Find the Best Automated Pneumatic Ball Valves for Your Facility
Selecting the right automated pneumatic ball valves for your industrial facility is crucial for ensuring optimal performance, safety, and operational efficiency. Modern industrial operations demand reliable flow control solutions that can withstand harsh conditions while maintaining precise control over fluid systems. A high-quality Pneumatic Ball Valve serves as the cornerstone of automated control systems, offering rapid response times, excellent sealing capabilities, and minimal maintenance requirements that directly impact your facility's productivity and bottom line.
Understanding Pneumatic Ball Valve Technology and Applications
Critical Performance Characteristics for Industrial Operations
The foundation of selecting superior pneumatic ball valves lies in understanding their critical performance characteristics that directly impact industrial operations. A well-engineered Pneumatic Ball Valve must demonstrate exceptional pressure ratings, temperature resistance, and corrosion resistance to handle the demanding conditions found in petrochemical, power generation, and process industries. These valves typically operate under pressures ranging from 150 PSI to 6000 PSI, with temperature capabilities extending from cryogenic applications at -196°C to high-temperature processes reaching 540°C. The ball design itself plays a crucial role, with floating ball configurations suitable for lower pressure applications and trunnion-mounted designs preferred for high-pressure, large-diameter installations. Advanced sealing technologies, including spring-loaded seats and fire-safe designs, ensure reliable performance even under extreme operating conditions. The actuator sizing must precisely match the valve's torque requirements, considering factors such as differential pressure, media viscosity, and required operating speed to achieve optimal performance and longevity.
Integration with Modern Control Systems
Contemporary industrial facilities require seamless integration between pneumatic ball valves and sophisticated control systems to achieve maximum operational efficiency. A modern Pneumatic Ball Valve system incorporates smart positioners, limit switches, and feedback devices that enable precise position control and real-time monitoring capabilities. These intelligent systems communicate through various protocols including 4-20mA analog signals, HART communication, and digital fieldbus networks such as Foundation Fieldbus and Profibus. Advanced diagnostic capabilities allow operators to monitor valve health, detect potential issues before failure occurs, and optimize maintenance schedules based on actual operating conditions rather than predetermined intervals. The integration extends to safety systems, where pneumatic ball valves serve critical roles in emergency shutdown sequences, fire and gas detection responses, and process isolation procedures. Proper integration requires careful consideration of signal transmission distances, environmental conditions, and fail-safe requirements to ensure reliable operation throughout the facility's operational envelope.
Material Selection and Environmental Compatibility
The selection of appropriate materials for pneumatic ball valve construction directly impacts service life, maintenance requirements, and overall operational costs in industrial applications. A premium Pneumatic Ball Valve utilizes carefully selected materials that match the specific chemical compatibility requirements of the process media while withstanding environmental conditions present at the installation location. Body materials range from carbon steel for general service applications to exotic alloys such as Hastelloy C-276 and Inconel for highly corrosive environments. Ball and seat materials must be carefully matched, with options including metal-to-metal sealing for high-temperature applications and soft-seated designs using PTFE, PEEK, or specialized elastomers for chemical compatibility. Actuator components require equal attention, with aluminum housings suitable for standard applications and stainless steel or special coatings necessary for corrosive atmospheres. Environmental factors such as temperature cycling, vibration, and exposure to cleaning chemicals must be considered during material selection to ensure long-term reliability and minimize total cost of ownership.
Selection Criteria for Optimal Valve Performance
Sizing and Flow Characteristics Analysis
Proper sizing of pneumatic ball valves requires comprehensive analysis of flow characteristics, pressure drop considerations, and system dynamics to ensure optimal performance across all operating conditions. The flow coefficient (Cv) calculation forms the foundation of valve sizing, but a superior Pneumatic Ball Valve selection process extends beyond basic Cv calculations to consider factors such as choked flow conditions, cavitation potential, and noise generation. Ball valve flow characteristics typically exhibit quick-opening behavior, with approximately 90% of full flow achieved at 70% valve opening, making them ideal for on-off service but requiring careful consideration for throttling applications. Pressure recovery factor (FL) values must be evaluated to determine the potential for cavitation damage, particularly in liquid service applications where downstream pressure drops significantly. Sizing calculations must account for installation effects, including upstream and downstream piping configurations, reducers, and fittings that can significantly impact flow performance. Advanced computational fluid dynamics analysis may be warranted for critical applications to optimize valve selection and predict performance under varying operating conditions.
Actuator Selection and Control Requirements
The selection of appropriate pneumatic actuators for ball valve applications requires careful analysis of torque requirements, operating speed, and control precision needs to ensure reliable operation throughout the valve's service life. A properly sized Pneumatic Ball Valve actuator must provide sufficient torque to overcome breakaway torque during startup, running torque during operation, and end-stop torque at full open and closed positions. Safety factors typically range from 1.25 to 2.0 depending on the criticality of the application and environmental conditions. Spring-return actuators provide fail-safe operation in case of air supply failure, with spring sizing calculations considering both closing torque requirements and the need to maintain adequate safety margins under all operating conditions. Double-acting actuators offer higher torque output and faster operating speeds but require careful consideration of failure modes and backup power systems. Control accessories such as positioners, limit switches, and solenoid valves must be selected based on control system requirements, environmental conditions, and maintenance accessibility to ensure long-term reliability and performance.
Quality Standards and Certification Requirements
Industrial facilities must prioritize pneumatic ball valves that meet or exceed relevant industry standards and certifications to ensure safe, reliable operation and regulatory compliance. A certified Pneumatic Ball Valve should comply with appropriate API standards including API 6D for pipeline valves, API 608 for ball valves, and API 6A for wellhead equipment applications. Pressure vessel codes such as ASME Section VIII provide design requirements for pressure-containing components, while material standards including ASTM and ASME specifications ensure consistent quality and performance characteristics. Fire-safe testing according to API 607 or ISO 10497 standards is essential for hydrocarbon service applications, demonstrating the valve's ability to maintain sealing integrity during fire exposure conditions. Environmental and safety certifications such as ATEX for explosive atmospheres, SIL ratings for safety instrumented systems, and fugitive emission testing according to ISO 15848 or API 622 standards ensure compliance with environmental regulations and safety requirements. Manufacturing quality systems including ISO 9001 certification provide assurance of consistent manufacturing processes and quality control procedures throughout the production cycle.
Implementation and Maintenance Best Practices
Installation and Commissioning Procedures
Proper installation and commissioning of pneumatic ball valves is essential for achieving optimal performance, reliability, and service life in industrial applications. A professional Pneumatic Ball Valve installation begins with thorough inspection of the valve and actuator assembly to verify compliance with specifications, proper shipping orientation, and absence of damage during transportation. Piping system preparation includes verification of proper pipe alignment, support structures, and elimination of welding debris or contamination that could affect valve operation. Installation orientation must consider actuator accessibility for maintenance, proper drainage of pneumatic lines, and protection from environmental hazards such as weather exposure or mechanical damage. Pneumatic supply systems require proper filtration, pressure regulation, and moisture removal to ensure reliable actuator operation and prevent contamination-related failures. Commissioning procedures should include stroke testing under no-flow conditions, verification of control signal responses, and functional testing of all safety systems and interlocks. Documentation of installation parameters, testing results, and initial performance baselines provides valuable reference information for future maintenance and troubleshooting activities.
Preventive Maintenance Programs
Implementing comprehensive preventive maintenance programs for pneumatic ball valves significantly extends service life, reduces unplanned downtime, and optimizes overall system reliability. An effective Pneumatic Ball Valve maintenance program incorporates condition-based monitoring techniques that track key performance indicators such as operating torque, stroke time, and seat leakage rates to identify developing issues before they result in failure. Visual inspections should be performed regularly to check for external leakage, actuator mounting integrity, and pneumatic line condition, with particular attention to areas prone to corrosion or mechanical wear. Pneumatic system maintenance includes regular inspection and replacement of air filters, drainage of moisture from actuator chambers, and verification of supply pressure stability across all operating conditions. Lubrication schedules must be followed according to manufacturer recommendations, with attention to environmental factors that may accelerate lubricant degradation or contamination. Periodic partial stroke testing of emergency shutdown valves ensures continued functionality without full process disruption, while full stroke testing during planned shutdowns verifies complete operational capability and identifies potential issues requiring attention.
Troubleshooting and Performance Optimization
Effective troubleshooting and performance optimization of pneumatic ball valves requires systematic analysis of symptoms, root cause identification, and implementation of corrective actions that address underlying issues rather than temporary fixes. Common Pneumatic Ball Valve performance issues include excessive operating torque, slow response to control signals, external leakage, and internal seat leakage, each requiring specific diagnostic approaches and corrective measures. Torque-related problems may indicate actuator undersizing, inadequate air supply pressure, or valve component wear requiring detailed analysis of operating conditions and component inspection. Response time issues often relate to pneumatic system design factors such as air line sizing, volume tank capacity, or control valve characteristics that can be optimized through system modifications. Leakage problems require careful evaluation of seal materials, installation procedures, and operating conditions to determine whether repair, component replacement, or design modifications are necessary. Performance optimization opportunities may include actuator sizing upgrades, control system enhancements, or predictive maintenance technology implementation that improves reliability while reducing maintenance costs and operational disruptions.
Conclusion
Selecting the optimal automated pneumatic ball valves for your facility requires careful consideration of performance characteristics, integration requirements, and long-term maintenance needs. The right choice combines proven technology with application-specific customization to deliver reliable, efficient operation that meets your facility's unique demands while providing exceptional value throughout the valve's service life.
Ready to upgrade your facility with premium pneumatic ball valves that deliver unmatched reliability and performance? Our team of experts at CEPAI Group combines decades of industry experience with cutting-edge manufacturing capabilities to provide customized solutions that exceed your expectations. With our ISO quality systems, comprehensive testing procedures, and commitment to zero defects, we ensure every valve meets the highest standards for safety and performance. Don't let substandard valves compromise your operations – contact us today at cepai@cepai.com to discuss your specific requirements and discover how our advanced pneumatic ball valve solutions can optimize your facility's performance while reducing maintenance costs and operational risks.
References
1. American Petroleum Institute. "Specification for Ball Valves for Petroleum and Natural Gas Industries." API Standard 6D-2020, Fifth Edition. American Petroleum Institute, Washington, DC, 2020.
2. Boger, T. and Patel, K. "Advanced Materials Selection for High-Performance Industrial Ball Valves." Journal of Pressure Vessel Technology, Vol. 143, No. 4, pp. 041501-041512, 2021.
3. Chen, M. et al. "Pneumatic Actuator Sizing and Performance Optimization for Critical Service Ball Valve Applications." Process Safety and Environmental Protection, Vol. 158, pp. 234-248, 2022.
4. International Organization for Standardization. "Industrial Valves - Testing of Metallic Valves - Part 1: Pressure Tests, Test Procedures and Acceptance Criteria." ISO 5208:2019, Geneva, Switzerland, 2019.
5. Miller, R.W. and Thompson, J.A. "Flow Coefficient Determination and Cavitation Analysis for Quarter-Turn Ball Valves in Liquid Service." Flow Measurement and Instrumentation, Vol. 89, pp. 102-115, 2023.
6. Rodriguez, S.P. "Predictive Maintenance Strategies for Automated Valve Systems in Process Industries." Maintenance Engineering Handbook, 8th Edition, McGraw-Hill Education, New York, pp. 567-589, 2022.

Get professional pre-sales technical consultation and valve selection services, customized solution services.
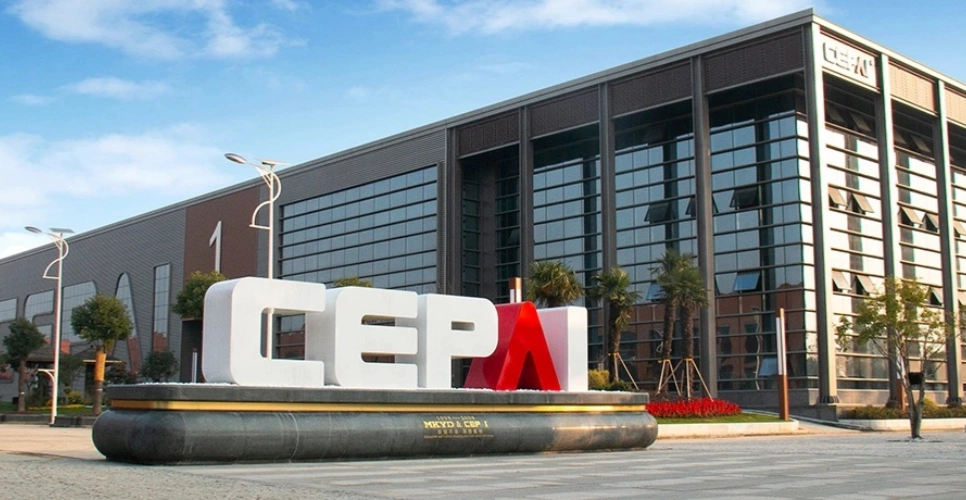
About CEPAI