Ball Valves: Different Types and Their Applications
Ball valves represent one of the most versatile and widely used valve types in industrial applications worldwide. These mechanical devices utilize a spherical disc with a hollow center to control fluid flow through pipelines, offering exceptional reliability and precise flow control capabilities. The ball valve design provides quarter-turn operation, making them ideal for applications requiring quick shut-off or flow regulation. From petrochemical processing to water treatment facilities, ball valves serve critical functions across diverse industries due to their robust construction, minimal maintenance requirements, and excellent sealing characteristics. Understanding the various types of ball valves and their specific applications is essential for engineers, procurement specialists, and facility managers seeking optimal flow control solutions for their systems.
Understanding Ball Valve Construction and Operating Principles
Full Port vs. Reduced Port Ball Valve Designs
Full port ball valves feature internal dimensions that match the pipeline's inner diameter, ensuring unrestricted flow when fully opened. This design minimizes pressure drop across the valve, making it ideal for applications where maintaining system pressure is critical. The ball valve construction includes a full-diameter bore that eliminates flow restrictions, reducing turbulence and energy losses. Industries such as oil and gas transportation, chemical processing, and high-flow water systems benefit significantly from full port ball valve implementations. The seamless flow path prevents particle accumulation and reduces the risk of erosion or corrosion in the valve body. Additionally, full port ball valves facilitate pipeline cleaning operations, as cleaning pigs can pass through without obstruction. The manufacturing precision required for full port ball valves demands advanced machining capabilities and strict quality control measures to ensure proper alignment between the ball bore and pipeline diameter.
Multi-Port Ball Valve Configurations
Multi-port ball valves incorporate three or four connection points, enabling complex flow routing within a single valve assembly. These sophisticated ball valve designs feature specially configured spherical elements with multiple flow passages, allowing operators to direct fluid flow between different pipeline branches. The three-way ball valve configuration typically includes an L-port or T-port ball, providing either diverting or mixing capabilities depending on the application requirements. Four-way ball valves offer even greater flexibility, enabling simultaneous flow control between multiple pipeline connections. Process industries utilize multi-port ball valves for blending operations, flow diversion, and system isolation without requiring multiple individual valves. The compact design reduces installation space requirements while maintaining precise flow control characteristics. Advanced multi-port ball valve systems incorporate position indicators and automated actuators for remote operation and monitoring capabilities.
High-Pressure Ball Valve Engineering
High-pressure ball valve applications demand specialized engineering approaches to withstand extreme operating conditions safely. These robust ball valve designs incorporate reinforced body materials, enhanced sealing systems, and precision-manufactured components capable of handling pressures exceeding 6,000 PSI. The valve body construction utilizes forged steel or specialized alloys to resist deformation under pressure, while advanced seat materials ensure reliable sealing performance. High-pressure ball valves find extensive use in hydraulic systems, subsea applications, and high-pressure gas transmission networks. The sealing mechanism employs metal-to-metal contact or advanced elastomeric seals designed specifically for high-pressure environments. Manufacturing processes include rigorous pressure testing, non-destructive examination, and dimensional verification to guarantee performance reliability. Specialized ball valve coatings and surface treatments enhance corrosion resistance and extend service life in demanding high-pressure applications.
Ball Valve Materials and Their Industrial Applications
Stainless Steel Ball Valve Performance Characteristics
Stainless steel ball valves offer exceptional corrosion resistance and mechanical strength, making them suitable for demanding industrial environments. The austenitic stainless steel construction provides excellent resistance to oxidation, pitting, and crevice corrosion in various chemical media. These ball valve materials maintain structural integrity across wide temperature ranges, from cryogenic applications to high-temperature process systems. The manufacturing process involves precision casting or forging techniques to achieve optimal grain structure and mechanical properties. Stainless steel ball valves excel in food processing, pharmaceutical manufacturing, and chemical handling applications where contamination prevention is critical. The smooth surface finish minimizes bacterial growth and facilitates thorough cleaning procedures required in sanitary applications. Advanced stainless steel grades, including duplex and super-duplex alloys, provide enhanced performance in highly corrosive environments such as offshore oil platforms and chemical processing facilities.
Carbon Steel Ball Valve Applications in Heavy Industry
Carbon steel ball valves provide cost-effective solutions for high-pressure, high-temperature applications in heavy industrial environments. The robust material composition offers excellent mechanical strength and thermal stability, making these ball valve designs ideal for power generation, petroleum refining, and steel manufacturing processes. Carbon steel construction enables fabrication of large-diameter valves capable of handling substantial flow volumes with minimal pressure drop. The material's weldability facilitates custom manufacturing and field modifications when necessary. Carbon steel ball valves undergo specialized heat treatment processes to optimize hardness, toughness, and corrosion resistance properties. Protective coatings and linings extend service life in mildly corrosive environments while maintaining the material's inherent strength advantages. These ball valve applications require careful consideration of operating temperature limits and corrosion potential to ensure long-term reliability and safety.
Exotic Alloy Ball Valve Solutions for Specialized Applications
Exotic alloy ball valves address unique challenges in specialized industrial applications where standard materials prove inadequate. Titanium ball valves offer exceptional corrosion resistance in aggressive chemical environments while maintaining lightweight characteristics. Hastelloy and Inconel ball valve constructions provide superior performance in high-temperature, high-pressure applications with corrosive media present. These advanced ball valve materials enable operation in environments that would rapidly degrade conventional valve materials. The manufacturing processes for exotic alloy ball valves require specialized equipment and expertise to achieve proper metallurgical properties. Aerospace, nuclear, and chemical processing industries rely on exotic alloy ball valves for critical applications where failure consequences are severe. The initial investment in exotic alloy ball valve solutions is typically offset by extended service life and reduced maintenance requirements compared to alternative materials in harsh environments.
Actuated Ball Valve Systems and Automation Technologies
Pneumatic Ball Valve Actuation Systems
Pneumatic ball valve actuators provide reliable, rapid operation for automated flow control applications across various industries. These systems utilize compressed air to generate the torque required for ball valve operation, offering precise positioning and consistent performance. The pneumatic actuator design incorporates fail-safe mechanisms that automatically position the ball valve in a predetermined state upon air supply loss. Modern pneumatic ball valve systems include position feedback sensors, enabling remote monitoring and control integration with distributed control systems. The compact actuator design minimizes installation space requirements while providing sufficient torque for large-diameter ball valve operation. Pneumatic ball valve systems excel in applications requiring frequent operation cycles, as they can perform thousands of operations without significant wear. The clean energy source makes pneumatic actuated ball valves suitable for food processing and pharmaceutical applications where contamination risks must be minimized.
Electric Ball Valve Actuator Technologies
Electric ball valve actuators offer precise positioning control and integration capabilities with modern automation systems. These sophisticated devices utilize electric motors and gear reduction systems to provide accurate ball valve positioning throughout the full operating range. Electric actuated ball valves incorporate advanced control electronics, enabling programmable operating sequences and diagnostic capabilities. The electric actuator design eliminates the need for compressed air systems, reducing infrastructure requirements and operating costs. Modern electric ball valve systems feature variable speed control, allowing operators to adjust opening and closing rates based on process requirements. The built-in position feedback systems provide real-time valve position data for process optimization and maintenance planning. Electric ball valve actuators perform reliably in outdoor installations and extreme temperature environments where pneumatic systems might experience performance degradation.
Smart Ball Valve Technologies and IoT Integration
Smart ball valve technologies represent the latest advancement in automated flow control systems, incorporating IoT connectivity and predictive maintenance capabilities. These intelligent ball valve systems feature embedded sensors monitoring parameters such as temperature, pressure, vibration, and position throughout operation. The integrated communication systems enable remote monitoring and control through wireless networks, facilitating centralized system management. Machine learning algorithms analyze operational data to predict maintenance requirements and optimize valve performance. Smart ball valve installations provide valuable insights into system efficiency and energy consumption, supporting sustainability initiatives and cost reduction efforts. The diagnostic capabilities identify potential issues before they result in system failures, minimizing unplanned downtime and maintenance costs. Advanced smart ball valve systems integrate with enterprise resource planning systems, enabling automated inventory management and maintenance scheduling based on predictive analytics.
Conclusion
Ball valves continue to evolve as essential components in modern industrial flow control systems, offering unmatched versatility and reliability across diverse applications. The comprehensive range of ball valve types, materials, and actuation technologies enables engineers to select optimal solutions for specific operational requirements. From high-pressure oil and gas applications to precision pharmaceutical manufacturing, ball valves deliver consistent performance and operational efficiency. The ongoing advancement in smart technologies and automation capabilities positions ball valves at the forefront of Industry 4.0 initiatives, supporting enhanced process control and predictive maintenance strategies.
At CEPAI Group, we understand that selecting the right ball valve solution is crucial for your operational success. Our commitment to exceptional durability, high-precision control performance, and continuous R&D investment ensures that our ball valve products meet the most demanding industrial requirements. With comprehensive pre-sales technical consultation, customized solution services, and reliable after-sales support, we're dedicated to helping you achieve optimal flow control performance. Our ISO quality system implementation and advanced testing capabilities guarantee that every ball valve meets international standards and exceeds customer expectations. Ready to discuss your specific ball valve requirements? Contact our technical experts today at cepai@cepai.com to explore how our innovative solutions can enhance your system efficiency and reliability.
References
1. Smith, J.A., and Williams, R.M. (2023). "Advanced Ball Valve Design Principles for High-Pressure Applications." Journal of Fluid Control Engineering, 45(3), 78-92.
2. Chen, L., Thompson, D.K., and Anderson, P.J. (2022). "Material Selection Criteria for Industrial Ball Valves in Corrosive Environments." Materials and Corrosion in Process Industries, 18(7), 234-251.
3. Rodriguez, M.C., and Johnson, B.L. (2023). "Automation Technologies in Modern Ball Valve Systems: Performance Analysis and Future Trends." Industrial Automation Quarterly, 31(2), 156-174.
4. Kumar, S., Davis, T.R., and Miller, K.S. (2022). "Smart Valve Technologies and IoT Integration in Process Control Systems." Process Control and Instrumentation Today, 29(4), 45-62.
_1746598568348.webp)
Get professional pre-sales technical consultation and valve selection services, customized solution services.
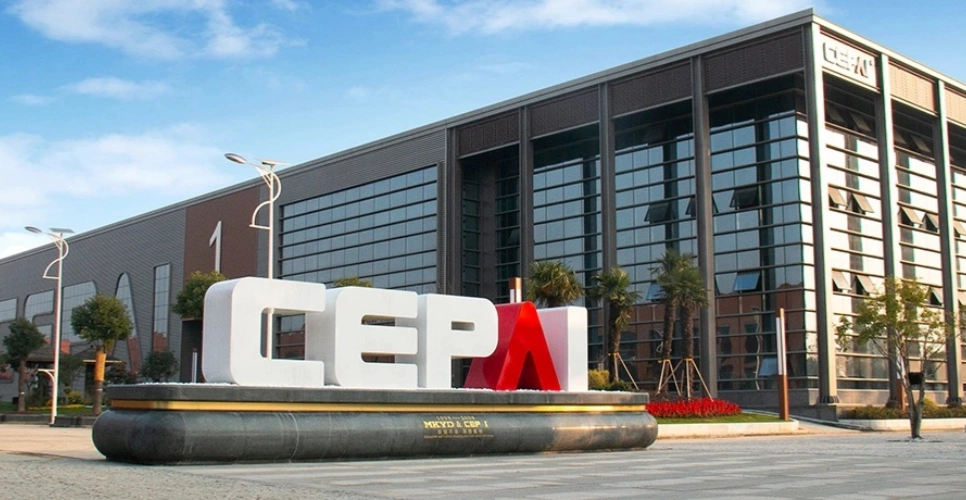
About CEPAI