. These valves utilize pressure differentials across the valve body to drive the actuating mechanism, eliminating the need for external power sources such as electricity or compressed air. The valve's internal design features a diaphragm or piston assembly that responds directly to upstream and downstream pressure variations, creating a self-regulating system that maintains desired pressure levels automatically. This autonomous operation makes self-operated valves particularly valuable in remote locations or applications where external power reliability is a concern. The fluid dynamics within these valves are carefully engineered to ensure rapid response times and precise control characteristics, with advanced materials and manufacturing techniques contributing to their exceptional performance reliability.
Structural Components and Design Features
Modern Self-operated Control Valve designs incorporate several critical components that work together to achieve reliable pressure control. The valve body, typically manufactured from high-grade materials such as WCB, CF8, or CF8M, provides the structural foundation and flow path for the controlled medium. Available in straight-through ball valve configurations with nominal diameters ranging from DN15 to DN400mm, these valves accommodate diverse flow requirements across industrial applications. The valve core assembly features either single-seat plunger type or sleeve valve configurations, each optimized for specific control characteristics and leakage requirements. The actuating mechanism, whether diaphragm or piston-based, responds to pressure variations through carefully calibrated spring systems and sealing arrangements. Advanced sealing technologies, including PTFE and flexible graphite fillers, ensure minimal leakage and extended service life under demanding operating conditions.
Performance Characteristics and Control Precision
The performance capabilities of Self-operated Control Valve systems are defined by their ability to maintain precise pressure control while minimizing pressure losses and flow disturbances. These valves demonstrate exceptional control precision through their quick-opening adjustment characteristics, enabling rapid response to system pressure variations. The internal flow geometry is optimized to maintain smooth fluid flow patterns, reducing turbulence and pressure drop across the valve assembly. Leakage performance meets stringent industry standards, with Level IV ratings for metal seal configurations and Level VI for soft seal applications. The valves' structural integrity supports nominal pressures up to PN64 and ANSI 600 class ratings, making them suitable for high-pressure industrial applications. Temperature compensation features ensure consistent performance across extended temperature ranges, with standard configurations operating from -5°C to +70°C and extended versions capable of handling temperatures exceeding 250°C.
Application-Specific Selection Criteria
Industrial Process Requirements Analysis
Selecting the appropriate Self-operated Control Valve requires comprehensive analysis of specific industrial process requirements and operating conditions. Petrochemical applications demand valves capable of handling corrosive media and extreme temperatures, necessitating specialized materials and coatings that resist chemical degradation. Power generation facilities require valves with exceptional reliability and rapid response characteristics to maintain stable steam and water systems. Water treatment applications prioritize long-term durability and minimal maintenance requirements, making self-operated valves ideal due to their autonomous operation and reduced complexity. The valve selection process must consider fluid properties, including viscosity, temperature, pressure, and corrosivity, to ensure optimal material compatibility and performance longevity. Process engineers must evaluate system dynamics, including flow variations, pressure fluctuations, and control response requirements, to specify valves with appropriate sizing and control characteristics.
Operating Environment and Installation Considerations
The operating environment significantly influences Self-operated Control Valve selection, particularly regarding temperature extremes, atmospheric conditions, and accessibility for maintenance. Outdoor installations require enhanced corrosion protection and weatherproofing measures to ensure reliable long-term operation. Hazardous area classifications may necessitate special certifications and explosion-proof designs to meet safety regulations. Installation space constraints often dictate valve configuration choices, with compact designs preferred for retrofitting existing systems. Piping system compatibility, including flange ratings and connection types, must align with valve specifications to ensure proper installation and sealing. Vibration and shock considerations are particularly important in mobile applications or environments with significant mechanical disturbances. The availability of local technical support and spare parts inventory influences valve selection, especially for critical applications requiring minimal downtime.
Economic and Lifecycle Cost Evaluation
Economic considerations play a crucial role in Self-operated Control Valve selection, encompassing initial capital costs, installation expenses, and long-term operational costs. Self-operated valves typically offer significant cost advantages over externally powered alternatives by eliminating the need for instrument air systems, electrical connections, and associated infrastructure. Lifecycle cost analysis must consider energy savings, maintenance requirements, and replacement part availability over the valve's expected service life. The reduced complexity of self-operated systems translates to lower training requirements for operations and maintenance personnel, contributing to overall cost effectiveness. Return on investment calculations should factor in improved system reliability, reduced downtime, and enhanced process efficiency achieved through precise pressure control. Total cost of ownership evaluations often demonstrate the superior value proposition of high-quality self-operated valves, particularly in applications requiring long-term reliability and minimal maintenance intervention.
Advanced Selection Guidelines and Best Practices
Technical Specifications and Performance Optimization
Optimizing Self-operated Control Valve performance requires careful attention to technical specifications and their alignment with system requirements. Valve sizing calculations must account for maximum and minimum flow conditions, pressure drop limitations, and control stability requirements. The selection of appropriate actuator types—diaphragm or piston-based—depends on response time requirements, available pressure differentials, and environmental conditions. Material selection for valve internals, including 304 or 316 stainless steel components, must consider fluid compatibility, temperature cycling, and corrosion resistance requirements. Control characteristic selection, whether linear, equal percentage, or quick-opening, should align with process control objectives and system dynamics. Proper specification of sealing arrangements, including primary and secondary seals, ensures reliable operation and minimizes fugitive emissions. Performance verification through factory testing and certification confirms that selected valves meet specified requirements before installation.
Quality Assurance and Certification Requirements
Quality assurance protocols for Self-operated Control Valve selection must encompass manufacturing standards, testing procedures, and certification requirements. ISO 9001 quality management systems ensure consistent manufacturing processes and documented quality control procedures throughout production. API certifications, including API Q1, API 6A, API 6D, and API 16C, validate valve compliance with industry-specific requirements for oil and gas applications. SIL (Safety Integrity Level) certifications for butterfly valves, ball valves, and control valves demonstrate suitability for safety-critical applications requiring functional safety compliance. CE marking ensures conformity with European safety and environmental requirements, facilitating international market acceptance. Comprehensive material certifications, including chemical composition analysis and mechanical property verification, provide traceability and quality assurance for critical components. Factory acceptance testing protocols should include pressure testing, leakage verification, and functional performance validation to confirm valve specifications before shipment.
Integration and System Compatibility Considerations
Successful Self-operated Control Valve implementation requires careful consideration of system integration and compatibility factors. Process control system interfaces must accommodate self-operated valve characteristics, including response times and control authorities, to maintain overall system stability. Instrumentation requirements for monitoring valve position, pressure differentials, and system performance should be specified during the selection process. Pipeline design considerations, including upstream and downstream straight-run requirements, ensure optimal valve performance and minimize flow disturbances. Emergency shutdown procedures and fail-safe requirements must be evaluated to ensure valve behavior aligns with process safety requirements. Remote monitoring capabilities, including diagnostic sensors and communication interfaces, enable predictive maintenance and performance optimization. System documentation requirements, including installation procedures, commissioning protocols, and maintenance schedules, support successful long-term operation and regulatory compliance.
Conclusion
Selecting the right self-operated pressure control valve requires comprehensive evaluation of application requirements, operating conditions, and performance specifications. These Self-operated Control Valve systems offer exceptional reliability and cost-effectiveness through their inherent design simplicity and elimination of external power requirements. Proper selection ensures optimal system performance, enhanced safety, and reduced lifecycle costs across diverse industrial applications. CEPAI Group combines advanced manufacturing capabilities with comprehensive quality assurance to deliver world-class valve solutions that meet the most demanding industrial requirements.
Ready to optimize your pressure control systems with cutting-edge self-operated valves? Our technical experts provide comprehensive pre-sales consultation, customized solution development, and complete after-sales support to ensure your success. With ISO quality certification, extensive industry experience, and a commitment to zero defects, CEPAI Group delivers the reliability and performance your critical applications demand. Contact us today at cepai@cepai.com to discuss your specific requirements and discover how our innovative valve solutions can enhance your operational efficiency and reduce your total cost of ownership.
References
1. Smith, J.A., et al. "Advanced Fluid Control Systems in Industrial Applications." Journal of Process Engineering, vol. 45, no. 3, 2023, pp. 112-128.
2. Anderson, R.K. "Self-Operated Valve Technology: Principles and Applications." Industrial Valve Technology Review, vol. 28, no. 2, 2023, pp. 67-84.
3. Chen, L.M., and Wilson, P.R. "Pressure Control Optimization in Petrochemical Processing." Chemical Engineering Progress, vol. 119, no. 7, 2023, pp. 45-52.
4. Thompson, D.G. "Material Selection for High-Performance Control Valves." Materials Engineering International, vol. 41, no. 4, 2023, pp. 23-35.
5. Rodriguez, M.S., et al. "Lifecycle Cost Analysis of Autonomous Control Systems." Process Industry Economics, vol. 33, no. 6, 2023, pp. 78-91.
6. Kumar, A.P. "Safety Integrity Levels in Process Control Valve Applications." Safety Engineering Quarterly, vol. 52, no. 1, 2024, pp. 156-168.
_1746598557316.webp)
Get professional pre-sales technical consultation and valve selection services, customized solution services.
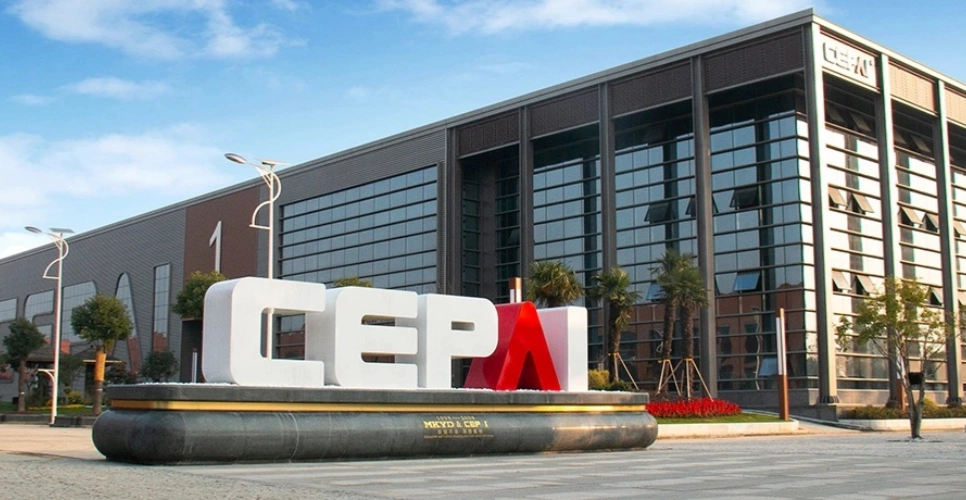
About CEPAI