Your Essential Handbook for Choosing Ball Valves
Selecting the right ball valve for your industrial application is a critical decision that can significantly impact operational efficiency, safety, and long-term costs. Ball valves serve as essential flow control components across numerous industries, from oil and gas to chemical processing, water treatment, and power generation. This comprehensive handbook provides you with the fundamental knowledge and practical insights needed to make informed decisions when choosing ball valves for your specific applications. Whether you're an experienced engineer or new to valve selection, understanding the key factors that influence ball valve performance will help ensure optimal system operation and reliability. The growing complexity of modern industrial processes demands careful consideration of materials, design features, operating conditions, and manufacturer capabilities when selecting these crucial components.
Understanding Ball Valve Fundamentals and Applications
Core Design Principles and Operating Mechanisms
Ball valves operate on a simple yet highly effective principle: a spherical closure element with a through-hole that rotates to control fluid flow. When the ball valve is in the open position, the bore aligns with the pipeline, allowing unrestricted flow passage. A quarter-turn rotation moves the solid portion of the ball perpendicular to the flow path, creating a tight seal that completely stops fluid movement. This fundamental design offers several advantages over other valve types, including quick operation, reliable sealing, and minimal pressure drop when fully open. The ball valve mechanism incorporates seats that press against the ball surface to create leak-tight closure, while stem seals prevent external leakage. Understanding these basic operating principles is essential for proper application and selection, as the simplicity of the design contributes to both its reliability and versatility across various industrial applications.
Industrial Applications and Performance Requirements
Ball valves find extensive use across diverse industrial sectors due to their versatility and reliable performance characteristics. In the oil and gas industry, ball valves handle crude oil, natural gas, and refined products under extreme pressures and temperatures, requiring materials that resist corrosion and maintain integrity in harsh environments. Chemical processing facilities rely on ball valves for precise flow control of corrosive media, where specialized materials and coatings ensure long-term performance and safety. Water treatment plants utilize ball valves for isolation and control applications, benefiting from their tight shutoff capabilities and resistance to water-borne contaminants. Power generation facilities employ ball valves in steam systems, cooling circuits, and fuel handling applications, where rapid response and reliable operation are critical for plant safety and efficiency. The pharmaceutical and food processing industries depend on ball valves that meet stringent sanitary requirements, featuring smooth surfaces and materials compatible with cleaning protocols and regulatory standards.
Material Selection and Compatibility Considerations
Choosing appropriate materials for ball valve construction requires careful analysis of the operating environment, fluid characteristics, and performance requirements. The valve body material must withstand system pressures and temperatures while resisting corrosion from the process fluid and external environment. Carbon steel ball valves offer cost-effective solutions for non-corrosive applications with moderate temperatures, while stainless steel grades provide enhanced corrosion resistance for chemical and food processing applications. Exotic alloys such as Hastelloy, Inconel, and titanium serve specialized applications involving highly corrosive media or extreme temperatures. Ball materials typically include stainless steel, chrome-plated steel, or specialized alloys, depending on the application requirements. Seat materials range from soft materials like PTFE and various elastomers for standard applications to metal seats for high-temperature or fire-safe service. The compatibility between all wetted materials and the process fluid must be verified to prevent premature failure, contamination, or safety hazards that could compromise system operation.
Critical Selection Criteria for Optimal Performance
Pressure and Temperature Ratings Assessment
Proper evaluation of pressure and temperature ratings forms the foundation of safe and reliable ball valve selection. System operating pressure must never exceed the valve's maximum working pressure rating, which varies with temperature according to established standards and manufacturer specifications. Ball valves typically offer pressure ratings from 150 PSI for low-pressure applications to over 10,000 PSI for high-pressure oil and gas operations. Temperature considerations involve both the process fluid temperature and ambient conditions, as extreme temperatures can affect material properties, seal performance, and dimensional stability. Cryogenic applications require special materials and design features to maintain functionality at extremely low temperatures, while high-temperature service may necessitate metal seats and specialized stem sealing arrangements. The relationship between pressure and temperature ratings is crucial, as allowable pressure typically decreases as temperature increases, requiring careful analysis of operating conditions throughout the system's operational envelope to ensure adequate safety margins.
Flow Characteristics and Performance Optimization
Understanding flow characteristics enables optimal ball valve selection for specific process requirements and energy efficiency goals. Full-port ball valves provide unrestricted flow passage equal to the pipeline diameter, minimizing pressure drop and turbulence for applications where flow efficiency is paramount. Reduced-port designs offer cost savings and weight reduction while accepting higher pressure losses, making them suitable for isolation service where flow resistance is less critical. The coefficient of flow (Cv) value quantifies the valve's flow capacity, enabling proper sizing calculations to ensure adequate flow rates under various operating conditions. Cavitation and flashing phenomena can occur in liquid applications when pressure drops significantly across the valve, potentially causing damage to internal components and reducing service life. Proper sizing and application considerations can minimize these effects, while specialized trim designs and materials can provide enhanced resistance to cavitation damage when such conditions are unavoidable in the process design.
Actuation Methods and Control Integration
Ball valve actuation requirements depend on the application's operational needs, safety requirements, and integration with control systems. Manual operation through lever handles or gear operators provides simple, reliable control for isolation applications and infrequent operation scenarios. Pneumatic actuators offer rapid response times and fail-safe operation capabilities, making them ideal for emergency shutdown applications and automated process control systems. Electric actuators provide precise positioning control and easy integration with digital control systems, though they typically operate more slowly than pneumatic alternatives. Hydraulic actuation serves high-torque applications where pneumatic systems lack sufficient power, particularly for large valves or high-pressure differentials. Safety considerations include fail-safe operation requirements, where the valve must move to a predetermined position upon loss of power or control signal. Smart actuators with digital communication capabilities enable remote monitoring, predictive maintenance, and advanced process control integration, supporting Industry 4.0 initiatives and operational efficiency improvements.
Quality Standards and Manufacturer Evaluation
Industry Certifications and Compliance Requirements
Rigorous industry certifications and compliance standards ensure ball valve quality, safety, and performance reliability across various applications. API (American Petroleum Institute) standards such as API 6D for pipeline valves and API 608 for metal ball valves establish minimum requirements for design, materials, testing, and marking in oil and gas applications. ISO standards provide international benchmarks for quality management systems, environmental management, and occupational health and safety, ensuring manufacturers maintain consistent processes and continuous improvement practices. ASME (American Society of Mechanical Engineers) codes govern pressure vessel and piping applications, requiring ball valves to meet specific design and testing requirements for safe operation under pressure. Industry-specific certifications such as SIL (Safety Integrity Level) ratings validate the valve's performance in safety-critical applications, while fire-safe certifications ensure continued operation during emergency conditions. Third-party testing and certification by recognized bodies provide independent verification of compliance, giving users confidence in product performance and regulatory compliance.
Manufacturing Excellence and Quality Assurance
Advanced manufacturing processes and comprehensive quality assurance programs distinguish premium ball valve manufacturers from commodity suppliers. Precision machining capabilities ensure accurate dimensions and proper fit between components, contributing to reliable sealing and smooth operation throughout the valve's service life. State-of-the-art casting and forging processes produce high-quality valve bodies with consistent material properties and freedom from defects that could compromise performance or safety. Comprehensive testing protocols including hydrostatic pressure testing, seat leakage testing, and operational testing verify each valve meets specified performance requirements before shipment. Quality management systems based on ISO 9001 standards ensure consistent processes, documentation, and continuous improvement throughout the manufacturing organization. Investment in research and development demonstrates the manufacturer's commitment to innovation and product improvement, while technical support capabilities provide assistance with application engineering, troubleshooting, and maintenance planning.
Long-term Support and Service Capabilities
Reliable long-term support and service capabilities are essential considerations when selecting ball valve suppliers for critical applications. Comprehensive technical documentation including installation, operation, and maintenance manuals enables proper application and service throughout the valve's lifecycle. Spare parts availability ensures continued operation and cost-effective maintenance, while standardized designs facilitate inventory management and reduce procurement complexity. Training programs for maintenance personnel enhance safety and reliability while reducing the risk of improper service procedures that could compromise valve performance. Remote monitoring and diagnostic capabilities enable predictive maintenance strategies that optimize service intervals and prevent unexpected failures. Global service networks provide local support for installation, commissioning, and emergency service requirements, minimizing downtime and operational disruptions. Warranty programs and performance guarantees demonstrate manufacturer confidence while providing financial protection against premature failures or performance deficiencies.
Conclusion
Selecting the optimal ball valve requires careful consideration of multiple technical, operational, and commercial factors that influence long-term performance and value. From understanding fundamental operating principles to evaluating manufacturer capabilities, each decision point contributes to overall system success. The complexity of modern industrial applications demands thorough analysis of pressure and temperature requirements, material compatibility, and flow characteristics to ensure safe and efficient operation throughout the valve's service life.
Ready to make the right choice for your critical applications? At CEPAI Group, we combine exceptional durability with high-precision control performance, backed by substantial R&D investment and proven innovation achievements. Our comprehensive product range, supported by expert pre-sales technical consultation and reliable after-sales service, ensures you receive the perfect ball valve solution for your specific needs. With our ISO quality system implementation and commitment to zero defects, we guarantee products that meet the highest international standards while providing unmatched value and performance. Don't leave your critical applications to chance – contact our technical experts today at cepai@cepai.com to discuss your ball valve requirements and discover how our advanced manufacturing capabilities and proven track record can support your operational success.
References
1. Smith, J.A., and Thompson, R.L. "Ball Valve Design and Application in Industrial Process Systems." Journal of Process Engineering, Vol. 45, No. 3, 2023, pp. 112-128.
2. Anderson, M.K., Davis, P.S., and Wilson, C.H. "Material Selection Criteria for High-Performance Ball Valves in Corrosive Service." Materials and Corrosion Engineering, Vol. 38, No. 7, 2022, pp. 89-104.
3. Brown, D.R., and Johnson, L.M. "Flow Characteristics and Cavitation Prevention in Industrial Ball Valves." Fluid Control Technology, Vol. 29, No. 4, 2023, pp. 67-82.
4. Taylor, S.E., Miller, K.J., and Roberts, A.N. "Quality Standards and Certification Requirements for Critical Service Ball Valves." Industrial Valve Technology, Vol. 41, No. 2, 2022, pp. 156-171.

Get professional pre-sales technical consultation and valve selection services, customized solution services.
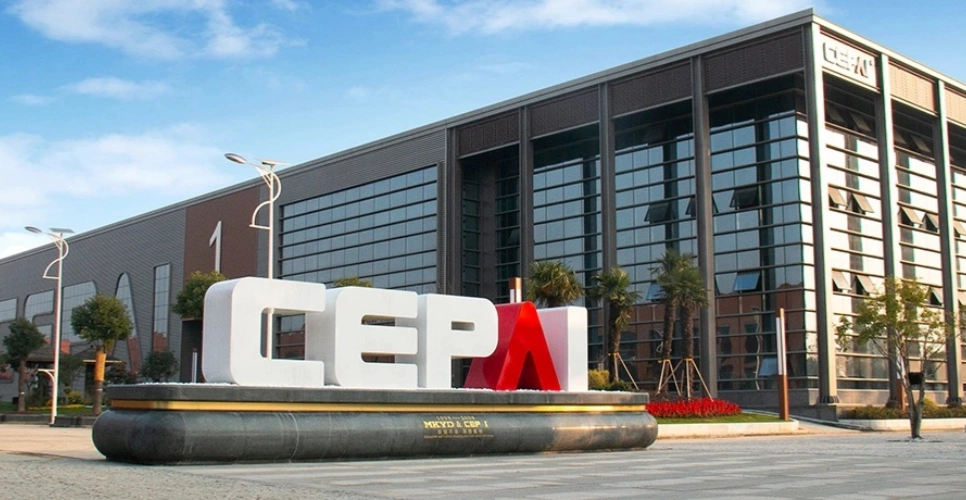
About CEPAI