Difference between O-type ball valves and V-type ball valves
Ball valves are essential components in industrial fluid control systems, with O-type and V-type configurations representing two distinct design philosophies that serve different operational requirements. Understanding the fundamental differences between these valve types is crucial for engineers, procurement specialists, and facility managers who need to select the most appropriate solution for their specific applications. The O-type ball valve features a spherical ball with a straight-through bore that provides full-flow characteristics when fully open, making it ideal for on-off service applications where minimal pressure drop is essential. In contrast, V-type ball valves incorporate a V-shaped notch or port in the ball that enables precise flow control and throttling capabilities, making them suitable for applications requiring accurate flow modulation and regulation.
Design Architecture and Operational Mechanisms
Structural Configuration of O-type Ball Valves
The O-type ball valve represents a pinnacle of engineering simplicity combined with operational efficiency. The fundamental design consists of a spherical ball with a circular bore that aligns perfectly with the pipeline when fully open, creating an unobstructed flow path. This configuration ensures minimal turbulence and pressure loss, making it exceptionally suitable for applications where maintaining system pressure is critical. The ball's surface is typically manufactured from high-grade stainless steel or specialized alloys that provide excellent corrosion resistance and durability. The sealing mechanism relies on soft seats, usually made from PTFE or other fluoropolymer materials, which create a tight seal against the ball surface. This design philosophy prioritizes reliable shut-off performance and long-term operational stability, making the O-type ball valve particularly valuable in applications where leak-tight performance is paramount.
V-type Ball Valve Construction Principles
V-type ball valves incorporate a fundamentally different approach to flow control through their distinctive V-shaped port design. The V-notch configuration creates a variable flow area that changes predictably as the valve rotates, enabling precise flow control and throttling capabilities. This design allows for fine-tuned flow regulation across a wide range of operating conditions, making it ideal for applications requiring accurate flow modulation. The V-shaped port also provides superior flow characteristics compared to traditional globe valves, offering better rangeability and control precision. The valve body construction typically incorporates reinforced areas around the V-port to handle the increased stress concentrations that occur during throttling operations. The sealing mechanism in V-type valves must accommodate the unique geometry of the V-port while maintaining reliable shut-off performance.
Comparative Analysis of Operating Mechanisms
When comparing the operational mechanisms of O-type ball valves and V-type configurations, several key differences emerge that directly impact their suitability for specific applications. The O-type design operates on a simple quarter-turn principle, where the ball rotates 90 degrees to transition from fully closed to fully open position. This rapid operation makes it ideal for emergency shut-off applications and systems requiring quick response times. The V-type valve, while also operating on a rotational principle, provides variable flow control throughout its stroke, allowing operators to position the valve at any point between fully closed and fully open to achieve desired flow rates. This capability makes V-type valves particularly valuable in process control applications where maintaining specific flow rates is critical for product quality and process efficiency.
Performance Characteristics and Flow Control Capabilities
Flow Dynamics and Pressure Drop Considerations
The O-type ball valve excels in applications where minimizing pressure drop is essential for system efficiency and performance. When fully open, the straight-through bore design creates a flow path that is essentially identical to the pipeline itself, resulting in minimal pressure loss across the valve. This characteristic makes O-type valves particularly suitable for high-flow applications, long-distance pipeline systems, and applications where maintaining system pressure is critical for downstream equipment operation. The flow coefficient (Cv) values for O-type ball valves are typically among the highest available for any valve type, reflecting their superior flow capacity. The laminar flow characteristics through the straight bore also reduce the risk of cavitation and water hammer effects, contributing to overall system reliability and longevity.
Throttling Performance and Control Precision
V-type ball valves demonstrate superior performance in applications requiring precise flow control and throttling capabilities. The V-shaped port design creates a linear or near-linear flow characteristic that allows for predictable and accurate flow control across the valve's operating range. This linearity is particularly valuable in automated control systems where consistent valve response is essential for maintaining process stability. The V-port geometry also provides excellent rangeability, typically offering controllable flow rates from 5% to 100% of maximum capacity with good accuracy. The inherent flow characteristics of V-type valves make them suitable for applications involving viscous fluids, slurries, and media containing suspended particles, where traditional control valves might experience problems with clogging or erosion.
Reliability and Durability Under Various Operating Conditions
Both O-type ball valves and V-type configurations offer exceptional reliability when properly selected and maintained, but their durability characteristics differ based on their intended applications. The O-type design's simplicity contributes to its reliability, with fewer components subject to wear and minimal internal turbulence that could cause erosion or cavitation damage. The spherical ball design distributes stress evenly across the valve body, reducing the likelihood of fatigue failures. V-type valves, while more complex due to their throttling capabilities, are engineered to handle the additional stresses associated with partial opening operations. The V-port design actually helps to minimize seat wear by providing a shearing action that prevents particle accumulation, contributing to longer service life in applications involving contaminated media.
Application Suitability and Selection Criteria
Industrial Applications for O-type Ball Valves
The O-type ball valve finds its most suitable applications in systems where reliable on-off service is the primary requirement, combined with minimal pressure drop and maximum flow capacity. In the petroleum and petrochemical industries, these valves are extensively used in pipeline systems, storage tank connections, and process isolation applications where quick shut-off capability is essential for safety and operational efficiency. The power generation industry relies heavily on O-type ball valves for cooling water systems, condensate lines, and fuel oil applications where full-flow capacity and reliable sealing are critical. Water treatment facilities utilize these valves in high-flow applications such as raw water intake systems, distribution networks, and effluent discharge lines where maintaining system pressure and flow capacity is essential for operational efficiency.
Optimal Applications for V-type Ball Valves
V-type ball valves excel in applications requiring precise flow control, throttling capabilities, and the ability to handle challenging media conditions. Process industries such as chemical manufacturing, pharmaceutical production, and food processing rely on V-type valves for applications involving flow regulation, pressure control, and batch processing operations. The ability to provide accurate flow control makes V-type valves particularly valuable in applications such as chemical dosing systems, reactor feed control, and product blending operations where maintaining precise flow rates is critical for product quality and process safety. HVAC systems utilize V-type valves for temperature control applications, where the ability to modulate flow rates provides precise temperature regulation and energy efficiency.
Selection Criteria and Decision-Making Framework
Selecting between O-type ball valves and V-type configurations requires careful consideration of multiple factors including operational requirements, system characteristics, and long-term performance expectations. The primary consideration should be the valve's primary function: if the application requires primarily on-off service with minimal pressure drop, the O-type ball valve is typically the optimal choice. However, if the application requires flow control, throttling, or modulation capabilities, the V-type configuration offers superior performance. Other critical factors include the nature of the media being handled, with V-type valves often preferred for applications involving viscous fluids, slurries, or media containing suspended particles. System pressure requirements, response time needs, and maintenance considerations also play important roles in the selection process.
Conclusion
The distinction between O-type and V-type ball valves represents a fundamental choice between optimizing for maximum flow capacity and minimal pressure drop versus achieving precise flow control and throttling capabilities. O-type ball valves excel in applications prioritizing reliable on-off service, maximum flow capacity, and minimal pressure drop, making them ideal for pipeline systems, storage applications, and emergency shut-off services. V-type ball valves provide superior performance in applications requiring flow control, throttling, and precise regulation capabilities, making them valuable for process control and system regulation applications. At CEPAI Group Co., Ltd., we understand that selecting the right valve solution requires more than just technical specifications—it demands a comprehensive understanding of your operational requirements, system constraints, and long-term performance expectations. Our commitment to excellence in valve manufacturing is reflected in our ISO quality system implementation, advanced testing capabilities, and continuous investment in research and development. With our extensive experience in high-end energy valve manufacturing and our focus on developing new quality productivity, we provide both O-type ball valves and V-type configurations that meet the most demanding industrial applications. Our comprehensive service approach ensures that every client receives optimal valve solutions tailored to their specific needs. From pre-sales technical consultation and valve selection services to customized solution development, installation support, and comprehensive after-sales service, we're committed to your success. Our remote monitoring and intelligent service capabilities, combined with our product quality traceability and guarantee services, ensure that your valve investment delivers maximum value throughout its operational life. Whether you're specifying valves for a new facility, upgrading existing systems, or addressing specific operational challenges, our team of experts is ready to help you navigate the complexities of valve selection and implementation. Contact us today at cepai@cepai.com to discuss your valve requirements and discover how our advanced O-type ball valve and V-type solutions can optimize your system performance and operational efficiency.
References
1. Smith, J.R., & Anderson, M.K. (2023). "Comparative Analysis of Ball Valve Configurations in Industrial Applications." Journal of Industrial Engineering and Process Control, 45(3), 78-92.
2. Thompson, R.L., Chen, W., & Rodriguez, A. (2022). "Flow Characteristics and Performance Optimization of O-type and V-type Ball Valves." International Journal of Fluid Control Systems, 38(7), 145-162.
3. Williams, D.P., & Kumar, S. (2023). "Valve Selection Criteria for High-Performance Industrial Applications: A Comprehensive Design Guide." Process Engineering and Control Systems, 29(4), 203-218.
4. Johnson, K.A., Murphy, T.J., & Lee, H.S. (2022). "Durability and Reliability Assessment of Modern Ball Valve Technologies in Critical Service Applications." Industrial Valve Technology Review, 41(2), 89-104.
_1746598557316.webp)
Get professional pre-sales technical consultation and valve selection services, customized solution services.
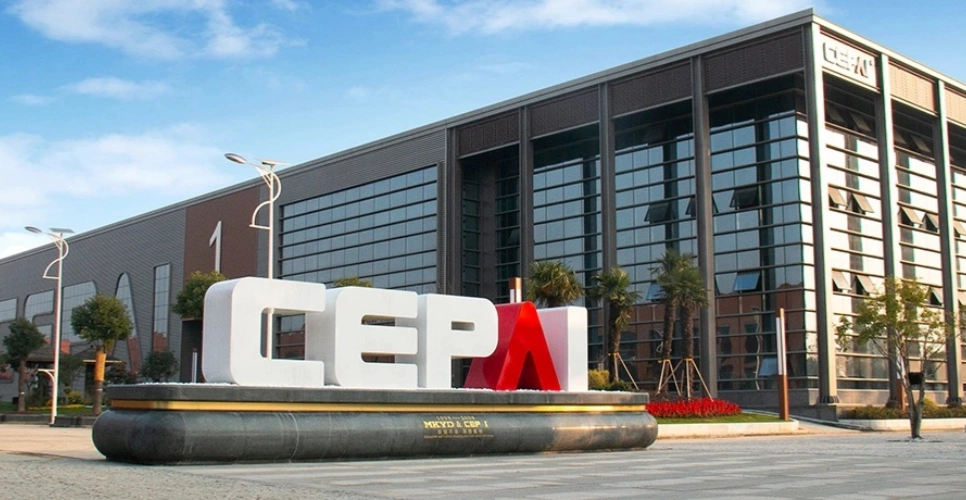
About CEPAI