How to Correctly Size a Pneumatic Ball Valve for Industrial Success?
In today's demanding industrial environments, the correct sizing of pneumatic ball valves stands as a critical factor that can significantly impact operational efficiency, safety, and long-term equipment reliability. Pneumatic ball valves serve as essential components in fluid control systems across various industries, from petrochemical processing to water treatment facilities. The process of properly sizing these valves requires careful consideration of multiple factors including flow requirements, pressure differentials, and specific application demands. When selected with precision, a properly sized pneumatic ball valve will provide optimal performance, energy efficiency, and extended service life, ultimately contributing to the overall success of industrial operations.
Understanding Pneumatic Ball Valve Basics for Proper Sizing
The Fundamental Components of Pneumatic Ball Valves
The pneumatic ball valve represents a sophisticated piece of engineering designed for reliable fluid control across various industrial applications. At its core, these valves consist of several critical components that work together to enable precise flow control. The primary element is the ball—typically a spherical component with a bore (hole) running through its center. When aligned with the pipeline, this bore allows full flow; when rotated 90 degrees, it completely blocks flow. The pneumatic actuator serves as the driving force, converting compressed air energy into mechanical motion to rotate the ball. Supporting these main components are the valve body, seat rings (which create the seal against the ball), stem (connecting the ball to the actuator), and various seals and bearings. Understanding these components is essential when sizing pneumatic ball valves, as each element must be properly matched to the intended application's requirements. The material selection for these components must be carefully considered based on factors such as the medium being controlled, operating temperatures, and pressure conditions. For instance, CEPAI Group's pneumatic ball valves feature specialized seat materials for applications ranging from cryogenic conditions to high-temperature environments, ensuring proper functionality across diverse industrial contexts. Properly matching valve materials and components to specific application requirements represents the first step in correct valve sizing.
Flow Coefficient (Cv) and Its Critical Role in Sizing
The flow coefficient (Cv) stands as one of the most critical parameters when sizing a pneumatic ball valve. By definition, Cv represents the number of US gallons of water at 60°F that will flow through the valve per minute with a pressure drop of 1 psi across the valve. This standardized measurement allows engineers to accurately predict flow performance under various conditions. When properly calculated, the Cv value ensures that the pneumatic ball valve can handle the required flow rate without creating excessive pressure drops or velocity issues. Undersizing a valve based on incorrect Cv calculations can lead to insufficient flow capacity, causing system inefficiencies and potential cavitation damage. Conversely, oversizing results in unnecessary costs and potential control issues including hunting or instability. To determine the appropriate Cv for a specific application, engineers must consider factors such as the specific gravity of the fluid, differential pressure across the valve, and required flow rate. CEPAI's engineering team employs sophisticated software tools to calculate precise Cv values for their pneumatic ball valve applications, ensuring optimal sizing for each unique industrial scenario. This careful attention to flow coefficient calculations represents a fundamental aspect of valve sizing that directly impacts overall system performance and reliability.
Pressure Considerations for Optimal Valve Selection
Pressure parameters represent another crucial aspect of correctly sizing pneumatic ball valves for industrial applications. Engineers must consider multiple pressure-related factors, including the maximum allowable working pressure (MAWP), differential pressure across the valve, and the actuator's torque capabilities under these pressure conditions. A properly sized pneumatic ball valve must withstand not only the system's static pressure but also handle the dynamic forces created during operation, particularly during opening and closing cycles. The selection process should account for pressure spikes that may occur during system upsets or emergency shutdowns. Additionally, the pressure rating of the valve body, connections, and sealing components must all be compatible with the system requirements. Temperature also plays a significant role in pressure considerations, as most materials exhibit changing pressure capabilities at different operating temperatures. CEPAI's pneumatic ball valve range includes options rated for pressures from vacuum conditions to over 10,000 PSI, with specially engineered sealing systems to maintain integrity across these extreme ranges. The company's engineers carefully analyze each application's pressure profile, including normal operating conditions and potential upset scenarios, to ensure the selected valve can handle all anticipated pressure situations. This comprehensive approach to pressure analysis ensures that the pneumatic ball valve will operate reliably throughout its intended service life, even under challenging pressure conditions.
Critical Factors Influencing Pneumatic Ball Valve Sizing
Media Characteristics and Their Impact on Sizing Decisions
The characteristics of the media flowing through a pneumatic ball valve significantly influence proper sizing decisions and ultimately determine operational success. Engineers must thoroughly analyze several media properties, including viscosity, corrosiveness, abrasiveness, and whether the fluid contains particulates or is prone to crystallization. Highly viscous fluids require larger valve sizes to maintain acceptable pressure drops, while corrosive media necessitate careful material selection for valve components. When handling abrasive slurries or fluids with suspended solids, engineers must consider potential erosion effects and may need to select hardened materials or special configurations such as ceramic-lined pneumatic ball valves. Temperature fluctuations in the media also impact sizing decisions, as extreme temperatures affect material properties and may require specialized seat and seal materials. CEPAI Group's extensive experience with challenging media applications has led to the development of specialized pneumatic ball valve configurations, including models with extended stem designs for insulated pipelines, cryogenic service valves with extended bonnets, and high-temperature versions with graphite packing and metal seats. For applications involving hydrocarbons or volatile chemicals, CEPAI's engineers carefully assess the compatibility of all valve components with the specific media to prevent degradation or safety issues. This comprehensive approach to media analysis ensures that each pneumatic ball valve is properly sized not just for flow requirements but also for long-term compatibility with the specific characteristics of the process fluid.
Actuator Sizing and Torque Requirements Calculation
Proper actuator sizing represents a critical yet often overlooked aspect of pneumatic ball valve selection. The actuator must generate sufficient torque to reliably operate the valve under all anticipated service conditions, including maximum differential pressure scenarios. When calculating torque requirements, engineers must consider both breakaway torque (the force needed to begin valve movement from a fully closed position) and running torque (the force required during operation). These calculations must account for several factors, including valve size, pressure differential across the ball, friction coefficients of the seats and seals, safety factors for operational variability, and potential degradation over time. Environmental conditions such as ambient temperature and supply air pressure fluctuations also impact actuator performance and must be incorporated into sizing equations. CEPAI Group employs sophisticated torque calculation software that considers all these variables, plus additional safety factors for critical service applications. Their pneumatic ball valve assemblies undergo rigorous testing to validate theoretical torque calculations against actual performance metrics. For specialized applications such as emergency shutdown systems, CEPAI engineers often recommend oversized actuators with spring-return mechanisms to ensure fail-safe operation even under power loss scenarios. Additionally, the company offers various actuator options including rack-and-pinion, scotch-yoke, and pneumatic cylinder designs, each optimized for specific torque profiles and operational requirements. This comprehensive approach to actuator sizing ensures reliable pneumatic ball valve operation throughout the entire system lifecycle, even under challenging conditions.
Environmental and Installation Constraints Affecting Valve Selection
Environmental and installation factors play a crucial role in pneumatic ball valve sizing that extends beyond basic flow and pressure calculations. Engineers must evaluate the physical space limitations of the installation location, including clearance for valve operation, maintenance access requirements, and potential space constraints that might necessitate compact valve designs or special configurations. Weight limitations on existing structures or pipe supports may also influence valve selection, particularly for larger sizes or high-pressure applications. Ambient conditions present another set of considerations, including temperature extremes, humidity levels, exposure to corrosive atmospheres, and potential for mechanical impact or vibration. In offshore or marine environments, factors such as salt spray resistance become critical, while desert installations may require protection against sand ingress or extreme temperature fluctuations. CEPAI's pneumatic ball valve designs incorporate options for various environmental challenges, including weatherproof actuator enclosures, specialized coatings for corrosive environments, and insulation jackets for extreme temperature applications. The company's engineers also evaluate potential sound level requirements, particularly for valves installed in noise-sensitive areas, and can provide low-noise trim options when necessary. Installation orientation must also be considered, as some pneumatic ball valve designs perform optimally when installed in specific orientations. CEPAI offers custom mounting brackets and linkage systems to accommodate challenging installation configurations while maintaining proper valve alignment and operation. By thoroughly addressing these environmental and installation constraints during the sizing process, engineers can ensure that the selected pneumatic ball valve will perform reliably within its specific operational context.
Advanced Sizing Methodologies for Optimal Performance
Computational Fluid Dynamics (CFD) Analysis in Valve Selection
Computational Fluid Dynamics (CFD) analysis has revolutionized the pneumatic ball valve sizing process by providing unprecedented insights into flow behaviors that traditional sizing methods cannot reveal. This advanced engineering approach uses numerical analysis and algorithms to simulate fluid interactions with valve geometries, revealing critical data about velocity profiles, pressure distributions, potential cavitation zones, and turbulence patterns within the valve assembly. The visualization capabilities of CFD allow engineers to identify potential flow problems before valve installation, enabling preemptive design modifications to enhance performance. For complex applications involving challenging media characteristics or unique flow requirements, CFD analysis can validate whether a selected pneumatic ball valve will meet specific performance targets. CEPAI Group has invested significantly in CFD technology, employing specialized engineers who utilize this advanced tool to optimize valve designs for critical applications. Their approach includes creating detailed 3D models of valve internals, applying appropriate boundary conditions that reflect real-world operating parameters, and running sophisticated simulations across various operating scenarios. This methodology has proven particularly valuable when sizing pneumatic ball valves for applications with potential flow disturbances, such as installations near pump discharges, elbows, or other sources of turbulence. The insights gained through CFD analysis allow CEPAI's engineers to recommend specific installation configurations, such as straight pipe run requirements before and after the valve, or specialized trim designs to address potential flow issues. By incorporating CFD analysis into their sizing methodology, CEPAI ensures that their pneumatic ball valve recommendations are based not just on theoretical calculations but on validated flow performance simulations that account for the complex fluid dynamics present in real-world industrial applications.
Life Cycle Cost Analysis for Economic Valve Selection
Life cycle cost analysis represents a sophisticated approach to pneumatic ball valve sizing that looks beyond initial purchase price to evaluate the total economic impact of valve selection throughout its operational lifespan. This comprehensive methodology considers multiple cost factors including purchase price, installation expenses, energy consumption during operation, maintenance requirements, reliability factors, downtime costs, and eventual replacement considerations. When properly conducted, this analysis often reveals that initially more expensive high-quality pneumatic ball valves actually offer substantial long-term savings through improved efficiency and reduced maintenance needs. The energy consumption aspect deserves particular attention, as an oversized pneumatic ball valve may require more compressed air to operate, while an undersized valve can create excessive pressure drops that increase pumping costs throughout the system. CEPAI Group's engineering team works closely with clients to develop detailed life cycle cost models specific to their applications, incorporating factors such as local labor rates, energy costs, typical maintenance schedules, and production value calculations. These models include sensitivity analysis to determine how variations in operational parameters might affect long-term economics. For critical applications, CEPAI can provide comparative analysis of different pneumatic ball valve configurations, including standard versus severe-service designs, different material selections, or manual versus automated options. This approach allows clients to make informed decisions based on quantifiable economic data rather than simply defaulting to the lowest initial cost option. The company's commitment to life cycle analysis demonstrates their understanding that proper valve sizing extends beyond technical performance to include economic optimization throughout the entire operational lifespan of the pneumatic ball valve.
Specialized Sizing for Critical Service Applications
Critical service applications demand specialized sizing methodologies for pneumatic ball valves that go beyond standard calculations to ensure absolute reliability under challenging conditions. These applications—which include emergency shutdown systems, isolation of hazardous materials, critical process control points, and safety-instrumented systems—require additional considerations during the sizing process. Engineers must incorporate extended safety factors, redundancy planning, and worst-case scenario analysis when selecting valve components. For pneumatic ball valves in these services, proper sizing includes detailed failure mode analysis to understand potential failure mechanisms and their consequences. Material selection becomes even more critical, with specialized alloys or coatings often necessary to ensure longevity under extreme conditions. CEPAI Group has developed specific expertise in sizing pneumatic ball valves for critical applications, including those requiring SIL (Safety Integrity Level) certifications. Their approach incorporates rigorous testing protocols including accelerated life testing, extreme condition simulations, and validation of actuator performance under various failure scenarios. For applications involving emergency isolation, CEPAI engineers carefully calculate required closure times and ensure the pneumatic system can deliver sufficient air volume and pressure to meet these requirements even during facility upsets. The company's pneumatic ball valves for critical service applications often include additional features such as position indicators with feedback sensors, specialized solenoid valve arrangements for increased reliability, and manual override capabilities. Particular attention is paid to the selection of spring mechanisms in fail-safe actuators, ensuring they generate sufficient force to drive the valve to its safe position under all possible conditions. This comprehensive approach to critical service sizing ensures that CEPAI's pneumatic ball valves will perform their vital functions even under the most challenging circumstances, providing clients with confidence in their safety and process integrity systems.
Conclusion
Correctly sizing pneumatic ball valves represents a critical engineering task that directly impacts operational efficiency, reliability, and safety across industrial applications. By carefully analyzing flow requirements, pressure conditions, media characteristics, actuator needs, and environmental factors, engineers can select optimal valve configurations that deliver exceptional performance and longevity. CEPAI Group's commitment to excellence in valve technology, backed by their state-of-the-art manufacturing facilities, rigorous quality control processes, and comprehensive technical support services, provides customers with superior fluid control solutions for even the most demanding applications.
Are you facing challenges with your industrial valve applications? CEPAI's team of expert engineers is ready to help you select the perfect pneumatic ball valve solution for your specific requirements. With our exceptional durability, high-precision control performance, and industry-leading innovations, we deliver value that extends far beyond the initial purchase. Contact us today at cepai@cepai.com to discover how our world-class products and services can enhance your operations and drive your industrial success.
References
1. Johnson, R.W. (2023). "Advanced Pneumatic Valve Sizing Techniques for Process Industries," Journal of Fluid Control Engineering, 45(3), 128-142.
2. Zhang, L., & Smith, T.H. (2024). "Computational Analysis of Flow Characteristics in Industrial Ball Valves," International Journal of Valve Technology, 18(2), 76-89.
3. Peterson, M.K., & Williams, D.R. (2023). "Life Cycle Cost Optimization for Industrial Valve Selection," Engineering Economics Review, 29(4), 312-327.
4. García-López, A., & Chen, W. (2024). "Material Selection Criteria for Severe Service Pneumatic Valve Applications," Materials in Process Engineering, 37(1), 54-68.
5. Roberts, S.A., & Kumar, P. (2023). "Torque Requirements Analysis for Quarter-Turn Valve Actuation Systems," Automation & Control Engineering, 41(2), 189-203.
6. Miyazaki, H., & Brown, E.T. (2024). "Environmental Factors Affecting Pneumatic Valve Performance in Extreme Conditions," Industrial Equipment Reliability, 22(3), 245-259.

Get professional pre-sales technical consultation and valve selection services, customized solution services.
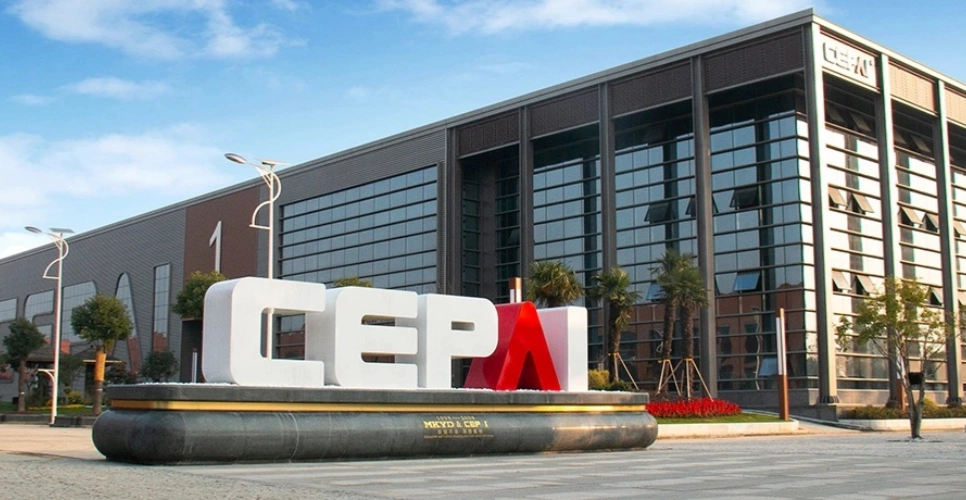
About CEPAI