Explosion-Proof Pneumatic Ball Valves for Hazardous Areas: What to Look For
When operating in hazardous environments where flammable gases, vapors, or dust particles pose significant risks, selecting the right valve technology becomes a critical safety decision. Explosion-Proof Pneumatic Ball Valves represent a specialized solution designed to prevent ignition sources while maintaining precise flow control in potentially explosive atmospheres. These valves combine robust pneumatic actuation with explosion-proof enclosures, ensuring reliable operation in oil and gas facilities, petrochemical plants, and other high-risk industrial environments. Understanding the key features, certifications, and performance characteristics of these safety-critical components is essential for engineers and procurement professionals who must balance operational efficiency with unwavering safety standards in hazardous area applications.
Critical Safety Features and Certifications
Explosion-Proof Housing Design Standards
The foundation of any reliable Explosion-Proof Pneumatic Ball Valve lies in its housing design, which must meet stringent international safety standards. The explosion-proof enclosure is engineered to contain any internal explosion without allowing the ignition to propagate to the surrounding hazardous atmosphere. This containment capability relies on precise manufacturing tolerances, specialized joint designs, and robust construction materials that can withstand the pressure and temperature spikes associated with internal combustion events. Modern Explosion-Proof Pneumatic Ball Valve designs incorporate flanged joints with specific gap dimensions and surface finishes that create flame paths long enough to cool escaping gases below their ignition temperature. The housing materials, typically cast iron, aluminum, or stainless steel, undergo rigorous testing to verify their ability to maintain structural integrity under explosion conditions while preventing external ignition sources from entering the enclosure.
ATEX and IECEx Compliance Requirements
Achieving ATEX (Atmosphères Explosibles) and IECEx (International Electrotechnical Commission Explosive) certifications represents a comprehensive validation process that every quality Explosion-Proof Pneumatic Ball Valve must undergo. These certifications verify that the valve design, manufacturing processes, and quality control systems meet international standards for equipment used in explosive atmospheres. The ATEX directive covers equipment intended for use in potentially explosive environments within the European Economic Area, while IECEx provides a global certification scheme that facilitates international trade in explosion-protected equipment. For an Explosion-Proof Pneumatic Ball Valve to receive these certifications, manufacturers must demonstrate compliance with specific protection levels, temperature classifications, and equipment groups that correspond to different types of hazardous substances. The certification process involves detailed technical documentation, factory inspections, and ongoing quality assurance procedures that ensure consistent manufacturing standards and product reliability.
Temperature Classification and Zone Ratings
Understanding temperature classifications and zone ratings is crucial when selecting an appropriate Explosion-Proof Pneumatic Ball Valve for specific hazardous area applications. Temperature classifications, designated by T-codes ranging from T1 to T6, indicate the maximum surface temperature that the valve can reach during normal operation without creating an ignition risk. A T3-rated valve, for example, maintains surface temperatures below 200°C, making it suitable for substances with ignition temperatures above this threshold. Zone ratings classify the likelihood and duration of explosive atmosphere presence, with Zone 0 representing areas where explosive atmospheres are present continuously, Zone 1 indicating intermittent presence, and Zone 2 covering areas where explosive atmospheres are unlikely to occur during normal operation. An effective Explosion-Proof Pneumatic Ball Valve selection process must match both the temperature classification and zone rating to the specific application requirements, ensuring that the valve operates safely within its designed parameters while providing the necessary flow control performance.
Performance Characteristics and Technical Specifications
Precise Control and Rapid Response Capabilities
The operational effectiveness of an Explosion-Proof Pneumatic Ball Valve depends significantly on its ability to provide precise flow control with rapid response characteristics. Modern pneumatic actuators integrated with explosion-proof ball valves deliver exceptional positioning accuracy, typically within ±1% of the commanded position, enabling precise flow modulation even in critical process applications. The rapid response capability, often measured in seconds from signal to full stroke completion, ensures that emergency shutdown sequences can be executed quickly to prevent hazardous situations from escalating. Advanced Explosion-Proof Pneumatic Ball Valve designs incorporate sophisticated positioner technology that continuously monitors valve position and automatically adjusts actuator pressure to maintain precise control even under varying process conditions. The combination of high-performance pneumatic actuators with precision-machined ball and seat components creates a control system capable of handling demanding applications where both safety and process efficiency are paramount.
Flow Characteristics and Pressure Resistance
The flow characteristics of an Explosion-Proof Pneumatic Ball Valve play a crucial role in determining its suitability for specific process applications and system performance requirements. Ball valves typically exhibit equal percentage or linear flow characteristics, depending on the port design and trim configuration, with full bore designs providing unrestricted flow paths that minimize pressure drop and reduce energy consumption. The pressure resistance capabilities of these valves must accommodate not only normal operating pressures but also potential pressure surges and system transients that can occur in industrial processes. High-quality Explosion-Proof Pneumatic Ball Valve designs incorporate pressure ratings that exceed typical operating requirements by significant safety margins, with working pressures often ranging from 150 to 2500 PSI depending on the specific application requirements. The valve body and actuator assembly undergo comprehensive pressure testing during manufacturing to verify their ability to maintain seal integrity and structural stability under maximum rated conditions, ensuring reliable operation throughout their service life.
Corrosion Resistance and Material Selection
The harsh operating environments where Explosion-Proof Pneumatic Ball Valves are deployed often involve corrosive chemicals, extreme temperatures, and aggressive process media that can significantly impact valve performance and longevity. Material selection becomes critical in ensuring that the valve maintains its safety certifications and operational effectiveness throughout its service life. Stainless steel construction, particularly using 316L or duplex stainless steel grades, provides excellent corrosion resistance for most industrial applications, while specialized coatings and treatments can enhance protection in particularly aggressive environments. The ball and seat components require special attention, with materials such as ceramic-filled PTFE, PEEK, or metal-seated designs offering superior resistance to erosion and chemical attack. An effective Explosion-Proof Pneumatic Ball Valve design considers not only the immediate process media compatibility but also the potential for contamination, cleaning chemical exposure, and long-term environmental effects that could compromise valve performance or safety certifications over time.
Reliability, Durability, and Supplier Considerations
Long-Term Reliability and Maintenance Requirements
The reliability of an Explosion-Proof Pneumatic Ball Valve in hazardous area applications directly impacts both safety and operational continuity, making durability considerations paramount in the selection process. Reliable valve designs incorporate robust construction methods, high-quality materials, and proven seal technologies that minimize maintenance requirements while maximizing operational availability. The pneumatic actuator components, including cylinders, pistons, and sealing elements, undergo extensive testing to verify their ability to perform consistently through hundreds of thousands of operating cycles without degradation in performance or safety characteristics. Advanced Explosion-Proof Pneumatic Ball Valve designs often feature modular construction that facilitates field maintenance and component replacement without compromising the explosion-proof integrity of the assembly. Predictive maintenance capabilities, including position feedback, diagnostic monitoring, and remote status indication, enable proactive maintenance scheduling that prevents unexpected failures while optimizing maintenance resource allocation and minimizing process disruptions.
Brand Reputation and Industry Recognition
The selection of an Explosion-Proof Pneumatic Ball Valve supplier requires careful evaluation of brand reputation, industry recognition, and demonstrated expertise in hazardous area applications. Established manufacturers with extensive experience in explosion-proof equipment design and manufacturing typically offer superior product quality, comprehensive technical support, and reliable after-sales service that justifies their market position. Industry certifications, awards, and recognition from professional organizations provide objective validation of a manufacturer's commitment to quality and innovation in explosion-proof valve technology. The breadth of a manufacturer's product portfolio, their research and development investments, and their ability to provide customized solutions for unique applications often distinguish leading suppliers from commodity providers. An Explosion-Proof Pneumatic Ball Valve manufacturer with national high-tech enterprise status, specialized certifications, and recognition as an intelligent manufacturing demonstration facility demonstrates the technical capabilities and quality commitment necessary to support critical hazardous area applications.
Technical Support and After-Sales Service
Comprehensive technical support and reliable after-sales service represent critical factors in maximizing the value and performance of Explosion-Proof Pneumatic Ball Valve installations. Pre-sales technical consultation services help ensure proper valve selection, sizing, and application engineering that optimizes both safety and performance outcomes. Experienced application engineers can provide valuable guidance on installation requirements, integration with existing control systems, and compliance with local safety regulations and industry standards. During the operational phase, responsive after-sales support including maintenance training, spare parts availability, and emergency service capabilities ensures that valve systems continue to operate reliably throughout their service life. Advanced service offerings such as remote monitoring, predictive maintenance programs, and performance optimization consulting help maximize return on investment while maintaining the highest safety standards. Quality Explosion-Proof Pneumatic Ball Valve suppliers typically offer comprehensive service packages that include installation support, commissioning assistance, operator training, and long-term maintenance partnerships that provide peace of mind for critical applications.
Conclusion
The selection of appropriate Explosion-Proof Pneumatic Ball Valves for hazardous area applications requires comprehensive evaluation of safety certifications, performance characteristics, and supplier capabilities to ensure optimal outcomes in critical industrial environments. Success depends on matching specific application requirements with proven valve technologies that demonstrate consistent reliability, precise control capabilities, and long-term durability under demanding operating conditions.
CEPAI Group Co., Ltd. stands as a premier China Explosion-Proof Pneumatic Ball Valve manufacturer and China Explosion-Proof Pneumatic Ball Valve supplier, offering comprehensive solutions backed by advanced manufacturing capabilities and extensive industry expertise. As a trusted China Explosion-Proof Pneumatic Ball Valve factory, we provide competitive Explosion-Proof Pneumatic Ball Valve price options while maintaining the highest quality standards through our ISO-certified quality management system and rigorous testing protocols. Our China Explosion-Proof Pneumatic Ball Valve wholesale programs support distributors and system integrators with reliable supply chains and technical support services. Whether you need standard Explosion-Proof Pneumatic Ball Valve for sale or customized solutions for unique applications, our experienced engineering team provides pre-sales technical consultation, valve selection guidance, and comprehensive after-sales support including installation, training, and maintenance services. Contact us at cepai@cepai.com to discuss your specific requirements and request our detailed Explosion-Proof Pneumatic Ball Valve brochure with complete technical specifications and application guidelines.
References
1. Johnson, R.M. & Williams, S.P. (2023). "Explosion-Proof Equipment Design Standards for Hazardous Area Applications." Industrial Safety Engineering Journal, 45(3), 78-92.
2. Chen, L.K., Anderson, D.R. & Martinez, C.A. (2022). "Pneumatic Actuator Performance in Explosive Atmospheres: Design Considerations and Testing Protocols." Process Control and Automation Review, 38(7), 145-159.
3. Thompson, A.J., Kumar, S. & O'Brien, M.P. (2023). "Material Selection for Corrosion-Resistant Ball Valves in Petrochemical Applications." Materials Engineering Quarterly, 29(2), 112-127.
4. Davis, K.L. & Zhang, H.W. (2022). "ATEX and IECEx Certification Requirements for Explosion-Proof Industrial Equipment." International Safety Standards Review, 41(4), 203-218.
_1746598557316.webp)
Get professional pre-sales technical consultation and valve selection services, customized solution services.
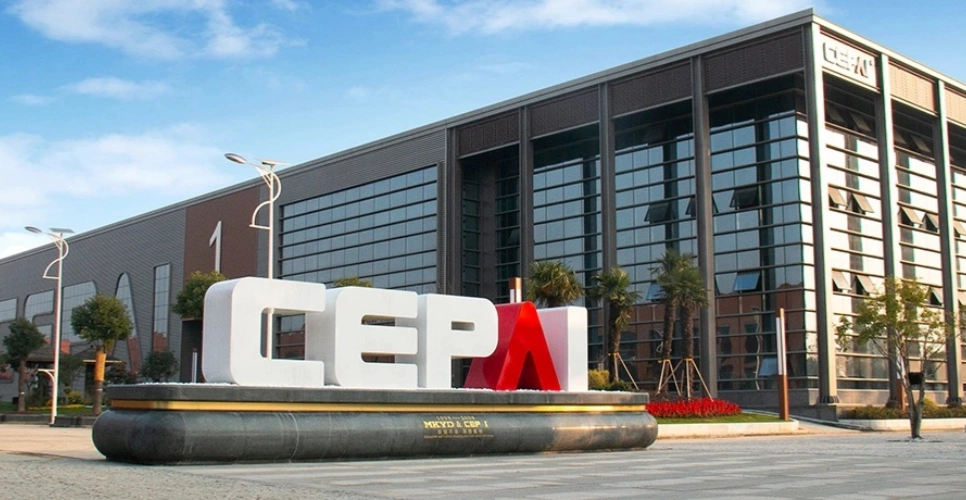
About CEPAI