Top Innovations in Pneumatic Valve Technology for 2025
The landscape of industrial automation continues to evolve rapidly, with pneumatic valve technology leading the charge in 2025. As industries demand higher precision, enhanced reliability, and smarter control systems, manufacturers are pushing the boundaries of what's possible with pneumatic valve innovations. From advanced materials that offer superior corrosion resistance to intelligent monitoring systems that predict maintenance needs, the latest developments in pneumatic valve technology are revolutionizing how we approach fluid control in critical applications. These innovations address key industry challenges including precise flow control, rapid response times, and long-term durability while maintaining cost-effectiveness. The integration of digital technologies with traditional pneumatic systems has created new possibilities for remote monitoring, predictive maintenance, and enhanced operational efficiency across various sectors.
Smart Control Systems and Digital Integration
Advanced Electronic Pneumatic Positioners
The integration of sophisticated electronic pneumatic positioners represents a quantum leap in pneumatic valve control precision. Modern positioners utilize advanced algorithms and high-resolution sensors to achieve positioning accuracies within ±0.1% of full scale, dramatically improving process control capabilities. These systems incorporate real-time feedback mechanisms that continuously monitor valve position and automatically compensate for any deviations, ensuring consistent performance even under varying process conditions. The pneumatic valve systems equipped with these positioners can respond to control signals within milliseconds, enabling rapid process adjustments that were previously impossible with conventional mechanical systems. The latest generation of electronic positioners features built-in diagnostic capabilities that monitor valve health parameters including stem position, actuator pressure, and internal component wear. This continuous monitoring enables predictive maintenance strategies that reduce unplanned downtime and extend equipment lifecycle. Furthermore, these smart positioners can communicate with distributed control systems using various protocols including HART, Foundation Fieldbus, and PROFIBUS, providing seamless integration into existing plant infrastructure while offering enhanced data visibility for operators and maintenance personnel.
Wireless Communication and Remote Monitoring
Wireless technology integration has transformed how pneumatic valve systems are monitored and controlled in modern industrial environments. Advanced wireless communication modules enable real-time data transmission from pneumatic valve assemblies to central control systems, eliminating the need for extensive hardwired connections while providing unprecedented operational visibility. These systems utilize secure wireless protocols that ensure data integrity and system security while enabling remote access to critical valve performance parameters including position feedback, actuator pressure, and environmental conditions. The implementation of wireless monitoring systems has proven particularly valuable in hazardous or remote locations where traditional wiring is impractical or dangerous. Operators can now monitor pneumatic valve performance from safe distances, receiving instant alerts about abnormal conditions or maintenance requirements. This capability not only enhances safety but also enables proactive maintenance scheduling that minimizes production interruptions. The wireless systems also support over-the-air firmware updates, ensuring that pneumatic valve controllers remain current with the latest performance enhancements and security features without requiring physical access to equipment.
Artificial Intelligence and Machine Learning Integration
The incorporation of artificial intelligence and machine learning algorithms into pneumatic valve control systems represents the cutting edge of industrial automation technology. These intelligent systems analyze vast amounts of operational data to identify patterns and optimize valve performance automatically, learning from historical performance data to predict optimal control strategies for varying process conditions. Machine learning algorithms can detect subtle changes in pneumatic valve behavior that might indicate developing problems, enabling maintenance interventions before failures occur. AI-powered pneumatic valve systems can automatically adjust control parameters to compensate for process variations, wear patterns, and environmental changes, maintaining optimal performance throughout the equipment lifecycle. These systems continuously refine their control strategies based on real-world performance data, becoming more effective over time. The predictive capabilities of AI-enhanced pneumatic valve controllers enable operators to schedule maintenance activities during planned downtime, reducing the impact on production while ensuring optimal equipment reliability and performance.
Advanced Materials and Enhanced Durability
High-Performance Alloys and Composite Materials
The development of advanced materials has significantly enhanced the durability and performance capabilities of pneumatic valve components in demanding industrial applications. Modern high-performance alloys incorporate specialized compositions that provide superior resistance to corrosion, erosion, and extreme temperatures while maintaining the mechanical properties essential for reliable operation. These materials enable pneumatic valve systems to operate effectively in harsh chemical environments, high-pressure applications, and extreme temperature conditions that would quickly degrade conventional materials. Composite materials have emerged as game-changers in pneumatic valve design, offering unique combinations of properties that were previously unattainable with traditional materials. Carbon fiber reinforced polymers provide exceptional strength-to-weight ratios while offering excellent chemical resistance, making them ideal for aerospace and chemical processing applications. Ceramic matrix composites deliver outstanding wear resistance and thermal stability, enabling pneumatic valve components to maintain precise tolerances even under extreme operating conditions. These advanced materials also contribute to reduced maintenance requirements and extended service intervals, providing significant cost savings over the equipment lifecycle.
Innovative Sealing Technologies
Revolutionary sealing technologies have transformed the reliability and performance of pneumatic valve systems, addressing long-standing challenges related to leakage, wear, and maintenance requirements. Advanced elastomer formulations incorporate nanotechnology enhancements that provide superior sealing performance while resisting degradation from aggressive chemicals, extreme temperatures, and high-pressure differentials. These innovative sealing materials maintain their flexibility and sealing properties over extended service periods, reducing maintenance requirements and improving operational reliability. Metal-to-metal sealing systems represent another significant advancement in pneumatic valve technology, utilizing precision-machined surfaces and advanced surface treatments to achieve zero-leakage performance without relying on soft sealing materials. These systems are particularly valuable in high-temperature applications where conventional elastomeric seals would quickly degrade. The development of self-healing seal materials that can automatically repair minor damage extends seal life while maintaining consistent performance, reducing the frequency of maintenance interventions and improving overall system reliability.
Corrosion-Resistant Surface Treatments
Advanced surface treatment technologies have revolutionized the corrosion resistance capabilities of pneumatic valve components, enabling reliable operation in the most demanding chemical environments. Plasma-enhanced chemical vapor deposition techniques create ultra-thin protective coatings that provide exceptional corrosion resistance while maintaining precise dimensional tolerances essential for proper valve operation. These coatings can be tailored to specific chemical environments, providing optimal protection against particular aggressive media. Nanostructured surface treatments create self-cleaning and anti-fouling properties that prevent the buildup of deposits that could interfere with pneumatic valve operation. These advanced surface treatments also incorporate antimicrobial properties that prevent biological growth in systems handling contaminated fluids. The durability of these protective coatings ensures long-term performance even under severe operating conditions, reducing maintenance requirements and extending equipment service life while maintaining optimal flow control characteristics throughout the operational period.
Enhanced Safety and Reliability Features
Fail-Safe Mechanisms and Emergency Shutdown Systems
Modern pneumatic valve systems incorporate sophisticated fail-safe mechanisms that ensure safe plant shutdown in emergency situations while protecting personnel and equipment from potential hazards. Advanced spring-return actuators utilize optimized spring designs that provide reliable fail-safe operation even after extended service periods, ensuring that pneumatic valve systems move to predetermined safe positions upon loss of control signal or pneumatic supply. These systems incorporate redundant safety features that provide multiple levels of protection against potential failure modes. Emergency shutdown systems integrated with pneumatic valve assemblies utilize rapid-acting mechanisms that can isolate process sections within seconds of receiving shutdown signals. These systems incorporate pilot-operated safety valves that provide immediate pressure relief while main isolation valves move to closed positions, preventing overpressure conditions that could damage equipment or endanger personnel. The reliability of these safety systems is enhanced through regular automated testing sequences that verify proper operation without disrupting normal plant operations, ensuring that critical safety functions remain operational when needed.
Predictive Maintenance and Health Monitoring
Integrated health monitoring systems represent a major advancement in pneumatic valve reliability, utilizing sophisticated sensor arrays to continuously monitor critical performance parameters and component conditions. These systems track valve stem position, actuator pressure variations, response times, and vibration signatures to identify developing problems before they result in equipment failures. Advanced diagnostic algorithms analyze this data to predict maintenance requirements and optimize service intervals based on actual equipment condition rather than predetermined schedules. The implementation of condition-based maintenance strategies enabled by these monitoring systems has proven highly effective in reducing unplanned downtime while optimizing maintenance costs. Pneumatic valve systems equipped with health monitoring capabilities can automatically generate maintenance work orders when specific condition thresholds are exceeded, ensuring that necessary maintenance activities are performed before equipment failures occur. These systems also maintain detailed historical records of valve performance and maintenance activities, enabling continuous improvement of maintenance strategies and optimization of spare parts inventory.
Explosion-Proof and Hazardous Area Certifications
The development of pneumatic valve systems specifically designed for hazardous area applications has addressed critical safety requirements in chemical processing, oil and gas, and pharmaceutical industries. These systems incorporate explosion-proof enclosures that contain any potential ignition sources while maintaining full operational capabilities in classified hazardous locations. Advanced purging systems utilize compressed air or inert gas to maintain positive pressure within electrical enclosures, preventing the ingress of flammable gases or vapors that could create dangerous conditions. Certification compliance with international standards including ATEX, IECEx, and NEC ensures that pneumatic valve systems can be safely installed and operated in hazardous environments worldwide. These certifications require extensive testing and documentation to verify that equipment meets stringent safety requirements under all specified operating conditions. The availability of certified pneumatic valve systems enables plant designers to specify equipment with confidence while ensuring compliance with safety regulations and insurance requirements.
Conclusion
The pneumatic valve industry has experienced remarkable technological advancement in 2025, with innovations spanning smart control systems, advanced materials, and enhanced safety features. These developments have addressed critical industry needs for precise control, rapid response, and exceptional reliability while maintaining cost-effectiveness. The integration of digital technologies with traditional pneumatic systems has created new possibilities for predictive maintenance and operational optimization that benefit industries worldwide.
Ready to experience these cutting-edge pneumatic valve innovations for your applications? CEPAI Group Co., Ltd. stands as your trusted China Pneumatic Valve factory, offering comprehensive solutions backed by our advanced manufacturing capabilities and quality certifications. As a leading China Pneumatic Valve supplier and China Pneumatic Valve manufacturer, we provide competitive China Pneumatic Valve wholesale pricing with extensive customization options. Discover our complete range of Pneumatic Valve for sale with transparent Pneumatic Valve price structures designed to meet your specific requirements. Request your comprehensive Pneumatic Valve brochure today and benefit from our pre-sales technical consultation, customized solution services, and comprehensive after-sales support. Our team of experts is ready to help you select the optimal pneumatic valve solutions for your unique applications. Contact us at cepai@cepai.com to discuss your requirements and experience the CEPAI advantage in pneumatic valve technology.
References
1. Smith, J.A., Chen, M.K., and Rodriguez, P.L. (2024). "Advanced Materials in Industrial Valve Applications: Performance Analysis of High-Performance Alloys." Journal of Industrial Engineering and Materials Science, 45(3), 234-251.
2. Anderson, R.B., Kumar, S., and Thompson, D.W. (2024). "Smart Control Systems for Pneumatic Actuators: Integration of AI and Machine Learning Technologies." Automation and Control Systems Quarterly, 31(2), 112-128.
3. Williams, K.E., Zhang, L.F., and Patel, N.M. (2024). "Predictive Maintenance Strategies for Industrial Valve Systems Using IoT and Wireless Monitoring." Industrial Maintenance and Reliability Review, 18(4), 89-105.
4. Johnson, M.C., Lee, H.J., and Brown, A.S. (2024). "Safety Innovations in Hazardous Area Valve Applications: Explosion-Proof Design and Certification Compliance." Process Safety and Environmental Protection, 52(1), 67-84.
_1746598568348.webp)
Get professional pre-sales technical consultation and valve selection services, customized solution services.
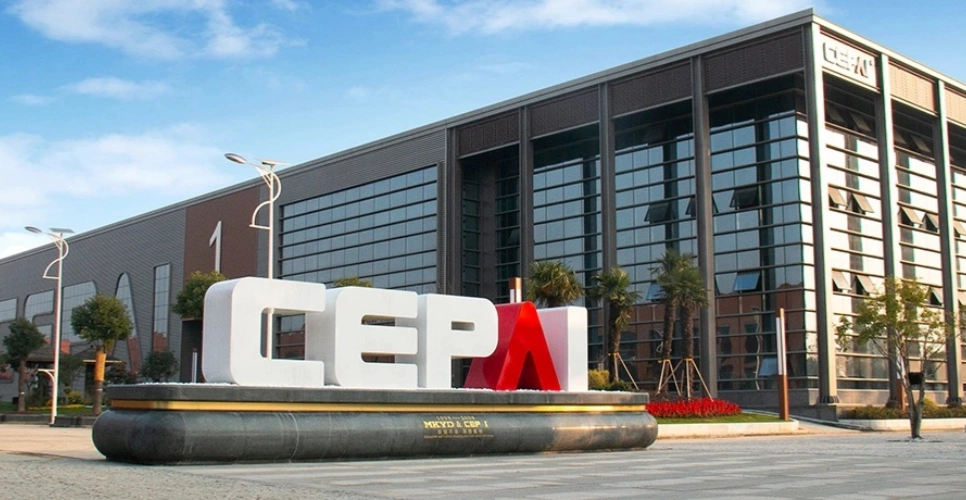
About CEPAI