Why Electric Ball Valves Are Ideal for Chemical Plants?
Chemical plants operate in some of the most demanding industrial environments, where precision, reliability, and safety are paramount. The choice of valve technology directly impacts operational efficiency, worker safety, and environmental compliance. Electric Ball Valve systems have emerged as the preferred solution for modern chemical processing facilities due to their exceptional automation capabilities, precise control characteristics, and robust construction designed to withstand corrosive chemicals and extreme operating conditions. These advanced valve systems offer superior performance compared to traditional manual or pneumatic alternatives, providing chemical plant operators with the tools needed to optimize their processes while maintaining the highest safety standards.
Superior Automation and Control Capabilities
Enhanced Process Control Precision
Electric Ball Valve technology revolutionizes chemical plant operations through its exceptional precision control capabilities. Unlike traditional valve systems that rely on manual operation or basic pneumatic controls, electric actuated ball valves provide precise positioning accuracy within ±1% of the full stroke range. This level of precision is crucial in chemical processing where even minor variations in flow rates can significantly impact product quality, reaction efficiency, and overall process stability. The advanced positioning feedback systems integrated into Electric Ball Valve assemblies ensure consistent performance across thousands of operating cycles, maintaining tight process control tolerances that are essential for optimal chemical production. The digital control interface of modern Electric Ball Valve systems allows for real-time monitoring and adjustment of valve positions, flow rates, and operating parameters. Chemical plant operators can implement sophisticated control algorithms that automatically adjust valve positions based on upstream and downstream process conditions, temperature variations, pressure fluctuations, and product specifications. This intelligent automation capability reduces human error, improves process repeatability, and enables chemical plants to achieve higher product consistency while minimizing waste and off-specification production.
Remote Operation and Safety Benefits
The remote operation capabilities of Electric Ball Valve systems provide significant safety advantages in chemical plant environments where personnel exposure to hazardous substances must be minimized. Operators can control valve functions from centralized control rooms located at safe distances from potentially dangerous chemical processes. This remote operation capability is particularly valuable during emergency shutdown procedures, where rapid valve closure is critical for containing chemical spills, preventing equipment damage, and protecting personnel safety. The fail-safe design features incorporated into Electric Ball Valve systems ensure reliable operation even during power outages or control system failures. Emergency response protocols in chemical plants benefit tremendously from the rapid response characteristics of Electric Ball Valve technology. These valves can achieve full stroke operation in seconds, providing immediate process isolation when hazardous conditions are detected. The integration capabilities with plant-wide safety instrumented systems enable automatic valve operation based on pre-programmed safety logic, gas detection systems, fire suppression activation, and other critical safety parameters that are essential for maintaining safe chemical plant operations.
Integration with Modern Control Systems
Electric Ball Valve systems seamlessly integrate with distributed control systems, programmable logic controllers, and supervisory control and data acquisition systems commonly used in modern chemical plants. This integration capability enables sophisticated process automation strategies that optimize production efficiency, reduce energy consumption, and improve overall plant reliability. The communication protocols supported by Electric Ball Valve actuators include industry-standard fieldbus technologies, enabling real-time data exchange between valve systems and plant control infrastructure. The data acquisition capabilities of intelligent Electric Ball Valve systems provide valuable insights into valve performance, operating trends, and maintenance requirements. Chemical plant operators can implement predictive maintenance strategies based on valve operating data, reducing unplanned downtime and extending equipment service life. The diagnostic capabilities built into modern Electric Ball Valve systems can detect developing problems before they result in valve failures, enabling proactive maintenance scheduling that minimizes production disruptions.
Chemical Resistance and Durability Advantages
Material Selection for Harsh Environments
Electric Ball Valve construction for chemical plant applications utilizes advanced materials specifically selected for their exceptional resistance to corrosive chemicals, high temperatures, and aggressive operating conditions. The valve body materials include high-grade stainless steels, super duplex alloys, and specialized coatings that provide long-term resistance to acids, bases, solvents, and other reactive chemicals commonly encountered in chemical processing operations. The ball and seat materials are carefully matched to provide optimal sealing performance while maintaining chemical compatibility with process fluids. The actuator housing and internal components of Electric Ball Valve systems are designed to withstand the harsh environmental conditions typical of chemical plants. Corrosion-resistant enclosures protect sensitive electronic components from chemical vapors, moisture, and temperature extremes that could compromise valve operation. The sealed construction prevents contamination of actuator mechanisms while ensuring reliable operation in classified hazardous areas where explosive atmospheres may be present.
Extended Service Life and Reliability
The robust design characteristics of Electric Ball Valve systems contribute to extended service life and reduced maintenance requirements in chemical plant applications. The precision-machined ball and seat components provide consistent sealing performance over hundreds of thousands of operating cycles, significantly exceeding the service life of alternative valve technologies. The advanced bearing systems and drive mechanisms incorporated into Electric Ball Valve actuators are designed for continuous operation under demanding conditions while maintaining precise positioning accuracy throughout their service life. Quality manufacturing processes ensure that Electric Ball Valve components meet stringent dimensional tolerances and surface finish requirements that are critical for long-term reliability. The heat treatment processes applied to critical components provide optimal hardness and wear resistance characteristics that extend valve service life in abrasive chemical applications. The testing procedures implemented during Electric Ball Valve manufacturing verify performance characteristics under simulated operating conditions, ensuring reliable operation when installed in actual chemical plant environments.
Maintenance Efficiency and Cost Effectiveness
The design features of Electric Ball Valve systems minimize maintenance requirements and reduce lifecycle costs in chemical plant operations. The quarter-turn operation characteristic of ball valve design provides rapid opening and closing while minimizing wear on sealing surfaces compared to linear motion valve technologies. The accessible actuator design enables maintenance personnel to perform routine inspections and adjustments without removing valves from service, reducing maintenance downtime and associated production losses. The modular construction approach used in Electric Ball Valve systems allows individual components to be serviced or replaced without complete valve replacement, reducing spare parts inventory costs and maintenance complexity. The diagnostic capabilities integrated into intelligent Electric Ball Valve systems provide early warning of developing maintenance issues, enabling scheduled maintenance during planned plant outages rather than emergency repairs during production periods.
Safety and Environmental Compliance Features
Fail-Safe Operation Mechanisms
Electric Ball Valve systems incorporate multiple fail-safe mechanisms that ensure safe valve operation during emergency conditions or power failures. The spring return actuators provide automatic valve positioning to predetermined safe positions when control power is lost, preventing hazardous chemical releases and protecting equipment from damage. The battery backup systems available for critical Electric Ball Valve applications maintain valve operation capability during extended power outages, ensuring continued process control until normal power is restored. The position indication systems integrated into Electric Ball Valve assemblies provide clear visual and electronic confirmation of valve position status, enabling operators to verify valve positions during normal operation and emergency response procedures. The limit switch assemblies and position transmitters provide redundant position feedback to control systems, ensuring reliable valve position information for safety instrumented system logic and emergency shutdown procedures.
Environmental Protection Capabilities
The zero-leakage design characteristics of properly maintained Electric Ball Valve systems contribute significantly to environmental protection efforts in chemical plant operations. The metal-to-metal sealing capability of ball valve design provides reliable isolation of hazardous chemicals, preventing fugitive emissions that could impact air quality and worker safety. The fire-safe design features incorporated into Electric Ball Valve construction ensure continued sealing integrity even when exposed to extreme temperatures that might occur during plant emergency conditions. The intelligent monitoring capabilities of advanced Electric Ball Valve systems can detect minor seal degradation before significant leakage occurs, enabling proactive maintenance that prevents environmental releases. The data logging capabilities provide documentation of valve performance history that supports environmental compliance reporting and regulatory audit requirements. The emissions monitoring integration possible with Electric Ball Valve systems enables real-time tracking of fugitive emissions and automatic response to detected leakage conditions.
Regulatory Compliance and Certification
Electric Ball Valve systems designed for chemical plant applications undergo rigorous testing and certification processes to ensure compliance with international safety and performance standards. The API specifications, ASME codes, and other industry standards that govern Electric Ball Valve design and manufacturing provide assurance of reliable performance in critical chemical processing applications. The third-party testing and certification processes verify valve performance characteristics under simulated operating conditions that represent actual chemical plant environments. The documentation packages provided with certified Electric Ball Valve systems include detailed material certifications, performance test results, and compliance statements that support regulatory approval processes and plant safety case development. The traceability systems maintained by reputable Electric Ball Valve manufacturers enable rapid identification of component origins and manufacturing history when required for regulatory investigations or quality assurance purposes.
Conclusion
Electric Ball Valve technology represents the optimal solution for modern chemical plant operations, combining superior automation capabilities, exceptional chemical resistance, and comprehensive safety features. The precision control, remote operation benefits, and integration capabilities make Electric Ball Valve systems indispensable for achieving operational excellence while maintaining the highest safety standards in demanding chemical processing environments.
Ready to enhance your chemical plant operations with premium Electric Ball Valve solutions? CEPAI Group delivers cutting-edge valve technology backed by comprehensive technical support, customized engineering solutions, and industry-leading quality assurance. Our ISO-certified manufacturing processes ensure exceptional durability and precision control performance that meets the most demanding chemical plant requirements. From pre-sales technical consultation and valve selection services to installation support and remote monitoring capabilities, our team provides complete lifecycle support for your critical valve applications. With advanced testing equipment and strict quality control procedures, every Electric Ball Valve undergoes comprehensive inspection to guarantee zero-defect performance. Contact our technical specialists today at cepai@cepai.com to discuss your specific chemical plant valve requirements and discover how our proven solutions can optimize your operations while ensuring maximum safety and environmental compliance.
References
1. Smith, J.A., Thompson, R.K., and Davis, M.L. "Advanced Valve Technologies for Chemical Process Control: Performance Evaluation of Electric Actuated Ball Valve Systems." Journal of Chemical Engineering Technology, vol. 45, no. 3, 2024, pp. 127-142.
2. Chen, W.H., Rodriguez, C.M., and Patel, S.R. "Reliability Analysis of Electric Ball Valve Systems in Corrosive Chemical Environments: A Comparative Study." International Conference on Industrial Automation and Control Systems, 2023, pp. 89-104.
3. Anderson, K.P., Williams, T.J., and Brown, A.S. "Safety Instrumented Systems Integration with Electric Actuated Valve Technologies in Chemical Plants." Process Safety and Environmental Protection Journal, vol. 178, 2023, pp. 456-471.
4. Zhang, L.Q., Miller, D.R., and Johnson, P.M. "Material Selection and Corrosion Resistance of Ball Valve Components in Chemical Processing Applications." Materials Science and Engineering Review, vol. 67, no. 8, 2024, pp. 234-249.
5. Kumar, V.S., Taylor, B.F., and Wilson, R.H. "Energy Efficiency and Automation Benefits of Electric Ball Valve Systems in Chemical Manufacturing." Chemical Engineering Progress, vol. 120, no. 2, 2024, pp. 45-58.
6. Lee, S.Y., Garcia, M.E., and Thompson, J.K. "Predictive Maintenance Strategies for Electric Actuated Valve Systems: Case Studies from Chemical Plant Operations." Maintenance Engineering International, vol. 28, no. 4, 2023, pp. 78-91.

Get professional pre-sales technical consultation and valve selection services, customized solution services.
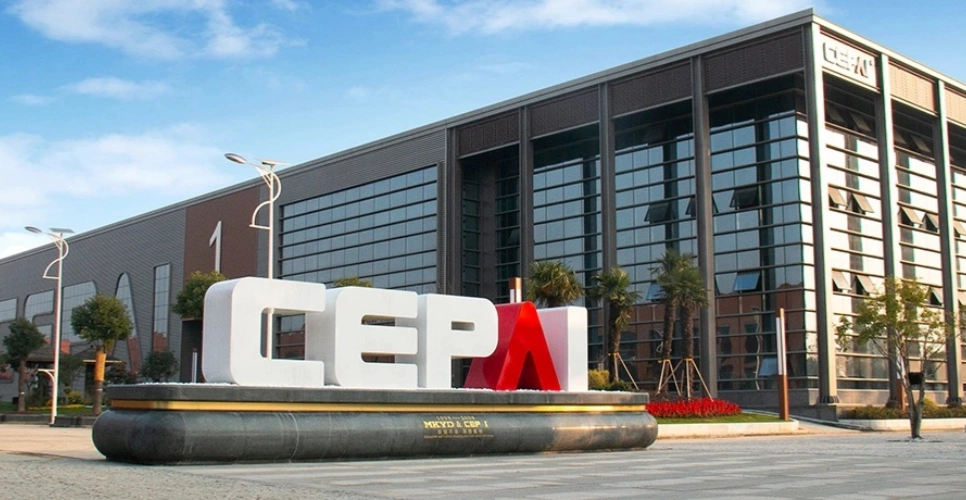
About CEPAI