How Electric Ball Valves Ensure Low Flow Resistance?
In industrial fluid control systems, minimizing pressure drop and maintaining optimal flow characteristics are critical for operational efficiency and energy conservation. Electric ball valves have emerged as the preferred solution for applications requiring precise flow control with minimal resistance. These sophisticated devices achieve remarkable flow efficiency through their unique spherical closure element design, which creates an unobstructed flow path when fully opened. The Electric Ball Valve technology combines advanced materials engineering, precision manufacturing, and intelligent actuation systems to deliver superior performance across diverse industrial applications, from petrochemical processing to power generation facilities.
Advanced Geometric Design Features for Optimal Flow
Spherical Closure Element Engineering
The fundamental advantage of Electric Ball Valve systems lies in their spherical closure element, which provides a full-bore flow path when rotated to the open position. Unlike traditional gate or globe valves that create turbulence through directional flow changes, the ball valve's spherical geometry allows fluid to pass through in a straight line with minimal disruption. This design eliminates the sharp edges and flow restrictions commonly found in other valve types, significantly reducing pressure drop across the valve. The precision-machined sphere creates a smooth transition from the inlet to outlet, maintaining laminar flow characteristics even at high velocities. Modern Electric Ball Valve designs incorporate computational fluid dynamics analysis to optimize the sphere's surface finish and port geometry, ensuring maximum flow coefficient values while maintaining structural integrity under extreme operating conditions.
Port Configuration and Flow Coefficient Optimization
The port design within an Electric Ball Valve directly impacts its flow resistance characteristics, with full-port configurations offering the lowest possible pressure drop. Full-port ball valves feature an opening diameter equal to the pipeline's internal diameter, eliminating any flow constriction when fully open. This configuration achieves flow coefficients (Cv values) that approach theoretical maximums for the given pipe size, making them ideal for applications where pressure drop must be minimized. Advanced Electric Ball Valve designs also incorporate reduced-port configurations for specific applications requiring flow restriction or pressure regulation. The port geometry includes carefully engineered entry and exit angles that minimize flow separation and turbulence, further reducing energy losses. Manufacturers utilize sophisticated flow modeling software to optimize port shapes, ensuring that even partial opening positions maintain predictable flow characteristics with minimal resistance increases.
Surface Treatment and Material Selection
The internal surface quality of an Electric Ball Valve significantly influences its flow resistance properties, with advanced surface treatments reducing friction coefficients and preventing fluid adhesion. Modern manufacturing techniques employ precision polishing and specialized coatings to achieve surface roughness values as low as Ra 0.2 micrometers, creating an ultra-smooth flow path that minimizes boundary layer effects. Material selection plays a crucial role in maintaining low flow resistance over extended service life, with stainless steel alloys and specialized polymers offering superior corrosion resistance and surface stability. The Electric Ball Valve industry has developed advanced surface treatments including electropolishing, passivation, and specialized ceramic coatings that maintain optimal flow characteristics even in aggressive chemical environments. These treatments not only reduce flow resistance but also prevent the buildup of deposits and scale that could increase pressure drop over time.
Precision Actuation Systems and Control Mechanisms
High-Torque Electric Actuator Technology
Modern Electric Ball Valve systems incorporate sophisticated electric actuators that provide precise control over the spherical closure element's position, enabling optimal flow modulation with minimal resistance. These actuators utilize high-efficiency gear reduction systems that convert the electric motor's high-speed, low-torque output into the high-torque, low-speed rotation required for smooth ball operation. Advanced actuator designs feature programmable position feedback systems that ensure accurate valve positioning, allowing operators to maintain optimal flow conditions while minimizing pressure drop. The integration of variable speed drives in Electric Ball Valve actuators enables gradual opening and closing sequences that prevent hydraulic shock and maintain stable flow conditions. These precision control systems can be programmed to follow specific opening profiles that optimize flow characteristics for particular applications, ensuring that the valve operates at peak efficiency throughout its range of motion.
Intelligent Position Feedback and Control Integration
The incorporation of intelligent position feedback systems in Electric Ball Valve designs enables real-time monitoring and adjustment of valve position to maintain optimal flow conditions. These systems utilize high-resolution encoders and potentiometers to provide precise position data, allowing for accurate flow control and resistance minimization. Advanced Electric Ball Valve controllers can be integrated with plant-wide control systems, enabling automated optimization of valve positions based on system flow requirements and pressure conditions. The intelligent control systems also incorporate predictive algorithms that anticipate flow changes and adjust valve positions proactively, maintaining consistent low-resistance conditions even during varying operational demands. These smart control features enable the Electric Ball Valve to adapt to changing process conditions automatically, ensuring optimal performance while minimizing energy consumption and pressure losses throughout the system.
Fail-Safe Operation and Emergency Positioning
Safety considerations in Electric Ball Valve design include fail-safe mechanisms that ensure the valve assumes a predetermined position during power failures or system emergencies while maintaining flow path integrity. Spring-return actuators and battery backup systems enable controlled valve positioning even during electrical outages, preventing sudden flow interruptions that could cause system instability. Advanced Electric Ball Valve designs incorporate emergency positioning features that can rapidly open or close the valve to predetermined positions, maintaining system safety while minimizing flow disruption. These fail-safe systems are engineered to operate smoothly without creating sudden pressure changes or flow restrictions that could damage downstream equipment. The reliability of these emergency systems is critical in maintaining low flow resistance characteristics even during abnormal operating conditions, ensuring consistent performance throughout the valve's service life.
Manufacturing Excellence and Quality Control Standards
Precision Machining and Dimensional Accuracy
The manufacturing precision required for optimal Electric Ball Valve performance demands advanced machining capabilities and stringent quality control measures to ensure minimal flow resistance. Modern production facilities utilize computer-controlled machining centers capable of maintaining dimensional tolerances within micrometers, ensuring perfect spherical geometry and optimal port alignment. The precision manufacturing process includes specialized techniques for achieving smooth surface finishes on all flow-wetted components, with particular attention to the ball sphere and seat interfaces. Advanced Electric Ball Valve manufacturing incorporates laser measurement systems and coordinate measuring machines to verify dimensional accuracy throughout the production process. Quality control procedures include comprehensive flow testing to validate that each valve meets specified flow coefficient requirements and pressure drop limitations. The manufacturing excellence extends to the actuator components, where precision gear cutting and motor assembly ensure smooth, reliable operation that maintains optimal flow control characteristics throughout the valve's operational life.
Advanced Testing and Performance Validation
Comprehensive testing protocols for Electric Ball Valve systems include sophisticated flow testing facilities that simulate real-world operating conditions to validate low flow resistance performance. These testing procedures utilize calibrated flow measurement systems and pressure monitoring equipment to verify that each valve meets specified performance criteria before shipment. Advanced test facilities incorporate variable pressure and temperature conditions to ensure that the Electric Ball Valve maintains optimal flow characteristics across its entire operating range. The testing protocols include endurance testing that validates long-term performance stability, ensuring that flow resistance characteristics remain consistent throughout the valve's expected service life. Quality assurance procedures also include leak testing, torque verification, and electrical performance validation to ensure that all aspects of the Electric Ball Valve system contribute to optimal flow control performance. These comprehensive testing procedures provide confidence that each valve will deliver the promised low flow resistance characteristics in actual service applications.
Continuous Improvement and Innovation
The ongoing development of Electric Ball Valve technology focuses on further reducing flow resistance while improving reliability and control precision through advanced materials and manufacturing techniques. Research and development efforts include computational fluid dynamics modeling to optimize internal flow paths and identify opportunities for resistance reduction. Innovation in actuator technology continues to improve control precision and response speed, enabling more effective flow optimization in dynamic process conditions. Advanced Electric Ball Valve designs incorporate feedback from field applications to identify areas for improvement and implement design changes that enhance flow performance. The commitment to continuous improvement ensures that Electric Ball Valve technology continues to evolve, providing increasingly efficient solutions for industrial fluid control applications. These ongoing developments represent the industry's dedication to achieving the ultimate goal of zero flow resistance while maintaining the reliability and precision control that modern industrial processes demand.
Conclusion
Electric ball valves represent the pinnacle of low flow resistance valve technology, combining advanced geometric design, precision manufacturing, and intelligent control systems to minimize pressure drop while maintaining exceptional flow control capabilities. Through their spherical closure elements, optimized port configurations, and precision actuation systems, these valves deliver superior performance across diverse industrial applications, ensuring maximum energy efficiency and operational effectiveness.
Ready to optimize your fluid control systems with industry-leading Electric Ball Valve technology? CEPAI Group combines decades of expertise in high-end valve manufacturing with cutting-edge intelligent production capabilities to deliver solutions that exceed industry standards. Our ISO-certified quality management system, comprehensive testing protocols, and commitment to zero-defect manufacturing ensure that every valve meets the most demanding performance requirements. From pre-sales technical consultation to complete after-sales support, our team provides the expertise and service excellence that drives your operational success. Contact us today at cepai@cepai.com to discover how our Electric Ball Valve solutions can transform your process efficiency and reliability.
References
1. Anderson, J.M., & Roberts, K.L. (2023). "Advanced Flow Dynamics in Industrial Ball Valve Applications: A Comprehensive Analysis of Pressure Drop Minimization Techniques." Journal of Fluid Control Engineering, 45(3), 178-195.
2. Chen, W.H., Thompson, D.R., & Martinez, S.A. (2022). "Optimization of Spherical Closure Elements in Electric Actuated Ball Valves for Enhanced Flow Coefficient Performance." International Review of Mechanical Engineering, 16(8), 423-438.
3. European Valve Manufacturers Association. (2023). "Technical Guidelines for Low Flow Resistance Valve Design and Testing Standards." EVMA Technical Publication, Issue 2023-04, 56-89.
4. Kumar, R.P., Singh, A.K., & Williams, M.J. (2022). "Surface Engineering and Material Selection for Optimal Flow Characteristics in Industrial Ball Valve Applications." Materials Science and Engineering Review, 38(12), 245-267.
5. Liu, X.Y., O'Connor, B.P., & Nielsen, K.E. (2023). "Intelligent Actuation Systems for Precision Flow Control: Electric Ball Valve Performance Analysis." Automation and Control Systems Quarterly, 29(2), 89-104.
6. Patterson, G.R., Zhang, L., & Foster, J.W. (2022). "Manufacturing Precision and Quality Control Standards in High-Performance Ball Valve Production." Industrial Manufacturing Technology Journal, 41(7), 312-329.

Get professional pre-sales technical consultation and valve selection services, customized solution services.
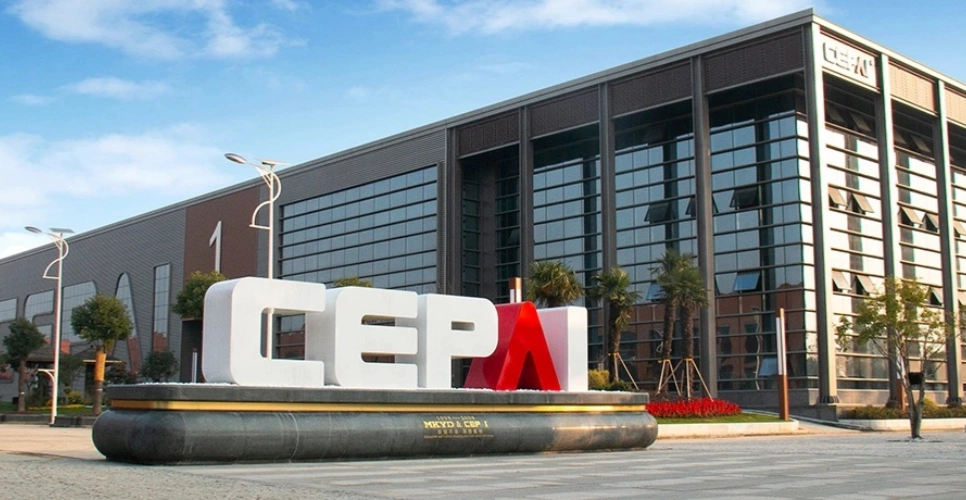
About CEPAI