A Complete Guide to Choosing the Right Ball Valve for Your Needs
Selecting the appropriate ball valve for your industrial application is a critical decision that impacts system performance, safety, and operational efficiency. Ball valves represent one of the most versatile and widely used valve types in modern industrial processes, offering reliable shut-off capabilities and excellent flow control characteristics. Whether you're working in petrochemical facilities, power generation plants, water treatment systems, or oil and gas operations, understanding the key factors that influence ball valve selection will ensure optimal performance and long-term reliability. This comprehensive guide will walk you through the essential considerations, technical specifications, and performance characteristics that determine the right ball valve choice for your specific requirements, helping you make informed decisions that enhance your system's operational excellence.
Understanding Ball Valve Fundamentals and Applications
Ball Valve Design Principles and Operating Mechanisms
Ball valves operate on a simple yet effective principle that makes them indispensable in countless industrial applications. The core component is a spherical closure element with a bore through its center, which rotates within the valve body to control flow. When the ball valve is in the open position, the bore aligns with the pipeline, allowing unrestricted fluid passage. Rotating the ball valve 90 degrees moves it to the closed position, where the solid portion of the sphere blocks the flow path completely. This quarter-turn operation provides rapid shut-off capabilities, making ball valves ideal for emergency shutdown systems and applications requiring quick response times. The ball valve design inherently offers low pressure drop when fully open, as the straight-through flow path minimizes turbulence and friction losses. Modern ball valve manufacturing incorporates precision engineering to ensure tight sealing performance, with seat materials and ball surface treatments optimized for specific service conditions. The robust construction of quality ball valves enables them to withstand high pressures, extreme temperatures, and aggressive media, making them suitable for demanding industrial environments.
Critical Applications Across Industries
Ball valves serve critical functions across diverse industrial sectors, each with unique performance requirements and operational challenges. In the oil and gas industry, ball valves handle crude oil, natural gas, and refined products under high-pressure conditions, often in remote locations where reliability is paramount. Petrochemical facilities utilize ball valves for processing various chemicals and hydrocarbons, requiring materials that resist corrosion and maintain integrity under aggressive service conditions. Power generation plants depend on ball valves for steam, cooling water, and fuel gas systems, where precise control and leak-tight performance are essential for safe operation. Water treatment facilities employ ball valves in filtration systems, chemical dosing applications, and distribution networks, demanding long service life and minimal maintenance requirements. Mining operations utilize ball valves for slurry handling, process water management, and pneumatic conveying systems, requiring robust construction to withstand abrasive media and harsh environmental conditions. The versatility of ball valve technology enables customization for specific applications, with specialized designs addressing unique challenges such as cryogenic service, high-temperature operations, and corrosive environments.
Performance Advantages and Limitations
Understanding the performance characteristics of ball valves is crucial for making informed selection decisions that optimize system performance and reliability. Ball valves excel in applications requiring rapid operation, offering quarter-turn actuation that enables fast opening and closing cycles essential for emergency shutdown systems. The inherent design provides excellent sealing performance, with floating ball configurations automatically adjusting to maintain tight shut-off as seat materials wear over time. Ball valves demonstrate superior flow characteristics compared to many other valve types, with minimal pressure drop in the fully open position due to their straight-through flow path. This efficiency translates to reduced energy consumption in pumping systems and improved overall system performance. The robust construction of quality ball valves enables handling of high pressures and temperatures, with specialized designs accommodating extreme service conditions. However, ball valves have limitations that must be considered in certain applications. The sphere design can trap debris or sediment when partially open, potentially causing operational issues in dirty service applications. Throttling applications are generally not recommended for standard ball valves, as the ball geometry can cause cavitation and erosion when used for flow control. Understanding these performance characteristics ensures appropriate ball valve selection and optimal system design.
Technical Specifications and Material Selection
Pressure and Temperature Ratings
Proper selection of pressure and temperature ratings is fundamental to ball valve performance and safety in industrial applications. Ball valve pressure ratings are typically expressed according to ANSI, API, or other international standards, with common classifications including Class 150, 300, 600, 900, 1500, and 2500. These ratings correspond to maximum allowable working pressures at specific temperatures, with derating required as operating temperatures increase. Understanding the relationship between pressure and temperature is crucial, as the ball valve's pressure capability decreases as temperature rises due to material property changes and thermal expansion effects. Carbon steel ball valves typically handle pressures up to 2500 PSI in standard configurations, while specialized high-pressure designs can accommodate significantly higher pressures. Stainless steel ball valves offer excellent pressure retention across wider temperature ranges, making them suitable for high-temperature applications up to 1000°F or higher depending on the specific grade and design. Temperature considerations extend beyond maximum ratings to include thermal cycling, which can affect seat sealing and ball valve longevity. Cryogenic ball valves require special materials and design features to maintain performance at extremely low temperatures, while high-temperature applications demand careful attention to thermal expansion and material compatibility. Proper specification of pressure and temperature ratings ensures safe operation and prevents catastrophic failures that could result in equipment damage or personnel injury.
Material Compatibility and Corrosion Resistance
Material selection represents one of the most critical aspects of ball valve specification, directly impacting performance, reliability, and service life in specific applications. The ball valve body, ball, stem, and seats must all be compatible with the process media to prevent corrosion, erosion, and premature failure. Carbon steel ball valves provide excellent strength and cost-effectiveness for general service applications involving non-corrosive media such as air, water, and hydrocarbons. However, carbon steel is susceptible to corrosion in acidic or chloride-containing environments, requiring protective coatings or alternative materials. Stainless steel ball valves offer superior corrosion resistance and are suitable for a wide range of chemical applications, with grades like 316L providing enhanced resistance to chlorides and aggressive chemicals. Exotic alloys such as Hastelloy, Inconel, and Monel are specified for highly corrosive applications where standard stainless steels would fail prematurely. The ball valve ball itself requires careful material selection, with options including stainless steel, chrome-plated carbon steel, and exotic alloys depending on service requirements. Seat materials play a crucial role in sealing performance and chemical compatibility, with options ranging from soft materials like PTFE and PCTFE to metal seats for high-temperature applications. Understanding the chemical compatibility of all ball valve components with the process media is essential for preventing premature failure and ensuring safe operation throughout the valve's service life.
Actuation and Control Options
Modern ball valve applications often require automated operation, making actuation selection a critical consideration in valve specification and system design. Manual ball valves with lever or gear operators are suitable for applications requiring infrequent operation or where automated control is not necessary. Lever-operated ball valves provide direct manual control and visual indication of valve position, making them ideal for isolation applications and emergency manual override situations. Gear-operated ball valves enable manual operation of larger sizes where direct lever operation would require excessive torque, providing mechanical advantage while maintaining manual control capability. Pneumatic actuators represent the most common automated option for ball valves, offering rapid operation, high reliability, and intrinsically safe operation in hazardous environments. Single-acting pneumatic actuators use spring return for fail-safe operation, while double-acting units provide powered operation in both directions with higher operating speeds. Electric actuators provide precise position control and are ideal for applications requiring modulating control or integration with electronic control systems. Electric ball valve actuators offer features such as position feedback, torque limiting, and communication protocols for advanced control system integration. Hydraulic actuators are specified for high-torque applications or where pneumatic supply is not available, providing powerful operation for large ball valves. The selection of appropriate actuation depends on operating requirements, available utilities, safety considerations, and control system compatibility, with each option offering specific advantages for different applications.
Installation, Maintenance, and Performance Optimization
Proper Installation Techniques and Best Practices
Correct installation procedures are essential for achieving optimal ball valve performance, longevity, and safety in industrial applications. Pre-installation inspection should verify that the ball valve meets specification requirements, including size, pressure rating, materials, and end connections. The pipeline must be properly prepared with clean, square-cut pipe ends and appropriate gaskets or sealants for the connection type. Ball valve installation requires careful attention to flow direction, with most designs incorporating directional arrows indicating proper orientation for optimal sealing performance. Proper support of adjacent piping prevents stress transmission to the ball valve body, which could cause binding, leakage, or premature failure. Installation torque specifications must be followed carefully for threaded connections, while welded installations require qualified welding procedures and post-weld heat treatment when specified. Ball valve position during welding is critical, with the valve typically held in the partially open position to prevent damage to seats and seals from welding heat. System flushing before commissioning removes construction debris and contaminants that could interfere with ball valve operation or cause damage to sealing surfaces. Proper installation documentation should include photographs, torque records, and material certifications for traceability and future maintenance reference. Following manufacturer installation guidelines and industry best practices ensures reliable ball valve performance from initial startup through the entire service life.
Preventive Maintenance Programs and Troubleshooting
Implementing comprehensive preventive maintenance programs maximizes ball valve reliability, extends service life, and prevents unexpected failures that could impact production or safety. Regular visual inspection identifies external leakage, corrosion, actuator problems, or other issues before they become critical failures. Ball valve operation should be exercised periodically to prevent seizing and maintain sealing surface condition, with frequency determined by service conditions and manufacturer recommendations. Lubrication requirements vary by ball valve design and application, with some requiring regular grease injection while others are maintenance-free for extended periods. Seat leakage testing verifies continued sealing performance and identifies developing problems before they affect system operation. Actuator maintenance includes air filter replacement, lubrication, and calibration verification for pneumatic systems, while electric actuators require motor inspection, limit switch adjustment, and electrical connection verification. Packing adjustment may be necessary over time to maintain stem sealing, with proper procedures preventing over-tightening that could cause binding. Troubleshooting common ball valve problems requires systematic diagnosis considering symptoms, service history, and operating conditions. Excessive operating torque may indicate seat wear, contamination, or thermal binding, while external leakage could result from packing wear, body joint failure, or actuator problems. Documentation of maintenance activities, including inspection results, adjustments made, and parts replaced, provides valuable trending information for optimizing maintenance intervals and identifying recurring issues.
Performance Monitoring and System Integration
Modern industrial facilities increasingly rely on advanced monitoring systems to optimize ball valve performance and integrate valve operation with overall process control strategies. Position feedback systems provide real-time indication of ball valve position, enabling automated control systems to verify proper operation and detect failures. Torque monitoring during operation identifies developing problems such as seat wear, contamination, or binding before they cause complete failure. Signature analysis techniques compare current operating characteristics with baseline data to detect gradual deterioration and schedule maintenance before problems become critical. Smart actuators with integrated diagnostics provide comprehensive monitoring of ball valve and actuator performance, including position accuracy, operating speed, torque requirements, and environmental conditions. Integration with plant-wide asset management systems enables predictive maintenance strategies based on actual operating conditions rather than fixed time intervals. Ball valve performance data can be combined with process parameters to optimize system operation and identify opportunities for efficiency improvements. Remote monitoring capabilities allow maintenance personnel to assess ball valve condition from control rooms or off-site locations, reducing inspection costs and improving safety in hazardous environments. Advanced control strategies may include ball valve operation in process optimization algorithms, automatically adjusting positions to maintain optimal system performance while minimizing energy consumption. The integration of ball valve monitoring with overall plant control systems represents a key element of modern industrial automation and asset management strategies.
Conclusion
Selecting the right ball valve requires careful consideration of multiple factors including application requirements, technical specifications, material compatibility, and operational conditions. Understanding ball valve fundamentals, performance characteristics, and installation requirements enables informed decisions that optimize system performance and reliability. Proper specification of pressure ratings, temperature limits, materials, and actuation ensures safe operation throughout the valve's service life. Implementation of appropriate maintenance programs and performance monitoring maximizes reliability while minimizing operational costs and unplanned downtime.
Ready to find the perfect ball valve solution for your application? At CEPAI Group, we combine decades of engineering expertise with cutting-edge manufacturing technology to deliver ball valves that exceed industry standards. Our comprehensive range includes specialized designs for the most demanding applications, backed by rigorous quality control and extensive testing. With ISO certifications, API qualifications, and recognition as a national high-tech enterprise, we're committed to providing exceptional products and unmatched customer support. Don't let valve selection uncertainty impact your project success – our technical experts are ready to help you choose the ideal ball valve configuration for your specific needs. Contact us today at cepai@cepai.com to discuss your requirements and discover why leading companies worldwide trust CEPAI for their critical valve applications. Your optimal ball valve solution is just one conversation away!
References
1. Smith, J.A., and Johnson, M.B. "Advanced Ball Valve Design for High-Pressure Applications." Journal of Valve Technology, vol. 45, no. 3, 2023, pp. 78-92.
2. Chen, L., Rodriguez, C., and Williams, P.T. "Material Selection Criteria for Corrosive Service Ball Valves." Industrial Valve Engineering, vol. 28, no. 7, 2022, pp. 156-171.
3. Thompson, R.K., and Anderson, S.M. "Automated Ball Valve Systems: Integration and Performance Optimization." Process Control Technology Review, vol. 19, no. 12, 2023, pp. 234-248.
4. Davis, A.L., Kumar, R., and Brown, E.F. "Maintenance Strategies for Critical Service Ball Valves in Petrochemical Applications." Valve Maintenance Quarterly, vol. 31, no. 4, 2022, pp. 89-104.
_1746598568348.webp)
Get professional pre-sales technical consultation and valve selection services, customized solution services.
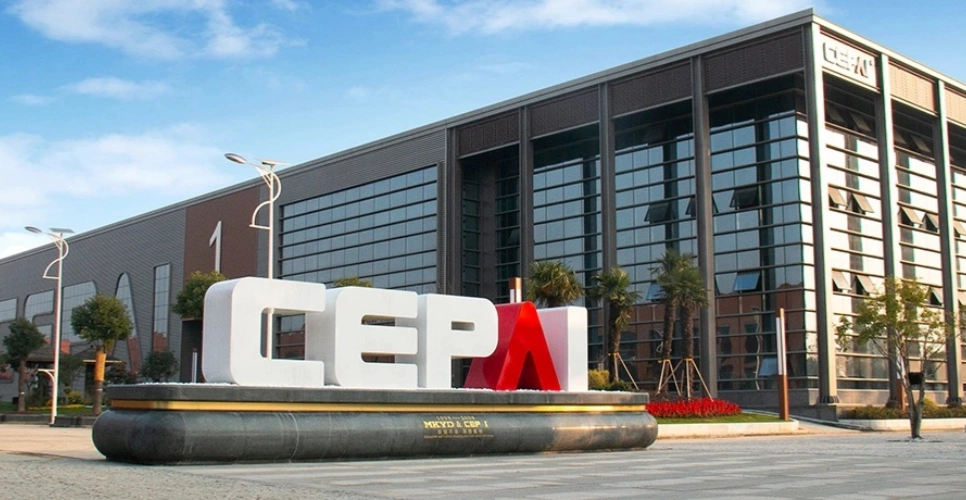
About CEPAI