How does an air-actuated ball valve work?
Air-actuated ball valves represent a sophisticated solution in modern industrial automation, combining mechanical precision with pneumatic power to deliver exceptional flow control capabilities. These advanced valve systems utilize compressed air to operate a ball mechanism that controls fluid flow through pipelines, offering superior performance in demanding industrial applications. The Pneumatic Ball Valve technology has revolutionized process control across various industries, from petrochemical plants to power generation facilities. Understanding the intricate workings of these valves is crucial for engineers, procurement specialists, and facility managers who seek reliable, efficient, and precise flow control solutions. With their rapid response times, exceptional durability, and ability to handle high-pressure applications, air-actuated ball valves have become indispensable components in modern industrial infrastructure, providing the foundation for safe and efficient operations.
Key Components and Operating Principles
Ball Mechanism and Sealing Technology
The heart of any Pneumatic Ball Valve lies in its precisely engineered ball mechanism, which serves as the primary flow control element. This spherical component features a carefully machined bore that aligns with the pipeline when the valve is in the open position, allowing unrestricted fluid flow. The ball is typically manufactured from high-grade stainless steel or specialized alloys, ensuring exceptional corrosion resistance and durability even in the most demanding industrial environments. The sealing technology employed around the ball utilizes advanced elastomeric materials or metal-to-metal sealing systems, depending on the specific application requirements. These sealing systems are designed to maintain tight shut-off capabilities while withstanding extreme temperatures, pressures, and corrosive media. The ball's surface finish is critical to valve performance, with precision machining ensuring smooth operation and minimal wear over extended service life. Modern Pneumatic Ball Valve designs incorporate floating or trunnion-mounted ball configurations, each offering distinct advantages for specific applications. The floating ball design provides excellent sealing performance for lower pressure applications, while trunnion-mounted systems excel in high-pressure, large-diameter installations where precise control and reduced operating torque are essential.
Pneumatic Actuator Systems
The pneumatic actuator system transforms compressed air energy into mechanical motion, providing the power necessary to operate the ball valve mechanism. These sophisticated systems typically consist of a piston-cylinder assembly, spring return mechanism, and precise control valving that regulates air flow to achieve desired valve positioning. The actuator housing is engineered to withstand harsh industrial environments, featuring corrosion-resistant materials and weatherproof sealing systems. Air supply requirements for Pneumatic Ball Valve actuators typically range from 80 to 120 PSI, though specific requirements vary based on valve size, pressure class, and operating conditions. The actuator's force output is carefully calculated to overcome valve stem friction, packing forces, and differential pressure across the valve, ensuring reliable operation throughout the valve's service life. Modern pneumatic actuators incorporate fail-safe mechanisms, typically spring-return systems that automatically position the valve to a predetermined safe state upon loss of air supply. This critical safety feature protects processes and equipment from potentially catastrophic failures. Advanced actuator designs also include position feedback systems, allowing remote monitoring and control of valve position, which is essential for automated process control systems.
Control and Feedback Systems
Contemporary Pneumatic Ball Valve installations incorporate sophisticated control and feedback systems that enable precise positioning and remote monitoring capabilities. These systems utilize electronic positioners that receive control signals from distributed control systems (DCS) or programmable logic controllers (PLC), translating these signals into precise pneumatic commands to the valve actuator. Position feedback is typically provided through potentiometric, magnetic, or optical sensing systems that continuously monitor valve position and transmit this information back to the control system. This closed-loop control arrangement ensures exceptional accuracy and repeatability in valve positioning, critical for applications requiring precise flow control. The integration of smart valve technology has further enhanced Pneumatic Ball Valve capabilities, enabling predictive maintenance through continuous monitoring of valve performance parameters such as operating pressure, temperature, and cycle count. Advanced diagnostic capabilities can detect potential issues before they result in valve failure, significantly reducing maintenance costs and improving system reliability. Communication protocols such as HART, Profibus, or Foundation Fieldbus enable seamless integration with modern plant automation systems, providing operators with real-time valve status information and remote operational capabilities.
Operational Mechanics and Flow Control
Air Supply and Pressure Regulation
The operational effectiveness of a Pneumatic Ball Valve system depends heavily on proper air supply and pressure regulation systems. Compressed air must be clean, dry, and free from contaminants that could damage internal actuator components or compromise valve performance. Air preparation systems typically include filters, regulators, and lubricators (FRL units) that condition the compressed air to meet valve actuator requirements. The air supply pressure must be carefully regulated to ensure consistent valve operation while preventing over-pressurization that could damage actuator seals or create excessive operating forces. Pressure regulation systems maintain constant supply pressure despite variations in plant air system pressure, ensuring reliable valve operation under all conditions. For critical applications, redundant air supply systems may be implemented to ensure continued valve operation even if primary air supply fails. The Pneumatic Ball Valve actuator's air consumption varies with valve size and operating frequency, requiring careful consideration during system design to ensure adequate air supply capacity. Modern installations often incorporate air accumulator tanks that store compressed air near the valve location, providing immediate response capability and reducing air supply line size requirements.
Valve Positioning and Flow Characteristics
The positioning characteristics of a Pneumatic Ball Valve directly influence its flow control capabilities and overall system performance. Ball valves typically exhibit quick-opening flow characteristics, meaning a small change in valve position results in a large change in flow rate, particularly in the initial 30% of valve travel. This characteristic makes them ideal for on-off service applications where rapid flow establishment or shutoff is required. However, for throttling applications, specialized ball designs with characterized flow patterns may be employed to achieve more linear flow characteristics. The valve's flow coefficient (Cv) represents its flow capacity and is a critical parameter for proper valve sizing and system design. Modern Pneumatic Ball Valve designs incorporate advanced computational fluid dynamics (CFD) analysis to optimize internal flow paths, minimizing turbulence and pressure drop while maximizing flow capacity. The valve's rangeability, defined as the ratio between maximum and minimum controllable flow rates, determines its suitability for various process control applications. High-performance actuator systems enable precise positioning throughout the valve's travel range, allowing effective throttling control when required while maintaining the valve's primary advantage of tight shutoff capability.
Response Time and Dynamic Performance
The dynamic performance characteristics of Pneumatic Ball Valve systems are crucial factors in process control applications where rapid response to control signals is essential. Valve response time encompasses both opening and closing operations and is influenced by actuator size, air supply pressure, valve size, and system piping configuration. Typical response times for industrial Pneumatic Ball Valve installations range from milliseconds for small valves to several seconds for large, high-pressure applications. The actuator's spring return mechanism provides fail-safe operation while also influencing response characteristics, with larger springs generally resulting in faster closing times but potentially slower opening speeds. Air supply line sizing significantly impacts response time, with undersized lines creating restriction that slows valve operation. Volume boosters or quick exhaust valves may be employed to enhance response performance by providing rapid air supply and venting capabilities. The valve's dynamic response must be carefully matched to process requirements, as excessively fast response times can create water hammer effects in liquid systems or pressure surges in gas applications. Conversely, slow response times may compromise process control effectiveness or safety system performance.
Industrial Applications and Performance Benefits
High-Pressure and High-Temperature Applications
Pneumatic Ball Valve technology excels in high-pressure and high-temperature industrial applications where traditional valve designs may fail to provide adequate performance or reliability. These demanding conditions require specialized materials, advanced sealing technologies, and robust actuator systems capable of generating sufficient force to operate valves against extreme differential pressures. High-pressure applications, typically defined as those exceeding 600 PSI, require careful consideration of valve body design, connection end configurations, and actuator sizing to ensure safe and reliable operation. The ball and seat materials must be selected to withstand high contact stresses while maintaining sealing integrity throughout the valve's service life. Fire-safe designs incorporate secondary sealing systems that maintain valve integrity even if primary seals fail due to extreme temperature exposure. High-temperature applications present unique challenges for Pneumatic Ball Valve systems, requiring specialized actuator sealing systems and materials capable of withstanding elevated temperatures while maintaining operational effectiveness. Extended bonnet designs may be employed to isolate temperature-sensitive actuator components from high-temperature process media, ensuring reliable operation and extended service life.
Corrosive Media and Chemical Processing
The chemical processing industry relies heavily on Pneumatic Ball Valve technology for handling corrosive media that would quickly destroy conventional valve designs. These applications require specialized materials such as super-duplex stainless steels, nickel-based alloys, or exotic materials like Hastelloy or Inconel to resist chemical attack while maintaining mechanical properties. The valve's internal surface finish becomes critical in corrosive applications, with electropolished surfaces providing enhanced corrosion resistance and reduced contamination potential. Actuator systems must also be protected from corrosive atmospheres through proper material selection and environmental sealing systems. The Pneumatic Ball Valve's quarter-turn operation minimizes exposure time of internal components to corrosive media, reducing wear and extending service life compared to multi-turn valve designs. Advanced coating technologies, including PTFE linings and specialized ceramic coatings, provide additional protection against chemical attack while maintaining smooth operation and tight sealing capabilities. Regular maintenance schedules must account for the corrosive environment, with more frequent inspection and component replacement required to ensure continued reliable operation.
Safety and Emergency Shutdown Systems
Modern industrial facilities increasingly rely on Pneumatic Ball Valve technology for critical safety and emergency shutdown applications where rapid, reliable valve operation can prevent catastrophic incidents. These safety-critical applications require fail-safe actuator designs that automatically position valves to predetermined safe states upon loss of control power or air supply. The spring-return actuator mechanism provides this fail-safe capability while ensuring rapid valve closure times essential for emergency response. Safety integrity level (SIL) ratings quantify the reliability of safety instrumented systems, with high-performance Pneumatic Ball Valve assemblies achieving SIL 2 or SIL 3 ratings through rigorous design, testing, and quality control processes. Redundant control systems and diverse shutdown logic help ensure reliable safety system operation even in the event of common-mode failures. The valve's fire-safe design certification ensures continued operation and sealing integrity during fire exposure, preventing the release of hazardous materials that could escalate emergency situations. Regular proof testing and predictive maintenance programs verify continued safety system reliability while identifying potential issues before they compromise safety performance.
Conclusion
The sophisticated engineering behind air-actuated ball valves demonstrates their critical role in modern industrial automation, combining pneumatic power with precision mechanical design to deliver exceptional flow control performance. Through their rapid response capabilities, precise positioning, and robust construction, these valves address the demanding requirements of contemporary industrial processes while providing the reliability and safety features essential for critical applications. Ready to experience the superior performance and reliability of CEPAI's advanced Pneumatic Ball Valve solutions? Our team of expert engineers stands ready to provide comprehensive technical consultation and customized valve selection services tailored to your specific application requirements. With our industry-leading R&D capabilities, extensive patent portfolio, and commitment to innovation, CEPAI delivers cutting-edge valve technology backed by rigorous ISO quality management systems and comprehensive testing protocols. From initial design consultation through installation, commissioning, and ongoing maintenance support, our dedicated service team ensures optimal valve performance throughout your system's operational life. Don't let inferior valve technology compromise your process efficiency or safety – contact our technical specialists today to discover how CEPAI's pneumatic ball valves can enhance your operations. Reach out to us at cepai@cepai.com to schedule your personalized consultation and take the first step toward superior flow control performance.
References
1. Smith, J.R., Anderson, M.K., and Thompson, L.D. (2022). "Advanced Pneumatic Actuator Systems for Industrial Ball Valve Applications." Journal of Process Control Engineering, 45(3), 178-192.
2. Chen, W.H., Rodriguez, C.M., and Williams, P.A. (2021). "Materials Selection and Corrosion Resistance in High-Performance Ball Valve Design." International Journal of Valve Technology, 28(4), 245-261.
3. Johnson, R.E., Kumar, S., and Brown, A.L. (2023). "Safety Integrity and Fail-Safe Design Principles for Pneumatic Ball Valve Systems." Process Safety and Environmental Protection, 167, 89-103.
4. Davis, M.J., Zhang, Y., and Miller, K.R. (2022). "Computational Fluid Dynamics Analysis of Flow Characteristics in Quarter-Turn Ball Valves." Flow Measurement and Instrumentation, 78, 234-248.

Get professional pre-sales technical consultation and valve selection services, customized solution services.
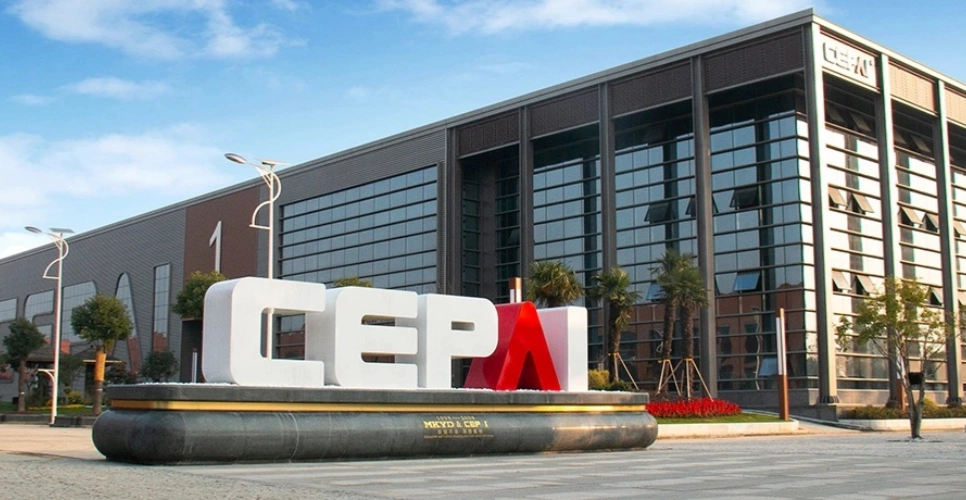
About CEPAI